اتصل
هاتف
+0086-371-86162511
عنوان
تشنغتشو ، الصين
function of mill in cement manufacturing process
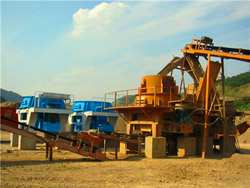
Analysis of material flow and consumption in cement
Clinkering is the primary step in the cement manufacturing process. The function of the kiln in the cement industry is to first convert limestone into lime, then react it with silica, aluminum oxide, and ferric oxide to form clinker compounds: C 3 S, C A cement mill (or finish mill in North American usage ) is the equipment used to grind the hard, nodular clinker from the cement kiln into the fine grey powder that is cement. Most cement is currently ground in ball mills and also vertical roller mills which are more effective than ball mills. Cement mill
احصل على السعر
Optimization of Cement Manufacturing Process
Cement manufacturing process is now operated with the aid of various control systems, such as raw meal composition control, kiln control and mill control. There are four stages in the manufacture of portland cement: (1) crushing and grinding the raw materials, (2) blending the materials in the correct proportions, (3) burning the Cement Extraction, Processing, Manufacturing Britannica
احصل على السعر
Rawmill
A raw mill is the equipment used to grind raw materials into "rawmix" during the manufacture of cement. Rawmix is then fed to a cement kiln, which transforms it into clinker, which is then ground to make cement in the cement mill. The raw milling stage of the process effectively defines the chemistry (and therefore physical properties) of the finished cement, and has a large effect upon the effIntroduction Cement is manufactured by heating a mixture of ground limestone and other minerals containing silica, alumina, and iron up to around 1450 C in Cement Finish Milling (Part 1: Introduction & History)
احصل على السعر
11.6 Portland Cement Manufacturing US EPA
11.6 Portland Cement Manufacturing 11.6.1 Process Description1-7 Portland cement is a fine powder, gray or white in color, that consists of a mixture of The portland cement manufacturing industry is relying increasingly on replacing virgin materials with waste materials or byproducts from other manufacturing operations, to 11.6 Portland Cement Manufacturing U.S. Environmental
احصل على السعر
Reducing energy consumption of a raw mill in cement
Raw mills are used to grind the raw materials into the farine which is the semi product of clinker. It is then fed to the rotary burners which transforms it into clinker Cement production is one of the most energy-intensive manufacturing industries, and the milling circuit of cement plants consumes around 4% of a year's Modeling of energy consumption factors for an industrial cement
احصل على السعر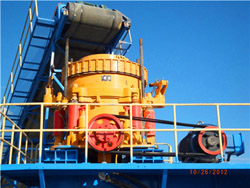
Corrosion Assessment of Gas Conditioning Tower in Cement Manufacturing
wool and aluminium that functions to minimize the power consumption by about 0.5 kWh/ton of Raw Mill fossil fuels to produce energy needed for the cement manufacturing process.In this process, the steps of raw material processing, fuel preparation, clinker burning and cement grinding constitute major emission sources for particulate components. While particulate emissions of up to 3,000 mg/m 3 were measured leaving the stack of cement rotary kiln plants as recently as in the 1960s, legal limits are typically 30 mg/m 3 today, Cement kiln
احصل على السعر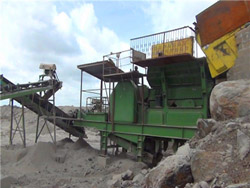
Coal Mill In Cement Plant, Air-swept Coal Mill Coal Mill
AGICO CEMENT supplies air-swept coal mill in cement plant, you can choose coal mill from trustedChina cement plant manufacturer. welcome to contact! Skip to content +86 13683722138. Slag Cement Manufacturing Process. rotary kiln for sale. Activated Carbon Rotary Kiln. Lime Rotary Kiln. Gypsum rotary kiln. 0.5mm Tolerance Cement Cement grinding is a key process in the cement industry. During this phase,gypsum and mineral or artificial raw materials (eg pozzolan, ash, limestone) are added to the clinker (basic raw material for cement production) and, then grinded in special mills until a very small grain size is achieved. During the grinding process, corrective(287a) Machine Learning for Process Applications in Cement
احصل على السعر
The 6 Main Process Fans in Cement factory
Raw mill exhaust fans or stack fans are also called as de-dusting fans. In cement industry raw mill exhaust fans handle 2.2 ton of exhaust gases for the production of 1 ton of clinker. Raw mill exhaust fans are operated with very adverse situations because the fan handles mainly gases such as CO2, N2, NOx and Sox along with some dust particles.The process of manufacturing cement is known to be an energy-intensive process; it involves the consumption of coal (fossil fuel), electrical energy, as well as other resources of energy, and thisEnergy consumption assessment in a cement production plant
احصل على السعر
11.6 Portland Cement Manufacturing U.S. Environmental
11.6 Portland Cement Manufacturing 11.6.1 Process Description1-7 Portland cement is a fine powder, In the wet process, water is added to the raw mill during the grinding of the raw materials in ball as a function of location and temperature of Clinker grinding technology is the most energy-intensive process in cement manufacturing. Traditionally, it was treated as "low on technology" and "high on energy" as grinding circuits use more than 60 per cent of total energy consumed and account for most of the manufacturing cost. Since the increasing energy cost started burning the benefits Clinker grinding technology in cement manufacturing
احصل على السعر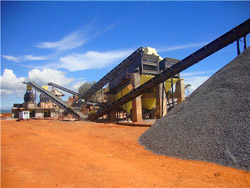
Volume 3, Issue 5, November 2013 Study of Processing and IJEIT
II. STAGES OF CEMENT MANUFACTURING Stage-1.Opencast lime stone mining function of the hammer at a high speed, the materials are thrown to the impact device above the rotor continuously. Process of raw mill The cement industry is highly energy-intensive, consuming approximately 7% of global industrial energy consumption each year. Improving production technology is a good strategy to reduce the energy needs of a cement plant. The market offers a wide variety of alternative solutions; besides, the literature already provides reviews of Technological Energy Efficiency Improvements in Cement Industries
احصل على السعر
Effects of Mill Speed and Air Classifier Speed on Performance of
Optimum performance of ball mill could potentially refine Blaine fineness, thereby improving the cement quality. This study investigates the effects of separator speed and mill speed on BlaineMaterials Many of the precursors and inputs into the cement manufacturing process are inherently abrasive, including limestone, silica, slag, ash, and others. the airlock function. Finish mill feeders must handle large throughputs, 100 What You Need to Know About Rotary Feeders In Cement Plants
احصل على السعر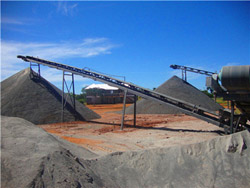
Cement Manufacturing Process sbmchina
Generally speaking, limestone accounts for 80% of the raw materials for cement manufacturing, which is the main material for cement manufacturing. Classification of cement. According to application and performance, cement can be divided into: (1) General cement: general cement usually used in general civil engineering.11.6 Portland Cement Manufacturing 11.6.1 Process Description1-7 Portland cement is a fine powder, gray or white in color, that consists of a mixture of hydraulic cement materials comprising primarily calcium silicates, aluminates and aluminoferrites. More than 30 raw materials are known to be used in the manufacture of 11.6 Portland Cement Manufacturing US EPA
احصل على السعر
How To Measure Your Cement Mill And Cement Classifier? AGICO CEMENT
With the increase of cement mill specifications and the requirement of energy saving, high yield, and high quality of cement grinding plant, the closed-circuit grinding is an inevitable trend of cement grinding unit.The essential equipment of a closed-circuit grinding system is a cement classifier, also known as a cement separator.The All the cement plants set up after 1980 use the dry process for the manufacture of cement. In this process, the calcareous materials such as limestone are crushed and stored in silos or storage tanks. The argillaceous material such as clay is thoroughly mixed with water in a container known as the wash mill.Cement Manufacturing Process: How the Cement is Made?
احصل على السعر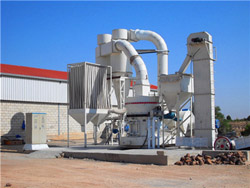
11.6 Portland Cement Manufacturing U.S. Environmental
11.6 Portland Cement Manufacturing 11.6.1 Process Description1-7 Portland cement is a fine powder, In the wet process, water is added to the raw mill during the grinding of the raw materials in ball as a function of location and temperature of The results show that approximately 2.48 t, 4.69 t, and 3.41 t of materials are required to produce a ton of the product in raw material preparation, clinker production, and cement grinding stages, and their waste rates are 63.31%, 74.12%, and 78.89%, respectively. The recycling rate of wastes during clinker production is remarkably higher Analysis of material flow and consumption in cement production process
احصل على السعر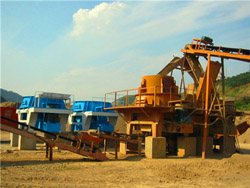
INFINITY FOR CEMENT EQUIPMENT Everything you need to
Scheduling of the cement mill in most cement plants is Points in the cement manufacturing process are identified as to frequency of required analysis and for long- and/or short-term analyses, quality control reports, etc. By automating the laboratory and integrating its function into the cement plant enterprise, greater
احصل على السعر- antimony flotation equipment for zircon in puerto rico
- مورد كسارة tph من الصين
- الآلات والمعدات صخرة محطم
- النحاس النحاس المستديرة
- Ilmenite Beneficiation Plant What Is Calcination
- شروط تعدين الذهب
- مطحنة الخرز للحبر الصين
- تعدين كسارة مخروطية ثابتة للبيع
- made in china agitation tank
- أهمية تكسير قيمة الركام
- آلة النقش تأثير
- از تجهیزات سنگ شکن آزمایشگاهی استفاده می شود
- Mining Machinery Manufacturer Spiral Separator Supplier
- تامین کننده آسیاب توپ با انرژی بالا
- سعر كسارة تصادمية الدولوميت المحمولة في أنغولا