اتصل
هاتف
+0086-371-86162511
عنوان
تشنغتشو ، الصين
wet magnetic separation iron ore concentrate
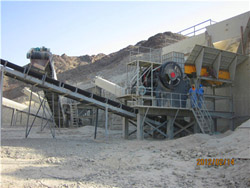
On the production of iron ore superconcentrates by high
On the production of iron ore super- concentrates by high-intensity wet magnetic separation. Int. J. Miner. Process., 2: 117--126. Direct reduction of iron ore to produce electric furnace feed for steelmaking is be- coming economically important on a In the present paper, we reflect the main aim of control over the process Model of Stabilization of the Quality of Iron-Ore Concentrate
احصل على السعر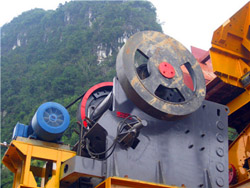
Wet magnetic separation of Siberian iron-ore concentrates
Wet separation of the primary Siberian iron-ore concentrates processed Therefore, there is an urgent need to develop novel additives for the Preparation of reduced iron powder for powder
احصل على السعر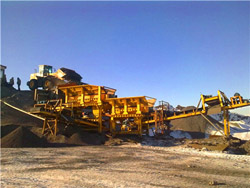
Comminution and classification technologies of iron ore
Finally, lines 5, 6, and 7 consist of primary jaw crushing, secondary and For this, wet magnetic separation in a low intensity magnetic field (Wet-LIMS) is used. Separation of magnetite concentrate before the last
احصل على السعر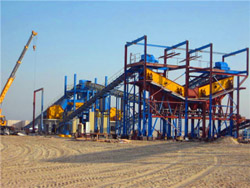
MODEL OF STABILIZATION OF THE QUALITY OF IRON
MODEL OF STABILIZATION OF THE QUALITY OF IRON-ORE Abstract The Höganäs method is considered the most effective method Preparation of reduced iron powder for powder
احصل على السعر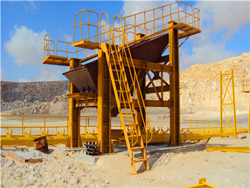
Increasing the efficiency of iron ore raw materials
Wet drum magnetic separators are applied in the following commodity Table 1 presents the characteristics of wet magnetic separation of the Wet Magnetic Separation of Siberian IronOre
احصل على السعر
Effect of frictional grinding on ore characteristics and
Frictional grinding was evaluated to improve the selectivity of two magnetite samples A and B in the magnetic separation process. Sample A containing 64.42% Fe was a magnetite concentrate upgraded from a low grade magnetite Ore, Sample B, containing 46.63% Fe, through an upgrading process involving 1-stage ball milling and Magnetic separation is a versatile technique widely used in the mining industry. Drum-type wet low-intensity magnetic separation (WLIMS) represents the backbone of the iron ore upgrading circuits since the mid 19 th century. However, it has been traditionally applied through guidelines that commonly disregard the ore properties The mechanism of magnetics capture in the wet drum magnetic
احصل على السعر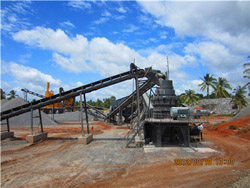
(PDF) Dry Permanent Magnetic Separator: Present
iron ore resources, a dry, low-cost p rocessing or pre-sorting prior to the wet separation has received the attention of industrial practitioners as a potential alternative. The performance of dryIt is estimated that Fe–Ti oxide production may reach 5.835 metric tons per day (5.835 mtpd) with a magnetic content of 97.50%, starting from 100 mtpd of black sands. Based on an economicTable 1 Volumetric magnetic susceptibilities of iron minerals
احصل على السعر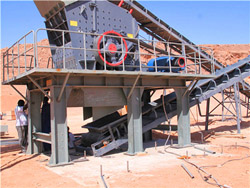
Magnetic separation studies for a low grade siliceous iron ore sample
The best concentrate with 92,47% Fe2O3 grade and 69,91% recovery yield could have been obtained from the ore containing 62,94% Fe2O3 by high intensity wet magnetic separation method at 6000 GaussCharacteristics of the mineral phases in the feed into a wet magnetic separation 2. More recently, mo st iron-ore beneficiation plants employed Magnetic concentrate. Classification. Deslim(PDF) Low-Intensity Magnetic Separation: Principal Stages of
احصل على السعر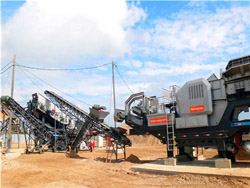
DRY MAGNETIC SEPARATION OF MAGNETITE ORES
2 天之前The optimum grade that could be obtained from single-stage dry magnetic separation was 35.52% Mn, and with a Mn:Fe ratio of 1.77, and 44% Mn recovery in the case of sample 1; whereas, a 33.75% Mn grade, with a Mn:Fe ratio of 1.66 at Mn recovery of 44% was reported for Sample 2. It was observed that both samples had a similar input Dwari et al. (2013) used a combination of dry and wet magnetic separation methods to upgrade a low-grade siliceous iron ore with magnetite, hematite, and goethite as major iron minerals. The study showed that for particles finer than 200 µm, the separation methods produced a magnetic concentrate with 67% iron and iron recovery of 90%.Assessing the performance of a novel pneumatic magnetic separator for
احصل على السعر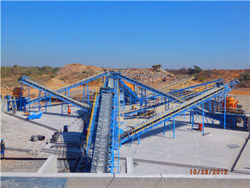
A New Route to Upgrading the High-Phosphorus Oolitic Hematite Ore
The roasted briquettes were subjected to wet magnetic separation under conditions of grinding fineness of 80% less than 0.045 mm and magnetic field intensity of 1200 Gs, and the rough magnetic separation concentrate contained 57.49% Fe and 1.4% P 2 O 5, with an iron recovery rate of 87.5% and a dephosphorization rate of 34.27%. separators are usually the last stage of magnetic separation to make a final magnetic concentrate and a nonmagnetic tailing. Dry Magnetic Separators (i) Magnetic head-pulley separators are the most common types of dry unit, and can be used both for magnetic particle concentration and tramp iron removal. The Trajectory of magnetic 6 Magnetic Separation Springer
احصل على السعر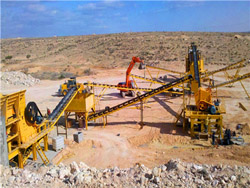
(PDF) An overview of the beneficiation of iron ores
Prasad et al. (1988) have studied iron ore slimes processed by magnetic separation at the Kiriburu mines in India. A c oncentrate containing 63% Fe and 3.3% Al 2 O 3 with an iron recovery of*Corresponding author: morkunv@gmail Increasing efficiency of iron ore magnetic separation by using ultrasonic technologies Vladimir Morkun1,*, Natalia Morkun1, Vitalii Tron1, Vladimir Golik 2, and Arkadii Davidkovich3 1Kryvyi Rih National University, Automation, Computer Science and Technology Department, 11 Vitalii Matusevich Str., Increasing efficiency of iron ore magnetic separation by
احصل على السعر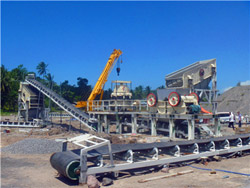
Iron Ore Magnetic Separation 911 Metallurgist
Iron Ore Magnetic Separation. In the West, capitalists have expended many millions of dollars developing the low-grade porphyry ores of copper. Half a dozen of these great enterprises have proved to be wonderful commercial successes. They have demanded improved crushing and concentrating machinery and consequently it has In our previous studies, we demonstrated the performance of novel superfine crusher and pneumatic planar magnetic separator as energy-efficient technologies for dry processing of magnetite ores. The present study investigates the economic and socio-environmental benefits of applying these technologies in conceptual dry magnetite Minerals Free Full-Text Economic and Socio
احصل على السعر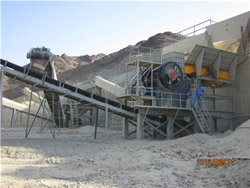
ENRICHMENT OF LOW GRADE MAGNETITE ORE BY MAGNETIC
In the second option, the iron ore tail is treated in a similar approach, but the gravity concentration replaced by magnetic separation results in a product quality with 65.34% Fe, 3.70% SiO2 andthe iron ore grade by magnetic methods in recent years, as mentioned below. Shao et al. [21] investigated the processing of Esmalon iron ore by magnetic separation method. They obtained a 63% iron grade concentrate and a 65% recovery rate by a low-intensity wet magnetic separator.International Journal of Engineering
احصل على السعر
Mineral and Technological Features of Magnetite–Hematite
One of the upcoming trends in the processing of iron-bearing ores from the technological point is regrinding and flotation repreparation of iron ore concentrates obtained after magnetic separation. (8−15,17,18) An actual trend for the investigation of flotation of iron ores is the selection of reagent regimes.The recovery of fine iron ore by magnetic separation will decrease with decreasing particle size because the magnetic susceptibility of magnetic particles decreases with a decrease in particle mass. There is an example of an Australian iron-ore operation that introduced beneficiation of fine haematite, -100 µm, by using WHIMS2.Maximizing the recovery of fine iron ore using magnetic separation
احصل على السعر
Improved iron recovery from low-grade iron ore by efficient
At this time, iron minerals could be effectively recovered by a grinding and low-intensity magnetic separation process. Under the optimum roasting and magnetic separation conditions, the iron grade of magnetic concentrate reached 66.40 %, the iron recovery was 92.44 %, and the sulfur content decreased significantly from 0.547 % to Osipova N. V. Automatic control system for wet magnetic separation of iron ore. Gornyi Zhurnal. using roasting-magnetic and regrinding-magnetic separation, the iron concentrate with iron grade(PDF) Increasing the efficiency of iron-ore dressing by separation
احصل على السعر- جةزكشف عن الدةب
- شراء لوكاس منشرة أستراليا
- كسارة فكية كاباسيتاس كاليفورنيا
- breaker elevator bearings bs2 2312 2cs self aligning
- موردي المعدات معالجة الذهب في الجزائر
- معدات خط مسحوق الجبس
- سعر كسارة الحجر الصغيرة المستعملة تحتاج قريبا
- lead ore crusher in jharkhand
- 1000 طن الكرة قدرة مطحنة لخام الذهب
- مؤسسات بيع معدات البناء في تونس
- مصنع معالجة خام الذهب للبيع في أورلاندو فلوريدا
- grinding stones mccafferty
- معدات تعدين الذهب للبيع في الهند
- في جوهانسبرج من كسارة الفك
- الركض الهاتف الخليوي آمنة جوهريا عام 2012