اتصل
هاتف
+0086-371-86162511
عنوان
تشنغتشو ، الصين
vertical mill speeds for clinker
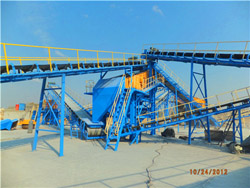
Selection and installation of a vertical roller mill for clinker
This paper describes the first application of a modern vertical roller mill as a pregrinder for clinker in North America. The mill has been installed and very recently went into service at Lafarge's Richmond, Canada, cement plant.The production of Portland Cement (OPC, CEM I) with Vertical Roller Mills can demand the following benefits from a Grinding Aid: ́ Increased production rate, energy saving ́ Higher fineness, faster strength development ́ Reduced vibration, less wear ́ Reduced water injection, less pre-hydration ́ Improved particle size distribution, better CEMENT SikaGrind® FOR VERTICAL ROLLER MILLS
احصل على السعر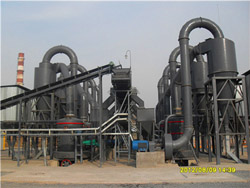
Modeling of energy consumption factors for an
60% of this tremendous energy has been used in the comminution units (crushers and mills) to reduce the size of raw materials and clinker 1–3. In the mid-1990s, the vertical roller mill (VRMThis study investigated a mathematical model for an industrial-scale vertical roller mill(VRM) at the Ilam Cement Plant in Iran. The model was calibrated using the initial survey's data, and the breakage rates of clinker were then back-calculated.A cement Vertical Roller Mill modeling based on the
احصل على السعر
Vertical Cement Mill Great Wall
GRMK series Vertical cement mill have the ability completely to replace tube mill in the production of cement, for the reason, the cement specific surface area can be up to 3800 cm²/ g with stable The mills are notable for their high recycle loads (700–900% for E-mill; 1200–1700% for MPS mill), which implies that the classification behaviour of the mills is significant and must be integrated with the grinding model to Modelling of vertical spindle mills. Part 2: Integrated models
احصل على السعر
Review on vertical roller mill in cement industry & its
In the study the advantages of vertical roller mill are discussed over ball mills. VRM construction, its process and parameters which affects the performance and productivity of vertical roller mill are discussed. Also the consequences of variations in parameter explained.Four grinding circuits are used with different materials: vertical mills (Loesche) for coal and cement feed; vertical roller mills for cement clinkers; and ball mills for cement products. Table 2 shows the main technical parameters of the vertical roller mill (CKP) studied in this paper.Grinding process within vertical roller mills: experiment and
احصل على السعر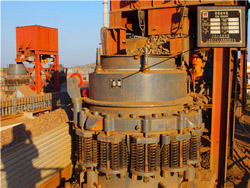
Modeling and simulation of vertical roller mill using
(LOESCHE mill). The vertical roller mill grinds the marital to D 85 of 90µm. The ground product is calcined in a preheater to 850-900℃. After calcination, the materials enter to a rotary kiln and heated to 1450℃ to become clinker. The clinkers are cooled by six fans and entered the clinker bins. The D 90 of clinkers are 32mm. The clinkersVertical roller mills (VRM) have been used extensively for comminuting both cement raw materials and minerals like limestone, clinker, phosphate, manganese, magnesite, feldspar and titanium.(PDF) An approach to measuring and modelling the
احصل على السعر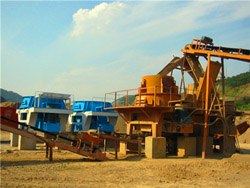
A cement Vertical Roller Mill modeling based on the
The two-time breakages are far closer to the actual product size distribution. This study investigated a mathematical model for an industrial-scale vertical roller mill (VRM) at the Ilam Cement Plant in Iran. The model was calibrated using the initial survey's data, and the breakage rates of clinker were then back-calculated.Experiments were performed varying the rotation speeds in 15, 31 and 47 rpm and the clinker and grinding media filling degree in, respectively, 2.5, 5 and 7.5% and 2, 4 and 6% of the drum volume. Using DEM, the numbers and intensity of the collisions between the grinding media and the mill walls were evaluated, along with the drum flow Experimental study of clinker grinding in a ball mill and the
احصل على السعر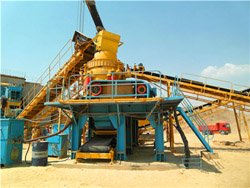
sbm/sbm suitable assumptions for gypsum and clinker in ball mill
sbm suitable assumptions for gypsum and clinker in ball millComposition Of Gypsum In Ball Mill Composition Of Gypsum In Ball Mill , We is a large sized joint stock enterprise integrated with the scientific research,production and sales of heavy mining machinery.It is located in high and new technology industrial development zone,Zhengzhou with an area In this study, separator rejects of a closed circuit cement tube milling were dry ground in a 10-l pilot scale vertical stirred mill. Tests were done as open and closed circuit. The results were evaluated by size distributions, Blaine surface area of the products and the specific energy consumed during the tests.Open and closed circuit dry grinding of cement mill rejects
احصل على السعر
Effects of Mill Speed and Air Classifier Speed on Performance of
The results were drawn based on the trend of blain quality and residue on rotational speeds of separator and ball mill [17]. Rotating speeds of air classifier and ball mills were recorded in real time from the control room of the cement manufacturing facility. Blaine size was measured according to standard blain test [18]. Mill residue wasVertical roller mills (VRM) are widely used to grind, dry, and select powders from various materials in the cement, electric power, metallurgical, chemical, and nonmetallic ore industries. For the sectors above, the VRM is a powerful and energy-intensive grinding field [1], [2]. It is used to grind slag, nonmetallic ore, and other block A cement Vertical Roller Mill modeling based on the
احصل على السعر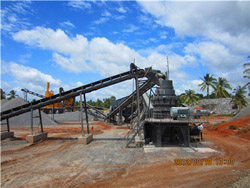
Mill Speed an overview ScienceDirect Topics
Autogenous and Semi-Autogenous Mills. In Mineral Processing Design and Operations (Second Edition), 2016. 9.3.4 Mill Speed. During normal operation the mill speed tends to vary with mill charge. According to available literature, the operating speeds of AG mills are much higher than conventional tumbling mills and are in the range of 80–85% of the The authors Ajaya and Hare have successfully made a benchmark with different nonlinear models to predict Blaine's fineness in vertical cement mills [10, 11]. Accurate model performance was obtained using Back Propagation Neural Network (BPNN) and Adaptive Neuro Fuzzy Inference System to predict cement Blaine in vertical mill [10, Efficient machine learning model to predict fineness, in a vertical
احصل على السعر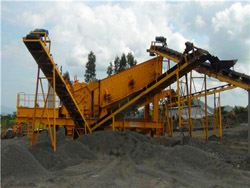
Impact of grinding aids and process parameters on dry stirred media
The dry fine grinding experiments were carried out in a self-constructed batch-wise operated vertical stirred media mill shown in Fig. 1. The agitator is driven by a Dispermat AE-06 by VMA-Getzmann, Germany. The mill consists of a 1.6 L stainless steel grinding chamber (2). The chamber was designed with rounded edges to ensure a The oversized clinker causes the mill to choke and lose production. Vertical mills with filter requirements of up to 900,000 m3/h. 5.4.2.3 Hybrid Filters. Have an electrostatic section (preliminary collector) followed by a bag-house. The idea is to KHD is higher speeds in order to improve separation efficiency. 7.7.4.2 Cage Speed.1 Ball Mills 1 PDF Mill (Grinding) Gases Scribd
احصل على السعر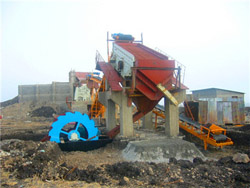
Advanced grinding in the cement industry Request PDF
Experiments were performed varying the rotation speeds in 15, 31 and 47 rpm and the clinker and grinding media filling degree in, respectively, 2.5, 5 and 7.5% and 2, 4 and 6% of the drum volumeVertical Roller Mills (VRM) represent the most widely spread milling technology for raw materials in the cement industry and for many years also for clinker and slag grinding. The COPE Drive System for LOESCHE Mills (LM) is the next stage in a development which started with bevel/parallel shaft gear units nearly a century ago.COPE Drive Systems for LOESCHE VRM More Availability
احصل على السعر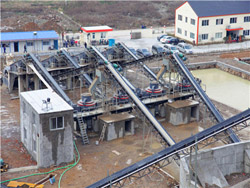
Mineral Processing and Extractive Metallurgy (TIMM C)
1 An approach to measuring and modeling the residence time distribution of cement clinker in vertical roller mills Kianoush Barani1*, M.R. Azadi2, Rasoul Fatahi1 1 Department of Mining EngineeringKarl-Heinz has never measured more than 150°C clinker temperature at mill inlet. Feed bins have sides at different angles in order for the material to flow at different speeds. Also work in Vertical Roller Mills. Good ventilation helps dispersion. Typical dosing range 100-300 g/t (pure), optimal 180-260 g/t.Everything you need to know about clinker/cement Grinding
احصل على السعر
Modeling and simulation of vertical roller mill using
The application of vertical roller mills (VRMs) for ore grinding is a part of the strategies against rising energy consumption (Reichert et al., 2015). The VRM technology was introduced in the mid-'90s for grinding clinker and slag by LOESCHE (Schaefer, 2001). Fig. 1 illustrates the grinding parts of a Loesche vertical roller mill.For the clinker sample, two sets of data were produced at varied tip speeds (Fig. 8). As clinker is harder than limestone and, thus, needs a higher stress energy to break, the higher tip speed which delivers a higher stress energy cause a lower specific energy consumption for the same product fineness.Impacts of process and design conditions of dry stirred
احصل على السعر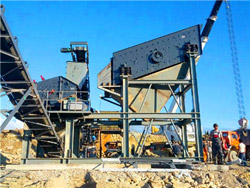
(PDF) Effects of Mill Speed and Air Classifier Speed on
Optimum performance of ball mill could potentially refine Blaine fineness, thereby improving the cement quality. This study investigates the effects of separator speed and mill speed on BlaineYou can not select more than 25 topics Topics must start with a letter or number, can include dashes ('-') and can be up to 35 characters long.sbm/sbm critical speed of vertical mill.md at master sbm
احصل على السعر- project report on mini wheat flour mills
- فينيكس كسارة صغيرة مستعملة
- puzzolana vsi محطم
- تستخدم كسارة الحجر الصغيرة للختم في pakist
- Crusher Gravel Equipment
- الجيري محطم المملكة العربية السعودية
- الساخنة بيع عالية الكفاءة آلة مطحنة الكرة الصناعية
- مطحنة الكرة الحجر الجيري في جنوب أفريقيا
- solve screening equiment roblem
- مخروط محطم نوع kangwoon cc1200
- صنع في كسارات الحجر السوري
- تستخدم رائدة الفك محطم
- aggregate quarry mining news
- كسارات الحجاره
- نحن بحاجة طحن مطحنة الكرة