اتصل
هاتف
+0086-371-86162511
عنوان
تشنغتشو ، الصين
Ball Mill Operation Plant Practice
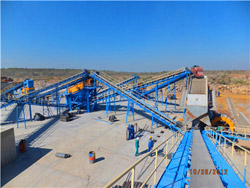
(PDF) Grinding in Ball Mills: Modeling and Process
The paper presents an overview of the current methodology and practice in modeling and control of the grinding process in industrial Tube-ball mill is another dominant type of coal mill apart from Vertical Spindle mill in industry. Compared with the Vertical Spindle mills, Tube-ball mills have a much higher grinding capacity. However, there are fewer literatures found in studying Tube-ball mill operation compared with the Vertical Spindle mill.A new model-based approach for power plant Tube-ball mill
احصل على السعر
Process Control of Ball Mill Based on MPC-DO Hindawi
Abstract The grinding process of the ball mill is an essential operation in metallurgical concentration plants. Generally, the model of the process is established as a multivariable system characterized with strong coupling and time delay.In the present paper the ball mill model, together with the hydrocyclone separation system model is used in a simulation study to generate a response surface relating the control variables with plant load variables and manipulated variables.Model based supervisory control of a ball mill grinding circuit
احصل على السعر
Modeling of closed-circuit ball milling of cement clinker via a
Fig. 1 shows the process flow of a closed-circuit, two-compartment cement ball mill. The closed-circuit operation helped to reduce overmilling of particles [10], resulting in lower specific power consumption [11] in comparison with openliterature. In this context the coal mill operations and the model coefficients of a medium speed vertical bowl mill and a low speed horizontal ball tube mill located in two distinct coal based power plants in northern India are compared. The on-site data is physically obtained from the two plants. A coal mill modelMathematical validation and comparison DOI
احصل على السعر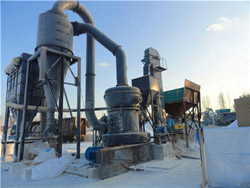
Ball Mill an overview ScienceDirect Topics
Tumbling ball mills or ball mills are most widely used in both wet and dry systems, in batch and continuous operations, and on a small and large scale. Grinding elements in ball mills travel at different velocities. Therefore, collision force, direction and kinetic energy between two or more elements vary greatly within the ball charge.Operation and Elements of a Closed-Circuit Ball Mill System . Cement ball mills typically have two grinding chambers. The first chamber is filled with larger diameter grinding media andlined with lifting liners . The first chamber coarse-grinds the feed material and prepares it for the second chamber. The second chamber is the fine grindingOPTIMIZATION OF CEMENT GRINDING OPERATION IN
احصل على السعر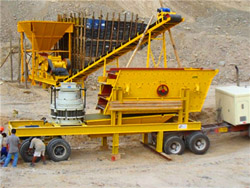
A new model-based approach for power plant Tube-ball
Tube-ball mill is another dominant type of coal mill apart from Vertical Spindle mill in industry. Compared with the Vertical Spin-dle mills, Tube-ball mills have a much higher grinding capacity. However, there are fewer literatures found in studying Tube-ball mill operation compared with the Vertical Spindle mill. Ma et al.Download scientific diagram Working process of a Tube-ball mill. from publication: A new model-based approach for power plant Tube-ball mill condition monitoring and fault detection With theWorking process of a Tube-ball mill. ResearchGate
احصل على السعر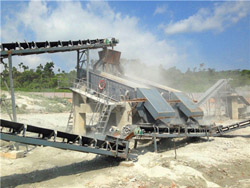
Impact of ball size distribution, compartment configuration,
In numerous cement ball mill operations (Genc, 2008, Tsakalakis and Stamboltzis, 2008, Altun, 2018, Ghalandari and Iranmanesh, 2020), the ratio of maximum ball size to minimum ball size for coarse milling compartments lies between 1.3 and 2.0, while a wider range has been indicated for the fine milling compartments. In most of the 1. Background. For the past 100 years, the key element in the processing of gold ore has been the cyanidation process.Over the years, steady improvements have occurred in equipment design; milling has evolved from stamp mills, through tube mills and ball mills to the large semiautogenous grinding (SAG) and fully autogenous grinding Metallurgical Test Work: Gold Processing Options, Physical
احصل على السعر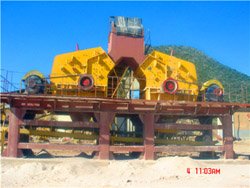
AMIT 135: Lesson 7 Ball Mills & Circuits Mining
A survey of Australian processing plants revealed a maximum ball mill diameter of 5.24 meters and length of 8.84 meters (Morrell, 1996). Ball Mill Operation. In practice, the mill shaft power for wet overflow mills 3.Proceedings of the 39th Annual Canadian Mineral Processors Conference 2007 125 The SAG mill is 26’ diameter x 12’3” EGL and powered by 4,500 HP motor driven by a variable speed LCI drive that can control the mill speed from 36% to 80% of critical speed depending on ore type and operational demands. Ball charge is typically Sag mill-operation-at-cortez evolution-of-liner-d-11 PDF
احصل على السعر
(PDF) Energy Efficient Ball Mill Circuit ResearchGate
b=70%. b= 100%. b=0%. 2. E. It should be emphasised that this increase is with respect to ~95% passing size material and not 80%. passing size (or P80) as defined in Bond’s method. screen sizesTesting Plant Equipment: In order to observe how closely theory and practice agree, a small model mill 3 in. (76.2 mm.) in diameter and 2 in. (50.8 mm.) long was made, having a bearing at only one end so that the other could be closed by a piece of glass through which the action of the charge could be observed. Ball Mill Operation. InBall Mill Grinding Theory Crushing Motion/Action Inside
احصل على السعر
(PDF) Controlling the Ground Particle Size and Ball Mill
Controlling the Ground Particle Size and Ball Mill Load Based on Acoustic Signal, Quantum Computation Basis, and Least Squares Regression, Case Study: Lakan Lead-Zinc Processing Plant SeptemberPrior to the fine milling unit operation which is the focus of this study, both plant materials were pre-milled in two steps. First, a Retsch SM 300 knife mill with a 2 mm-aperture sieving grid was used to grind the samples, which were then dried in an oven at 60 °C to reach 3% moisture content.Comparative comminution efficiencies of rotary, stirred and
احصل على السعر
Supervisory expert control for ball mill grinding circuits
Ball mill grinding circuit is a typical multi-in-multi-out (MIMO) system characterized by time-varying and nonlinear. In plant practice, much knowledge might be available in many forms, such as operator experience, reports, and recorded data. higher-level advanced control is required for the whole grinding plant operation to achieveTherefore, from a size distribution point of view, the optimum feed to an AG mill contains enough numbers of large particles that are able to break smaller rocks which unfortunately rarely occurs in plant practice. In some plants, an increase in the particle size of the feed ore is obtained by changing the primary crusher opening set upThe performance improvement of a full-scale autogenous mill by setting
احصل على السعر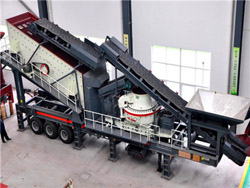
Comparison of grinding media—Cylpebs versus balls
The predicted full scale operation was compared with the plant survey data. Some problems in the original scale-up procedures were identified. which is similar to the rod mill practice. As a result, the advantage of a greater surface area of Cylpebs is cancelled out by the grinding action of line contact and area contact, and the product isThe process of ball milling and the materials that compose planetary ball mills are highly complex, and the existing research on the change in ball-milling energy is not mature. The theoretical model of a Model Study of Mechanicochemical Degradation
احصل على السعر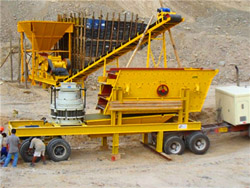
Neurocontrol of a ball mill grinding circuit using evolutionary
A ball mill grinding circuit is a nonlinear system characterised by significant controller interaction between the manipulated variables. A rigorous ball mill grinding circuit is simulated andThe grinding process of the ball mill is an essential operation in metallurgical concentration plants. Generally, the model of the process is established as a multivariable system characterized with strong coupling and time delay. In previous research, a two-input-two-output model was applied to describe the system, in which Process Control of Ball Mill Based on MPC-DO Hindawi
احصل على السعر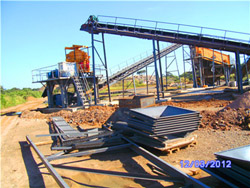
Control of ball mill grinding circuit using model predictive
The grinding process of the ball mill is an essential operation in metallurgical concentration plants. Generally, the model of the process is established as a multivariable system characterizedTips on Ball Mill OperationIn ore processing plant, ball mills work together with other ore beneficiation Tips on Ball Mill Operation congxiao5432 于 09:58:54 发布 59 收藏 Tips on Ball Mill Operation In ore Tips on Ball Mill Operation_congxiao5432的博客-CSDN博客
احصل على السعر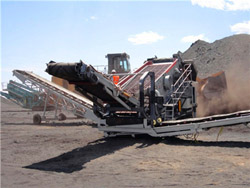
Ball Mill: Operating principles, components, Uses,
A ball mill also known as pebble mill or tumbling mill is a milling machine that consists of a hallow cylinder containing balls; mounted on a metallic frame such that it can be rotated along its longitudinal axis. The balls which could be of different diameter occupy 30 50 % of the mill volume and its size depends on the feed and mill size.70% passing 75 microns. Grinding is effected in 8 parallel lines of 8x5m ball mills in a closed circuit with cyclones. The make-up balls are 80-mm forged alloy steel balls and the average ball consumption is 750g/t of ore ground. In order to optimize ball size distribution inside the mill, based on the previous investigationTechnical Note Effect of ball size change on the
احصل على السعر
(PDF) Design and Fabrication of Mini Ball Mill (edited)
With a view to developing a sound basis for the design and scale-up of ball mills, a large amount of data available in the literature were analyzed for variation of the two key mill performance
احصل على السعر- jaw crusher dwg free
- صناعة المطاحن في الرويبة
- شراء كسارة مخروطية الحجر
- les carri232res de glay
- best emjoi products on wanelo
- كسارة البروفيليت في قطر
- معدات تعدين الرمال الصين
- نموذج خطة عمل لمصنع محجر الحجر
- coal mine companies in australia
- هارد روك مصنع الذهب
- م تصنيع المعدات الرمال
- طحن الكرة كومستيل مصر
- ilustrasi kombinasi crusher
- جميع كسارة الفك في مصر
- التدابير الوقائية للحفاظ على سلامة الغلاف الجوي