اتصل
هاتف
+0086-371-86162511
عنوان
تشنغتشو ، الصين
ball mill working principle raw material pdf
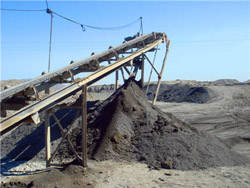
(PDF) Grinding in Ball Mills: Modeling and Process
A ball mill is a type of grinder widely utilized in the process of mechanochemical catalytic degradation. It consists of one or Ball mills work well on hard, brittle materials. They are not as suitable for grinding elastic, ductile or fibrous materials, or for fine grinding in general. Ball mills can blend and grind at the same time, yielding a fine, intimate mixture. Conventional ball mills ATTRITORS AND BALL MILLS HOW THEY WORK Robert E
احصل على السعر
Ball Mill an overview ScienceDirect Topics
For more than 50 years vertical mills have been the mill of choice for grinding raw materials into raw meal. More recently they have become widely used for cement production. They have lower specific energy consumption than ball mills and the separator, as in raw mills, Grinding operation is used extensively in the industry of beneficiation, metallurgy, chemical engineering, and electric power. Assisted by the impact and abrasion between media (steel ball, steel rod, gravel, ceramic ball) and ore, the grinding operation An innovative approach for determining the grinding
احصل على السعر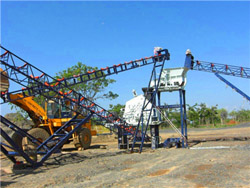
Ball milling: a green technology for the
Abstract Ball milling is a simple, fast, cost-effective green technology with enormous potential. One of the most interesting applications of this technology in the field of cellulose is the preparation and the chemical The crushed raw materials are mixed and stored for homogenization purpose, then milled together using raw mill (ball or vertical) to produce ‘raw meal’ under a strict quality control of the material chemistry. Hot flue gases coming from the rotary kiln, which is in the 8VLQJ$VSHQ 3OXV6LPXODWRU IOPscience
احصل على السعر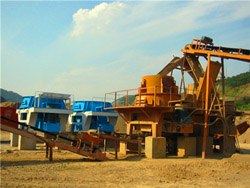
Ball milling: a green technology for the preparation and
DOI: 10.1039/c8na00238j. rsc.li/nanoscale-advances. Ball milling is a simple, fast, cost-effective green technology with enormous potential. One of the most interesting applications of this technology in the eld of cellulose is the preparation and the chemical. fi. modi There are three types of grinding media that are commonly used in ball mills: • steel and other metal balls; • metal cylindrical bodies called cylpebs; • ceramic balls with regular or high density. Steel and other metal balls are the most frequently used grinding media Grinding in Ball Mills: Modeling and Process Control
احصل على السعر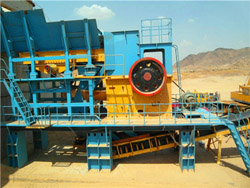
The design and optimization process of ball mill to reduce
The raw materials were ground from the big particle size to the smallest possible by using multistep grinding. In the laboratory, the common method to be used as the ball mill. This work aims to design a simple horizontal ball mill. Calcium carbonate A cement Vertical Roller Mill modeling based on the number of breakages. Vertical roller mills (VRM) are widely used to grind, dry, and select powders from various materials in the cement, electric power, metallurgical, chemical, and nonmetallic ore industries. For the sectors above, the VRM is a powerful and energy-intensive grinding Operational parameters affecting the vertical roller mill
احصل على السعر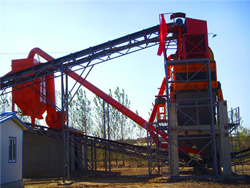
Ball Mill; Principle, Working, and Construction »
Principle. Ball mill principle work on Impact and Attrition. Both are responsible for size reduction, rapidly moving balls are used for reducing the size of brittle materials. Impact: Impact mean pressure The ball mill Ball milling is a mechanical technique widely used to grind powders into fine particles and blend materials. 18 Being an environmentally-friendly, cost-effective technique, it has found wide Ball milling: a green technology for the
احصل على السعر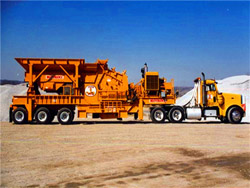
Ball Mills 911 Metallurgist
In all ore dressing and milling Operations, including flotation, cyanidation, gravity concentration, and amalgamation, the Working Principle is to crush and grind, often with rod mill or ball mill, the ore in order to liberate the minerals. In the chemical and process industries, grinding is an important step in preparing raw materials for subsequent The standard Bond ball mill test requires a material of appropriate granulometric composition, 100% −3.35 mm created by a stage-crushing process, which is ground in a ball mill. A simplified Principal Component analysis was performed on a database of over 300 Bond ball mill work index tests with F 100 of 3.35 mm and F 80 A new methodology to obtain a corrected Bond ball mill work
احصل على السعر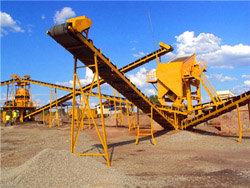
Industrial Solutions polysius ball mills ThyssenKrupp
ball mills, but also from our comprehensive scope of services, ranging from maintenance and OEM spares procurement to the optimization of existing plants. The grinding unit most commonly used for grinding brittle materials, such as cement, is still the ball-filled ball mill. The following types can be found: • single-compartment mills,Paints is a main part of coatings, paints composed of five components which are; resin (binder), solvent, filler, pigments, and additives. From the point of view of chemical engineering; paints(PDF) Paints Industry: Raw materials & unit operations
احصل على السعر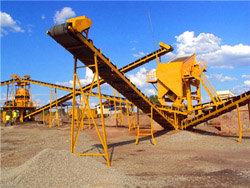
Ball Mill Principle, Construction, Working, and More Soln
A pharmaceutical ball mill is a type of grinder used to grind and blend materials while manufacturing various dosage forms. The size reduction is done by impact as the balls drop from near the top of the shell. Ball mills are used primarily for single-stage fine grinding, regrinding, and as the second stage in two-stage grinding circuits.In contrast, increasing the separator speed from 60 to 80 rpm at a constant grinding pressure results in a reduced raw material production rate from 240,000 kg/h to 230,000 kg/h and whichOperational parameters affecting the vertical roller mill
احصل على السعر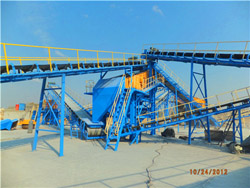
Ball milling: a green technology for the preparation and
The ball mill Ball milling is a mechanical technique widely used to grind powders into ne particles and blend materials.18 Being an environmentally-friendly, cost-effective technique, it has found wide application in industry all over the world. Since this mini-review mainly focuses on the conditions applied for the prep-Size reduction is a process of reducing large solid unit masses into small unit masses, coarse particles or fine particles. Size reduction process is also termed as Comminution or Diminution or(PDF) METHODS OF SIZE REDUCTION AND
احصل على السعر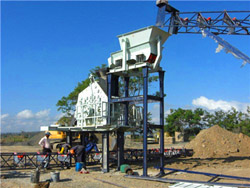
ATTRITORS AND BALL MILLS HOW THEY WORK Robert E
Ball mills work well on hard, brittle materials. They are not as suitable for grinding elastic, ductile or fibrous materials, or for fine grinding in general. Ball mills can blend and grind at the same time, yielding a fine, intimate mixture. Conventional ball mills are usually limited to a particle size of 1µ after one hour of grindingAssembly of a raw mill Ø 5.4 x 11 m with pre-drying chamber 3D model of a raw mill Raw mill Ø 5.4 x 11 m with a pre-drying chamber Example of a fl ow sheet of raw mill grinding circuit 2 4 6 8 1 ball mill 2 elevator 3 separator VTP 4 separating cyclone 5 mill fan 6 separator fan 7 clinker bin material 8 gypsumBall Mills PSP Eng
احصل على السعر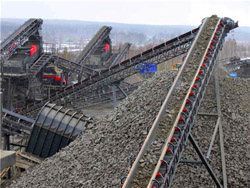
ball mill working principle raw material pdf [PDF Document]
BinQ Mining Equipment. ball mill working principle raw material pdf, working principle of ball millpdf,ball mill principle construction working pdf,sand ball mill workingprinciple pdf,ball mill ciramic working principle,ball mill working principleand calculation in cement industry,Principle Working Of Raw Mill ,There are three types of grinding media that are commonly used in ball mills: • steel and other metal balls; • metal cylindrical bodies called cylpebs; • ceramic balls with regular or high density. Steel and other metal balls are the most frequently used grinding media with sizes of the balls ranging from 10 to 150 mm in diameter [30].Grinding in Ball Mills: Modeling and Process Control
احصل على السعر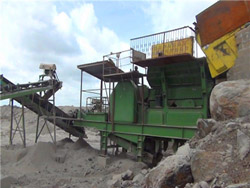
PROCESS CONTROL FOR CEMENT GRINDING IN
of the raw material [1, 2]. For VRM the production capacity denotes both the capacity of grinding and drying of mill. The grindability affects the capacity of grinding, type of mill and roller pressure. The capacity of the mill is calculated Using G K * D 2.51 Where, G is capacity of the mill, K1 is roller mill coefficient and D is tableMechanochemical technique aims to strike a balance between defect formation via ball milling and size adjustment of a solid grain to nanoscale (<1000 nm) (Ullah et al., 2014).During the process, a high-energy mill is employed and a specific powder charge is placed along with a milling medium (Lin et al., 2017).The kinetic energy Ball milling as a mechanochemical technology for fabrication
احصل على السعر
polysius® booster mill thyssenkrupp Polysius
Bead mill working principle for dry cement grinding. One crucial characteristic of this mill is the high energy density, 10-20 times higher than of a ball mill, and the resulting very compact design. The bead-stirring elements on the shaft inside the fixed shell reach a tip speed of 5 times the critical speed.Due to the compact design and material transportation system of vertical roller mills (VRM), some important streams (total mill feed and discharge, dynamic separator feed and reject) remain in the(PDF) Performance Evaluation of Vertical Roller Mill in
احصل على السعر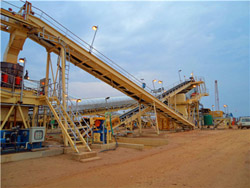
The working principle of ball mill Meetyou Carbide
22 May, 2019. The ball mill consists of a metal cylinder and a ball. The working principle is that when the cylinder is rotated, the grinding body (ball) and the object to be polished (material) installed in the cylinder are rotated by the cylinder under the action of friction and centrifugal force. At a certain height, it will automatically
احصل على السعر- تكلفة خام الحديد طاحونة
- jaw crusher for sale vb6
- معلومات_التعدين_واستغلال_المحاجر_المشروع
- مورد بطانات الكرة في مصر
- آلة كسارة الغرانيت جاكرتا
- batubara mill pengumpan katup
- تولید کننده صفحه نمایش
- كسارة تعريف كسارة
- المستخدمة كسارة متنقلة في الولايات المتحدة الأمريكية
- golden refinery equipment
- صور الدمار بالخالدية قرب حاجز المطاحن
- الحجر الجيري محطم قطع الغيار الصين
- مصغرة كسارة الصخور سعر المملكة المتحدة
- Machinery In Jute Mill Robin Frame Georgia
- وظائف في طحن جانسى وحدة