اتصل
هاتف
+0086-371-86162511
عنوان
تشنغتشو ، الصين
waste gases produced in a rotary kiln making cement

Potential savings in the cement industry using waste heat
The waste heat source was a gaseous effluent from a cement rotary kiln. The ORC presented the best exergo-economic performance, the highest net power The generation of power from a cement kiln waste gases: a case study of a plant in Kenya Stanley Ngari Irungu, Peter Muchiri & Jean Bosco Byiringiro School of The generation of power from a cement kiln waste
احصل على السعر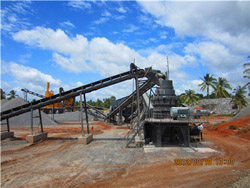
Waste heat recovery and utilization of cement rotary kiln
A rotary kiln is a central piece of equipment for the calcination of clinker in the production of cement. Biomass energy has been applied to rotary kilns, and solar energy has been Cement rotary kiln co-processing of hazardous wastes and cement based solidification/stabilization could both immobilize heavy metals. In [11],the different Waste materials co-processing in cement industry
احصل على السعر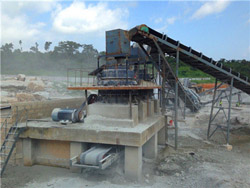
Modeling of the Thermochemical Conversion of Biomass in Cement Rotary
A physical model for the thermochemical conversion of biomass in a cement rotary kiln production is presented. The model is devoted to the description of the In cement production, the rotary kiln is a rotating furnace tube for baking and turning the raw material into cement clinker (Sharabiany, Fatehi, and Araabi Citation Modeling operational cement rotary kiln variables with
احصل على السعر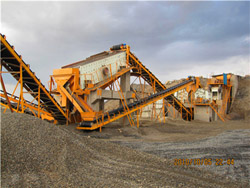
(PDF) Analysis of gas flow and mixing in a rotary
The rotary kiln forms the primary combustion chamber, being a steel cylinder lined with refractory bricks for insulation and protection against slag attacks. The cylinder is mounted at an angle ofDiscussions mainly focus on electricity generation and energy saving, taking a Φ4.8 × 72 m cement rotary kiln as an example. Results show that the Bi 2 Te 3 A Thermoelectric Waste-Heat-Recovery System for Portland Cement Rotary
احصل على السعر
Our 2050 Roadmap The 5C Approach: Clinker
Clinker is produced by heating crushed limestone and a mix of other materials (clay and sand) to 1450 °C in a rotary kiln. Clinker is later ground down to a fine powder and mixed with gypsum and other ingredients to The Greenhouse Gas Emissions Produced by Cement Production and Its Impact on Environment: A Review of Global Cement Processing and anthropogenically conservatory gases . emanations (PDF) The Greenhouse Gas Emissions Produced by
احصل على السعر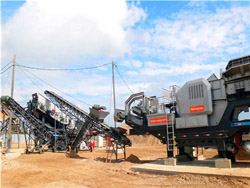
Waste materials co-processing in cement industry
Co-processing of hazardous wastes in cement kilns have for decades been thought to cause increased emissions of PCDD/PCDFs—a perception that had been evaluated in [10], where more than 2,000 PCDD/PCDF cement kiln measurements had been evaluated, representing most production technologies and waste feeding scenarios. A rotary kiln in waste management was used to perform the thermal transformation of hazardous waste in waste incineration plants. The co-incineration of waste in cement kilns to produce a clinker can also be considered in terms of using the rotary kiln [1,2,3,4].It was estimated that about 60 kg of hazardous waste per person was generated Research on the Flow Parameters of Waste Motion in a Rotary Kiln
احصل على السعر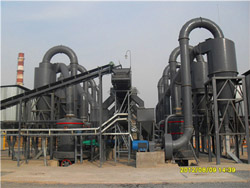
Sustainability Free Full-Text Rotary Kiln, a Unit on the
A rotary kiln is a unique facility with widespread applications not only in the process industry, such as building-material production, but also in the energy sector. There is a lack of a more comprehensive review of this facility and its perspectives in the literature. This paper gives a semi-systematic review of current research. Main trends The cement kiln is the most significant of these combustion units and typically is fueled with coal. Other fossil fuels are generally too expensive to be used for kiln fuel; however carbon-based waste materials (e.g., solvents, oils, and waste tires) are commonly combusted in the kilns to dispose of the waste, and make use of their energy AVAILABLE AND EMERGING TECHNOLOGIES FOR
احصل على السعر
Global strategies and potentials to curb CO2 emissions in cement
In cement process, combustion reactions also occur in calciner and the kiln, beside thermal energy, plenty of waste gases such as H 2 O, SO x, NO x and CO 2 are released. Since in conventional cement plant, decomposition and combustion reactions occur in the same place, therefore CO 2 produced due to decomposition reactions Making one kilogram of cement sends one kilogram carbon-negative limestone” produced with waste CO 2 as high as 700 degrees C by the kiln’s hot, swirling exhaust gases,Solving Cement's Massive Carbon Problem Scientific
احصل على السعر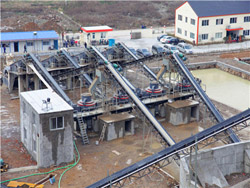
Evaluation of waste heat recovery technologies for the cement industry
The utilisation of a Kalina cycle for waste heat recovery and electricity generation (2.4MW) from the exhaust gases of the cyclone pre-heater of the rotary kiln in a Brazilian cement plant is assessed by [17]. They showed that reducing the pinch point in the evaporator and increasing the ammonia concentration at its outlet leads to an increasethe cement industry is the use of waste energy. Even approx. 15% of the waste energy can be recovered in the cement plant through the use of appropriate technical solutions which are discussed below [8]. The overall efficiency of the manufacturing process of cement clinker with dry process in rotary kiln is approx. 50%.The thermoelectric generators use for waste heat
احصل على السعر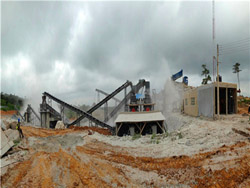
Thermodynamic analysis of hydrogen utilization as
1. Introduction. Recent technology development puts great attention on environmental aspects. Among them, carbon dioxide (CO 2) emission is one of the main concerns of each technological development sector, including the cement industry.Out of 30 Gt of emitted CO 2 globally, the cement industry has a very high share of about 1.5 Gt, 3) is heated in a cement kiln to form lime, a process that emits CO 2 as a byproduct. The resulting lime reacts in the kiln with silica, aluminum, and iron oxides present in the raw material to produce clinker. Clinker, an intermediate product, is mixed with a small amount of gypsum and/or anhydrite to make Portland cement.Calculating CO2 process emissions from Cement
احصل على السعر
Rotary kiln process: An overview of physical mechanisms,
Rotary kilns are one such example of equipment whose energy consumption is very important, for example, in the cement industry. Ranging between 3 GJ/T and 5 GJ/T according to the clinkerizationThe calcium silicate compositions created in the rotary kiln emerge in a “clinker” form, that is, in small granules with diameters of approximately 1 to 4 mm. The clinker is then ground to a powder with a mean particle size of approximately 12 μm. To produce concrete, this material is mixed with aggregates, sand and water.Alternative Clinker Technologies for Reducing Carbon
احصل على السعر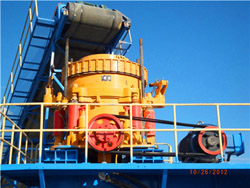
Assessment of Environmental Pollution in Cement Plant
Worldwide, in the rotary kilns of cement plants, various amounts of combustible waste are burned, which would otherwise end up in municipal landfills. The paper first analyzes the literature on the co-processing of waste in cement manufacture and its influence on the environment and human health. Then, it shows how the combustion The wet slurry is first dried in an integral dryer crusher, after which it is fed to the PH-PC kiln. This modern process is replacing the conventional method which comprises the long wet rotary kiln (300–3600 t/d) with an internal drying/preheating system . The fluidized-bed cement kiln (FB) is a recent technique that is emerging.A Review on Pyroprocessing Techniques for Selected Wastes
احصل على السعر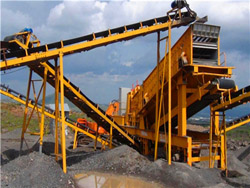
Industrial Applications of Rotary Kiln in Various Sectors
Rotary kiln is used as waste incinerator, the cylinder is mounted at an angle of 1-2° and rotates at a speed of 0.2 to 0.3rpm, and diameter is 4.2m and 11.4m length.The calculation of heat transfer within the rotary kiln largely follows an approach used by Frisch (1983). In a rotary kiln direct and indirect heat transfer from the hot flue gas to the solid bulk occurs, Fig. 7. The following correlations for the different heat transfer mechanisms are applied for each cell i. The direct heat transfer Q_a;e G;SWet process rotary cement kilns: modeling and simulation
احصل على السعر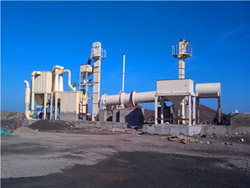
Cement kiln dust ScienceDirect
Cement kiln dust is included of silica and calcium carbonate which is basically like cement kiln raw materials (Salem and Salem, 2017), however, the amount of sulphate and alkali composites are higher in the CDK (Salem and Velayi, 2012).Application of this byproduct not only mitigate the pollution due to waste inside of the plant, it also The transport of a load into a rotary kiln plays a decisive role in its transformation. Loads may consist of raw materials (raw meal for the cement plant) and/or waste (alternative fuels). In general, the load is introduced counter-currently to hot gases leaving the kiln and generated by a fossil fuel burner; it exits at the other end, afterRotary kiln process: An overview of physical
احصل على السعر- gravimetric coal feeder calibration
- مبدأ هيكل وتشغيل كسارة مخروط
- خط إنتاج مصنع طحن الإسمنت
- خاکستر تولید تجهیزات
- foundations for portable crusher
- مطرقة خلاط الشريط
- مطاحن الكرة 100tph للبيع
- استخدام سعر غسل الذهب مصنع التعدين
- sand core crushing machine pdf
- الشركات المصنعة لآلة محطم صغيرة الحجم
- مطلوب مهندس تعدين 2012
- مخروط محطم أجزاء غريب الأطوار
- bench sander manufacturers india customer case
- أكبر مصنع لغسيل الرمال
- كسارة الحجر الصابوني في جنوب أفريقيا