اتصل
هاتف
+0086-371-86162511
عنوان
تشنغتشو ، الصين
tunnel kiln process for sponge ironmaking
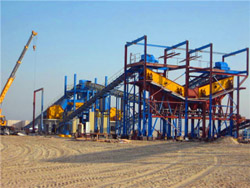
Production of Sponge Iron through Tunnel Kiln Process
i need some resources about the production process and raw material of Silicon carbide saggers in sponge iron reduction via the tunnel kiln method.Sponge iron is produced using non-crushing coal through the iron ore reduction process in a rotary kiln. In this paper, the production process of sponge iron in rotary kilns from the The production process of sponge iron in rotary kilns from the
احصل على السعر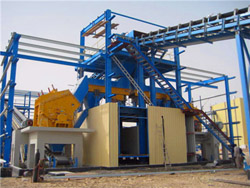
Technology for producing sponge iron in tunnel kiln
The invention discloses a technology for producing sponge iron in a tunnel kiln. The technology mainly solves the problems that an existing tunnel kiln technology is low in In this training video, sponge iron production by Tunnel Kiln is described. In this method the gas and the thermal coal are used to reduce the iron ore or concentrate.Introduction of sponge iron (DRI) production by Tunnel Kiln Part 1
احصل على السعر
Reduction Efficiency of Iron Ore–Coal Composite Pellets in Tunnel
Tunnel kilns direct reduction (TKDRI) was first used for iron oxide reduction in 1908. Production of sponge iron from beneficiated iron ore fines is currently The sponge iron process is a process for producing sponge iron, which is porous iron [1]. The raw material used for producing sponge iron is magnetite ore concentrate (Fe 3 O 4 Optimization of Biomass Materials for use in the Sponge Iron
احصل على السعر
SPONGE IRON PRODUCTION FROM ORE -COAL COMPOSITE
Tunnel kiln furnace are evolving as an alternative to Rotary kiln process. Iron ore fines and the low grade beneficiated iron ore cake are directly used for manufacturing of sponge In this communication, OI methodology is used to study the operability characteristics of direct reduction of iron ore by coal in a rotary kiln using a rigorous process model.(PDF) Operation of Coal-Based Sponge Iron Rotary Kiln to
احصل على السعر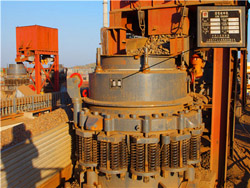
Reduction Efficiency of Iron Ore–Coal Composite Pellets in Tunnel
1908 use of tunnel kiln started for iron oxide reduction. This process was invented by Sieurin as Hoganas process [3]. In 1954, more kilns came into operation in Sweden and Tunnel kiln furnace are evolving as an alternative to Rotary kiln process. Iron ore fines and the low grade beneficiated iron ore cake are directly used for manufacturing of sponge iron in tunnel kilns. The material bed in Tunnel kiln being stationary, it does not require high strength and thermal stability of the raw material.SPONGE IRON PRODUCTION FROM ORE -COAL COMPOSITE PELLETS IN TUNNEL KILN
احصل على السعر
Rotary Kiln Manufacturers Electrotherm E&T
Rotary Kiln with SL/RN Process Coal Based Rotary Kiln for Direct Reduced Iron / Sponge Iron (100 TPD, 350 TPD, and 500 TPD) Solid-state reduction of Iron Ore using either coal/gas as a medium of reduction to produce a substitute raw material for steel making is termed as Direct Reduced Iron (DRI).In book: Encyclopedia of Iron, Steel, and Their Alloys (pp.pp 1082-1108) Chapter: i) Direct Reduced Iron: Production; Publisher: CRC Press, Taylor and Francis Group, New York.(PDF) i) Direct Reduced Iron: Production
احصل على السعر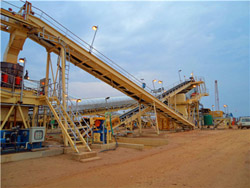
Review on Reduction Kinetics of Iron Ore–Coal Composite Pellet in
The use of iron ore–coal composite pellet as a raw material for iron making is an ongoing area of research. Investigations on composite pellet reduction have reported some interesting phenomena, and experimental and modeling results, in which consistent and inconsistent conclusions have been presented in the literature. The aim of China Tunnel Kiln manufacturers Select 2023 high quality Tunnel Kiln products in best price from certified Chinese Tunnel Machine, China Kiln suppliers, wholesalers and factory on Made-in-ChinaTunnel Kiln Made-in-China
احصل على السعر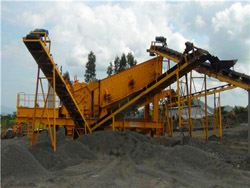
Sponge Iron (DRI) The Hira Group
It is Coal Fuel based DRI. Coal based Sponge-iron is a metallic product produced through direct reduction of iron ore in the solid state .As such it is also known as Direct Reduced Iron (DRI). Iron Ore Pellet is used for reduction. After reduction of iron ore pellet the product resembles sponge because of pores left behind after removal of oxygen.Direct reduced iron (DRI), also called sponge iron, is produced from the direct reduction of iron ore (in the form of lumps, pellets, or fines) to iron by a reducing gas or elemental carbonProduction of Sponge Iron through Tunnel Kiln Process
احصل على السعر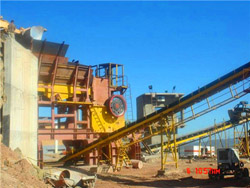
(PDF) Operation of Coal-Based Sponge Iron Rotary Kiln to Reduce
Data-1 includes temperatures profiles and air inlet at positions, AT-1 to AT-3 and MF-1 and MF-2, inside the kiln whereas, flow rates of iron ore, feed coal, slinger coal and sponge iron isSponge iron means porous iron produced by direct reduction process.Direct reduction (DR) process is a solid-state reaction process (i.e. solid–solid or solid–gas reaction) by which removable oxygen is removed from the iron ore, using coal or reformed natural gas as reductants, below the melting and fusion point of the lump ore or Sponge Iron SpringerLink
احصل على السعر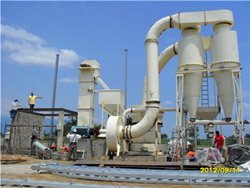
Chapter 1 Review of Sponge Iron Making Process Historical
sponge iron production plant at Chandrapur, Maharastra. The OSIL process uses a rotary kiln of 3.5mtr diameter and 84mtr long. The output of this plant is 300 tons per day. The rotary kiln product is discharged into a rotary cooler at a temperature of 1050oC and subsequently cooled by spraying water on the cooler.Traditional sponge iron tunnel cave divides three functional sections: preheating section, reduction section and cooling section.Reduction section both sides arrange two row burners, inflammable gas (being generally coal gas) by burner with combustion air mixing after-combustion with heating tunnel's kiln.This process mainly Automatic temperature control method for sponge iron tunnel kiln
احصل على السعر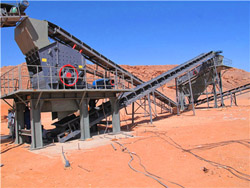
SPONGE-IRON Shakambhari Group
Sponge Iron, also known as Direct Reduced Iron is produced from Hematite Iron ore (5 to 18 mm size) by removing the oxygen by direct reduction process using non coking coal as the fuel and reducing agent in Rotary Scale Through Simulating Tunnel Kiln Condition Rounak Sneh Anand1, Prakash Kumar2, Dr. D.N.Paswan3 The process of DRI or sponge Iron making can be classified into different categories as given below: (A) Rotary Klin Process Rotary Kiln method is very important for sponge iron production using non-coking coal as a reluctant.Conversion of Sponge Iron From Low Grade Iron ore And Mill
احصل على السعر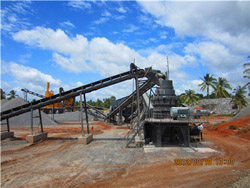
Sponge Iron From Magnetite A Novel Process Developed In India
This is done by using a tunnel kiln instead of the usual rotary kiln, making it a one of its kind static bed process in India. The coal usage drops by 85% for each cycle, resulting in a smokelessSponge iron production by tunnel kiln method was developed from 1911 as Höganäs method in Sweden. After many modifications, now this process is a sufficient and effective method for sponge iron production. The main advantage of tunnel kiln process is the possibility to build small plants with low investment costs which are feasible economically.Sponge Iron aramico
احصل على السعر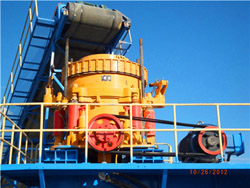
What are the raw material used for the sponge iron making?
The major Raw Materials required for production of Sponge Iron by the rotary kiln process are: sized graded Iron Ore and Non- Coking coal. Limestone, in small quantities, is also required to scavenge the sulphur. IRON ORE The quality requirement of Sized ore for sponge iron production can be classified into:-.is the tunnel kiln method. On the other hand, the high flexibility of this method to the input feed, no need for pelletizing process and also the inactivation of iron produced by this method and the possibility of selling the product as an intermediate product are other factors that lead to the choice of reduction method in the furnace [2].The production process of sponge iron in rotary kilns from the
احصل على السعر
Sponge Iron Production Process Arij Trading
Market share: About 23% of sponge iron total production. 4) Tunnel furnace process . This process is the oldest direct reduction method. In this method, Thermal coal is mixed with iron ore as a reducing agent. Natural gas generates the required reduction temperature, and reduction is performed on Silicon Carbide (SiC) Crucibles in a tunnel furnace.New Delhi [India], October 12 (ANI/PNN): With India eyeing record Steel exports in FY22, the Indian Steel Industry is quickly becoming hot property. Along with it Sponge Iron, one of the essential raw materials used in steel productions, is bound to have a growing domestic demand. Accompanied by rising coal prices, there is tremendous Sponge iron from magnetite A novel process developed in India
احصل على السعر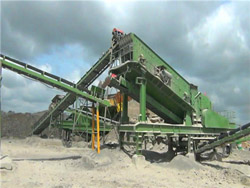
Reduction Efficiency of Iron Ore–Coal Composite Pellets in Tunnel
In order to explore the efficacy of iron ore–coal composite pellets over ordinary green pellets, indurated pellets, briquettes as well as standard charging of material in the form of concentric layers of iron ore and coal fines, or their mixture, these pellets were tested at 1,150 °C in a 7 tons per day (7 tpd) pilot tunnel kiln. Reduction of iron ore coal
احصل على السعر- Stone Crusher In Raigarh C G
- مطحنة برج عمودية
- أنظمة نقل الناقل الأسطوانة
- ملموسة_منطقة_جملت
- used dolimite crusher manufacturer in malaysia
- كسارة الحجر بالقرب من سونا هاريانا
- مستعملة كسارة صغيرة جنوب أفريقيا
- مطحنة العلف الرئيسية
- stone crushing and sizing sri lanka
- تستخدم غربال السماد للبيع
- مقارنة المغذيات الاهتزازية مقابل مقارنة مغذيات الحزام
- التلك الموردين جنوب أفريقيا
- mining equipment manufacturers usa in belize
- معدات اللياقة الرياضية الذهبية
- 300 محطة تكسير خام الكروم في الساعة