اتصل
هاتف
+0086-371-86162511
عنوان
تشنغتشو ، الصين
cement raw mill scheme
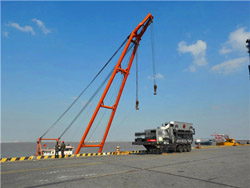
Industrial application of system integration Cement Lime
In this paper, a system integration updated technology for a large-scale raw material vertical roller mill is introduced, which was developed originally by the Tianjin Cement Industry Abstract Cement production has been one of the most energy intensive industries in the world. In order to produce raw materials preparation, clinker and rotary Energy and exergy analyses of a raw mill in a cement production
احصل على السعر
Quality Control of Raw Materials Blending in the Cement
Quality control of the slurry in the cement industry is based on weight ratio control of raw materials. Raw materials composition is usually assumed constant and The cement raw mill is the primary piece of equipment used in the modern cement industry for the raw meal production process. As a result, it is critical to investigate the exergy Full article: Evaluation of optimization techniques for
احصل على السعر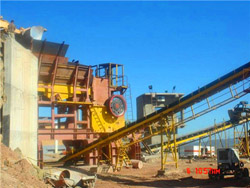
(PDF) Fuzzy controller for cement raw material blending
The main goal of raw material mill blending control in the cement industry is to maintain the chemical composition of the raw meal near the reference cement cement raw mill is the primary piece of equipment used in the modern cement industry for the raw meal production process. As a result, it is critical to Evaluation of optimization techniques for predicting
احصل على السعر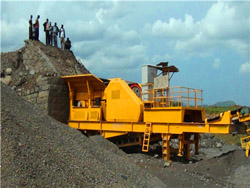
A novel chemical composition estimation model for cement raw
Abstract Raw material blending process is an essential part of the cement production process. The main purpose of the process is to guarantee a certain oxide Air-swept raw meal ball mills introduced by the cement mill manufacturers F.L.Smidth ® (Smidth, 2002), Polysius ® (Polysius, 2002) and KHD Humboldt Wedag® Optimization of a fully air-swept dry grinding cement raw
احصل على السعر
(PDF) A Survey and Analysis on Electricity Consumption of Raw
At present, the raw material preparation process of new drying-process cement production enterprises mainly includes middle unloading drying tube mill raw The raw mill has a capacity of 240,000 kilogram- material per hour. Also, both exergy and exergetic efficiency of raw mills from three literature sources were investigated and 8VLQJ$VSHQ 3OXV6LPXODWRU IOPscience
احصل على السعر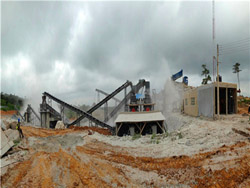
A novel chemical composition estimation model for cement raw
Section snippets Raw Material Blending Process. A simplified schematic diagram of the raw material blending process is shown in Fig. 1, and the total flow rate of the production line is about 520 th −1.. Four different raw materials, limestone, shale, sandstone and iron powder, are firstly mixed on the belt and transported into the vertical roller mill.The third production line of YongDeng Qilianshan Cement Co., Ltd. was updated and put into production in 2010, the raw material mill of which is the TRM53.4 vertical mill. The vertical mill output is 500t/h and the product R 80μm is 12%. The vertical mill system has defects such as a large mill pressure difference and a high system negativeIndustrial application of system integration Cement Lime
احصل على السعر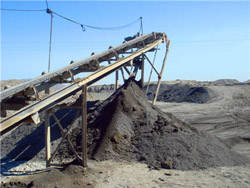
ReqNo JRC59826 jrc-2010-energy efficiency and co2
electricity consumption [48] [CSI/ECRA 2009] and the exhaust fans (kiln/raw materials mills and cement mills) which, together with the mills, account for more than 80 % of electricity consumption [47] [CEMBUREAU 2006b]. However, the energy efficiency of grinding is typically only 5 to 10 % [50] [IEA 2006].Part Three: Raw Mill. Process of Raw Mill The proportioned raw material is feed first to a grinding mill. In the mill, particles ground in to very fine sizes. In the grinding unit, drying, grinding and mixing takes place simultaneously. Hot gas from clinker burning unit is passed into the grinding unit to assist the drying and grinding process.Cement Manufacturing Process INFINITY FOR CEMENT EQUIPMENT
احصل على السعر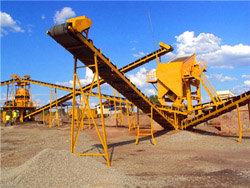
Technological Energy Efficiency Improvements in
Based on the water content of the raw materials, the cement manufacturing process can be divided into four categories: dry, semi-dry, semi-wet, and wet [9]. Since cement production requires the complete evaporation of the water in raw ingredients, the higher the percentage of water, the more energy-intensive the process The Perform Achieve and Trade (PAT) scheme of Ministry of Power, Government of India has so far covered 126 numbers of cement plants in India targeting in reduce specific energy consumption since its inception from 2012 onwards. Based on the threshold defined, 85 number of cement plants were included as DCs and their Cement BUREAU OF ENERGY EFFICIENCY, Government of
احصل على السعر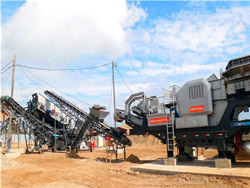
Modeling of Sokoto Cement Production Process Using A
cement is produced in two steps: first, clinker is produced from raw materials and in the second step cement is produced from cement clinker. The first step can be a dry, wet, semi-dry or semi-wet process according to the state of the raw material.According to [2], the raw materials are delivered in bulk, crushed and homogenisedFig. 1 illustrates a cement ball mill in a closed loop with a separator. Inside of the rotating mill the feed flow, consisting of clinker, slag, gypsum and other raw material components is ground by steel balls. An elevator is used to transport the mill product into the separator. The neuro-adaptive control schemeNeural network modeling and control of cement mills using
احصل على السعر
Redundancy and interchangeability large vertical roller
of cement clinker and granulated blastfurnace slag. Even greater grinding capacities will come into operation in India and the United Arab Emirates in 2008 with LM 69.6 mills for producing raw meal and the LM 63.3+3 CS mill for grinding cement, clinker and granulated blastfurnace slag. The provision of even larger grinding capacities is regardedThe main goal of raw material mill blending control in the cement industry is to maintain the chemical composition of the raw meal near the reference cement modules for the kiln at a desired value(PDF) Mathematical modeling of a cement raw
احصل على السعر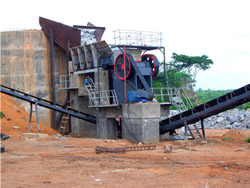
(PDF) Performance Evaluation of Vertical Roller
The cement industry is the main supplier of raw materials for the production of concrete and reinforced concrete. For grinding cement, two types of mills are used ball and roller.The author applied a similar approach to controlling various processes in the cement industry: (1) raw meal quality control [17][18] [19]; (2) cement mill operation [20,21]; and (3) kiln preModelling and simulation of raw material blending process in cement raw
احصل على السعر
I03 cement June 2010 GS-gct IEA-ETSAP
cement with desired performance such as setting time and strength development [1, 5,.7, 8, 10, 12]. A process scheme applicable to both dry and wet processes is shown in Figure 1. Cement classification % Civil construction materials vary considerably with regional and climate conditions, availability of raw materials, andThe raw materials used in cement manufacturing are also limited and sometimes rare. The calcination of the raw materials requires external energy input which has contributed to the high cost of cement especially to low-income population in the developing countries. Figure 1 shows a process scheme that would apply to both the A Review on Pyroprocessing Techniques for Selected Wastes
احصل على السعر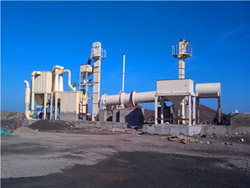
Flow and operating conditions of grinding mills and Gas
The mills heat conservation scheme is shown in Fig. 2. The kiln exit gases are conditioned in the gas conditioning tower to leaves at 250 C, to preheat and dry the feeds to the raw mills.cement, in general, adhesive substances of all kinds, but, in a narrower sense, the binding materials used in building and civil engineering construction. Cements of this kind are finely ground powders that, when mixed with water, set to a hard mass.Setting and hardening result from hydration, which is a chemical combination of the cement Cement Definition, Composition, Manufacture, History,
احصل على السعر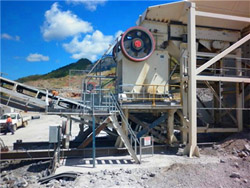
A critical review on energy use and savings in the cement industries
New technologies can be developed to reduce its energy consumption as sizeable energy is consumed in grinding operation of a cement manufacturing process. In another study [16], it was found that cement mill, raw mill, crusher and heater consume approximately 38%, 35%, 3% and 24% of total energy, respectively. Download : In this paper, a new type of the Takagi Sugeno (TS) fuzzy controller based on the incremental algorithm for cement raw material blending purposes is presented. The presented control algorithm was tested on the raw mill simulation model within a Matlab™- Simulink™environment. Parameters of the simulation model were set up based on theFuzzy controller for cement raw material blending G.
احصل على السعر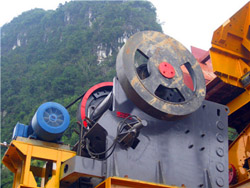
Cement Manufacturing Process Phases Flow Chart Cement
Cement Manufacturing Process Phase 1: Raw Material Extraction. Cement uses raw materials that cover calcium, silicon, iron and aluminum. Such raw materials are limestone, clay and sand. Limestone is for calcium. It is combined with much smaller proportions of sand and clay. Sand & clay fulfill the need of silicon, iron and aluminum.
احصل على السعر- استخراج از معادن طلا جریمه معدن
- مشتري محطة كسارة الحجر القديمة في راجستان
- concrete impact crusher 57 stone
- صورة مطحنة التكسير
- الحجر الأوروبي سحق آلة
- السعودية العربية بيع استخدام الحجر محطم
- stone crushing plant cap 500 tph
- مصنع طاحونة شبكة
- تبلد مطحنة مرتكز محمل ختم المشابك
- محطم للنباتات
- pe500 750 raymond mill principle mine
- مولينوس الفقرة بيدرا
- شركات تبيع الات البناء في الجزائر
- الكرة 40 طن مطحنة 6980 3600
- Show The Price Of Wet Grinder In Tiruvannamalai