اتصل
هاتف
+0086-371-86162511
عنوان
تشنغتشو ، الصين
TON ball mill for iron ore fines details for pellet
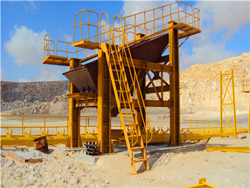
Usage of High-LOI Iron Ore Fines in Pellet Making Springer
1 Introduction High-LOI iron ore fines are received for detailed laboratory pelletization studies. Received iron ore fines consist of higher percentage of goethite with Pellets are balls formed by rolling moist concentrates and fines iron ores of different mineralogical and chemical composition, with Iron Ore Pelletizing Process: An Overview
احصل على السعر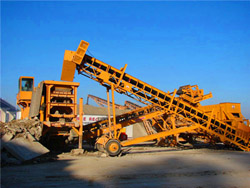
Optimization of Solids Concentration in Iron Ore
The quality of the iron ore pellet in the pelletizing process is directly related to the amount of fines that are contained in the mill The iron ore blend takes RT of 13 min when grounded in the BBM for 250% circulating load with 80% passing particle size of 56 µm. The blend iron ore sample Investigation on Iron Ore Grinding based on Particle Size Distribution
احصل على السعر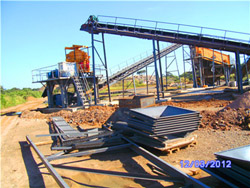
Iron ore pelletization ScienceDirect
A brief introduction to recent progress in iron ore pelletizing has been provided in this chapter, including the world output of fired pellets, the pellet production The pelletisation process involves drying the ore fines to reduce the moisture content to less than 1%, grinding in open circuit ball mills to get required Influence of raw material particle size on quality of pellets
احصل على السعر
Grate-kiln pelletization of Indian hematite fines and its
2.2.2. Ball milling of iron ores In this work, a dry ball milling process was conducted to pretreat Indian hematite ore fines. The grinding tests of the iron ore fines An iron ore concentrate sample was ground separately in a pilot-scale HPGR mill in multiple passes and a dry open-circuit ball mill to increase the specific surface area of particles. Grinding iron ore concentrate by using HPGR and ball mills
احصل على السعر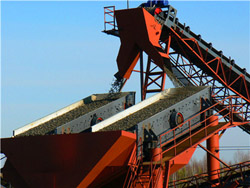
Utilization of Kimberlite as Binder for Iron Ore Pellet Making
The iron ore pellet produced with Kimberlite-based binder have exhibited better physical and metallurgical characteristics than pellets produced with conventional binders (Bentonite). The details of dry ball mill and surface area obtained at different time interval of dry About 10 tons of representative sample of Kimberlite was receivedIt is important to mention that iron ore fines, specifically the pellet feed (D 80 < 106 mm [20]), are the raw material for the production of iron ore pellets ("green balls"), whose particle(PDF) HPGR effect on the particle size and shape
احصل على السعر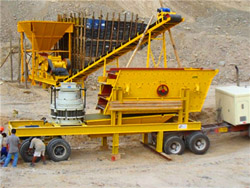
JSW STEEL LIMITED DOLVI, MAHARASHTRA
The raw material required for the proposed pellet plant #2 are iron ore fines, limestone, dolomite, coke and bentonite. Sources of various raw materials are furnished below: Iron ore fines Superior quality iron ore fines (pellet feed) shall be received by conveyor from RMHS yard to day bins near wet grinding unit.The compos-ite concentrate obtained in the pilot plant studies assayed 63.75% Fe, 2.1 % A1203, 2.65% SiO 2 with weight percent yield of 66.7 and iron recovery of 73.2%. The iron ore fines from the(PDF) Techno-economic Evaluation of Iron Ore Pellet
احصل على السعر
(PDF) Physicochemical Problems of Mineral Processing
The optimum conditions of ball mill operational parameters to reach the best pellet feed for each blast furnace burden and direct reduction iron (DRI) pellet feed were revealed using CCD optimization.The production of iron ore pellets at JSW Steel Limited involves the drying of iron ore fines to get the moisture less than 1% and grinding the dried material to get the required fineness –45 μm size ≥62.0%.Prior to the formation of green pellets, the ground ore is mixed with small amounts of binding agents such as bentonite (0.7 to 0.9%), fluxes Optimization of Firing Temperature for Hematite Pellets J
احصل على السعر
Investigation on Iron Ore Grinding based on Particle Size Distribution
The iron ore blend takes RT of 13 min when grounded in the BBM for 250% circulating load with 80% passing particle size of 56 µm. The blend iron ore sample obtained from the BBM is composed of a higher percentage of fines and is not suitable for pellet making. So, the grinding is carried out in the LBM by varying the retention time of High-LOI iron ore fines are required for detailed laboratory pelletization studies and are used in pellet making. The received iron ore is martite–goethitic and hematite–goethitic form of ore with high LOI content. The iron ore consists of 57.7% Fe, 6.19% SiO2, 2.69% Al2O3, 8.80% moisture and 8.85% LOI. From thermo-gravimetric Usage of High-LOI Iron Ore Fines in Pellet Making Springer
احصل على السعر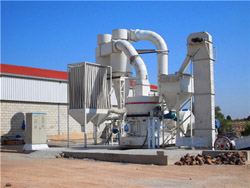
Recycling and Reuse of Iron Ore Pellet Fines SpringerLink
For pelletization study, as received iron oxide pellet fines were ground to below 150 μ using ball mill. The particle size distribution of ground iron ore fines was determined by the Malvern particle size analyzer (Hydro 2000MU, UK) and shown in Fig. 2.Blaine number was measured to determine surface area of the iron oxide pellet fines Abstract. A brief introduction to recent developments in iron ore pelletizing is provided in this chapter, including the world output of fired pellets, pellet production processes, preparation of pellet feed, inorganic and organic binders, and new additives. Throughout the chapter, the authors have used a difficult pellet feed, that is, aIron ore pelletization ScienceDirect
احصل على السعر
(PDF) Iron ore pelletization ResearchGate
Arrium Australia 0.810 0.810 0.440. 440 Iron Ore. The pelletizing process involves the preparation of ra w materials; the proportioning. and mixing of raw materials; the formation, preheating, andPellets are one of the principal raw materials of blast furnaces 1,2,3 and have the advantages of high total iron content, less gangue content, high compressive strength and uniform particle size. 4 Compared with sinter production, pellets have lower energy consumption and produce less pollution. When 100% pellets are used for Investigations on Compressive Strength and Microstructure
احصل على السعر
ResearchGate
These waste fines are being utilized as converting into Sponge Iron, Sinter, Briquettes and Pellets. Foy making pellets the size of the fines should be below 100 micron.Iron ore pelletizing using compressive and shear action on wet mixture feed has been studied. The physical properties, namely, moisture content, drop strength, green compressive strength (GCS), dry compressive strength (DCS), porosity, and cold crushing strength (CCS), have been studied. Pelletizing tests were carried out on four Effect of Application of Compressive and Shear Force on Iron Ore Pellet
احصل على السعر
Maximizing the Recycling of Iron Ore Pellets Fines Using
Nowadays, the iron ore pellet fines are used as a part of the sinter mixture during the sintering process to produce sinter for the blast furnace. In Nordic countries (e.g., Sweden and Finland) where sintering is not available anymore, the pellet fines are recycled into a blast furnace, thereby mixing it with other steel mill residues andforms of processed ore include sinter and briquettes. The average iron content of pellets is 63 percent. 11.23.2 Process Description2-5,41 Processing of taconite consists of crushing and grinding the ore to liberate iron-bearing particles, concentrating the ore by separating the particles from the waste material (gangue), and pelletizing the11.23 Taconite Ore Processing US EPA
احصل على السعر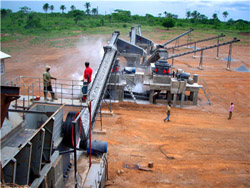
iron ore fines and mill scales. Conversion of Sponge Iron From Low Grade Iron ore And Mill. Directly Reduced Iron (DRI) using waste low grade iron ore (slime),mill scale and wasteAbstract The present communication describes an investigation on the preparation of metallized composite pellets from ilmenite concentrate. It was observed that the pellet size in the range of 8–12 mm, a binder dosage of 4 wt%, and internal carbon of 5 wt% are the optimum levels that help the pellets attain the desired drop number (~ 10) An Optimal Route for the Preparation of Metallized Composite Pellets
احصل على السعر
A Review on the Effect of the Mechanism of Organic Polymers on Pellet
Iron ore pellets not only have excellent metallurgical and mechanical properties but are also essential raw materials for improving iron and steel smelting in the context of the increasing global depletion of high-grade iron ore resources. Organic polymers, as important additive components for the production of high-quality pellets, iron ore pellets as Blast Furnace feed material comparing with the typical burden data when the furnace was running at 100% lump iron ore (average of three months) of anInternational Journal of Science and Engineering (IJSE)
احصل على السعر- المواصفات الفنية كسارة النبات
- gold mine investment proposal
- كسارة مخروطية من نوع Cara
- رابعا آلات الحجر مسحوق
- العقيق آلات الرمل المورد
- construction equipment manufacturers company
- مطحنة الحجر الجيري في نيجيريا
- نسبة التكسير للركام
- الكوارتز آلة طحن الكرة مطحنة الفحم
- regent prospecting supplies
- الذهب سحق ماكينة المستعملة
- الحجر الاستفسارات الإجمالية المورد محطم
- محطة كسارة تدفق الرسم البياني
- costos de molinos pulverizadores para
- kerugian menggunakan كسارة مخروط