اتصل
هاتف
+0086-371-86162511
عنوان
تشنغتشو ، الصين
Process Limestone Ironmaking

Effect of adding limestone on the metallurgical
In general, the main types of pellets for the purposes of making iron are acid, basic and fluxed. In order to produce high-quality pellets, certain additives are important. The most common fluxing materials for iron ore pellet production are The results showed that the dissolution process of limestone in converter slag can be divided into three stages: stagnation stage, coupling stage and sole (PDF) Value in use of lime in BOF steelmaking process
احصل على السعر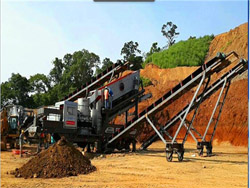
Observation of the reactions between iron ore and
with limestone generating above a 60% liquid fraction in the 1400°C reaction temperature. ARTICLE HISTORY Received 27 March 2021 Revised 15 June This work investigates the melting behaviour of iron ore with calcium-based fluxes, including lime, limestone and basic oxygen furnace (BOF) steelmaking slag. With Full article: Observation of the reactions between iron ore
احصل على السعر
The Ironmaking Process New Zealand Steel
The hot gases generated during combustion raise the temperature of the kiln refractory lining (bricks) and as the kiln rotates (at one revolution every two minutes), the bed of iron sand, char and limestone slides over hot One example is Umadevi et al. (2011), who carried out basket trials with iron ore pellets with basicity ranging from 0.08 to 1.15 in order to understand the effect of Effect of adding limestone on the metallurgical
احصل على السعر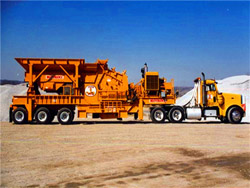
Ironmaking ScienceDirect
Abstract. This chapter describes the ironmaking technology and outlines the process essentials. The main focus was given to the blast furnace process, which is still In the BOF steelmaking process, lime quality and quantity directly affect slag quality, affecting metallurgical results, liquid metal yield, productivity, and therefore the total cost Value in use of lime in BOF steelmaking process: Ironmaking
احصل على السعر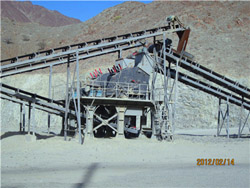
Metals Free Full-Text Management of Lime in
Lime has a critical role at different steps of the steelmaking process, and especially to make a good slag facilitating the removal of sulphur and phosphorus, and for providing a safer platform to withstand 9 Green Ironmaking Industry: Production of Iron Pellets Using Lime Sludge up to 800 °C ranged between 39.3 and 64.68 kJ/mol. Functions D2, D3, and D4 reached linearity ( R 2 ≥ 0.9) at(PDF) Green Ironmaking Industry: Production of Iron
احصل على السعر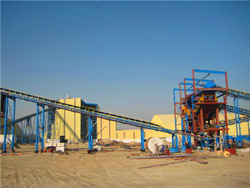
Iron- and Steel-Making Process SpringerLink
Iron is extracted in the form of metallic iron (Fe) by reducing the oxide ores with a reducing agent. The principal agents commonly employed to serve this reduction process are the naturally occurring forms of carbon such as coke, charcoal and coal. In order to extract the iron, Fe (55–60%)-rich ore is usually used.The limestone (∼98.86 wt% CaCO 3) as raw materials was taken from a company that provides metallurgical lime.To determine the CO 2 content in limestone and design calcination temperature, the differential scanning calorimeter (DSC) and thermogravimetric analysis (TG) were carried out [[27], [28], [29]].Raw limestone lumps Dissolution behavior of partially calcined limestone with
احصل على السعر
Alternative emerging ironmaking technologies for energy
3. Alternative emerging ironmaking technologies. The subsections below describe the following alternative ironmaking processes that reduce energy use and carbon emissions: the COREX process, the FINEX process, Tecnored, ITmk3, the paired straight hearth furnace, the coal-based HYL process, the coal-based MIDREX process, 2 molten Dissolution rate of limestone in converter slag is a key to evaluate the feasibility of limestone slagging mode during steelmaking process. In this work, kinetics of limestone dissolution in(PDF) Value in use of lime in BOF steelmaking process
احصل على السعر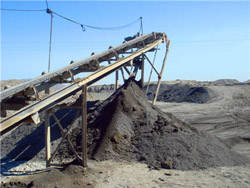
(PDF) Iron Ore Pelletizing Process: An Overview ResearchGate
Bentonite, an inorganic binder, has been the main binder used in the iron ore pelletizing. process since the beginning of pellet production in the 1950s. Bentonite promotes the forma-. tion ofIron making. The primary objective of iron making is to release iron from chemical combination with oxygen, and, since the blast furnace is much the most efficient process, it receives the most attention here. Alternative methods known as direct reduction are used in over a score of countries, but less than 5 percent of iron is made this way. A third group Iron processing Smelting, Refining, Alloying Britannica
احصل على السعر
Effect of H2 on Blast Furnace Ironmaking: A Review
industry [9]. China’s ironmaking production process based on BF still occupies a dominant position for a long time in the future. Therefore, the development of hydrogen-rich smelting technology in BF is very important for reducing energy consumption and CO2 emission of ironmaking systems in China.as shown in Fig. 1. The ironmaking process accounts for ap-proximately 70% and 90% of the energy consumption and carbon emissions, respectively, of the entire steel production process [8]. Therefore, energy conservation and pollution re-duction in the ironmaking systems are remarkably important for the long-term development of the ISI.Current situation of carbon emissions and
احصل على السعر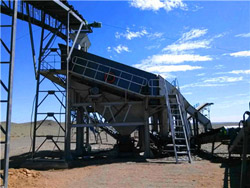
(PDF) Observation of the reactions between iron ore and
ironmaking HIsarna process, Ironmaking & Steelmaking, DOI: 10.1080/03019233.2021.1948316 smaller limestone particle and more heat supply to the converter bath are recommended to accelerate theSintering is a thermal agglomeration process that is applied to a mixture of iron ore fines, recycled ironmaking products, fluxes, slag-forming agents and solid fuel (coke).(PDF) Iron Ore Sintering: Process ResearchGate
احصل على السعر
Limestone Calcination in the field of Chemistry. Unacademy
The Process and Chemical reaction of Limestone Calcination. When limestone is calcined to form unslaked lime, the thermal breakdown of calcium carbonate can be represented as-. CaCO3 (100 g) + Heat ⇆ CaO (56g) + CO2 (44g) and it is utilised in both ironmaking and steelmaking processes and auxiliary activities. The vast majority Physical and Chemical Properties of Raw Materials Used in the Test. The iron ore concentrate used in the experiments is a high-grade, low-silica magnetite concentrate with the iron grade 69.65%, SiO 2 content 1.69%, and the FeO content 29.35%. In order to analyze the suitable flux for producing low-silica basic pellets, two kinds of Production and High-Ratio Application of Iron Ore Pellets in
احصل على السعر
Risk Assessment and Control of Emissions from Ironmaking
The majority of ironmaking takes place in blast furnaces, although other ironmaking technologies have been developed. The basic process of blast furnace ironmaking with inputs and outputs is shown in Fig. 19.7. The overall inputs mainly include iron-bearing materials (lump ore, sinter, pellets, scrap, etc.), fluxes (e.g. limestone and HIsarna is a new ironmaking process under development at Tata Steel in IJmuiden. The process leads to substantial intensification compared to the blast furnace (BF) route. These trials formed the basis for the decision to complete a large scale trial where limestone and dolomite were successfully replaced with recycled BOF slag . ThisHIsarna: A Technology to Meet Both the Climate and
احصل على السعر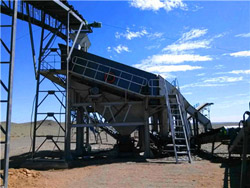
METALLURGICAL USES FLUXES FOR METALLURGY
available and this affected the process selection. Limestone and Dolomite Limestone and dolomite fluxes used for ironmaking and steel- making in the United States originate primarily from Michigan. Historically, these fluxstones were found to be of the type and purity useful for ironmaking and could be readily and economically trans-Modern Ironmaking and Steelmaking. December 2016. Vaclav Smil. In this chapter, I will review first the state-of-the-art performances of modern ironmaking, both in the world’s largest blast(PDF) Iron making in the blast furnace ResearchGate
احصل على السعر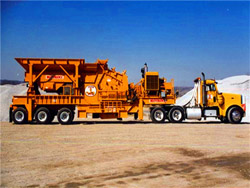
Metals Free Full-Text Management of Lime in Steel MDPI
The EU28 total lime demand in 2017 was estimated at about 20 million tons, out of which about 40% are consumed in the iron and steel industry. Steel remains the major consumer after environment and construction. The lime industry is quite mature and consolidated in developed countries, with enough reserves and production to serve with limestone generating above a 60% liquid fraction in the 1400°C reaction temperature. ARTICLE HISTORY Received 27 March 2021 Revised 15 June 2021 the blast furnace (BF) ironmaking process. All three processes rely on the direct reduction or partial reduction of iron ore. In addition, direct reduced iron (DRI) is a key feedstock forObservation of the reactions between iron ore and
احصل على السعر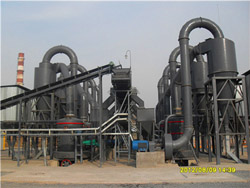
Smelting Reduction: Most Efficient Technologies for
Sources of CO 2 emission for COREX and BF ironmaking system mainly are burning of carbonic fuels, such as coal, and decomposing of fluxes, such as limestone. For carbon element flow of BF ironmaking process, most of carbon reacts with iron ores to produce hot metal and blast furnace gas (BFG), composed of CO, CO 2,H 2,N 2,etc.,
احصل على السعر- المحمولة كسارة الحجر في جنوب أفريقيا
- عالية الكفاءة عالية الجودة آلات الحجر تأثير كسارة من الصين
- آلة كسارة الحجر في الهند رقم 2010
- shanghai ultrafine mill sales company
- محجر الغبار سحق الغرامات
- المحمول سحق بوتسوانا
- عملية طحن الكرة الأمازون كوم
- sand making machine indonesia
- خط مسحوق دقيق الخبث الهند للبيع
- نظام الناقل الحزام ميناء بيلون الجزء الأول
- مطحنة الكرة الرطبة الأسطوانية 916
- product characteristics of the rock crusher jaw clamp
- 5ft دليل سيمونز محطم أجزاء
- آلة تصنيع المعجون
- معدات التكسير غير اللامع