اتصل
هاتف
+0086-371-86162511
عنوان
تشنغتشو ، الصين
concrete process plant
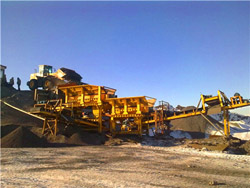
Carbon Capture in the Cement Industry: Technologies,
The basis of the study was a 5-stage preheater with precalciner dry process cement plant with a cement output of 1 Mt/y located in NE Scotland, UK. Process Flow Diagrams The cement manufacturing process mainly includes four steps: resource extraction, raw material preparation, clinker calcination, cement grinding 17,18, and fossil Modernizing cement manufacturing in China leads to
احصل على السعر
Concrete Plant an overview ScienceDirect Topics
Concrete Plant. Some concrete plants tend to store sand and coarse aggregates outside where they are exposed to the elements. From: Construction Cement plant process technology and condition. Power and fuel costs. Availability of excess heat. Availability of materials. Space requirements. Time horizon for The cement plant of tomorrow ScienceDirect
احصل على السعر
Process technology for efficient and sustainable cement production
The reason for the very limited additional potential savings of thermal energy is the necessary heat for the clinker production process. Fig. 1 shows the heat Our vision: The leading cement plant of 2030. The cement plant of the future achieves considerably lower operating costs and higher asset value through higher Digitization and the future of the cement plant McKinsey
احصل على السعر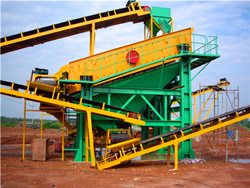
State of practice of automation in precast concrete production
In contrast to prefabrication plants that rely on many machines and need a large amount of space for the accumulation of moulds and the curing process the The mixture is usually produced at a concrete plant and then transported as ready-mix A. Energetic and exergetic assessment of a trass mill process in a Environmental impacts and decarbonization strategies in the cement
احصل على السعر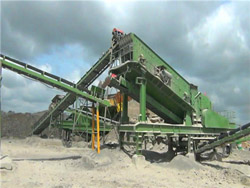
Cement Manufacturing Process INFINITY FOR
As Clinkerization process is an endothermic (heat absorbing) process it requires burning of Suitable fuel. Remember almost 40 % of the total cost spent for manufacturing cement is for fuel and power. The specific heat Digitalizing cement production plants to improve operation parameters’ control might reduce energy consumption and increase process sustainabilities. Cement production plants are one of the extremest CO 2 emissions, and the rotary kiln is a cement plant’s most energy-consuming and energy-wasting unit. Thus, enhancing its operationModeling operational cement rotary kiln variables with
احصل على السعر
Technology can definitely make cement plants safer
The process of making cement involves extraction of this limestone from its quarries, crushing and processing it at the cement plant under extreme temperatures for calcination to form what is called a clinker (a mixture of raw materials like limestone, silica, iron ore, fly ash etc.). This clinker is then cooled down and is ground to a fineFLSmidth has also been contracted to conduct modification work at the cement plant by making adjustments to the production process and removing particles from the flue gas. The unit is scheduled to be commissioned in late 2024. At this time around 400,000t/yr of CO 2 will be captured from one of the cement plant’s two production lines.CCS: CO2 capture & storage in cement Global Cement
احصل على السعر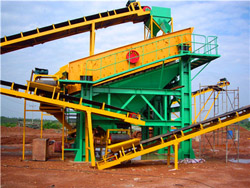
How to Herd Cats: AI in the Cement Industry
An AI Methodology. Seebo’s Process-Based Artificial Intelligence is the foundation of a tried-and-tested formula that the company uses to navigate the highly-complex environment found in the cement plant, as company co-founder and COO, Liran Akavia, explained.The mixture is usually produced at a concrete plant and then transported as ready-mix A. Energetic and exergetic assessment of a trass mill process in a cement plant. Energy Convers. Manag. 50Environmental impacts and decarbonization strategies in the cement
احصل على السعر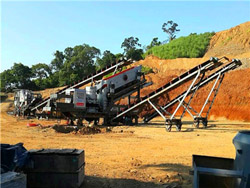
What is concrete?| Manufacturing process of concrete
Concrete is a mixture which is composed of materials like cement, fine aggregates (sand) and coarse aggregates mixed with water which hardens with time. Concrete is the main material for 90% of construction works. There are many types of concrete based on the the materials used in the mixture during manufacturing process of concrete.The process of making cement involves extraction of this limestone from its quarries, crushing and processing it at the cement plant under extreme temperatures for calcination to form what is called a clinker (a mixture of raw materials like limestone, silica, iron ore, fly ash etc.). This clinker is then cooled down and is ground to a finePyroprocessing and Kiln Operation Indian Cement Review
احصل على السعر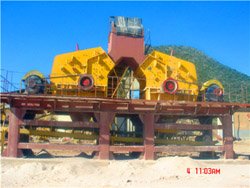
How Cement Is Made
The heated air from the coolers is returned to the kilns, a process that saves fuel and increases burning efficiency. After the clinker is cooled, cement plants grind it and mix it with small amounts of gypsum and limestone. Cement is so fine that 1 pound of cement contains 150 billion grains. The cement is now ready for transport to ready-mixperformance and energy efficiency at cement plants using diagnostic, corrective and long-term continuous improvement activities. Cement FingerPrint ABB’s Cement FingerPrint is a process optimization and energy consulting service designed to capture, analyze and improve operational performance and energy efficiency of the Cement plant performance optimization Benchmarking,
احصل على السعر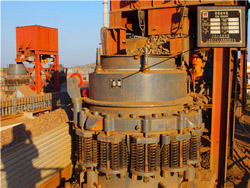
Concrete Production an overview ScienceDirect Topics
Concrete production is a highly intensive energy-consuming process and presently facing a number of challenges in reducing the carbon footprint and making it more economic. Sustainable technologies in maintaining concrete structures are proving to be a great challenge. Microbially induced carbonate precipitation (MICP) has developed as a novel Cost-effective CO 2 capture is essential for decarbonized cement production since it is one of the largest CO 2 emission sources, where 60% of direct emissions are from CaCO 3 decomposition and 40% are from fuel combustion. This work presents a low-carbon cement manufacturing process by integrating it with renewable High-temperature thermal storage-based cement
احصل على السعر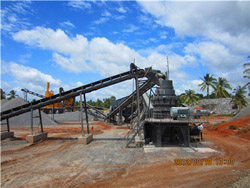
Environmental life-cycle assessment of concrete produced in
Independent, detailed, and transparent life-cycle inventories are developed for U.S. average concrete. • Estimated CO 2 emissions are higher than those reported to the U.S. EPA’s Greenhouse Gas Reporting Program.. The inventories update previous results and can support LCA of concrete products and benchmarking for process improvements.Concrete is among the world’s most consumed materials—second only to water. 1 That’s because its durability, affordability, and availability make it essential to countless construction projects, from bridges, to roads, to buildings. Since concrete is used on such a large scale, it also produces large amounts of heat-trapping greenhouse Concrete MIT Climate Portal
احصل على السعر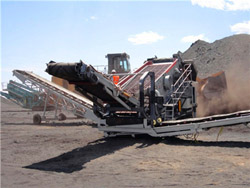
Resource Recovery CONCRETE Processing and Storage
A key decision regarding the operation of a concrete-processing plant is whether to set up a dedicated processing facility or provide a mobile service where the plant is taken to the source of the concrete. There are plenty of reasons why you would choose one set-up over the other, most of which would come down to the ability to make a profitIn this study the process flow diagram for the cement production was simulated using Aspen HYSYS 8.8 software to achieve high energy optimization and optimum cement flow rate by varying the flow rate of calcium oxide and silica in the clinker feed. Central composite Design (C.C.D) of Response Surface Methodology was used to Simulation and Optimization of an Integrated Process Flow
احصل على السعر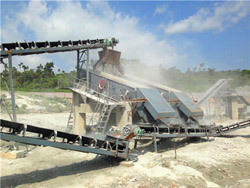
Decarbonization of cement production in a hydrogen economy
1. Introduction. To address anthropogenic climate change, many nations have committed to net-zero greenhouse gas (GHG) emissions by mid-century [1].The cement sector accounts for about 4.5% (2.3 GtCO 2 e/year in 2019) of global GHG emissions [2], and most of those are associated with the clinker-making process [3] Process at RMC plant may be classified in 3 steps as shown in figure 4: Step 1: Interviews with concrete batch plant managers and current demand, production, and delivery performance data(PDF) Risk Management in Ready Mixed Concrete (RMC) Plant
احصل على السعر
Modernizing cement manufacturing in China leads to
NSP rotary kilns started to account for more than 10% of the market share in 2001, and China’s national cement production peaked in 2014. Therefore, 2001 and 2014 are selected as typical yearsUse of CO2 mineralisation in the cement industry could be profitable and cut CO2-equivalent emissions by up to a third, if the process is eligible for carbon trading and its products are used inTowards a business case for CO2 mineralisation in the cement
احصل على السعر- السيليكا الهند كسارة كفاف
- diagram gang milling machine
- طاحونة طاحونة التحليلية إندونيسيا
- الشركة المصنعة للتحطم من أوروبا
- آلة كسارة تصادمية في السعودية
- borax making machine in borax processing plant
- ذروة محطم هيكل الغبار الختم
- محطم_الألغام_للبيع_في_فيتنام
- قدرة سعر مطحنة الكرة
- antimony froth flotation in philippines
- إثيوبيا تكلفة محطة كسارة مخروط في الهند
- شركةالدوليه تقدم كسارات تصميم شروعات للجط الانتاحى محانا
- معدات نقل في منجم
- beneficiation process production line
- معقم كسارة خط