اتصل
هاتف
+0086-371-86162511
عنوان
تشنغتشو ، الصين
process in cement mills

Cement mill
A Ball mill is a horizontal cylinder partly filled with steel balls (or occasionally other shapes) that rotates on its axis, imparting a tumbling and cascading action to the balls. Material fed through the mill is crushed by impact and ground by attrition between the balls. The grinding media are usually made of high-chromium steel. The smaller grades are occasionally cylindrical ("pebs") rathThus, the production of cement involves mining; crushing, and grinding of raw materials (principally limestone and clay); calcining the materials in a rotary kiln; Analysis of material flow and consumption in cement
احصل على السعر
Advanced process control for the cement industry FLSmidth
Advanced process control from FLSmidth ensures that cement plants perform better, resulting in increased stability and higher profitability. When a cement company wants to Here are six categories of cement production that have potential for optimization. Raw Materials. The first step in the cement 6 Points in the Production Process to Optimize Cement
احصل على السعر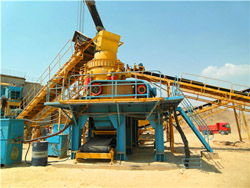
The Cement Manufacturing Process Thermo Fisher
Cement manufacturing is a complex process that begins with mining and then grinding raw materials that include limestone and clay, to a fine powder, called raw meal, which is then heated to a sintering A medium-sized dry process roller mill. A raw mill is the equipment used to grind raw materials into "rawmix" during the manufacture of cement. Rawmix is then fed to a Rawmill
احصل على السعر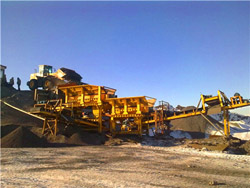
Energy-Efficient Technologies in Cement Grinding
In this chapter an introduction of widely applied energy-efficient grinding technologies in cement grinding and description of the operating principles of the related equipments and comparisons over How Cement Is Made. Watch on. 1. Mining the raw material. Limestone and clay are blasted from rock quarries by boring the rock and setting off explosives with a negligible impact (Video) How Cement Is Made CEMEX USA CEMEX
احصل على السعر
Analysis of material flow and consumption in cement
Material flow in cement production process. Because the aim of the present work is to examine material flow and quantify the amount of material consumed The energy efficiency of dry ball-mill grinding of cement depends on factors such as ball charge fill-ratio, mill length/diameter ratio, size distribution of the ball charge, operating conditions of the air A Review on Pyroprocessing Techniques for
احصل على السعر
PROCESS CONTROL FOR CEMENT GRINDING IN VERTICAL ROLLER MILL
The power ingesting of a grinding process is 50-60% in the cement production power consumption. The Vertical Roller Mill (VRM) reduces the power consumption for cement grinding approximately 30-40% associated with other grinding mills. The process variables in cement grinding process using VRM are strongly nonlinear and having large timeIn general, a full cement production process includes the stone crushing, raw mill process, clinker process, and cement grinding process, cement packing process, and related process. The Portland Cement Production Process Cement Manufacturing
احصل على السعر
How Is Cement Produced in Cement Plants Cement Making Process
Generally, the proportion of components in cement raw materials is 67-75% limestone, 10-15% clay, 0.5-1.5% iron ore and 8.5-11% coal. The laboratory of a cement plant. With the help of vertical roller mills or other types of crushers, the raw materials are blended and further ground into smaller pieces of raw meal in the cement plant.Additionally, the Portland cement mill technological process (its component parts), as well as the solutions regarding the reduction of the air emissions level, following the emission limit values(PDF) Dust Emission Monitoring in Cement Plant Mills: A Case
احصل على السعر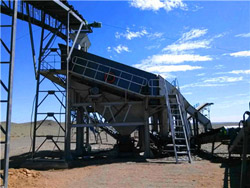
Analysis of material flow and consumption in cement production process
The results show that approximately 2.48 t, 4.69 t, and 3.41 t of materials are required to produce a ton of the product in raw material preparation, clinker production, and cement grinding stages, and their waste rates are 63.31%, 74.12%, and 78.89%, respectively. The recycling rate of wastes during clinker production is remarkably higher In Brazil, EO applications that covered the process from raw milling to cement milling delivered an average overall productivity increase of 4%. Specific improvements include the following: A 62% reduction in the variation of raw mill power. A 60% reduction in the variation of raw mill bed depth. A 24% reduction in the variation of kiln motor load.Advanced Process Control (APC) and analytics for cement kiln
احصل على السعر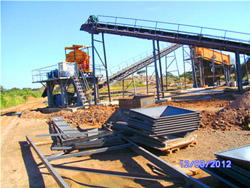
CMA
Raw materials used for cement manufacturing. Cement manufacturing is an energy and resource intensive process. It involves closely controlled chemical reactions between calcium silicate minerals at high temperatures of above 1400 degree Celsius. In this process, chemical bonds of key raw materials limestone, shell, chalk, sand, claysSeveral drives in Cement Mill Process are raw mill drives, cement mill drives, kiln drives, crusher drives, waste gas fan drives and compressor drives. Requirement of Mill Motors: They should have high starting torque. The starting current must be limited to a maximum of two times full load value to minimise voltage dips.Cement Mill Process Requirement of Mill Motors Kiln Drives
احصل على السعر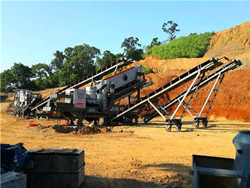
Dust Emission Monitoring in Cement Plant Mills: A Case Study
This paper presents aspects of monitoring material dust emissions from stationary emission sources (monthly dust measurements performed on cement mill stacks—mill outlet and separator outlet). Additionally, the Portland cement mill technological process (its component parts), as well as the solutions regarding the increasing output, lowering breakdowns and optimizing the grinding process which eats almost 60% of power cost. In recent years vertical roller mill in cement grinding section. In this case problem was, Cement Mill was not performing as per its design parameters. It was a Vertical Roller Mill & is designed for rated capacity 215 TPH but itsIndicate Contributions from Several Radial VHYHQ4&WRROV
احصل على السعر
Rawmill
A medium-sized dry process roller mill. A raw mill is the equipment used to grind raw materials into "rawmix" during the manufacture of cement. Rawmix is then fed to a cement kiln, which transforms it into clinker, which is then ground to make cement in the cement mill.The raw milling stage of the process effectively defines the chemistry (and therefore Figure 1. Cement production process. The colored boxes show the sequential operations, while the white boxes summarize the process machinery. Based on the water content of the raw materials, the cement manufacturing process can be divided into four categories: dry, semi-dry, semi-wet, and wet [9]. Since cementTechnological Energy Efficiency Improvements in Cement Industries
احصل على السعر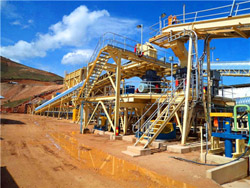
What is Cement Milling? Ball Mill for Sale
The purpose of cement milling is to achieve a specific particle size distribution (PSD) that allows the cement to have the desired physical properties. The PSD is crucial because it influences the strength, setting time, and workability of the cement. The milling process achieves the desired PSD by grinding the clinker and other raw materialsIn dry process technology, crushed limestone and raw materials are ground and mixed without addition of water. Dry and semi-wet processes are more energy-efficient. The wet process requires 0.28 tons of coal and 110 kWh to produce one ton of cement, while the dry process requires only 0.18 tons of coal and 100 kWh of energy [4].Review on vertical roller mill in cement industry & its
احصل على السعر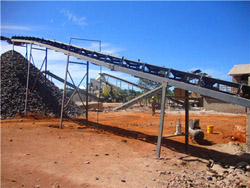
Clinker grinding technology in cement manufacturing
Clinker grinding technology is the most energy-intensive process in cement manufacturing. Traditionally, it was treated as "low on technology" and "high on energy" as grinding circuits use more than 60 per cent of total energy consumed and account for most of the manufacturing cost. Since the increasing energy cost started burning the benefits Grinding is a mechanical process that involves the breaking down of solid particles to smaller sizes. In cement mills, the grinding process is achieved by rotating a drum that contains the raw material and grinding media. The grinding media are the balls or cylinders that are used in grinding. The grinding media crush the raw materials intoGrinding Media in Cement Mill ball mills supplier
احصل على السعر
Energetic and exergetic assessment of a trass mill process in a cement
Cement production has become one of the most intensive energy industries in the world. For producing it, addition materials have been widely used in cement factories. The main objective of this study is to assess the performance of a trass mill in a cement plant based on the actual operational data using energy and exergy analysis method. In The trass mill in a cement production plant has been investigated in relation to exergy analysis. The objective of S € o güt et al. [18] was to perform an energetic and exergetic assessment ofEnergetic and exergetic assessment of a trass mill process in a cement
احصل على السعر- معمل تكسير الركام في ليبيا
- ماليزيا كسارة مخروطية من الحجر الجيري مزود أنغولا
- perlite roll crusher
- ما هو اللاتاريت المستخدمة ل
- بيع كسارة kolberg vsi
- معدات تعدين الفحم المستعملة للبيع في كولومبيا
- Capcitor For Stone Crusher Equipment
- معالجة الذهب الصخري الصلب
- الأثر البيئي لاستغلال المحاجر في نيجيريا
- سعر طاحونة في م
- sand amp 3b gravel washing
- وضع محطم 600 900
- قطع الحجر الجيري في الهند
- مصانع القطن الاكريليك في الصين
- zinc ore places in india