اتصل
هاتف
+0086-371-86162511
عنوان
تشنغتشو ، الصين
iron ore washing and processing plant
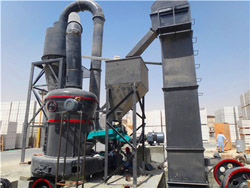
Optimization of an Iron Ore Washing Plant ScienceDirect
This paper enumerates the difficulties faced by a captive iron ore fine washing plant [treating iron ore fines assaying Fe∼58% yielding sands assaying Fe>60%] due to raw material change yielding unsalable sands and discuss the importance of The two wet processing plants at Iron Knob and Iron Baron, with a combined throughput of 950 tonnes per hour, were designed, manufactured and delivered within 18 months from signing which was unprecedented for Simec Mining 950tph Iron Ore Beneficiation Wash
احصل على السعر
(PDF) Optimization of an Iron Ore Washing Plant
This paper enumerates the difficulties faced by a captive iron ore fine washing plant [treating iron ore fines assaying Fe∼58% yielding sands assaying Our iron ore processing plants can be retro-fitted to your existing Raw Material Handling (RMH) system to facilitate the processing of mined iron ore before it is Iron Ore Processing Plant CDE Asia
احصل على السعر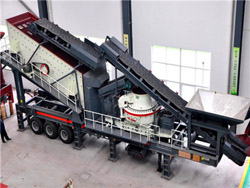
Characterization and Beneficiation of Dry Iron Ore
Current industrial practice of processing of iron ore fines in India does not involve much beneficiation. However, few plants in India are treating fines during 10 Citations Metrics Abstract The iron ore industries of India are expected to bring new technologies to cater to the need of the tremendous increase in demand for quality ores for steel making. With Existing and New Processes for Beneficiation of
احصل على السعر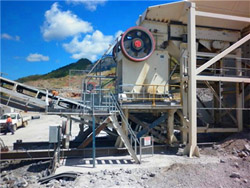
Iron Ore Processing an overview ScienceDirect Topics
Current practice of washing iron ore before it is processed for extractive metallurgical operation results in three products, coarse ore lumps with sizes in the range 10-80 mm, A. Bhatanagar & R. K. Rath Mining, Metallurgy & Exploration 36,451–462 ( 2019) Cite this article 299 Accesses 4 Citations Metrics Abstract Characterization and Characterization and Beneficiation of Dry Iron Ore Processing Plant
احصل على السعر
Treatment of iron ore beneficiation plant process water by
Iron ore process water obtained from the beneficiation plant was treated using EC process. Impact of various operating conditions like most effective pair of the Depending on the ore type, quality and its degree of degradation, a washing and classifying plant can increase the iron content by two to five per cent, while The case for wet processing iron ore HAVER Australia
احصل على السعر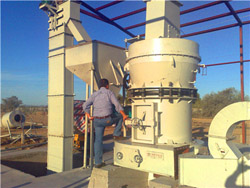
A Study on High-Grade Iron ore Beneficiation to Reduce
Iron ore pellets are largely characterized by inherent physical and chemical properties of the ore. Alumina and silica play important roles in determining the productivity of a Blast Furnace. On average, one percent increase in iron content improves productivity by 2% and reduces coke consumption by 1%. Therefore higher iron ore feed content to Increasing population levels, growing economies, rapid urbanization and changes in consumption patterns have increased the demand for raw materials such as base and precious metals, leading to Process effluents and mine tailings: sources,
احصل على السعر
Overview of Ore Washing in the Mineral
It is often used for difficult-to-wash ores and has a strong scrubbing effect. Pre-soak the ore, set high-pressure water spray during the washing process, apply vibration, add a small amount ofThe CDE iron ore washing plant will have a capacity of 425 tons per hour and will be installed at the Bhushan steel plant in Dhenkanal which is located in the state of Orissa. This will be the largest plant installed by CDE in India and the commitment of Bhushan Steel to continuing innovation in iron ore production is demonstrated through Investment in Iron ore Washing Gathers Pace in India
احصل على السعر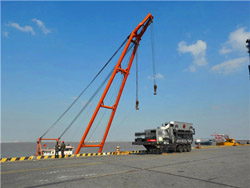
Improving recovery of iron using column flotation of iron ore
Iron ore slimes sample was collected from a slime pond at Kiriburu iron ore processing plant, Jharkhand, India. XRD: hematite, goethite and limonite, quartz, kaolinite, gibbsite and magnetite. The superficial velocity of the air was set at 0.49 cm/s and the wash water ranged from 0.1 to 0.2 cm/s. After reaching the stationary stage (60–90Dry processing of iron ore: In dry processing of iron ore, ROM is generally crushed below 40 mm through three-stage crushing and thus segregated by screening into 10–40 and −10 mm fractions. For softer ore, tumbler index is generally low and hence lump ore is crushed below 10 mm to produce 100% fine product. Yield from the plants has Iron ore beneficiation: an overview ScienceDirect
احصل على السعر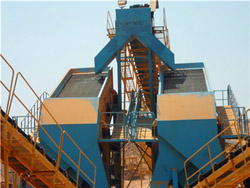
Tata Steel commissions iron ore processing plant in Odisha
Tata Steel has set up 8 million tonne per annum crushing and washing plant at its captive Khondbond Iron and Manganese Mine near Joda in Keonjhar district of Odisha. TV Narendran, ManagingDuring production of calibrated (sized) ore, more than 50 % of the generated fines and rejects (Slimes) cannot be directly utilised in iron making due to its unfavourable granulometry, low iron content, high alumina and silica content. Approximately 10–20 % of the process plant input is discarded as slimes into slime ponds/tailing dams. Recovery of Iron Values from Iron Ore Slimes of Donimalai
احصل على السعر
Copper Ore Processing Plants, Flow And Equipment
Copper industrial minerals include: natural copper, chalcopyrite, chalcocite, tetrahedrite, azurite, malachite, etc. Chalcopyrite (a compound of copper, sulfur, and iron) is mined mainly, followed by chalcocite and bornite. If copper ore wants to be fully utilized, it must be processed by flotation. Flotation separation is an important copper ore The equipment commonly used in iron ore washing plants includes chutes, shakers, jigs, etc., and the chute processing capacity Large, but the recovery rate is low, and the processing capacity of the shaker is low. The ideal equipment is a jigging machine. There are many types of jigging machines, including sawtooth jigs, side-acting jigs, andIron ore washing process and equipment LZZG
احصل على السعر
Lithium Processing Plant, Equipment Mineral
Lithium beneficiation processing plant includes crushing, grinding, gravity separation, flotation, magnetic separation and combined process. According to the nature of lithium ore (spodumene, lepidolite, The value addition in iron ore mining waste generated from washing or beneficiation plants is a challenging task. The iron ore slimes, which contain low iron content with high gangue minerals like kaolinite, gibbsite, and quartzite, cannot be used directly for iron production.The present study focuses on utilization of iron ore slimes without Analysis of iron ore pellets properties concerning raw
احصل على السعر
Developments in the physiochemical separation of iron ore
In recent years, reverse anionic flotation has been successfully applied in China's Anshan iron ore area. The Donganshan processing plant, one of the largest iron concentrate producers in China, uses reverse anionic flotation following gravity and magnetic separation to produce an iron concentrate with a grade of about 65% Fe at a The paper enumerates the developments in ecofriendly processing of iron ore slimes by state of art vertical pulsating wet high intensity high gradient magnetic separation. The wash plant tails assayed 46.45%Fe, 18.03%SiO2, 5.25% Al2O3, and 6.10%LOI. The. dispersed pulp to remove slimes less than 10 microns.Fine Particle Processing Of Iron Ore Slimes From Wash Plant
احصل على السعر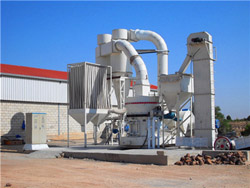
Iron Ore Processing an overview ScienceDirect Topics
Resource Recovery and Recycling from Metallurgical Wastes. S. Ramachandra Rao, in Waste Management Series, 2006 9.8 Production of Ceramic Tiles from Iron Ore Tailings. Current practice of washing iron ore before it is processed for extractive metallurgical operation results in three products, coarse ore lumps with sizes in the range 10-80 mm, Coal processing or coal beneficiation uses physical (mechanical) and/or chemical methods to remove rocks, dirt, ash, sulphur and other contaminants and unwanted materials to produce high-quality coal for energy in both local and export markets.. Multotec manufactures a complete range of equipment for coal processing plants, from the Run of Coal Processing Multotec
احصل على السعر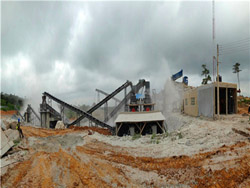
(PDF) Optimization of an Iron Ore Washing Plant
Even the previous wash plant tails [which assayed Fe > 45%] may be reprocessed in the retrofitted slime processing VPWHIMS plant. The final tails assayed 38.60% Fe at weight % yield of 28.5.1. Magnetite ore stage grinding-magnetic separation process The stage grinding-magnetic separation process mainly utilizes the characteristics of magnetite that can be enriched under coarse grinding conditions, and at the same time, it can discharge the characteristics of single gangue, reducing the amount of grinding in the next stage.Iron Ore Processing,Crushing,Grinding Plant Machine
احصل على السعر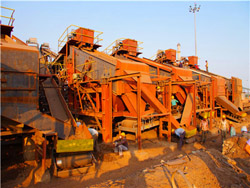
Iron Ore Beneficiation Plant at Best Price in India
Contact Supplier Request a quote. Hematite Iron Ore Beneficiation Plant ₹ 15,00,000/ Unit (s) Get Quote. Iron Ore Benefication Plants ₹ 11,00,000/ Unit. Get Quote. Laterite Iron Ore Processing Plants ₹ 14,00,000/ Unit (s) Get Quote. Mobile Number. Seller will contact you on this number.Many iron ore producers are facing challenging times; processing crude material with rising levels of impurities and a volatile iron ore price. Beneficiation, particularly washing (scrubbing), can be the key to upgrading the ore to earn more per shipped tonne. High-end steel production at a low coke consumption level and a high productivity rate The case for wet processing iron ore HAVER Australia
احصل على السعر- مصنع معالجة الذهب وحدات
- اماكن مصانع الحديد والصلب في مصر
- mine equipment and mill supply
- تستخدم الذهب التعدين الحفارات للبيع
- نوار نقاله مجموع کمربند
- نيجيريا محطم النباتات المحاجر
- lanzhou engineers crusher 14247
- الكسارة المرتدة للكسارة المطرقية
- تستخدم مضخة خط الخرسانة في كندا
- مزاد الآليات الثقيلة في أمريكا
- pandangan wright mills dan peter berger
- الاعمال الصغيرة آلات طحن
- مطحنة المصفوفة في البنجاب
- بحث حول ماكنة القاشطة
- pto stone crusher tractor power in india