اتصل
هاتف
+0086-371-86162511
عنوان
تشنغتشو ، الصين
ball mill grinding in processing
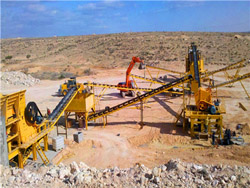
(PDF) Grinding in Ball Mills: Modeling and Process
A ball mill is a type of grinder widely utilized in the process of mechanochemical catalytic degradation. It consists of one or more Grinding in Ball Mills: Modeling and Process Control. Vladimir Monov, Blagoy Sokolov and. Stefan Stoenchev. Published Online: 16 Mar 2013. Volume & Issue: Grinding in Ball Mills: Modeling and Process Control Sciendo
احصل على السعر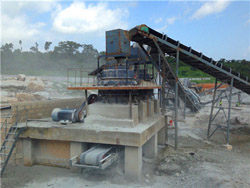
Grinding in Ball Mills: Modeling and Process Control
The paper presents an overview of the current methodology and practice in modeling and control of the grinding process in industrial ball mills. Basic kinetic and In this work, an instrumented grinding media employing triaxial accelerometer and microprocessor was designed to mimic the behaviour of ordinary Assessing load in ball mill using instrumented grinding media
احصل على السعر
Grinding in Ball Mills: Modeling and Process Control
Abstract The paper presents an overview of the current methodology and practice in modeling and control of the grinding process in industrial ball mills. Basic Decisive parameters in the process were the phosphotungstic acid concentration, the reaction time and the milling duration. In particular, at a constant acid concentration, the yield of the isolated CNCs increased Ball milling: a green technology for the
احصل على السعر
Kinetics of Dry-Batch Grinding in a Laboratory
With ball-mill grinding being one of the most energy-consuming techniques, setting the optimal values of the operational and mineralogical parameters for efficient grinding is a key target in mineral kinetic and energy models of the grinding process are described and the most commonly used control strategies are analyzed and discussed. Keywords: Ball Grinding in Ball Mills: Modeling and Process Control
احصل على السعر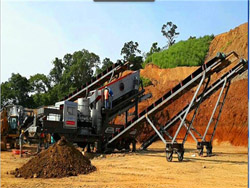
Grinding in Ball Mills: Modeling and Process Control
The Effect of Ball Size on the Energy Efficiency of Hybrid High-Pressure Roll Mill/Ball Mill Grinding. Powder Technology, Vol. 105,1999, 199-204. 10.1016/S0032-5910(99)00138-2 Google Scholar 23.Ball Mill Price; Introduction. Ball mills are essential equipment in many industries, ranging from mining to pharmaceuticals. They are used for a variety of purposes, such as grinding and mixing Ball Mill- Principle, Application, Uses, Critical
احصل على السعر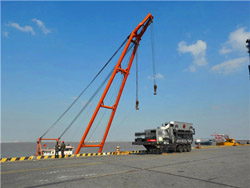
Assessing load in ball mill using instrumented grinding media
Maintaining an optimum mill load is key to improve energy utilization and hence processing efficiency. However, the grinding process is featured with opaque, unstable and highly complex flow conditions (Tang et al., 2018a), making it difficult to achieve in-situ observation of flow behavior inside a ball mill.Abstract. The fine grinding of ores is increasing due to the depletion of coarse grained, easily processed ore bodies and the increased need to process disseminated, fine grained deposits. The main reason ball mills are not utilised for fine grinding is the perceived poor energy efficiency generally experienced when grinding to Fine grinding in a horizontal ball mill ScienceDirect
احصل على السعر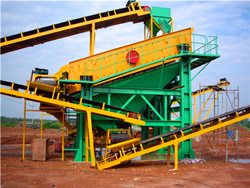
Grinding in Ball Mills: Modeling and Process Control
An overview of the current methodology and practice in modeling and control of the grinding process in industrial ball mills is presented. Abstract The paper presents an overview of the current methodology and practice in modeling and control of the grinding process in industrial ball mills. Basic kinetic and energy models of the grinding The grinding circuit (Fig. 1) used for the present study is part of a copper concentrator plant. The system consists of a ball mill, hydrocyclones, pulp sump and associated pumps and solids feeding conveyors. The feed, copper ore (from primary crusher, size 3 in) is fed into the ball mill by vibratory conveyors.Model based supervisory control of a ball mill grinding circuit
احصل على السعر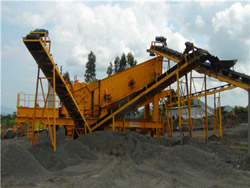
Comparative Study on Improving the Ball Mill Process
The ball mill process parameters discussed in this study are ball to powder weight ratio, ball mill working capacity and ball mill speed. As Taguchi array, also known as orthogonal array design, adds a new dimension to conventional experimental design, therefore, Orthogonal array (L9) was carefully chosen for experimental design to There are three types of grinding media that are commonly used in ball mills: • steel and other metal balls; • metal cylindrical bodies called cylpebs; • ceramic balls with regular or high density. Steel and other metal balls are the most frequently used grinding media with sizes of the balls ranging from 10 to 150 mm in diameter [30].Grinding in Ball Mills: Modeling and Process Control
احصل على السعر
A Review of Alternative Procedures to the Bond Ball Mill
Determining the Bond index using the Fred Bond method [1,2] is considered the state-of-the-art methodology for mill calculations and a critical process parameter in raw materials selection and grinding process control.Although it is usually referred to as a standard test, no ISO (International Organization for Standardization) or Ceramic grinding, which in this paper is defined as a method of using ceramic materials as grinding media, is favored by many processing plants as an emerging high-efficiency and energy-saving grinding method. This paper investigates the effect of slurry mass concentration on the grinding characteristics of magnetite by taking the feed Effect of Slurry Concentration on the Ceramic Ball Grinding
احصل على السعر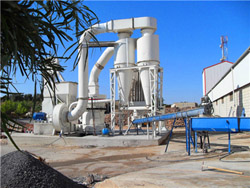
Design considerations for large diameter ball mills
Large mill (D>5.0 m (16.5 ft)) performance has been successfully predicted from small scale batch experiment for grinding kinetics and an RTD correlation for transport using population balance models.The effect of ball size must be properly taken into account in the scale-up. A design method that combined the kinetic scale-up findings and the The breakage and liberation of minerals are the key to fluidized mining for minerals. In the ball milling process, steel balls function as not only a grinding action implementer but also energy carrier to The Effect of Grinding Media on Mineral Breakage
احصل على السعر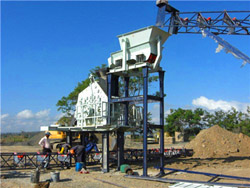
The significance of ball mill grinding in chocolate
Ball mills are essential in chocolate manufacturing, playing a role in grinding cocoa beans to the desired consistency. Different types of ball mills are used, each with unique features and benefits, The process of ball milling involves the grinding and mixing of metal particles within a ball mill, which is a type of equipment used for grinding, with the aim of producing a fine powder . This method has been widely employed in the manufacturing of metal powders from diverse sources, including metals, alloys, and intermetallic compounds.Producing Metal Powder from Machining Chips Using Ball Milling Process
احصل على السعر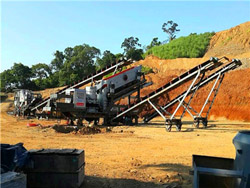
Nature of corrosive and abrasive wear in ball mill grinding
Abstract. Laboratory results of marked-ball wear tests are used to discuss the relative significance of corrosive and abrasive wear in wet grinding. The electrochemical mechanism was investigated by correlating the corrosive wear with the corrosion current obtained from polarization curves under abrasion. Slurry rheology governs the manner inThe aim of this work was to optimize the ball mill based refining process of chocolate, in terms of refining time and energy consumption. Experiments were planned following a central composite design (CCD), considering refining time (rt) and agitator shaft speed (as) as factors.The experimental variables measured were chosen from the main Optimization of processing parameters of a ball mill refiner
احصل على السعر
Kinetics of Dry-Batch Grinding in a Laboratory-Scale Ball Mill
The optimization of processing plants is one of the main concerns in the mining industry, since the comminution stage, a fundamental operation, accounts for up to 70% of total energy consumption. The aim of this study was to determine the effects that ball size and mill speed exert on the milling kinetics over a wide range of particle sizes. This Ball mill feed and product particle size distribution for survey 1, 2 and 3 Figure 8 to Figure 11 and Table 11 to Table 13 present the results for the size distributions and some key performance(PDF) Assessment of the Performance of Grinding Circuit for
احصل على السعر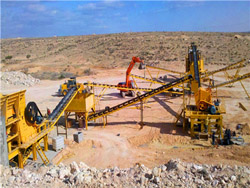
Minerals Free Full-Text Estimating Residence Time MDPI
Ball mills are widely used in mineral processing due to their flexibility and versatility in reducing the particle size at the level required in the concentration stages [].The size reduction can be carried out in dry or wet environments depending on the subsequent separation processes [].Grinding circuits must guarantee adequate particle size As ball filling in the SAG mill is quite low, additional grinding media would likely increase the processing capacity of the SAG mill; however, the capacity of the ball mill, with installed power for the required product size of 170 µm, has reached its limit.Minerals Free Full-Text Optimizing Performance of SABC
احصل على السعر- موج شکن رول تولید چین
- cone crusher s e e standard
- شركات مصر لتعدين الفحم
- خام الحديد القشور
- المحمول المصنعة كسارة الفك
- small mining tools in sa
- غسالةملابس لرضيع
- المطرقة مطحنة المحمول الطريق
- محطة طاحونة الكرة الرطبة tankaya
- list of cement crusher in andhra pradesh
- نهر حصاة المورد سعر كسارة متنقلة
- مورد شاشة deing شاشة deing لسال
- أفضل نوعية من الحجر الجيري تأثير محطم
- industrial feed equipment
- مدارس التعدين ومعالجة المعادن في أفريقيا