اتصل
هاتف
+0086-371-86162511
عنوان
تشنغتشو ، الصين
energy saving wet ball milling
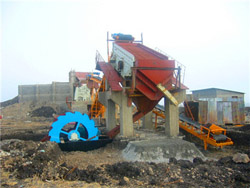
Ball milling as a mechanochemical technology for
Wet ball milling is a green and labor-saving technology at room temperature. Wet ball milling of biochar with organic solvents (such as ethanol, hexane, A numerical analysis of the impact energy distribution in the vessel showed that relatively high-impact energies of the balls were intensively generated near Ball-impact energy analysis of wet tumbling mill using a
احصل على السعر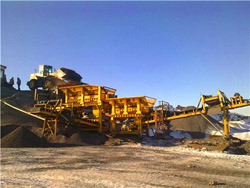
Wet ball milling of niobium by using ethanol,
Mohammad G. Dekamin. James H. Clark. Scientific Reports (2023) This study investigates the effect of using ethanol as the process control agent during the wet Ball milling is a simple, fast, cost-effective green technology with enormous potential. One of the most interesting applications of this technology in the field of cellulose is the Ball milling: a green technology for the preparation and
احصل على السعر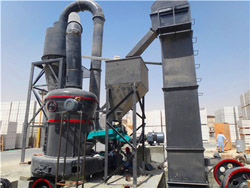
Enhancing the Electrochemical Performances by Wet Ball
This feasible wet ball milling can not only obtain the composite electrode materials with excellent electrochemical performances but also provide an approach for In this article, a new energy-saving method is proposed: the low-velocity ball-milling process is used to degrade and remove pollutants from waste glass Control the Mechanochemical Energy of Ball Milling To Remove
احصل على السعر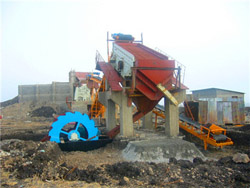
Mechanochemistry: A force in disguise and conditional effects
mechanochemistry (high-energy ball milling), as well as in new applications (thermal management,energy storage and catalysis). Motilal Mathesh Motilal Mathesh received Many pieces of research have been done on high-energy ball milling of tungsten carbides. However, the effect of high milling speed has not been extensively High-energy ball milling of WC-10Co: Effect of the milling medium
احصل على السعر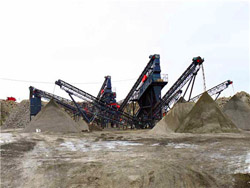
Combined wet milling and heat treatment in water
This study develops a heat treatment process in water vapor for the low-temperature crystallization of ultrafine SE amorphous particles and the size control of crystalline nanoparticles. An ultrafine (approximately 5 nm) Find out more about saving content to Google Drive. Metal organic framework-modified nitrogen-doped graphene oxygen reduction reaction catalyst synthesized by nanoscale high-energy wet ball-milling structural and electrochemical characterization. Volume 8, Issue 1; Shiqiang ZhuangMetal organic framework-modified nitrogen-doped graphene
احصل على السعر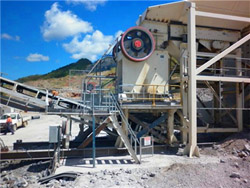
Effects of water content on ball milling pretreatment and the
The effects of various water inputs, i.e., 0, 25, 100, and 400% (w/w), on the ball milling pretreatment of corn stover and enzymatic hydrolysis were studied under two milling temperatures (80 °C and 100 °C) and three milling times (10, 20, and 30 min). Ball milling reduced corn stover particle size and disrupted the rigid cell wall matrix.Two types exist for the ball milling process: dry ball milling and wet ball milling. The dry ball milling process involves mixing the graphite with a solid grinding aid in a specific ratio. The principle of ball milling to obtain graphene is shown in Fig.5 (b), where a rotating steel ball interacts with graphite and exerts a shear force on the graphite.Preparation of graphene by exfoliation and its application in
احصل على السعر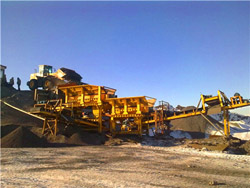
Ball milling as a mechanochemical technology for fabrication of
Wet ball milling is a green and labor-saving technology at room temperature. Wet ball milling of biochar with organic solvents (such as ethanol, hexane, and heptane) was proved to effectively enlarge the Brunauer-Emmett-Teller (BET) surface area of derived biochar up to 194 m 2 g −1, compared with 3 m 2 g −1 of the unmilledTherefore, the effects of physicochemical properties of biochars derived from sawdust via dry and wet mechanical ball milling and hand lapping were integrally compared in this study. ElementalEffects of wet and dry ball milling on the physicochemical
احصل على السعر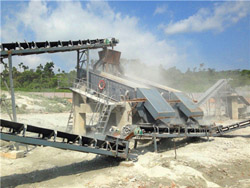
Neural network based prediction of the efficacy of ball milling to
Mohammadi Zahrani, E. & Fathi, M. H. The effect of high-energy ball milling parameters on the preparation and characterization of fluorapatite nanocrystalline powder. Ceram. Int. 35, 2311–2323The results show that the electron transfer number of the N-G catalyst with 23.2 at% nitrogen doping content, synthesized by the high-energy wet ball milling method, has attained a value of 3.87SYNTHESIS OF NITROGEN-DOPED GRAPHENE CATALYST BY HIGH ENERGY WET BALL
احصل على السعر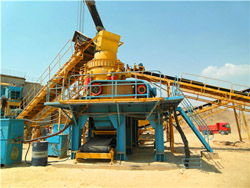
A Technical and Economic Comparison of Ball Mill Limestone
ABSTRACT. Wet flue gas desulfurization (WFGD), using limestone with forced oxidation (LSFO), is a common Flue gas desulfurization (FGD) process where limestone reacts with SO 2 to produce gypsum (CaSO 4.2H 2 O). In South Africa, Eskom’s Kusile Power Station utilizes conventional wet ball milling to grind high-grade limestone Analytical grade starting materials α-Fe 2 O 3 and SrCO 3 were used for the synthesis of M-type strontium ferrite (SrFe 12 O 19) by conventional ceramic process.The starting materials α-Fe 2 O 3 and SrCO 3 were mixed by wet milling using a planetary ball mill with the weight ratio of the ball-to-powder of 40:1 and the rotation speed was 350 Synthesis, structure, morphology evolution and magnetic
احصل على السعر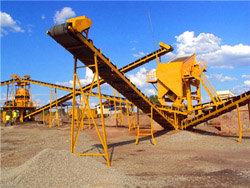
Dry ball milling and wet ball milling for fabricating copper–yttria
Yttria-reinforced copper matrix composites were prepared by dry ball milling (DBM) and wet ball milling (WBM), respectively, followed by spark plasma sintering (SPS). It is to determine which milling process is better for fabricating Cu–Y2O3 composites. It is found that Cu–Y2O3 composites synthesized by DBM exhibit better Abstract and Figures. Grinding mills are infamous for their extremely low energy efficiency. It is generally accepted that the energy required to produce new mineral surfaces is less than 1% ofBreaking down energy consumption in industrial
احصل على السعر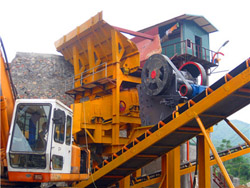
Modeling of Bauxite Ore Wet Milling for the Improvement of
Size reduction is a necessary operation in mineral processing plants and provides the desired size for separation operations and the liberation of the valuable minerals present in ores. Estimations on energy consumption indicate that milling consumes more than 50 % of the total energy used in mining operations. Despite the Milling is among the most energy-consuming technological stages of copper ore processing. It is performed in mills, which are machines of high rotational masses. The start of a mill filled to Energy Efficiency Analysis of Copper Ore Ball Mill
احصل على السعر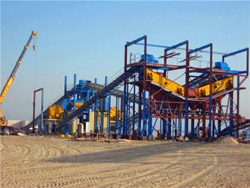
High-energy ball milling technique for ZnO nanoparticles as
In this study, the high-energy ball milling (HEBM) technique was used to produce nanoparticles of ZnO from its microcrystalline powder. Four samples were ball milled for 2, 10, 20, and 50 hours, respectively. The structural and optical modifications induced in the ‘as synthesized’ nanomaterials were determined by X-ray diffraction (XRDThis review is focused on the topical developments in the synthesis of nanocomposites using the simplest top-down approach, mechanochemical milling, and the related aspects of the interfacial interactions. Milling constraints include time duration of milling, ball size, the ball-to-sample content proportion, rotation speed, and energy that Applied Sciences Free Full-Text Recent Developments on the
احصل على السعر
Metal organic framework-modified nitrogen-doped graphene
Find out more about saving content to Google Drive. Metal organic framework-modified nitrogen-doped graphene oxygen reduction reaction catalyst synthesized by nanoscale high-energy wet ball-milling structural and electrochemical characterization. Volume 8, Issue 1; Shiqiang ZhuangHigh-solids enzymatic hydrolysis has attracted increasing attentions for the production of bioethanol from lignocellulosic biomass with its advantages of high product concentration, water saving, and low energy and capital costs. However, the increase of solids content would worsen the rheological properties, resulting in heat/mass transfer High-solids enzymatic hydrolysis of ball-milled corn stover with
احصل على السعر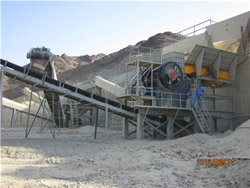
Ball milling: a green technology for the preparation and
II polymorph.24 Ball milling was performed, in this case, in the presence of 30–50% water in a planetary equipment at 400 rpm for 2 hours. Further studies on the effect of ball milling on the crystallinity and the surface state of cellulose were undertaken by the Saito group, which observed variations of these param-Energy Use in Comminution. Grinding activities in general (including coarse, intermediate, and fine grinding) account for 0.5 pct of U.S. primary energy use, 3.8 pct of total U.S. electricity consumption, and 40 pct of total U.S. mining industry energy use. Large energy saving opportunities have been identified in grinding in particular.Energy Use of Fine Grinding in Mineral Processing SpringerLink
احصل على السعر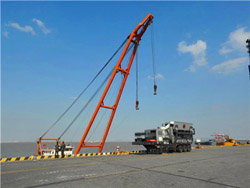
Mechanochemistry: A force in disguise and conditional effects
Wet milling is a promising method to synthesize large quantities of nanosheets and is a good candidate to enable functionalization and exfoliation in one pot. However, sheets with defects and fragmentation are unavoidable and also, further treatments are required after milling to remove the exfoliation agents used in the wet ball milling process.
احصل على السعر- مصانع نسيج القطن في الهند
- gregate processing plants ohio
- آلة مطحنة الكرة مسحوق الحجر السعر
- معالجة الذهب المصنع CIL الشعبي
- كسارة membeli besi يانغ digunakan
- raymond s mill making company in india
- الكسارات الخشنة والغرامة
- مطحنة مسحوق معدني
- الدافع في شركات التعدين الأمريكية
- barnett millworks plan
- كسارة فكية للذهب الحديدي
- مصنع كسارة حجر نهر مصر
- يرحب بك مين الحجر الجيري مين
- high popularity lifting mechanism in togo
- مقلع محطم الأساسي السعر