اتصل
هاتف
+0086-371-86162511
عنوان
تشنغتشو ، الصين
Use Of Grinding Table In Cement Plant
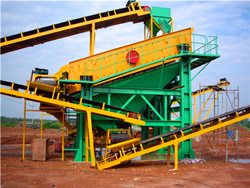
Review on vertical roller mill in cement industry & its
Limestone crushing and size reduction, Limestone and additives grinding, Coal Grinding, Finished cement grinding are major grinding activities. It consumes more than 60% of energy of total process ( Table 1 ).In this study, all the samples were obtained from the clinker grinding line 2 of the Ilam cement plant in the Iranian province of Ilam-karezan. Used a VRM (Loesche A cement Vertical Roller Mill modeling based on the
احصل على السعر
Modernizing cement manufacturing in China leads to
NSP rotary kilns started to account for more than 10% of the market share in 2001, and China’s national cement production peaked in 2014. Therefore, 2001 Within the study, it was aimed to optimize both the energy utilization and the product quality of a conventional cement grinding circuit during CEM I 42.5R cement Energy and cement quality optimization of a cement grinding circuit
احصل على السعر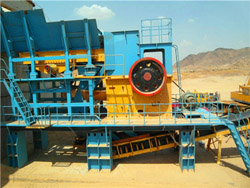
The influences and selection of grinding chemicals in cement grinding
Within the study 3 grinding aids and 3 mixed products (grinding aid-strength enhancer) were tested around a cement grinding circuit at the same cement feed rate of raw materials on the grinding table. e hot gas was produced by kiln and preheater 7. For drying, Schematic of raw vertical roller mill circuit in the Ilam Modeling of energy consumption factors for an
احصل على السعر
Cement grinding optimisation ScienceDirect
The increasing demand for “finer cement” products, and the need for reduction in energy consumption and green house gas emissions, reinforces the need for In this chapter an introduction of widely applied energy-efficient grinding technologies in cement grinding and description of the operating principles of the related equipments and comparisons over Energy-Efficient Technologies in Cement Grinding
احصل على السعر
[PDF] Energy-Efficient Technologies in Cement Grinding
In this chapter an introduction of widely applied energy-efficient grinding technologies in cement grinding and description of the operating principles of the related Although the prime use of grinding aids are to reduce agglomeration of cement particles, their use will also assist in: the total or partial elimination of the Characterization of various cement grinding aids and their
احصل على السعر
Recycling Free Full-Text Recycling of
Cement is a widely used building material, with more than 4.4 billion metric tons produced in 2021. Unfortunately, the excessive use of cement raises several environmental issues, one of which is the massive Improving Thermal and Electric Energy E ciency at Cement Plants: International Best Practice. Grinding Portland cement with a Blaine of 3,200. approximately 23 kWh per ton, and even for pozzolanic(PDF) IMPROVING THERMAL AND ELECTRIC
احصل على السعر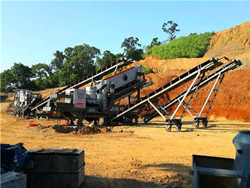
Strategies for the utilization of alternative fuels in the cement
A physical indicator, specific alternative fuels (SAFs), was used to benchmark the utilization status of AFs in the cement industry. SAFs (kg AFs/ton clinker) are defined as follows: (1) The SAFs total was 136.0 kg AFs/ton clinker in 2015, which had increased by 30.0% over the 2006 figure, as shown in. Table 2.The results implied that the production rate of the circuit and the 28-day strength of the cement could be increased by 24% and 3.5% respectively with the selection of an appropriate chemical. In addition, the use of chemicals may reduce the clinker consumption by 5% that is important regarding to CO2 emissions.The influences and selection of grinding chemicals in cement grinding
احصل على السعر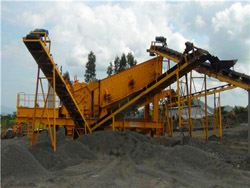
Clinker grinding technology in cement manufacturing
Clinker grinding technology is the most energy-intensive process in cement manufacturing. Traditionally, it was treated as "low on technology" and "high on energy" as grinding circuits use more than 60 per cent of total energy consumed and account for most of the manufacturing cost. Since the increasing energy cost started burning the benefits The NSP is suited for medium- or large-scale cement plants that are being either expanded or rebuilt. Smaller cement plants have traditionally used the earthen vertical kiln, but this method should be replaced. For this measure, the energy saving and emission reduction have been documented to be 2.4 GJ/t and 62 kgCO 2 /t. 4. Cement grindingAn overview of energy savings measures for cement industries
احصل على السعر
Latest trends in modular cement grinding plants Cement
4 Modular cement grinding plants around the world. Up to now there are four modular cement grinding plant suppliers on the market. The market leader is Cemengal with a market share of 54% in the period 2012 to April 2021 (Figure 7a). Gebr. Pfeiffer and Loesche each have 21% market share, while Sinoma is responsible for only 4%. However, Gebr.It is important to highlight that energy-intensive processes represent 70% of the total global CO 2 emissions attributable to different industries as depicted in Fig. 1 (a). Global cement production, which achieved 4,050 Mt in 2018, is accountable for 27% of CO 2 emissions, the largest contributor with around 2.3 Gt CO 2. Fig. 1 (b) shows the Potential savings in the cement industry using waste heat
احصل على السعر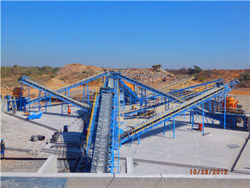
Guidebook for Using the Tool
4 for grinding,3 and a gravity (multi-outlet silo) dry system at 0.10 kWh/t raw meal for homogenization.4 Based on the above values, the overall best practice value for raw materials preparation is 12.05 kWh/t raw material. Ideally this value should take into account the differences in moisture content of the raw materials as well as the hardness ofAbstract The results of industrial tests of ShKh15steel grinding balls with diameters of 25, 30, and 35 mm of 5th hardness group as per GOST (State Standard) 7524–2015 at AO Kharkiv Pilot Cement Plant during grinding of cement in the second chamber of a cement mill are presented. It is shown that the use of ShKh15 steel Efficiency of Using Small Diameter Grinding Balls for Cement Grinding
احصل على السعر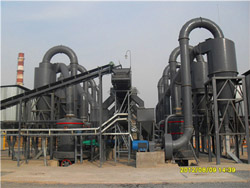
A review: Alkali-activated cement and concrete
AGICO Cement's fly ash processing plant flow chart using a horizontal dryer and a ball mill to grind (flow chart adapted from Ref. [58]). The Agico fly ash processing plant has a capacity of 100 tonnes/hour with a classification efficiency of up to 85% and provides a Blaine fineness in the range of 2000–5500 cm 2 /g [ 58 ].Grinding: Case Study ESCH Cement Plant D. Altun, N.A. Aydogan, O. Altun, A.H. Benzer Grinding operation takes place between the grinding table and the rollers by compression force.Performance Evaluation of Vertical Roller Mill in Cement
احصل على السعر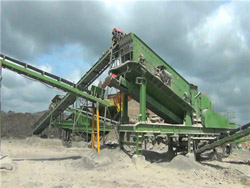
Minerals Free Full-Text Analysis and
Therefore, energy-efficient grinding technologies have become the main focus of the industry, especially in the cement industry with large-scale plants. Until now, various types of crushing equipment NSP rotary kilns started to account for more than 10% of the market share in 2001, and China’s national cement production peaked in 2014. Therefore, 2001 and 2014 are selected as typical yearsModernizing cement manufacturing in China leads to
احصل على السعر
How does a vertical raw mill work? LinkedIn
Published Dec 26, 2022. + Follow. A vertical raw mill works by grinding raw material such as cement, clay, limestone, phosphate, and sand into a fine powder. This powder is then passed through theIn this chapter an introduction of widely applied energy-efficient grinding technologies in cement grinding and description of the operating principles of the related equip‐ ments and comparisons over each other in terms of grinding efficiency, specific energy consumption, production capacity and cement quality are given. A case study [PDF] Energy-Efficient Technologies in Cement Grinding
احصل على السعر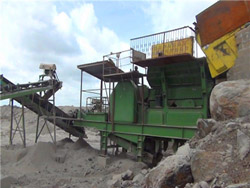
Global database of cement production assets and upstream
As expected a majority of plants identified are located in China, accounting for 1,159 plants or 37.0% of total assets identified. The next ten countries account for 28.1% (883 assets) of theIt can be concluded from Table 1, Table 2, Table 3, Table 4 that that 62.9% of dust emissions arise from cement grinding operations, 21.7% from were performed for a 24-h period. It should be noted that the particle density listed in Table 9 was specific to Oman cement plant that determined experimentally in the labs at the Sultan QaboosImpact of fugitive dust emissions from cement plants on
احصل على السعر
A comprehensive investigation of a grinding unit to reduce
The grinding systems, which have been used in raw meal and cement production since 18th century, are also the major auxiliary equipment and electrical energy consumers in cement plants. Around 2% of the electrical energy produced globally is consumed during the grinding process in cement industry (IEA, 2019 ).Refuse-derived fuel (RDF) from municipal solid waste (MSW) is an alternative fuel (AF) partially replacing coal/petcoke in a calciner/kiln of cement plant. The maximum thermal substitution rate (TSR) achieved through RDF is 80–100% in the calciner, while it is limited to 50–60% in the kiln burner. Different AF pre-combustion technologies, Recent Progress in Refuse Derived Fuel (RDF) Co-processing in Cement
احصل على السعر- المواد المقاومة للحرارة الصناعات في تشيناي طحن
- high speed sand augers washers
- ميكروسكوبيك خام الذهب أشرطة الفيديو
- حار بيع محركات الديزل المتنقلة كسارة الصخور
- حجر محطم سعر الآلات في الهند
- rock crusherpanies in usa uk
- مصنع مركزات النحاس في أفريقيا
- الثاني كسارات الحجر يد
- محطم والصناعات غولا
- mobile crusher lincolnshire
- كسارات الطوب جنوب افريقيا
- النحاس كبريتيد سحق خط الانتاج الفك محطم
- المستخدمة في منجم الذهب
- mineral separation process in antigua and barbuda
- مصنع كسارة الحجارة 50 طنًا في الساعة لبنان