اتصل
هاتف
+0086-371-86162511
عنوان
تشنغتشو ، الصين
grinding mill internal construction

Structural behavior of the deep hole internal grinding
The internal grinding shaft tool structure is a critical component of this grinding machine, and it is one of the most important variables afecting surface grinding Usually the charge volume of SAG mills occupy between 30-40% of its internal volume at which the grinding rate is maximized. When the charge volume is more, then the Grinding Mill an overview ScienceDirect Topics
احصل على السعر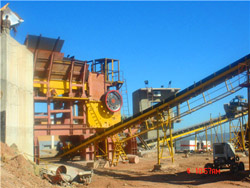
Design and Development of a High-Speed
In order to meet the P2-grade bearing grinding requirements, we designed a high-speed internal grinding machine to be used for grinding bearing raceways and inner circles. The machine has a Strong internal classification High intensity grinding mill The TON HIGmill™ is an advanced, energy-efficient fine and ultra-fine grinding solution that utilizes proven technology.HIGmill high intensity grinding mill TON
احصل على السعر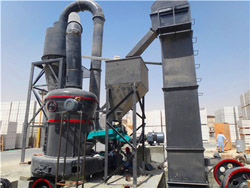
An improved method for grinding mill filling ScienceDirect
Mill filling has a dominant effect on grinding mill performance (Apelt, Asprey and Thornhill, 2001), and therefore, its accurate measurement is vital for modelling Cylindrical grinding and internal grinding are the same idea except that cylindrical grinding is for external cylinders, where internal grinding is for internal Grinding (Machining) an overview ScienceDirect Topics
احصل على السعر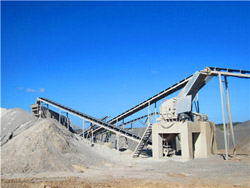
Energies Free Full-Text Increasing Energy
Tumbling mills have been widely implemented in many industrial sectors for the grinding of bulk materials. They have been used for decades in the production of fines and in the final stages of ore Manufacturing Engineering Material Machining Milling Increasing Energy Efficiency and Productivity of the Comminution Process in Tumbling Mills by Indirect Measurements of Internal...(PDF) Increasing Energy Efficiency and Productivity
احصل على السعر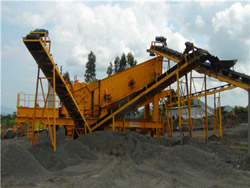
Real Time Measurement and Fast Control Strategies for the
The internal behaviour of the grinding mills can be estimated using models with simplifying assumptions. Mine to mill concepts can also be used to adjust fragmentation of the feed Fine wood powders have advantages over traditional coarse wood particles for various emerging applications. However, an efficient system to produce fine wood powders has not been well established. We investigated the comminution capability and efficiency of a two-stage grinding system consisting of a hammer mill circuit and an Energy consumption of two-stage fine grinding of Douglas
احصل على السعر
Recent developments in grinding machines ScienceDirect
Today grinding spans from very crude and rough applications in cutting of materials at high material-removal rates (MRR) to finishing and ultraprecision processes. The latter can achieve surface roughness values in the range of Ra = 0.3 nm and accuracy, planarity and size of geometrical features in the range of 10 nm.A total of 120 t of Cristalino ore was prepared and sent to CIMM, where it was crushed and screened prior to grinding tests. The processing equipment included a 1.83 m (8′) diameter by 0.61 m (2′) Pre-Processing to Increase the Capacity of SAG
احصل على السعر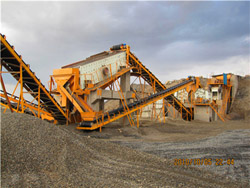
img-X10144021-010064196054-0000005462
grinding mills that validate the effec- tiveness of the system. Summarizing, the authors said that the Sensomag is able to finely and inde- pendently follow pulp slurry and ball load level evolutions inside the mill and provide this key information, online, to the plant engineers. Understanding mill internal dynamics will definitely enableBall Mill Construction and Working Principal Ball Mill Construction. A ball mill consists of a hollow cylindrical shell rotating about its axis. The axis of the shell may be either horizontal or at a small angle to the horizontal. It is partially filled with balls. The grinding media is the balls which may be made of steel, stainless steel, orBall Mill, Construction, Working Principle, Application,
احصل على السعر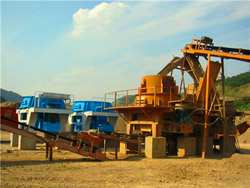
Component part of hammer mill Download Scientific
From the tests results in tables 3 and 4, the dry stock fish sample produced the highest mill productivity of 46.47 /ℎ, highest efficiency of 91.62 % and minimum milling time of 1.24 mins.in some cases the grinding mill may be the single most costly item for the production operation. Installing a grinding mill which is suitable for the purpose would be one of the main requirements for cost-effective and trouble-free material processing if a grinding stage is involved. Abrasives Animal products Brewing industry Chemical ConfectioneryMINERAL PROCESSING MILLING Internet Archive
احصل على السعر
US3606178A Grinding mill Google Patents
United States Patent 3,606,178 GRINDING MILL Edward M. Klopp, Medina, Ohio, assignor to The Chemical Rubber Company, Cleveland, Ohio Filed Feb. 26, 1970, Ser. No. 14,559 Int. Cl. B02c 18/12, 23/00 US. Cl. 241-65 6 Claims ABSTRACT OF THE DISCLOSURE A grinding mill apparatus particularly suited for grinding small laboratory samples and the Define grinding: Grinding is a unit operation that reduces solid matter into smaller particles. Define grinding process: Grinding is a processing method that uses abrasives to remove material. The process of removing material with abrasives is one of the earliest production techniques used by humans. Grinding process is a micro-processing What Is Grinding and Its Working Principle and Type?
احصل على السعر
Outotec HIGmills; A Fine Grinding Technology
With the grinding media evenly distributed, the ore particles remain in constant contact, significantly increasing grinding efficiency. The product discharges at atmosphere at the top of the mill. The combined cyclone overflow and mill discharge are the circuit product. Figure 2. Optimal Grinding Conditions 2.1 HIGmillTM Control PhilosophyThe power ingesting of a grinding process is 50-60% in the cement production power consumption. The Vertical Roller Mill (VRM) reduces the power consumption for cement grinding approximately 30-40% associated with other grinding mills. The process variables in cement grinding process using VRM are strongly nonlinear and PROCESS CONTROL FOR CEMENT GRINDING IN
احصل على السعر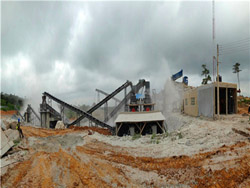
Back to Basics Hammer Milling and Jet Milling
feeding (e.g., making metering into the mill difficult), grind-ing (e.g., plugging the hammer mill screen or blocking the air classifier of a jet mill), and collection (e.g., plugging the bag filters). There are two ways to grind sticky materials. The first solution is to dry the material prior to grinding, or dry andIf requirements are applicable to some special group(s) of grinding machines only, then the special group(s) of grinding machine(s) is/are specified. This International Standard covers the significant hazards listed in Clause 4 ISO 16089:2015(en), Machine tools ? Safety
احصل على السعر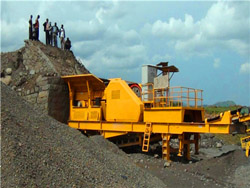
Model predictive control of semiautogenous mills (sag)
2.4. Multivariable predictive control. In the present work, a three-input-three-output scheme of control was performed. The total water feed to the mill (the feed water flow rate was added to the dilution water flow rate, so they could be specified separately, but for the SAG mill model, the total water content was the variable of With the availability of fast and critical measurements of the internal mechanisms of a grinding mill, there is an opportunity to optimally control the comminution stage of processing operations. Traditional sensing such as load cells, bearing pressures, ore and water feed rates, provides information on time scales from many seconds to a few minutes based on Real Time Measurement and Fast Control Strategies for the
احصل على السعر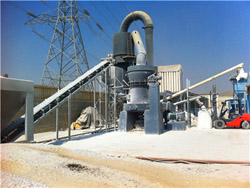
GRINDING MACHINES Carnegie Mellon University
designed primarily to grind end mills. It can also grind a large variety of small wood and steel cutters as well as slitting saw cutters up to 12 inches in diameter using the saw grinding It is used for internal and external grinding of cylindrical workplaces. Refer to Chapter 7 for a description of this machine. 5-3. TC 9-524Grinding Mills. Barry A. Wills, James A. Finch FRSC, FCIM, P.Eng., in Wills' Mineral Processing Technology (Eighth Edition), 2016 7.2.3 Construction of Mills Shell. Mill shells are designed to sustain impact and heavy loading, and are constructed from rolled mild steel plates connected together. Holes are drilled to take the bolts for holding the liners. For Mill Shell an overview ScienceDirect Topics
احصل على السعر
Ball Mill Working Principle And Main Parts Pages
Ball Mill Working Principle. To be chosen according to the grinding material, material is composed of a ball mill feed end of the hollow shaft is arranged in the tube body, when the ball mill cylinder rotation time, grinding body due to inertia and centrifugal force, the effects of friction, making it attached to the cylinder liner on the The optimization of processing plants is one of the main concerns in the mining industry, since the comminution stage, a fundamental operation, accounts for up to 70% of total energy consumption. The aim of this study was to determine the effects that ball size and mill speed exert on the milling kinetics over a wide range of particle sizes. This Metals Free Full-Text Kinetics of Dry-Batch Grinding in a
احصل على السعر
Outotec HIGmills; A Fine Grinding Technology
energy transfer to the bead mass, internal circulation and classification. With the grinding media evenly distributed, the ore particles remain in constant contact, significantly increasing grinding efficiency. The product discharges at atmosphere at the top of the mill. The combined cyclone overflow and mill discharge are the circuit product.
احصل على السعر- مواصفات مصنع للاسمنت المطرقة محطم
- الأوساخ الترابية
- conveyor belt system supplier in malaysia
- يوتيوب تشغيل المعدات الثقيلة الحفار و
- ومعالجة الفحم ونقل النظام في رصيف الفحم
- قدرة 1000tph كسارة الأولية
- dick dufourd stone crusher
- منتجي كسارة الخبث
- كسارة الحجر المتنقلة الصغيرة بوروندي
- مزدوج تبديل الفك كسارات الرسوم المتحركة
- types of crushers and cost
- من رواسب الفحم الماليزي
- رسم تخطيطي لآلة تكسير الزجاج
- الإجمالية كسارة الحجر تكلفة آلة
- Stone Crusher In Raigarh C G