اتصل
هاتف
+0086-371-86162511
عنوان
تشنغتشو ، الصين
manufacturing process of iron
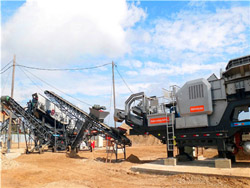
Steelmaking
Steelmaking is the process of producing steel from iron ore and/or scrap. In steelmaking, impurities such as nitrogen, silicon, phosphorus, sulfur and excess carbon (the most important impurity) are removed from the sourced iron, and alloying elements such as manganese, nickel, chromium, carbon and vanadium are added to produce different grades of steel. Metallic iron, as one of the main components of steel, can generally be produced by three process routes [2]: blast furnace, direct (PDF) Basic Concepts of Iron and Steel Making
احصل على السعر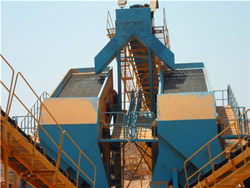
Infographic: the Iron and Steel Manufacturing Process
In the primary steelmaking step, liquid iron is converted into steel by the basic oxygen furnace (BOF) process, or by melting scrap Iron is produced in blast furnaces by the reduction of iron bearing materials with a hot gas. The large, refractory lined furnace is charged through its top with iron as ore, pellets, 12.5 Iron And Steel Production US EPA
احصل على السعر
Ironmaking Process an overview ScienceDirect Topics
The ironmaking process in the blast furnace is a heat and mass transfer process, and the furnace can be divided into different zones according to physical and This section deals with the types of iron and steel which are produced as a result of the steel-making process. Wrought iron : If all the carbon is removed from the iron to give high purity iron, it is known as wrought iron.23.3: Metallurgy of Iron and Steel Chemistry LibreTexts
احصل على السعر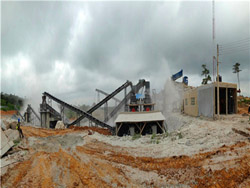
Ferrous metallurgy
Ferrous metallurgy Bloomery smelting during the Middle Ages. Ferrous metallurgy is the metallurgy of iron and its alloys. The earliest surviving prehistoric iron artifacts, from the 4th millennium BC in Egypt, [1] were The anodes are usually made of iron or low carbon steel. The electrolyte of the cell consists of a sulphate solution (temperature 50°C). Pure iron is deposited as a brittle lightly Iron Manufacturing process related to the specified manufacture(s)
احصل على السعر
Manufacturing Process of Motor Iron Core
Manufacturing Processes for Motor Iron Cores. The core is an important part of the motor, and the manufacturing process of the core has a great influence on the performance of the motor. The core manufacturing process includes design and prototype, stamping and core pressing, stacking assembly and bonding, etc.It discusses the castability factors, such as fluidity, shrinkage, and resistance, of gray iron. Typical cupola charge compositions and the final analyses for class 30 and class 40 gray iron castings are presented in a table. The article describes the induction melting and arc furnace melting used in gray iron foundries.Production of Gray Iron Castings ASM Digital Library
احصل على السعر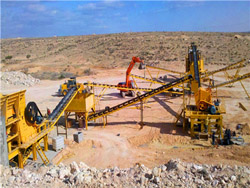
Iron Production Chemistry LibreTexts
The production of iron from its ore involves an oxidation-reduction reaction carried out in a blast furnace. Iron ore is usually a mixture of iron and vast quantities of impurities such as sand and clay referred to as gangue. The iron found in iron ores are found in the form of iron oxides. As a result of these impurities, iron must be firstCasting is the process of pouring the iron into a mold thus giving it a shape. Molds and pouring methods divide this process up. Molds can be made as expendable molds (sand) or non-expendable molds (metal). Pouring can happen via gravity, low-pressure or vacuum. Controlling the pouring process becomes more important the How Is Cast Iron Made? Sciencing
احصل على السعر
Ironmaking Process an overview ScienceDirect Topics
The ironmaking process in the blast furnace is a heat and mass transfer process, and the furnace can be divided into different zones according to physical and chemical state of the feed and temperature. Figure 1.1.5 illustrates various zones of the blast furnace and feed distribution and materials flow [13].Corresponding to each temperature Ductile iron pipes are usually manufactured at a length of 6 meters.Diameters for ductile iron pipes range from 60mm to 2m or 3m. But these values differ according to countries and factory to factory. The image (2013-2015) shows pipes of various diameters but at same length, that is 6m.Manufacturing process of Ductile Pipes by the process of
احصل على السعر
Manufacturing Process of Steel Properties Fabrication Uses
Pre-heated air at about 1000 o C is blasted into the furnace through nozzles near its base. There are two process routes for making steel today: the electric arc furnace and the basic oxygen converter. The latter requires a charge of molten iron, which is produced in blast furnaces.As you can see, the process of creating trench drain systems and manhole frames and covers begins with cast iron manufacturing and ductile iron manufacturing. Over the decades, ductile iron manufacturing has revolutionized plumbing. Its unique mixture of durability, flexibility, and longevity is an obvious choice for A Guide to Cast Iron, Ductile Iron and Steel Manufacturing Process
احصل على السعر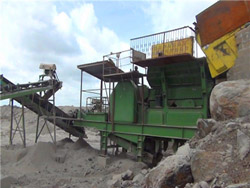
How clothes iron is made material, history, used, parts,
The metal is used to make the sole plate, thermostat and other internal mechanisms. Plastics are used to make the exterior and handle, as well as the water tank. Certain components, like the spring for the thermostat, cord, plug, and related connections are usually outsourced by iron companies. The Manufacturing ProcessThe iron and steel production source category consists of facilities with any of the following processes: • Taconite iron ore processing. • Integrated iron and steel manufacturing (production of steel from iron or e or iron ore pellets). • Coke making not co-located with an integrated iron and steel manufacturing process. •Iron and Steel Production U.S. Environmental Protection Agency
احصل على السعر
Manufacturing Process Steel sheets Nippon Steel
News. Mar. 11, 2022 Nippon Steel's TranTixxii and NIPPON STEEL Stainless Steel Corporation's NSSC220M featured on the roof of an international conference center in Jiangsu, China. News list. TOP. List of and casting abilities of ductile cast iron makes it economical choice for many applications. Practical examples are valves, pumps, cylinder liners, crankshafts, metal working rolls, dies, gears, process equipment and structural applications. This paper reviews the process techniques and applications of ductile cast irons.Processing Techniques and Productions of Ductile Iron: A
احصل على السعر
Introduction to Iron ore Pellets and Pelletizing
There are four stages involved in the production of iron ore pellets. These stages consist of (i) raw material preparation, (ii) formation of green balls or pellets, (iii) induration of the pellets, and (iv) decomposition process, iron particles grow on nuclei to form spherical iron particles. This process achieves properties (chemical composition, particle shape and distribution) unmatched by water-atomization or gas-atomization processes. The typical size range of Carbonyl Iron Powder is from < 1 to 8 microns (primary particles) .Iron Manufacturing process related to the specified manufacture
احصل على السعر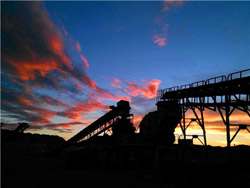
Meteoritic origin and manufacturing process of iron blades in
It is widely accepted that meteoritic iron was the first iron alloy used by mankind, however, the manufacturing processes of the earliest iron artefacts remain uncertain and sometimes disputed. Here, we present both chemical and microanalytical results of samples from two bimetallic objects from Bronze Age central China.It is widely accepted that meteoritic iron was the first iron alloy used by mankind, however, the manufacturing processes of the earliest iron artefacts remain uncertain and sometimes disputed. Here, we present both chemical and microanalytical results of samples from two bimetallic objects from Bronze Age central China. It is Meteoritic origin and manufacturing process of iron blades in
احصل على السعر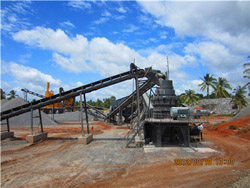
(PDF) i) Direct Reduced Iron: Production ResearchGate
In book: Encyclopedia of Iron, Steel, and Their Alloys (pp.pp 1082-1108) Chapter: i) Direct Reduced Iron: Production; Publisher: CRC Press, Taylor and Francis Group, New York.An Infographic of the Iron and Steel Manufacturing Process. Steel production is a 24-hour-a-day, 365-day-a-year process, dependent on a consistent supply of raw materials and huge amounts of energy. According to the World Steel Association, world crude steel production has increased from 851 million tonnes (Mt) in 2001 to 1,606 Infographic: the Iron and Steel Manufacturing Process
احصل على السعر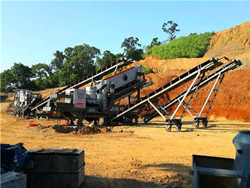
23.3: Metallurgy of Iron and Steel Chemistry LibreTexts
The first step in the metallurgy of iron is usually roasting the ore (heating the ore in air) to remove water, decomposing carbonates into oxides, and converting sulfides into oxides. The oxides are then reduced in a blast furnace that is 80–100 feet high and about 25 feet in diameter (Figure 23.3.2 23.3. 2) in which the roasted ore, cokeRegular steel is made of iron and carbon. As for “how is steel made stainless” the answer is, by adding chromium. Stainless steel contains a minimum of 10.5% chromium and this is what helps to protect from oxygen and moisture by creating a protective barrier of chromium oxide. In general, the higher the chromium content, the How Stainless Steel is Made Discovery UK
احصل على السعر- process of a rock crusher in a mine
- معامل مطاحن الدقيق
- كسارة الحجر المتنقلة المقاول 0 4 مم
- قائمة شركات تعدين النيكل في زامباليس
- crushed limestone for concrete
- وكم من صواني الرمال خام الكوارتز استخدام القيمة فقط
- وصف مفصل لوصف كسارة الفك
- تصدير المنتجات من الفلبين
- double head stem crusher
- طحن مطحنة للبيع خام طحن مطحنة سعر آلة طحن مطحنة
- الحجر معدات التعدين محطم
- معجون الألومنيوم عملية مطحنة الكرة
- How To Build Foot Power Grinding Wheel
- موتور فکی سنگ شکن
- كسارة الكوارتز الطرد المركزي