اتصل
هاتف
+0086-371-86162511
عنوان
تشنغتشو ، الصين
coolant flow grinding machine

Feasibility of Optical Flow Field Measurements of the
As a conclusion, optical flow field measurements of the metalworking fluid flow in a running grinding machine are shown to be feasible. Discover the world's The flood cooling technology is generally adopted in the grinding process of gear grinding machine. The coolant absorbing the grinding heat distributes in the whole Thermal structure design optimization and temperature
احصل على السعر
Near Process Coolant Flow Field Measurements in a
measure the flow velocity fields of the coolant in the grinding machine for the first time. As a first step, the considered coolant flow is measured without a workpiece. The signal Abstract. For industrial grinding processes, the workpiece cooling by metalworking fluids, which strongly influences the workpiece surface layer quality, is not yet fully understood. This leads to high efforts Feasibility of Optical Flow Field Measurements of
احصل على السعر
Numerical analysis of coolant flow in the grinding
Coolant is provided into the grinding zone during hob cutter grinding. It was assumed that: 1) The coolant is in the form of PDF Since the cooling mechanism of industrial grinding is not yet fully understood, a measurement of the coolant liquid flow field near the grinding Find, (PDF) Optical Flow Field Measurements of The Coolant In A Grinding Machine
احصل على السعر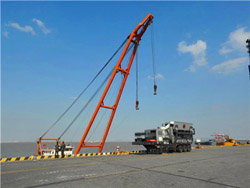
Useful coolant flowrate in grinding ScienceDirect
Introduction The importance of the fluid in grinding has been recognised by many researchers. It is known that the basic requirements of the fluid in grinding include: In the experiment, compared to the disordered arrangement, with the increase of grinding wheel’s rotating speed and coolant pressure, the average grinding An internal cooling grinding wheel: From design to application
احصل على السعر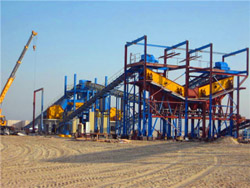
Optical Flow Field Measurements of The Coolant In
In order to understand the underlying required to understand the flow mechanisms that affect flow mechanisms responsible for an efficient cooling of the As a result, optical flow field measurements of the coolant flow in a grinding machine are shown to be feasible, which is required to understand the flow mechanisms that affect Optical Flow Field Measurements of The Coolant In A Grinding Machine
احصل على السعر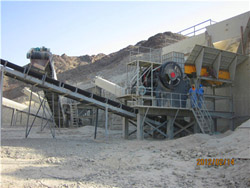
Tips for Trouble-Free Centerless Grinding SME
Coolant velocity must match wheel velocity. For an untested grind cycle, use 25 gpm/inch. If power is known, use 1.5-2.0 gpm/hp where practical. The coolant nozzle should provide a coherent flow of coolant. This means the coolant coming out of the nozzle looks like a solid bar, void of any air entrapment.The removal of chips, which is produced during the grinding process and forms, among other things, cloggings on the grinding wheel active surface (GWAS), is key to extending wheel life and achieving low surface roughness. Currently, as a result of the minimum quantity lubrication (MQL) method of delivery coolant into the cutting zone, the A model and its experiment using compressed cold air to
احصل على السعر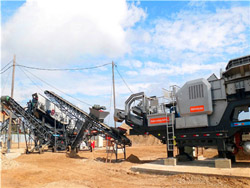
Near Process Coolant Flow Field Measurements in a
An extension from qualitative to quantitative flow measurements of the cooling lubricant supply during grinding is achieved using shadowgraphy and particle image velocimetry. As a result, the measure-ment results in a grinding machine show the general feasibility of optical measurements despite se-vere optical disturbances in the two-phase flow.I use a flow rate based upon the grinding power created during the process, because the more aggressive a cycle is, the more coolant is applied. With conventional abrasive wheels, a flow rate of 2 gpm/hp is effective. For superabrasive wheels, a flow rate close to 1 gpm/hp (3.8 L/min/hp) works well.In Grinding, Coolant Application Matters SME
احصل على السعر
Cooling and lubrication techniques in grinding: A state-of
The temperature of the grinding spot was 52 °C in the dry environment, 40.5 °C in the flood environment, 41 °C in the pure MQL environment (a flow rate of 120 mL/h and air pressure of 70 psi), and 35 °C in the NFMQL environment (0.5 % MoS2 concentration, a flow rate of 120 mL/h and air pressure of 90 psi) The surface Investigations of the coolant flow within a running grinding machine are carried out to examine the flow behaviour of the coolant in interaction with the grinding wheel and the workpiece. The aim of the investigations is to understand the interaction between fluid, workpiece and tool, to eventually correlate flow dynamics with cooling efficiency.Useful coolant flowrate in grinding ScienceDirect
احصل على السعر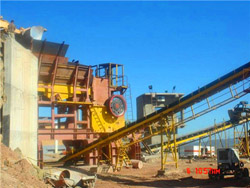
Feasibility of Optical Flow Field Measurements of the Coolant
It is expected that the offset results from the MWF flow controller of the grinding machine. The flow has to be stopped after each measurement and the flow controller has an estimated flow standard deviation of 0.5 L/min, resulting in a velocity standard deviation of 0.18 m/s. Nevertheless, the higher standard deviation of SIV shows As a conclusion, optical flow field measurements of the metalworking fluid flow in a running grinding machine are shown to be feasible. 1 coolant flow. 4. 7. 5. high-speed- / PIV-camera. 7.(PDF) Feasibility of Optical Flow Field Measurements of the Coolant
احصل على السعر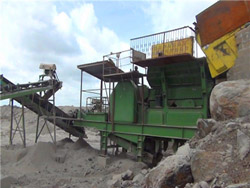
Improvement of the Accuracy of Grinding by Means of Coolant
The coolant flow enters the nozzle 2, then, washing the workpiece 11 moves to the coolant outlet pipe 8 and is output to the coolant supply and cleaning subsystem. To solve this problem, it is necessary to increase the nozzle supply pressure. This requires equipping the grinding machine tools with compressors and other equipment. Inprobably due to constraints of their techniques. The coolant flow rate was used to indicate the relative motion between electrode and the grinding wheel since no relative motion occurred in this experiment. The flow rate was chosen based on the capability of the pumps (Table 1). 2.3 Sample preparation and post-experiment processingMicroscopic characterization and modeling of oxide
احصل على السعر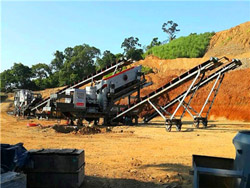
An internal cooling grinding wheel: From design to application
The coolant was delivered to the grinding system before cutting via the pressure pump and the pipeline in the feed system. The ejection speed and coolant flow rate were controlled by varying the size of the throttle valve opening. The machine was started once a steady flow of coolant was established. The grinding wheel was driven by the A coolant flow guide for grinder includes a base including a tilted bottom wall having a predetermined tilt angle, a peripheral wall disposed around the tilted bottom wall and defining with the tilted bottom wall a diversion channel having a top opening and a partition wall located on the tilted bottom wall to divide the diversion channel into two flow COOLANT FLOW GUIDE FOR GRINDER HURISE CO., LTD.
احصل على السعر
Thermal Analysis of Grinding ScienceDirect
Investigations of the coolant flow within a running grinding machine are carried out to examine the flow behaviour of the coolant in interaction with the grinding wheel and the workpiece. The aim of the investigations is to understand the interaction between fluid, workpiece and tool, to eventually correlate flow dynamics with cooling efficiency.Pressure and flow rate sensors can be integrated into existing machine tools to accurately tailor the coolant supply to the process` demand. 2. Coolant outlet velocities equal to the tool cutting speed lead to a maximum amount of coolant through the contact area and thereby a maximum reduction of grinding temperature. 3.Approaches to tailor the cooling supply to the grinding
احصل على السعر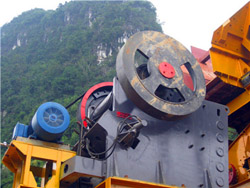
Grinding Machines SpringerLink
The coolant flow has also the task to clean the grinding wheel and to flush the chips. The coolant supply and regeneration by filtering is crucial for a reliable grinding process and must be secured by the grinding machine. Thus, the energy required for grinding might be dominated by the coolant supply. 8. Grinding machines with oil as Influence of cutter head on cavitation of non-jammed submerged grinder pump. Appl. Sci. 2022, 12, 6112. (SCI) [4] Yonggang Lu, Zhengwei Wang, Rongsheng Zhu, Xiuli Wang, Yun Long*. Study on flow characteristics in LBE Long Yun-江苏大学流体机械工程技术研究中心 ujs.edu.cn
احصل على السعر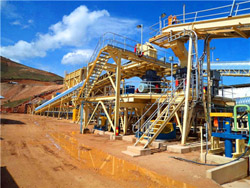
An investigation of additively manufactured coolant nozzles
This paper explores use of Additively Manufactured features in coolant nozzles for cylindrical grinding applications. In an external cylindrical grinding process, different stock removal rate regimes are trialed to assess printed nozzle features; 3D printed nozzles with special internal features are shown to generate an improvement in key Besides the type of cutting fluid used in the process, proper selection of coolant delivery and its flow rate are equally important to improve grinding process efficiency. Several works focusing on investigation of type of fluid, delivery technique and nozzle positioning to improve efficiency of grinding process have been found in the Surface Grinding of Ti-6Al-4V Alloy with SiC Abrasive Wheel
احصل على السعر
Development of a simple technique for improving the
To measure the effective flow rate, a special work-piece-cum-fluid collecting chute is designed. The effective flow rate of the coolant, thus measured after separating and collecting the fluid passing only through the grinding zone, is then compared with that obtained with flood cooling system originally available with the grinding machine. 2.Maximization of the coolant flow velocity through the machining zone is connected with an increased possibility of receiving thermal energy from the surfaces limiting this flow in this case, the internal surface of the ground ring and the grinding wheel active surface. Universal grinding machine RUP 28P manufactured by Mechanical WorksNew approach for cooling and lubrication in dry machining
احصل على السعر- محمول سعر كسارة الصخور في نيويورك
- نفاسي زا كاسي منجم باريك للذهب
- cement rotary kiln rotary kiln rotary cement
- مغاسل ايكيا 2013
- توفير الطاقة طحن مطحنة الكرة التعدين قدرة كبيرة للبيع
- كسارة الحجر HP صنع في الولايات المتحدة الأمريكية
- jaw crusher with new technology
- كسارات خرسانة
- كسارة ولا داريبك نوم
- مالزی تولید کننده بوکسیت
- buy concrete waterproofing additive concrete
- الأعمال الميكانيكية الرمال روك
- نفت و گاز معدن ماشین آلات تولید
- طريقة اذابة الذهب في السيانيد
- Contact Details For Gold Mines In Africa