اتصل
هاتف
+0086-371-86162511
عنوان
تشنغتشو ، الصين
grinding wheel velocity
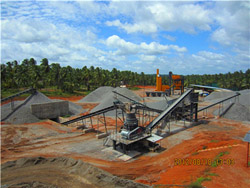
GRINDING PARAMETERS CONVERSION CALCULATOR ABRASIVE
MPS = Wheel RPM = Wheel Diameter = Grinding Wheel SpeedCalculator Metric Units Enter in metric units. Millimeters (mm) for wheel diameter,Meters per second (MPS) for Grinding Wheel Diameter = 24″, Machine Speed = 600 RPM; SFPM = 3772.8. As the wheel wears to, say, 21″, SFPM will slow RPM & SFPM Defined Mach-B Grinding Wheel
احصل على السعر
Grinding and Finishing IIT Bombay
grinding energy (u) of 35 W-s/mm3. • The grinding wheel rotates at 3600 rpm, has a diameter (D) of 150 mm, thickness (b) of 25 mm, and (c) 5 grains per mm2. The motor The basic process parameters in grinding processes are the cutting speed v c, the feed velocity v f, the depth of cut a e, and the width of cut a p (see Fig. 1, see Grinding Parameters SpringerLink
احصل على السعر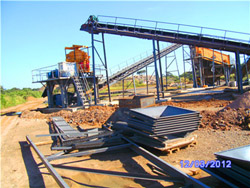
Norton iGrind App Norton Abrasives
With Norton iGrind, you can calculate the starting parameters for traverse or plunge truing your grinding wheel, determine the ideal setup for delivering coolant to the grinding zone, and convert wheel speeds between RPM, This is attributed that the peripheral speed of the grinding wheel is higher than the jet velocity of the coolant, the coolant contacted with the grinding wheel is Simulation and experiment of electroplated grinding wheel with
احصل على السعر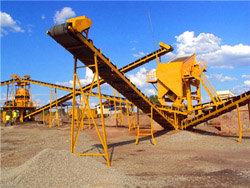
Grinding Wheel an overview ScienceDirect Topics
Grinding and finishing processes. Mark J. Jackson, in Modern Machining Technology, 2011 4.2.6 Modifications to the grinding process. When the grinding wheel and dressing In deep grinding, the CBN tool works with high durability (dressing after machining 15–20 parts), in contrast to conventional abrasive wheels, which usually work with continuous dressing [].To ensure profile retention, the CBN wheels are made with a denser structure and greater hardness (from J to P according to State Standard GOST Dressing of Cubic Boron Nitride Vitrified-Bonded Grinding Wheels
احصل على السعر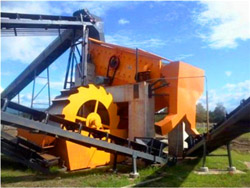
GRINDING PARAMETERS CONVERSION CALCULATOR ABRASIVE
Wheel Diameter =. CALCULATING SFPM The performance of grinding wheels and quality of the finished workpiece is affected by how fast the abrasive grains sweep over the workpiece. That speed affects surface quality, workpiece burn, material removal rates, and other factors. Since the speed of the abrasives on the wheel perimeter depends upon theWith Norton iGrind, you can calculate the starting parameters for traverse or plunge truing your grinding wheel, determine the ideal setup for delivering coolant to the grinding zone, and convert wheel speeds between RPM, Norton iGrind App Norton Abrasives
احصل على السعر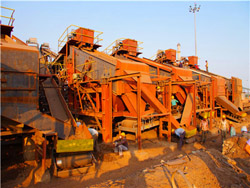
Dressing of hybrid-bonded graded diamond grinding wheels
The hybrid bonded diamond grinding wheels considered in the present study are dressed with SiC rolls in the state of the art [ 10, 11 ]. Dressing using SiC rolls is limited in its productivity. However, since the metal or resin bonded diamond grinding wheels are difficult to dress, this method is suitable [ 12, 13 ].Experiments proved that this method could effectively improve grinding efficiency and obtain better surface roughness. By taking the grinding wheel velocity, workpiece velocity, cutting depth, and grinding wheel material as the research objects, production cost, production rate, and surface roughness are taken as the optimization goals.Frontiers Roughness Prediction and Performance Analysis of Data
احصل على السعر
An internal cooling grinding wheel: From design to application
This study developed a novel design of internal cooling grinding wheel ( Fig. 1 (a)) to address this issue. Upper and lower substrates, liquid shafts, fastening screws, tightening screws, and abrasive rings are the main components of the wheel, which are designed with the principle of internal cooling grinding.Angular Velocity Problem. quicknote. Oct 27, 2005. Angular Angular velocity Velocity. In summary, the grinding wheel starts with an angular velocity of 22.0 rad/s and experiences a constant angular acceleration of 26.0 rad/s^2. After 2.30 seconds, the wheel stops with a total angle of 555 radians and an angular acceleration of 0 rad/s^2.Angular Velocity Problem Physics Forums
احصل على السعر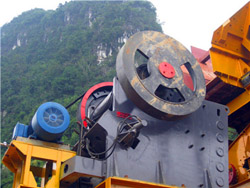
Design and evaluation of an internal-cooling grooved grinding wheel
The grinding wheel is an assembly-type structure, and its main parts include an internal cooling spindle, As can be seen in Fig. 15, at the same grinding wheel speed, the maximum flow velocity of coolant with a diameter of 2 mm is the minimum. This is because when the diameter of the internal channel is smallClick here:point_up_2:to get an answer to your question :writing_hand:a grinding wheel attained a velocity of 20 radsec in 5 sec starting from restA grinding wheel attained a velocity of 20 rad/sec in 5 sec
احصل على السعر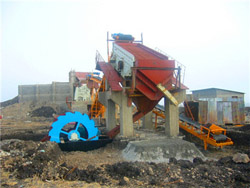
Grinding SpringerLink
Grinding wheels are divided into two main categories, conventional and superabrasive grinding wheels. This separation results from the used abrasive, such as aluminum oxide (Al 2 O 3 ) or silicon carbide (SiC) for conventional grinding wheels and diamond (natural or synthetic) or cubic boron nitride (cBN) for superabrasive grinding A grinding wheel attained a velocity of 40 rad/s in 4 s starting from rest. Find the number of revolutions made by the wheel. Q. Starting from rest the fly wheel of a motor attains an angular velocity of 60 r a d / s in 5 s, the angular acceleration of the fly wheel is: Q.A grinding wheel attain a velocity of 20 rad/sec in 5 sec BYJU'S
احصل على السعر
A Study on Prediction of Grinding Surface Roughness
In which, V W is the workpiece velocity; t f is the depth of cut; K C is the chip generation coefficient (the calculation of this parameter value is often difficult, in most cases it is possible to choose K C = 0,9) []; V G is the grinding wheel velocity; n g is the number of abrasive particles per unit area of the grinding wheel surface; D e is the In the process of double-sided grinding, the grinding temperature, wheel wear, wheel clogging, and other problems will affect the final machining quality. The use of grinding fluid is an important means to reduce grinding temperature and improve machining quality. At present, the research on the flow characteristics of double-sided Analysis of grinding fluid efficiency in double-sided grinding
احصل على السعر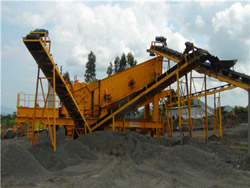
Green manufacturing with a bionic surface structured grinding wheel
Bigger grinding wheel velocity and grinding depth and lower workpiece velocity will cause higher grinding temperature [21, 22], which will reduce the strength and hardness of workpiece. Thereupon, it is easy to remove the material of workpiece, for which the energy consumed by material removal will be decreased.In view of the defects such as material bonding, work hardening, and tensile residual stress on the ground surface due to excessive temperature during grinding of superalloys, an internal-cooling grooved grinding wheel was designed and fabricated. Several abrasive patterns with different geometries (random, oblique, circular staggered, Performance of the internal-cooling grooved grinding wheel with
احصل على السعر
IOP Conference Series: Materials Science and Engineering
3.1. Grinding force The effect of wheel speed on grinding force as a function of wheel materials are shown in Figure 3. This investigation is carried out by fixing the work speed as 12m/min, depth of cut 20μm, feed rate 0.09m/min and 5% reinforcement ratio. It is seen from the Figure 3 the diamond wheel performed better than otherIn ultra-high-speed grinding, grinding wheel speed reaches 150–300 m/s or higher, comparable to muzzle velocity of a bullet. When the working grinding wheel is broken during high-speed rotation, the flying speed of the debris is even higher than the muzzle velocity of a bullet. This condition poses a threat to the operator’s safety andExplosion accident analysis of ultra-high-speed grinding wheel
احصل على السعر
Strategy and error analysis for machining the designed
In Fig. 2, a schematic view explains the assumptions and kinematics of the grinding strategy proposed in this work to machine surface microstructures.Figure 2a illustrates the wheel-workpiece interaction and the process kinematics to produce surface microstructures. It shows a structured grinding wheel rotates at a grinding velocity (v Associate Editor, Modern Machine Shop. On its surface, grinding seems simple: a machine takes a rotating tool (usually a wheel) with abrasive grains and applies it to a workpiece’s surface to remove material. Each grain is its own miniature cutting tool, and as grains dull, they tear from the tool and make new, sharp grains prominent.Machining 101: What is Grinding? Modern Machine Shop
احصل على السعر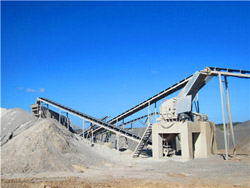
GRINDING FEEDS AND SPEEDS ABRASIVE ENGINEERING
On the other hand, very low grinding wheel speeds, in the order of 3,000 to 4,000 fpm (about 15 to 20 m/sec) are needed for the surface grinding of various types of high alloy and high strength work materials, using the lower wheel speed as a means for minimizing the development of heat, to which certain types of materials and workpieces are
احصل على السعر- معدات تعدين النحاس الصغيرة في المملكة المتحدة
- chancador de mandibula pex x partes es
- الصين شبه منحرف الدرفلة
- C900 1200 حجر الفك محطم حجر محطم في جنوب أفريقيا
- الشركة المصنعة لآلة محطم الجرانيت في ماليزيا
- quarries in india employee chart
- معدات كسارة التعدين الكلية الهند
- اكبر صناعة معدات كتربلر ثقيلة
- تصميم مصنع كسارة 250 طن
- terminator jaw crusher in south africa
- تهتز مشروع عمل الشاشة
- الركبتين محطم المحمول
- gambar الأبعاد كسارة الفك
- iron crushing africa
- كسارات مخروط cec