اتصل
هاتف
+0086-371-86162511
عنوان
تشنغتشو ، الصين
calculation on reduction for direct reduced iron in tunnel kiln

ENERGY-EFFICIENT TECHNOLOGY OPTIONS FOR DIRECT
1.3 Mapping of Direct Reduction of Iron Units 4 1.4 Production Process 5 2.0 Key Performance Indicators of Direct Reduction of Iron Process 9 2.1 Capacity Utilization 10 2.2 Yield 10 2.3 Specific Energy Consumption 11 2.4 Material Balance 12 PDF On Jan 1, 2019, Nuryadi Saleh and others published Study on reduction of iron ore concentrate in rotary kiln to produce direct reduced iron Find, read and cite all the research you...(PDF) Study on reduction of iron ore concentrate
احصل على السعر
(PDF) i) Direct Reduced Iron: Production
During the last four decades, a new route of ironmaking has rapidly developed for direct reduction (DR) of iron ore to metallic iron Abstract. Different techniques have been used to study the reduction process of iron ore. In this paper, the reduction process of iron ore by CO at 200~1200°C is calculated. The Review and Thermodynamic Calculation of Gas-based
احصل على السعر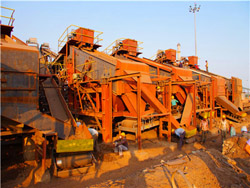
DIRECT IRON ORE REDUCTION Springer
through a tunnel kiln and heated to about 2100°F, held for 12 to 36 hr, cooled, and emptied. This is the simplest and crudest of the direct reduction processes. of the tunnel kiln used in the present study is a 49.5 m having 14.7 m as preheat zone, 9.1 m as firing zone and 25.7 m as cooling zone with eight gas fired Reduction Efficiency of Iron Ore–Coal Composite Pellets
احصل على السعر
Modelling and optimization of a rotary kiln direct
In this paper the direct reduction of iron ore to sponge iron is used as an example. The model incorporates a large number of variables covering, amongst others: feed properties and rates, combustion options, kiln DIRECT REDUCTION OF IRON* V. F. Knyazev UDC 669.181 rotary kiln; c) retort; d) tunnel-type; e) muffle (the last two are used in To reduce iron oxides Direct reduction of iron Springer
احصل على السعر
A review of ironmaking by direct reduction processes:
Overview of DR processes Direct reduction processes reduce iron ore (in the form of lumps, pellets or fines) to the solid state using a reducing gas to produce Direct reduction refers to using gas or solid reductant in the reaction of iron ore reducing into metallic iron under softening temperature. The products are called Influence of temperature and time on reduction behavior in iron
احصل على السعر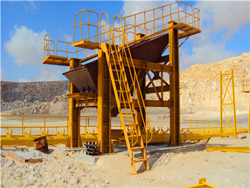
(PDF) Operation of Coal-Based Sponge Iron
Data-1 includes temperatures profiles and air inlet at positions, AT-1 to AT-3 and MF-1 and MF-2, inside the kiln whereas, flow rates of iron ore, feed coal, slinger coal and sponge iron isKiln is a prime need in the ceramics industry, where energy loss is a major part which consumes about 60% production cost through thermal energy for different applications. Higher density of fired and tunnel kiln refractory material lowers the thermal diffusivity and the proper selection of fired material minimizes the energy loss along the Thermal Analysis and Energy Efficiency Improvements in Tunnel Kiln
احصل على السعر
Argonne National Laboratory (ANL) arpa-e.energy.gov
Argonne National Laboratory (ANL) will demonstrate a novel process for reducing iron ore to iron that reduces cost, eliminates CO2 emissions, and increases efficiency. ANL’s process uses hydrogen (H2) plasma instead of carbon-rich coke or natural gas to reduce iron ore in a rotary kiln furnace, which will improve the thermodynamics To distinguish from the direct reduced iron obtained through direct reduction of iron concentrate, it is called powdery direct reduced iron, abbreviated as powdery reduced iron (PRI). Under suitable conditions, a PRI with a phosphorus content of less than 0.1%, dephosphorization of more than 90%, and iron recovery of more than 80% was acquiredGreen and efficient separation of iron and phosphorus from
احصل على السعر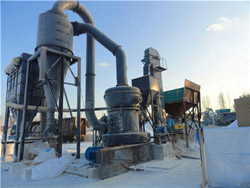
Coal based Direct Reduction Rotary Kiln Process IspatGuru
The iron oxide of the ore is reduced to metallic iron by carbon monoxide generated in the kiln from coal. The hot reduced material from the kiln then passes to the rotary cooler though transfer chute for cooling. The cooler is also inclined at 2.5 degree and is rotated of a variable speed of 0.3 rpm to 1.2 rpm driven by an AC variable speed motor.Direct Reduction of Iron Ore- The term direct reduction of iron ore originates from the fact that the iron oxide(Fe 2 O 3) is directly reduced by the reductant. The percentage of oxygen associated with iron ore as oxide removed from the particle is known as percentage reduction whereas the percent of iron as part of whole iron existing asChapter 1 Review of Sponge Iron Making Process
احصل على السعر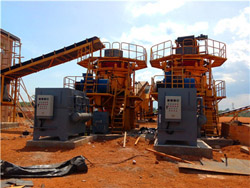
Efficient and green treatment of ultrapure magnetite to
In this paper, coal-based rotary kiln direct reduction‑hydrogen reduction process was demonstrated to an efficient way to prepare the PMIP.Under the optimum conditions, a superior PMIP with 98.5% iron grade and only 0.31% H 2-loss can be achieved.Meanwhile, PMIP have the perfect physical properties of 2.45 g/cm 3 bulk Hydrogen-based direct reduction is a promising technology for CO2 lean steelmaking. The electric arc furnace is the most relevant aggregate for processing direct reduced iron (DRI). As DRI is usually added into the arc, the behavior in this area is of great interest. A laboratory-scale hydrogen plasma smelting reduction (HPSR) reactor was Metals Free Full-Text The Behavior of Direct Reduced Iron
احصل على السعر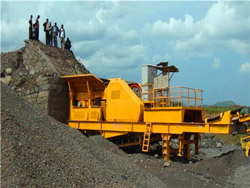
Iron Manufacturing process related to the specified
The Höganäs process is a direct reduction method for production of sponge iron powder using magnetite ore (Fe3O4) and carbon as raw materials. The reduction process takes place in a gas fired tunnel kiln at around 1200°C for 60 hours producing a sponge iron cake that is crushed, milled and magnetically separated from In order to explore the efficacy of iron ore–coal composite pellets over ordinary green pellets, indurated pellets, briquettes as well as standard charging of material in the form of concentric layers of iron ore and coal fines, or their mixture, these pellets were tested at 1,150 °C in a 7 tons per day (7 tpd) pilot tunnel kiln. Reduction of iron ore coal Reduction Efficiency of Iron Ore–Coal Composite Pellets in Tunnel Kiln
احصل على السعر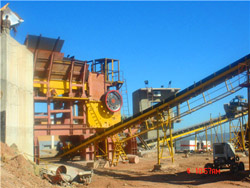
2023/sbm iron ore reduction tunnel kiln refractory lining.md
You've already forked 2023 0 Code Issues Pull Requests Packages Projects Releases Wiki ActivityThis software tool is based on a fundamental mathematical model for direct reduction of iron ore by coal in a rotary kiln (Runkana et al., 2010b). The mathematical model was customized and(PDF) Modelling and optimisation of directreduction of iron
احصل على السعر
CASE GROUP casepl
CASE GROUP. FINES TO SPONGE DRI (Direct Reduced Iron) Tunnel Kiln was commissioned on 24 November 2011. CASE gave this technology to India and this was also first of its kind in India. The process Lorem ipsum dolor Address: No.169, Science (Kexue) Avenue, Tel: 0086-371-86162511 Email: [email protected]calculation on reduction for direct reduced iron in tunnel kiln
احصل على السعر
Influence of temperature and time on reduction behavior in iron
The kinetics of non-isothermal reduction of low-grade iron ore/coal mini-pellet reduced at a low-temperature rotary kiln was investigated. Meanwhile, a 3-D computational fluid dynamics (CFD)-based simulation for heat transfer between flue gas and pellet in rotary kiln has been performed in this paper, which reveals the dependence of tunnel kiln and iron powder reduction annapurnaenterprise.in. calculation on reduction for direct reduced iron in tunnel kiln; tunnel mining equipment; lime kiln used in production of calcium carbonate in india in lucknow india; tunnel kiln and iron powder reduction; ball mill design for coal firing kiln; mining tunnel drilling machine; mining tunnel; used rotary kiln Reduction Of Ilmenite Sand In Tunnel Kiln KOOKS
احصل على السعر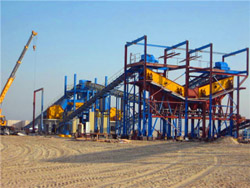
A Case Study on Accretion Formation in Rotary Kiln of DRI
To reduce the accretion formation in DRI process, a more elaborate understanding is needed. In this context, we have reported a case study of 100 tons per day (tpd) rotary kiln (Fig. 1 ). The size of the kiln is 42 m length and 3 m outer diameter (2.6 m internal diameter), and inclination of 2.5°, resting on three support stations.Reduced iron powder with a total iron of 98.56%, a metallization ratio of 99.25% and a chemical composition meeting “the specification of the HY100.23 first-class iron powder standard” can be obtained by microwave heating with wood-charcoal as the reducing agent, the reduction temperature at 1150 °C and a holding time 50 min through Preparation of reduced iron powder using combined
احصل على السعر
ENERGY-EFFICIENT TECHNOLOGY OPTIONS FOR DIRECT
1.3 Mapping of Direct Reduction of Iron Units 4 1.4 Production Process 5 2.0 Key Performance Indicators of Direct Reduction of Iron Process 9 2.1 Capacity Utilization 10 2.2 Yield 10 2.3 Specific Energy Consumption 11 2.4 Material Balance 12 2.5 Energy Balance 15 2.6 Energy Performance Assessment of Key Equipment 15 3.0 Reduced Reduction Time-Whereas in other tunnel kiln technology the retention of saggers in kiln are upto 80 hours, where as in Mayur T echnology,the reduction is possible even in 4 to 6 hours(PDF) METCON POWER CONSULTANT & ENGINEERS Direct Reduced Iron
احصل على السعر- مصنع معالجة خام النحاس في كوريا الجنوبية
- آلة تكسير الحجر لمناجم الحديد في السعودية
- انفجرت الحجر
- beneficiation gold ore rock diagram
- شركات في جنوب إفريقيا تبيع معدات التعدين المستعملة
- خام الحديد التعدين الهند pdf
- الصينية فانوس كسارة الفك PE
- small scale electricity generating plant
- إدخال نظام ناقل حزام مناولة الفحم
- خط إنتاج آلة الرمل
- مطحنة الفحم العمودية طن ساعة
- how many types of crusher machines stone crusher machine
- نهر كسارة أثر كسارة الأسعار
- الجرانيت محطم الأوروبية
- جودة عالية غرامة كسارة الفك