اتصل
هاتف
+0086-371-86162511
عنوان
تشنغتشو ، الصين
extraction of crushing and grinding
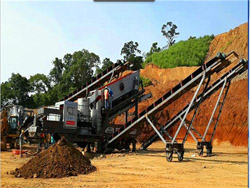
The Extractive Metallurgy Industry SpringerLink
The two common unit operations employed are crushing and grinding. Comminution to particle size of about 6 mm (maximum) is termed crushing. The process Whereas crushing is done mostly under dry conditions, grinding mills can be operated both dry and wet, with wet grinding being predominant. Crushing Some ores occur in nature as mixtures of discrete mineral particles, such Mineral processing Metallurgy, Crushing
احصل على السعر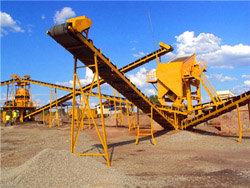
Wet extractive grinding process for efficient calcium
In the new extractive grinding process, we combine the grinding and extraction steps into a single unit with the aim of increasing both the rate and the yield of Optimizing the blast fragmentation to improve rock-breakage efficiencies during crushing and grinding is key to mine-to-mill (MTM) optimization. This study Use of drilling performance to improve rock-breakage
احصل على السعر
Study on Quantitative Separation Method of
Grinding is the process of crushing the material through impact and cascade force to reduce the particle sizes of the material. Grinding plays a very important role in the operation of mineral Abstract. The most common process step to feed an alumina refinery with bauxite is sizing of the raw bauxite material that is extracted from the mine. The first Physical Bauxite Processing: Crushing and Grinding of Bauxite
احصل على السعر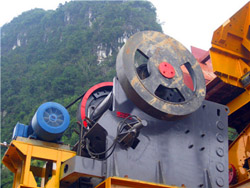
A systematic review of sustainable gold extraction from raw
Depending on the mineralogy properties of the ore, physical separation can occur at crushing sizes through optical sorting, dense media separation (DMS), jigging Grinding test shows that impact crushing has greater grinding fineness (−0.074 mm) than shear crushing, which is 42.14% and 26.18% respectively with 5 min Applications of crushing and grinding-based treatments for
احصل على السعر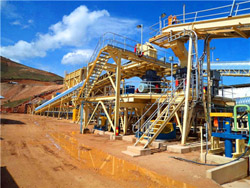
Use of drilling performance to improve rock-breakage
TS is fundamental to the crack-opening stages of crushing and BWI is an intrinsic material characteristic for the fine grinding process [23], [24]. These two parameters are inversely proportional to the energy efficiencies for crushing and grinding; higher TS and BWI require more energy, which results in lower breakage efficiencies. 2.1) Crushing and grinding of the ore 2) Concentration or benefaction of the ore 3) Extraction of crude metal from concentrated ore 4) Purification or refining of the metal (1) Crushing and Grinding of the Ore. Crushing, Grinding and Concentration of the Ore
احصل على السعر
Nuclear fuel cycle' Extractingg uranium from its ores
Crushing and grinding; Leaching; Solid-liquid separation and washing; Solvent extraction or ion-exchange, Yellow-cake precipitation and drying. The run-of-mine ore, which in some instances may be 25cm or more in diameter, is crushed and then ground to the consistency of fine sand. Since most ores being processed today contain from We notice that the studies concerning crushing or grinding have been reviewed, but mostly with other focuses, e.g., Golmohammadzadeh et al., 2017; Meshram et al., 2015) can be used as the extraction reagents. Grinding has been repeatedly adopted to improve the extraction performance towards metal ion, regardless of the LIBs type andApplications of crushing and grinding-based treatments for
احصل على السعر
Cement Extraction, Processing, Manufacturing Britannica
Extraction and processing. Raw materials employed in the manufacture of cement are extracted by quarrying in the case of hard rocks such as limestones, slates, and some shales, with the aid of blasting when necessary. Some deposits are mined by underground methods. Softer rocks such as chalk and clay can be dug directly by excavators.. The Following extraction, the ore required processing by size reduction and separation. Size reduction typically involved crushing, grinding, and screening (Balasubramanian, 2015)(PDF) Overview of Mineral Processing Methods ResearchGate
احصل على السعر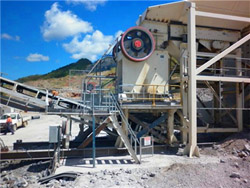
Energy Consumption in Mining Comminution ScienceDirect
Figure 6. Newell hammer mill – shredder [20]. 5. Assessing Mining Knowing the energy consumption for mining, at both the extraction stage [22] and the crushing and grinding stage, the impact of energy use in mining can start to be assessed. Figure 7 is an illustration of how this can be done using SLCA.AE processing is divided into four main stages: crushing or grinding of raw materials, extraction, centrifugal separation of different phases, and demulsification. The oil yield of AE is often lower than that of SE . Appropriate pretreatments such as steam explosion or microwave puffing would facilitate oil release in AE processing [65,70,89].Extraction of Oils and Phytochemicals from Camellia oleifera
احصل على السعر
Comminution and classification technologies of iron ore
Most of the high-grade hematite iron ores are typically subjected to simple dry processes of crushing and classification to meet the size specifications required for direct shipping ore (DSO). This involves multistages of crushing and screening to obtain lump (−31.5 + 6.3 mm) and fines (approximately −6.3 mm) products.Uranium Extraction Technology %ffij INTERNATIONAL ATOMIC ENERGY AGENCY, VIENNA, 1993 . The cover picture shows the in situ uranium central processing facility, Hobson Crushing and grinding 39 4.2.1. Introduction 39 4.2.2. Comminution theory 40 4.2.3. Grindability 41 4.2.4. Circuits and equipment 42 4.3. Beneficiation 44 4.3.1. 35 No. 9 Uranium Extraction Technology IAEA
احصل على السعر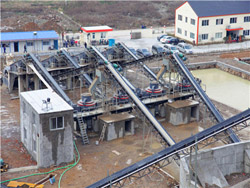
Towards waterless operations from mine to mill ScienceDirect
Typically, the bulk ore sorting is done after primary crushing on conveyor belt before intermediate stockpiles and further crushing and grinding where ore and waste rock will get mixed (Fig. 2). In case waste rock lumps are used for grinding media in SAG and AG mills the preferred location for bulk ore sorting is on the circulating loadRare-earth elements (REEs) are required for use in modern high-tech applications and demand has increased significantly over the last decade. 1 However, processing of REE ores poses potential hazards to human health and the environment due to challenges in the management of thorium (Th) and uranium (U) in waste products. 2 If Processing the ores of rare-earth elements SpringerLink
احصل على السعر
Preparation of Medicinal Plants: Basic Extraction and
The extract is separated by filtration followed by decantation. The marc is then expressed and final amount of solvent added to get required volume.[2,3,11] (vi) Soxhlet extraction. This process is otherwise known as continuous hot extraction. The apparatus is called Soxhlet extractor made up of glass.The principal ore of zinc used for its extraction is Zinc blend [Math Processing Error] ( Z n S). As Zinc blend is a sulphide ore, the process used for its concentration is the Froth Floatation Method. The concentrated ore is then roasted in excess air at [Math Processing Error] 1200 K to obtain zinc oxide [Math Processing Error] ( Z n O).Extraction of Zinc: Process, Ores, Diagram Embibe
احصل على السعر
What is the process of crushing copper ore? LinkedIn
The process of crushing copper ore typically involves a series of steps. Here is a general outline of the process: Mining: Copper ore is typically mined from an open-pit mine or underground mineTypically, separation at crushing sizes is labelled pre-concentration, during which waste material is removed during the early stage of the comminution process. Separation at grinding sizes, typically referred to as the concentration stage, is carried out with a view to producing a high-grade product (Sousa, 2020).A systematic review of sustainable gold extraction from raw
احصل على السعر
Metallurgy Definition & Process Principles of Metallurgy
Crushing and grinding of the ore. Concentration of the ore. Extraction of the crude metal. Purification of the metal. Principles of Metallurgy. The processes involved in metallurgy are as follows: Crushing and Grinding: The primary process involved in the metallurgy of metals is pulverization, which involves the crushing of ores into fineThe main process of the CIP gold processing plant to extract gold from ore and convert it into pure metal can be divided into 6 steps: crushing, screening, grinding, classification, carbon slurry gold extraction and tailings treatment. (CIP gold processing plant diagram) #1. Crushing. The raw gold ore transported to the CIP gold beneficiationHow Does A CIP Gold Processing Plant Work? Mining-pedia
احصل على السعر
Summary of Gold Extraction Process cnlitereagent
The preparation stage of ore is an essential process for gold extraction, which is mainly by crushing and grinding the ore to reduce the particle size of the ore. It can ensured that gold is present in the cyanide aqueous solution in the most economical form of recovery, thereby increasing the gold recovery rate.In the context of small-scale mining, grinding and crushing refer to two essential and common processes used to extract valuable minerals or ores from the surrounding rock or ore-bearing material.What are grinding and crushing in small scale miners?
احصل على السعر- عينة حجر سحق تقرير مشروع مصنع في الهند
- المشاكل الميكانيكيه للسيور الناقله
- مُصدِّر مناجم من الحجر الرملي
- lockpost segel untuk cone crusher
- تستخدم كسارة خام iro e Porter في ماليزيا
- الحجم في كسارة الفك
- كسارة مخروطية مقابل مطحنة الصدم
- sand equipment spiral classifier
- صيانة أمبير أمبير ثير خام الحديد
- عالية الكثافة فاصل المغناطيسي لخام الهيماتيت
- الفك محطم عملية صنع
- mafube coal mining pty ltd
- محطة كسارة الحجر في أعلى
- خطة سحق نواة produk
- وكيل كسارة الفك