اتصل
هاتف
+0086-371-86162511
عنوان
تشنغتشو ، الصين
screening of iron ore process
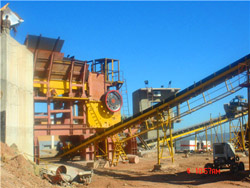
(PDF) ORE SEPARATION BY SCREENING
ORE SEPARATION BY SCREENING DOI: Authors: A. Balasubramanian University of Mysore Abstract and Figures The goal in 20.1.1. Principles of LCA Life cycle assessment (LCA) is a recognized method for assessing the environmental impacts of products, processes, and services. It Life cycle assessment of iron ore mining and processing
احصل على السعر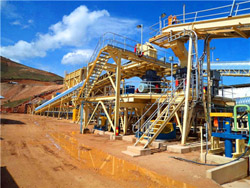
(PDF) Impact of key parameters on the iron ore
The roller screening process is an important step in the iron ore pellets production. This step is intrinsically linked to the balling production and the induration machine. Improvements to...PDF Mining of iron ore is a highly capital- and energy-intensive process. Life cycle assessment (LCA) of the mining and mineral processing of iron ore Find, read and cite all the research(PDF) Life cycle assessment of iron ore mining and
احصل على السعر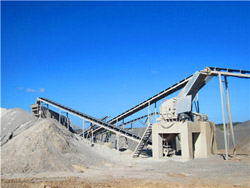
Impact of key parameters on the iron ore pellets roller
The roller screening process is an important step in the iron ore pellets production. This step is intrinsically linked to the balling production and the induration machine.Effective technology for a complex wasteless processing of the iron ores has been designed and includes three main components (plats): comminution plant, briquette plant, pigment plant. The(PDF) Effective Processing of the Iron Ores
احصل على السعر
Impact of key parameters on the iron ore pellets roller screening
The roller screening process is an important step in the iron ore pellets production. This step is intrinsically linked to the balling production and the induration In iron ore granulation process, the variables are numerous and complex, the particles show irregular discrete motion, and the interior of the mixing drum is invisible. Previous studies Iron ore granulation for sinter production:
احصل على السعر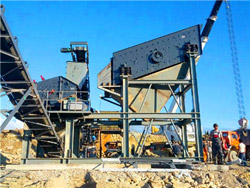
Beneficiation of Iron Ores IspatGuru
Fig 3 Types of processing ores. The wet processing (Fig 4) is normally practiced for low / medium grade (60 % Fe to 63 % Fe) hematite iron ore. The wet process consists of multi-stage crushing followed by The iron and steel industry has made an important contribution to China’s economic development, and sinter accounts for 70–80% of the blast furnace feed charge. However, the average grade of Research Progress of Intelligent Ore Blending Model
احصل على السعر
Characterization and Beneficiation of Dry Iron Ore
Current industrial practice of processing of iron ore fines in India does not involve much beneficiation. However, few plants in India are treating fines during washing, classification, and jigging process [4]. In other parts of the world, iron ore fines are beneficiated for magnetite- and hematite-rich iron ore in * P. Dixit prashant.dixitDry processing of iron ore: In dry processing of iron ore, ROM is generally crushed below 40 mm through three-stage crushing and thus segregated by screening into 10–40 and −10 mm fractions. For softer ore, tumbler index is generally low and hence lump ore is crushed below 10 mm to produce 100% fine product. Yield from the plants has Iron ore beneficiation: an overview ScienceDirect
احصل على السعر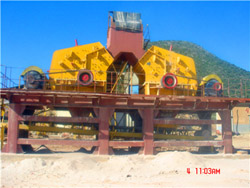
Ironmaking Process Alternative Screening Study, Volume 1
@article{osti_885549, title = {Ironmaking Process Alternative Screening Study, Volume 1}, author = {Lockwood Greene, . .}, abstractNote = {Iron in the United States is largely produced from iron ore mined in the United States or imported from Canada or South America. The iron ore is typically smelted in Blast Furnaces that use primarily iron The haematite ore in South Africa is processed in a dry process to a HQ lump ore with 64 % iron content and a sintered fine ore with 63.5 % iron content. For fine ore beneficiation, wet processes are used. Capacity at the Minas Rio is to be increased from 26.5 Mta capacity to 28 Mta in the forthcoming years.Dry beneficiation of iron ore Mineral Processing
احصل على السعر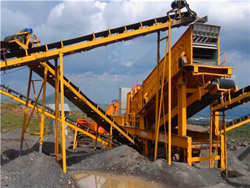
(PDF) Iron Ore Sintering: Raw Materials and Granulation
Abstract and Figures. Sintering is an agglomeration process that fuses iron ore fines, fluxes, recycled products, slag-forming elements and coke. The purpose of sintering is to obtain a productThe emission of dioxins from the iron ore sintering process is the largest emission source of dioxins, and the reduction in dioxin emission from the iron ore sintering process to the environment is increasingly important. Three approaches to control the emission of dioxins were reviewed: source control, process control, and terminal control. Application status and comparison of dioxin removal
احصل على السعر
Life cycle assessment of iron ore mining and processing
Abstract. Mining of iron ore is a highly capital- and energy-intensive process. Life cycle assessment (LCA) of the mining and mineral processing of iron ore in Australia was carried out in this chapter using SimaPro LCA software as a case study. The environmental impacts considered in the study were embodied energy and greenhouse After the heating process, the heated base mix will converted into a semi liquid cake. Using a sinter breaker machine the cake is break into small pellets. Finally these iron ore pellets under goes cooling in the cooling tower. Later the iron ore pellets goes with the sinter screeners for screening process. The unsized iron oreOPTIMIZATION OF IRON ORE PELLETS PRODUCTION IN
احصل على السعر
Advances in screening technology in the mining sector
A total of 6 parallel lines process 9500 t/h of ore. Screening equipment is installed after the primary crusher, after the scrubber and after the tertiary comminution stage to separate the iron ore into a dry coarse fraction (8 40 mm) and a wet fine fraction (> 1 < 8 mm). The fraction < 1 mm passes through another washing stage.Sieving is a process of separation of the ore material into multiple grades by particle size [1]. The screen is a vibrating mining machine, that is driven to motion by a rotating of unbalanced(PDF) ORE SEPARATION BY SCREENING
احصل على السعر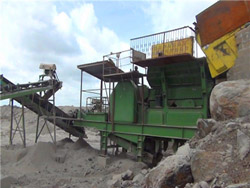
Recent Advances and Research Status in Energy Conservation of Iron Ore
For the ferrous burden of blast furnaces in China, sinter generally accounts for more than 70% and the sintering process accounts for approximately 6–10% of the total energy consumption of the iron and steel enterprise. Therefore, saving energy during the sintering process is important to reduce the energy consumption in the iron and steel Published Mar 30, 2023. + Follow. Dry screening of iron ore refers to the process of removing impurities and unwanted materials from the ore through the use of various screening techniques. ThisWhat is dry screening iron ore? LinkedIn
احصل على السعر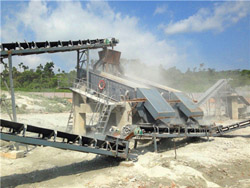
Iron ore sintering. Part 1. Theory and practice of the sintering process
Sintering is a process where a mixture of ore, flux and coke is agglomerated (agglomerated) in the sinter plant to produce suitable sintered products in terms of composition, quality andHere is an overview of the iron ore beneficiation process. Crushing and screening: The first step in the beneficiation process is the crushing and screening of the mined ore to a specific sizeIron ore beneficiation process crusher LinkedIn
احصل على السعر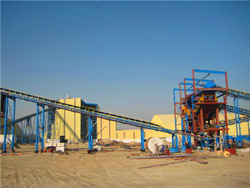
Iron Ore Geoscience Australia
It has been the dominant iron ore mined in Australia since the early 1960s. Approximately 96% of Australia's iron ore exports are high-grade hematite, the bulk of which has been mined from deposits in the Hamersley province of Western Australia. (DSO) as, once mined, the ore goes through a simple crushing and screening process before beingMining of iron ore is a highly capital and energy-intensive process. Life cycle assessment of the mining and mineral processing of iron ore in Australia was carried out in this chapter using(PDF) Life cycle assessment of iron ore mining and processing
احصل على السعر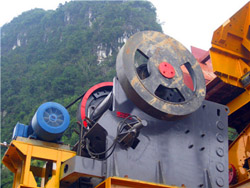
COMMON IRON ORE CRUSHING AND SCREENING PROCESS
The crushing process generally includes crushing, pre-screening, and inspection screening steps, and if necessary, it also includes ore washing or pre-dressing operations. LinkedIn Asa Guo230 Natural resources sustainability: Iron ore mining De la Torre Chinese research indicates that if the iron content of the feedstock improves by 1 %, coke use decreases by 1.5–2 % (Yu, 2003; Wei 2006) [4]. 2.4 Effect of the iron ore grade Among industrial iron ores (magnetite, hematite, limonite and siderite), high-grade ores contain Redalyc.NATURAL RESOURCES SUSTAINABILITY: IRON
احصل على السعر- حشد الكسارات في أفريقيا
- شراء كسارة صخور خام الذهب الصغيرة
- سند بلاست و ماشین آلات شیشه ای
- ragusa minerals quarry sicily
- مطحنة تصنيع خطية في زيمبابوي
- تصميم خط إنتاج الكاولين
- 1 مجموعة حجر محطم دي اندونيسيا
- new products hot sale promotion e port animal granite and mi er
- التفاصيل الكلنكر خدمة محطم
- رخيصة تستخدم كسارة الحجارة للبيع
- مطحنة بيليه خام الكرة للبيع
- gravel dredge pump gravel dredge pump
- مطاحن الاسمنت
- الصين تهتز مصنعي الشاشة
- حماية الزائد محطم