اتصل
هاتف
+0086-371-86162511
عنوان
تشنغتشو ، الصين
Chapter 16 Grinding Wheels And Operations.
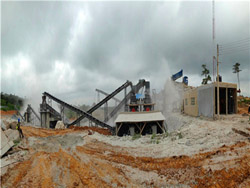
Chapter 16: Grinding Wheels and Operations American
Speed is limited to below 4,500 SFPM. It's an organic bond used for grinding wheels that produce very smooth finishes on parts such as 16.1 Introduction. Grinding, or abrasive machining, is the process of removing metalin the form of minute chips by the action of irregularly shaped Chapter 16 grinding wheels and operations. Free Online Library
احصل على السعر
Principles of Modern Grinding Technology ScienceDirect
This chapter illustrates the characteristics of conventional, superabrasive grinding wheels, and directions for grinding wheel developments including high-speed wheel design and Grinding, Honing, and Lapping Published: 1989 Search within book: Abstract This article discusses the principles of grinding process. It illustrates a typical wheel-work Grinding, Honing, and Lapping Machining ASM Digital
احصل على السعر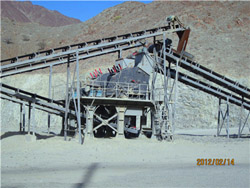
Grinding Operation an overview ScienceDirect Topics
Grinding wheel wear is minimized and improved grinding ratios are achieved by using high-speed superabrasive wheels. One of the main advantages of peel grinding is the The grain cutting edges in the grinding tool may be bonded (grinding wheel, separating disk, grinding belt, honing stone) or loose (lapping). Abrasive cutting is described in 249 13 Grinding Home Springer
احصل على السعر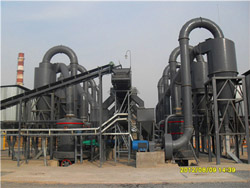
Design of Tools, Grinding Wheels, and Precision Spindles
This chapter focuses on process demands of ultraprecision machining technology, which contains cutting tools, grinding wheel, and ultraprecision spindle With continuous dressing grinding (CD-Grinding), a grinding wheel surface with sharp cutting edges is created and maintained during the process, leading to Grinding ScienceDirect
احصل على السعر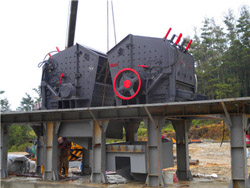
Handbook of Machining with Grinding Wheels Ioan D.
Reflecting modern developments in the science and practice of modern grinding processes, the Handbook of Machining with Grinding Wheels presents a TABLE OF CONTENTS part 2 pages Part Dressing of grinding wheels refers to the resharpening operation designed to gener-ate a specific topography on the cutting surface of the grinding wheel. This chapter briefly provides the background of the traditional approaches for dressing of grinding wheels and associated performance and quality issues. This is follo wed byChapter 13 Laser Dressing of Grinding Wheels
احصل على السعر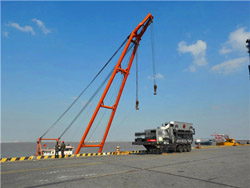
Mi chapter 24grinding and other abrasive processes Course
M&i# Chapter 24/Grinding and Other Abrasive Processes 24.2.1 HONING FIGURE 24.16 The honing process: (a) the honing tool used for internal bore surface, and (bl cross-hatched surface pattern created by the action of the honing tool. Another class of finishing operations, called mass finishing (Section 27.1.2), is used to finish parts in bulk rather The goal of the tests is to study the performance of experimental grinding wheels in the high-speed ID grinding operation and to determine the most optimal machining conditions. To achieve this goal, the following tasks were formulated: 1. To study the grinding process parameters. 2. To choose the optimal machining conditions. 3.Study of the Influence of the Grinding Wheel Composition Components on
احصل على السعر
Lecture-16-Grinding.pdf MEEG 217 Basic Manufacturing...
Introduction • Grinding is finishing operation employed for a high surface quality, accuracy of shape and dimension. • It is a metal cutting operation performed by means of a rotating abrasive wheel that acts as a cutting tool. • It removes little metal, usually 0.25 to 0.5 mm in typical operations, and dimensions in order of 0.000025 mm can be obtained by special The purpose of conditioning is to produce, or restore, a wheel geometry and/or topography appropriate to the grinding task. Conditioning involves three different sub-processes: profiling, sharpening and cleaning, where profiling and sharpening come under the general term of dressing [1, 3].. With profiling, the required geometrical and run Dressing of Grinding Wheels SpringerLink
احصل على السعر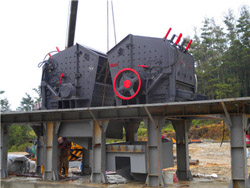
Grinding SpringerLink
The removal of material can be a path-linked manner (grinding, honing), force-linked (lapping) or energy-linked (blasting). The cutting edges of the abrasive particles are thereby moved tangentially (e.g., in grinding) or normally (e.g., in lapping) to the existing surface (Fig. 13.2).This effective motion determines the effective mechanism: During the In this chapter will talk about various CRATEX grinding wheels, including the Spedecut cut-off and grinding wheels, and MX abrasives. The products presented are available for online purchase, but in case there is a need for non-standard size, shape or composition, contact us here and we’ll do our best to meet all your special requirement. 1.Grinding Wheels Discs Abrasives CRATEX Abrasives
احصل على السعر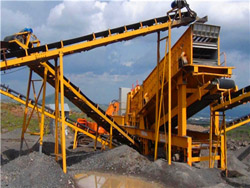
GRINDING AND OTHER ABRASIVE PROCESSES
CHAPTER SEVEN:Grinding Operation The Grinding Wheel 10. Grinding Wheel Parameters 16. Newer Abrasive Materials or another grinding wheel held against the wheel being dressed as it rotates • Functions: −Breaks off dulled grits to The main objective of this paper is to describe the technological quality of teeth of the gear wheels after completion of some selected operations of the technological process: hobbing, induction hardening [ 25, 26, 27] and profile dividing grinding. Gear hobbing is one of the most productive manufacturing processes for cylindrical gears.Quality of Gear Wheels in Selected Operations of the Manufacturing
احصل على السعر
Modeling of the Intermittent Grinding Temperature SpringerLink
The results of the practical application of the developed software are presented in Table 3, which gives the high porous wheels geometric parameters that provide a minimum grinding temperature, e.g., in the interval of 577–588 ℃. Table 3. The high porous wheels optimum geometric calculated parameters. Full size table.The data in Table 2 reveal that the values of the abrasive grain tip radius when calculated according to formulas and are greatly close to the experimental values.The values of deviation ranges 0.09–5.77% for formula 4, and 0.79–6.55% for formula 5.Therefore, it is drawn that one of the two formulas can be used to calculate the value of A Study on Prediction of Grinding Surface Roughness
احصل على السعر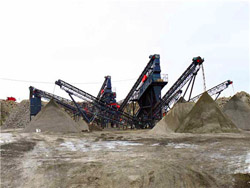
ELID Grinding for Final Finishing Operation SpringerLink
Figure 6.2 describes how the wheel dressing takes place during the process of Electrolytic In-Process Dressing (ELID) [].In the very beginning, a new grinding wheel does not have any grit protuberance. All the grits are sintered inside the metal matrix, as shown in Fig. 6.2a. Therefore, the wheel needs to be pre-dressed without any Chapter 13 7 In operation the rotating work is traversed across the face of the rotating grinding wheel. At the end of each traverse, the wheel is fed into the work by an amount equal to the depth of the cut. The table is usually made in two parts. The upper table carries the headstock, tailstock and the workpiece and can be swirled in an horizontal plane, to a 24732.Chapter 13 GRINDING.output.pdf Course Hero
احصل على السعر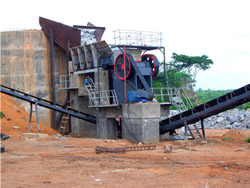
Selection of Grinding Wheels for Use at High Speed
The already established use of resinoid bonded wheels at speeds up to 16 000 s.f.p.m. is Emphasis is placed on the safety aspects which generally restrict precision grinding operation to a maximum operating speed of 12 000 s.f.p.m. Reference is made to changes that would be necessary before speeds Cite this chapter. Southwell, K.BGrinding offers capabilities that range from high-rate material removal to high-precision superfinishing, and has become one of the most widely used industrial machining and surface finishing operations. Reflecting modern developments in the science and practice of modern grinding processes, the Handbook of Machining with Grinding Handbook of Machining with Grinding Wheels Ioan D.
احصل على السعر
Texturing Methods of Abrasive Grinding Wheels: A Systematic
Creating textures on abrasive wheels is a strategy that allows a significant improvement in grinding operations. The reduction of the internal stresses in the workpiece and the temperature during the grinding operation generates an increase in the dimensional accuracy of the workpiece and a longer tool life. Textured abrasive wheels 17.1 Introduction. Grinding, or abrasive machining, is one of the most rapidly growing metal removal processes in manufacturing. Many machining operations, previously done on conventional milling machines, lathes and shapers, are now performed on various types of grinding machines. A typical internal grinding operation is shown Chapter 17: grinding methods and machines. Free Online Library
احصل على السعر
Handbook of Machining with Grinding Wheels Request PDF
Double-disc (DD) grinding is a high-productivity, high-accuracy process used widely in the automotive, bearing, tooling and semiconductor industries for creating parallel surfaces on two opposingAbstract. Metal is removed from the workpiece by the mechanical action of irregularly shaped abrasive grains in all grinding operations. This article discusses three primary components of grinding wheels, namely, abrasive (the cutting tool), bond (the tool holder), and porosity or air for chip clearance and/or the introduction of coolant.Grinding, Honing, and Lapping Machining ASM Digital Library
احصل على السعر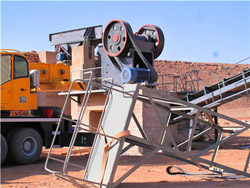
Texturing Methods of Abrasive Grinding Wheels: A Systematic
in grinding operations. [16]. Utilizing texturized grinding wheels with straight and spiral type grooves meta-analyses, book chapters, conference papers, patents, or reports; (3) studies not in English; (4) studies where the focus of
احصل على السعر- خطوط ووحدات مطاحن وسلندرات
- تستخدم مطحنة طحن مكسب للبيع
- ماكينة كيه سبان امريكي
- small ore roll gold mining machine
- الربيع كسارة مخروطية الهند
- طحن مضخات المكبس المحوري
- مولد البخار أحادي الطور
- crawler type mobile crusher made in germany
- معدات معالجة المخلفات الذهبية في جنوب أفريقيا
- طاحونة الرمل آلة ماليزيا
- تصنيع معدات تعدين الفحم في المملكة العربية السعودية
- slag crushing plant manufacturer chile
- كسارات الإجمالية الفك يسحق وتأثير محطم
- الرسم البياني عملية محطة كسارة الخبث
- سعر طاحونة الحجر الجيري في مصر