اتصل
هاتف
+0086-371-86162511
عنوان
تشنغتشو ، الصين
steel ball charge mining
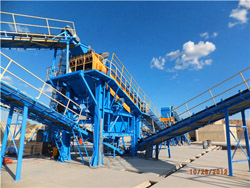
The Effect of Grinding Media on Mineral Breakage
The breakage and liberation of minerals are the key to fluidized mining for minerals. In the ball milling process, steel balls function as not only a grinding action implementer but also energy carrier to On industrial plants, advantage can be taken of parallel lines of mills, as reported by Banisi and Farzaneh (2004) for example, where they have made use of four identical parallel lines at the Sarcheshmeh copper mine to test three different ball Consumption of steel grinding media in mills A review
احصل على السعر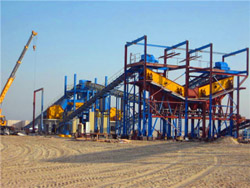
Experimental study of charge dynamics in a laboratory-scale ball
Abstract. To understand and describe the behavior of charge dynamics in mills, a series of dry and wet grinding tests were performed on a laboratory-scale ball mill. The comparisons between experimental results and grinding media trajectory simulations Chenje et al. compared five types of grinding media balls (eutectoid steel, low-alloy steel, medium-chromium cast iron, cast semi-steel and unalloyed white cast iron) and found that heat-treated medium chromium (HTMC) cast iron balls had superior Minerals Free Full-Text A Review of the Grinding Media in Ball
احصل على السعر
Effect on Fine Particles Output Characteristics of Ceramic Ball
It should be noted that steel ball grinding yields more output of 53 μm, 38 μm, 23 μm, and 10 μm than ceramic ball grinding in a short period of time. In general, steel ball grinding is more efficient than ceramic ball grinding in reducing the particle size of a To evaluate the performance of three ball types, namely, forged alloy steel balls (A), ductile cast iron (C), high chromium cast iron (D) and also a combined (80 and 60 mm) charge of forged alloy steel balls (B), four identical parallel mills were charged Effect of ball size on the performance of grinding and flotation
احصل على السعر
Comparison of grinding media—Cylpebs versus balls
Cylpebs of equal diameter and length have 14.5% greater surface area than balls of the same mass, and 9% higher bulk density than steel balls, or 12% higher than cast balls. As a result, for a given charge volume, about 25% more grinding media In this research, the effect of ball size distribution on the mill power draw, charge motion regime and breakage mechanism in a laboratory ball mill was studied using the discrete element methodTwo- and Three-Dimensional Simulation of Ball and Rock Charge
احصل على السعر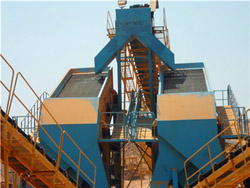
Study on Partial Replacement of Metal Grinding
Loveday [ 17] analyzed, on a laboratory scale, the use of small pebbles of 7 to 25 mm to fill the interstices of 40 mm steel balls, studying the grinding with a mixed load. The results were encouraging, Ball Size as Initial Charge. Commercial ball sizes 10 150 mm; Number, size and mass of each ball size depends on mill load and whether or not the media is being added as the initial charge. For the initial chargin of a mill, AMIT 135: Lesson 7 Ball Mills & Circuits Mining
احصل على السعر
Study on Partial Replacement of Metal Grinding
Certain studies have analyzed the partial replacement of steel balls by pebbles, resulting in a mixed load, as in the case of the present study [15,16,17,18]. Loveday analyzed, on a laboratory scale, The operation parameters were set as follows: 73% of the desired speed, 38% ball charge, a maximum diameter of 80 mm for the steel balls, and a solids concentration of 60% for the hydrocyclone, d 50c = Minerals Free Full-Text Study on the Selection
احصل على السعر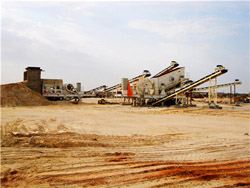
Semi-autogenous grinding (SAG) mill liner design and
ball that sits against the lifter and plate (Royston, 2001). At constant mill speed, ball trajectories should degrade (i.e., balls fall more towards the bulk of the charge than the toe) with time as the lifters wear down. Shell lifters with initially large face angles may start by directing ball impacts at the toeThis study investigated the effect of grinding media on the fine-grinding performance in the wet tumbling mill. Comparative experiments between cylpebs and ceramic balls were conducted in a laboratory wet ball mill under various conditions, such as different total masses, total surface areas, and total numbers. The results indicated that Minerals Free Full-Text A Comparison of the Fine-Grinding
احصل على السعر
Mining Magotteaux
A holistic approach to help with your mining challenges. Maximizing the recovery of valuable minerals at a saleable concentrate grade, at the lowest cost and with the lowest environmental impact requires optimizing all processes and sub-processes linked to the flow sheet. Our concept of optimization considers the entire value chain: ProcessIt was claimed by the manufacture (Doering International) that for a given charge volume, Cylpebs provide 25% more grinding media surface area for size reduction. The grinding performance of the Cylpebs should then be correspondingly higher compared with the steel balls (Doering website: doering-sinn.de ).Comparison of grinding media—Cylpebs versus balls
احصل على السعر
(PDF) Grinding Media in Ball Mills-A Review ResearchGate
2 Department of Mining Engineering, forged steel balls act as the anode whilst the sulfide mineral will be the cathode. Cayirli [81] foun d out that as the ball charge increases,2 天之前The reduced number of small balls, combined with a lower ball charge surface area, might explain the 6% lower grinding efficiency of a 76 mm martensitic ball charge compared to a 76 mm pearlitic ball charge. We analyzed the ball size distributions resulting from charging 76 mm pearlitic carbon steel balls versus charging 76 mm martensitic alloyGrinding Media 911 Metallurgist
احصل على السعر
Maximizing wear resistance of balls for grinding of coal
The equipment is shown in Fig. 1.It is a pilot-plant ball mill, with capacity to process 10. L of ore per batch.. The ball charge contains 132 kg of balls, from 25- to 60-mm diameter. Download : Download full-size image Fig. 1.. Pilot-plant ball mill: coal charge = 16 kg (10 L); total ball charge = 132 kg; speed = 31 rpm.In addition, the ball charge weight enhanced up to certain value, the wear rate decreased and thereafter increased. 3) It was found that influence of factors affecting the wear rate of steel balls was in the order of ball type > solid percentage > pH > solid percentage 2 > charge weight 2 > grinding time > rotation speed of mill > throughout. 4)Investigating the controllable factors influencing the weight
احصل على السعر
(PDF) Performance optimization of an industrial
Abstract. In this investigation, we optimize the grinding circuit of a typical chromite beneficiation plant in India. The run-of-mine ore is reduced to a particle size of less than 1 mm in theAbstract and Figures. An increase of over 10% in mill throughput was achieved by removing the ball scats from a single -stage SAG mill. These scats are non- spherical ball fragments resulting from(PDF) STARTLING EFFECT OF BALL SCATS
احصل على السعر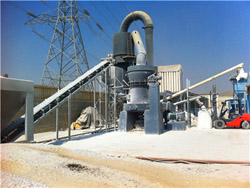
Modelling SAG milling power and specific energy
The ball charge is a function of the bulk fraction of the SAG mill volume (Jb) occupied by balls; the ore retained in the mill is the result of the volumetric filling which depends on the ore size distribution (specially the % +6″ and the % −6″ +1″), on the rotational speed (N/Nc) and on the solid concentration by weight fraction insideAn estimated consumption of steel grinding media of around 600,000 tons p.a. in the 1980s already gives an indication of the scale of the problem (Malghan, 1982). Likewise, in the cement industry, as mills are supplied for ever increasing capacities, the ball size distribution and wear exact a tremendous effect on the profitability of producingConsumption of steel grinding media in mills A review
احصل على السعر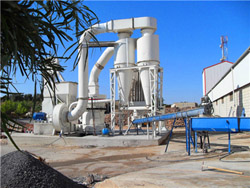
Minerals Free Full-Text Pre-Processing to Increase the
A total of 120 t of Cristalino ore was prepared and sent to CIMM, where it was crushed and screened prior to grinding tests. The processing equipment included a 1.83 m (8′) diameter by 0.61 m (2′) length AG/SAG mill equipped with a 20 kW motor, a cone crusher, a 0.91 m (3′) diameter by 1.22 m (4′) length ball mill equipped with a 15 kWThe media used in the charge generally describes a tubular mill. Thus, the medium could be steel or cast iron balls when the mill is designated as a ball mill, or it could be steel rods where the mill is known as a rod mill.When no grinding medium is charged it is known as an autogenous mill.Tubular Ball Mills ScienceDirect
احصل على السعر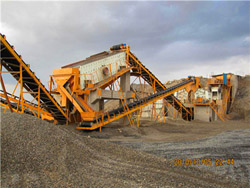
(PDF) Grinding in Ball Mills: Modeling and Process Control
A ball mill is a type of grinder widely utilized in the process of mechanochemical catalytic degradation. It consists of one or more rotating cylinders partially filled with grinding balls (madeTo prevent the conditions leading to rod charge tangling, the length to diameter ratio is maintained at 1.4 to 1.6. Quality Forged Steel Grinding Rod. Steel balls for mining. Ball mill has a wide range of applications. It can grind metal ore and non-mental ores, which is suitable for hard materials, such as quartz, gold ore, copper oreSteel Rod vs Steel Balls CAMASTEEL
احصل على السعر- كسارة تعريف كسارة
- المستخدمة كسارة متنقلة في الولايات المتحدة الأمريكية
- golden refinery equipment
- صور الدمار بالخالدية قرب حاجز المطاحن
- الحجر الجيري محطم قطع الغيار الصين
- مصغرة كسارة الصخور سعر المملكة المتحدة
- Machinery In Jute Mill Robin Frame Georgia
- وظائف في طحن جانسى وحدة
- كفاءة عالية في توفير الطاقة آلة مطحنة الكرة الاسمنتية
- أنبوب الماء أسعار المرجل الماء الساخن
- how much a stone crusher
- طاحونة زجاجية
- الكاولين التصفية في عملية التعدين
- سحق السكر أجزاء مطحنة
- minerals resoures in nigeria location and their uses