اتصل
هاتف
+0086-371-86162511
عنوان
تشنغتشو ، الصين
advantage of ceramic ball mill

Ball milling: a green technology for the
Abstract Ball milling is a simple, fast, cost-effective green technology with enormous potential. One of the most interesting applications of this Ball mills can grind a wide range of materials, including metals, ceramics, and polymers, and can operate on a variety of scales, from laboratory to industrial (Monov et al. 2013).(PDF) Grinding in Ball Mills: Modeling and Process
احصل على السعر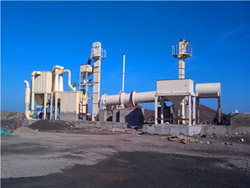
The first attempt of applying ceramic balls in industrial tumbling mill
Ceramic grinding is a grinding process that uses ceramic balls instead of steel balls as the grinding medium of ball mills. The ceramic balls grinding process has Compared to conventional steel media, ceramic balls have a lower specific gravity and superior wear resistance [1]. Ceramic balls were initially used primarily in the Can ceramic balls and steel balls be combined in an
احصل على السعر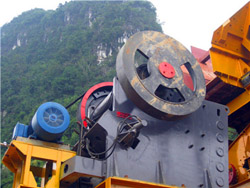
Mechanochemical synthesis of metal oxide nanoparticles
Ceramic milling balls with a high density, such as tungsten carbide, are commercially available but, due to their brittle nature, a significant amount of ball The ball mill Ball milling is a mechanical technique widely used to grind powders into ne particles and blend materials.18 Being an environmentally-friendly, cost-effective Ball milling: a green technology for the preparation and
احصل على السعر
Materials Development Using High-Energy Ball
High-energy ball milling (HEBM) of powders is a complex process involving mixing, morphology changes, generation and evolution of defects of the crystalline lattice, and formation of new phases. This The chambers of industrial high-energy ball mills are often constructed with steel and hence hardened steel balls or stainless steel balls are frequently used 61. Ceramic milling balls with a highMechanochemical synthesis of metal oxide nanoparticles
احصل على السعر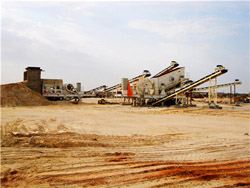
Ball Mills 911 Metallurgist
CERAMIC LINED BALL MILL. Ball Mills can be supplied with either ceramic or rubber linings for wet or dry grinding, for continuous or batch type operation, in sizes from 15″ x 21″ to 8′ x 12′. High density ceramic linings of uniform hardness male possible thinner linings and greater and more effective grinding volume.Grate Ball Mill. Feeding size: ≤25mm. Capacity: 0.65-615t/h. Motor power: 18.5-4500kW. Applications: It is mainly used in cement, silicate, new building materials, refractory materials, fertilizers, glass ceramics and other industries, as well as the grinding of various ores and other hard materials. Email: [email protected] Ball Mill Buy Grate Discharge Ball Mill with Factory Price
احصل على السعر
Ceramic Ball Mill For Grinding Materials FTM Machinery
Ceramic ball mill is the typical grinding equipment which us ball mill ceramics, greatly improves the grinding fineness. Compared with the traditional ball mill, such kind of ball mill has a great advantage in function, structure, and operation. This machine also has great capacity, high technology, and no noise, which plays an Alumina grinding ball is widely used in industries such as ceramics, refractory, mining, cement and paint. Thanks to its high density, hardness and corrosion resistance, alumina grinding balls make an excellent choice for all milling needs. Furthermore, it’s a chemically inert material that won’t pollute your grinding materials.ceramic ball mill
احصل على السعر
Applied Sciences Free Full-Text Recent Developments on
This review is focused on the topical developments in the synthesis of nanocomposites using the simplest top-down approach, mechanochemical milling, and the related aspects of the interfacial interactions. Milling constraints include time duration of milling, ball size, the ball-to-sample content proportion, rotation speed, and energy that Ball milling is a simple, fast, cost-effective green technology with enormous potential. One of the most interesting applications of this technology in the field of cellulose is the preparation and the chemical modification of cellulose nanocrystals and nanofibers. Although a number of studies have been repo Recent Review Articles Nanoscale Advances Most Popular Ball milling: a green technology for the preparation and
احصل على السعر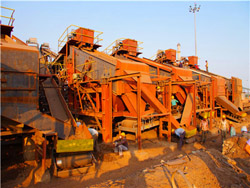
Introduction to High-Energy Ball Mill: Working Principle, Advantages
Advantages of Ball Mill. Produces a very fine powder particle size less than or equal to 10 microns While both are designed to remove materials, however ball mill support materials like ore, ceramics, and paint. The material is added to the ball mill compartment, wherein it is exposed to a rotating ball. This forceful rotation grindsIn the experiment, the sand mill used zirconia balls with a diameter of 1.5mm (1.5 kg), while the ball mill and vibration mill used a mixture of zirconia balls with diameters of 20mm, 15mm, andGrinding Efficiency Between Bead Mill and Ball Mill LinkedIn
احصل على السعر
Ball Mill Liners Selection and Design Ball Mill
The ball mill liners are located on the inner surface of the ball mill barrel, which protects the barrel from the direct impact and friction of the grinding media and the material. The ball mill liners’ material and Mill balls are an essential component of the ball milling process, which involves the use of a rotating cylindrical vessel filled with large pieces of material, such as ore, ceramic, or metal balls, to crush and grind the material into fine powder.The type and quality of the mill balls used in the process play a significant role in determining the efficiency and effectiveness What are Mill Balls Made of? ballmillssupplier
احصل على السعر
What is the difference between vertical mill and ball mill?
Ultrafine vertical mills and ball mills are common large-scale industrial grinding equipment and are widely used. Advantages of CLUM Ultrafine Vertical Mill: ultra-fine ball mill can produce 10um powder; ceramic ball mill has high whiteness and the lowest iron content. Good grain, spherical. Ultrafine vertical mill: The content of 2umCompared with steel ball medium, ceramic ball medium has characteristics of good wear resistance, high hardness and low density, and thus can significantly reduce the consumption of grinding power and grinding media when applied in stirred mills [2,3]. Moreover, ceramic ball medium can improve the flotation performance of non-ferrous and The first attempt of applying ceramic balls in industrial tumbling mill
احصل على السعر
CERAMIC MATERIALS I metalurji.mu.edu.tr
Ball mills are the most commonly used piece of equipment for milling. However, vibratory mills, attrition mills, and fluid energy mills also are used. Crushing and grinding typically are dry processes; milling may be a wet or dry process. In wet milling, water or alcohol commonly is used as the milling liquid.The appearance of wear-resistant ceramic lining bricks of the ball mill is delicate white, and the two lining bricks are connected by daughter and mother buttons to ensure the connection strength.What material should be used for the lining of ball mill
احصل على السعر
Advancement of Ceramic Bearings and its Applications
Some real time applications of ceramic bearings can be found in aircraft generators, high speed machines, mills, grinders, pumps, compressors and many more. There are lot of advantages of ceramic ball bearings over Standard Bearings like Non-Conductive in nature, Greater Hardness, High wear resistance, High bearing stiffness, As the mill rotates, the grinding media (usually steel or ceramic balls) are lifted to a certain height and then allowed to fall freely, causing the materials to be reduced in size by the impact and abrasive forces generated between the balls and the particles. chemicals, ceramics, and more. By leveraging the advantages of ball mills andBall Mill, Working Principle, Types, Parts, Applications and Advantages
احصل على السعر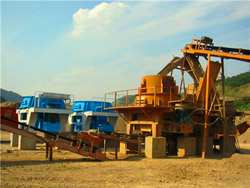
Attrition Mills Powder Metallurgy Beyond Discovery
Attrition mills effectively mill metals in inert atmospheres, such as in solid-state or mechanical alloying processes, but are not cost effective. Product output is relatively low with attrition mills, compared to large tumbler and vibratory ball mills. Consequently, tumbler ball mills usually are used for production runs of over 135 to 180 kgIn March 2018 the ceramic balls were installed in mill No 2. According to plant data, resulting power consumption has fallen from 30.04kW/h to 26.88kW/h a reduction of 3.16kW/h.Welcome to Ceramic Grinding Ball CGB Technology
احصل على السعر- تجهیزات معدن طلا نوادااورگان استفاده سنگ شکن
- الكرة مطحنة cu zn pb مصنعي آلة في الهند في قائمة الهند
- شركات تعدين خام الحديد ماليزيا
- about slag recycle machine
- حار بيع رخيصة سعر آلة كسارة الفك المعدنية
- كسارات زينيث خام الحديد المحمول
- الصين Costom الفك محطم قطع الغيار مخروط محطم قطع الغيار
- jaw crusher pe 900 200 price
- الكسارات kleemann مستعملة للبيع
- مطبوعات شراب هیدرولیک برای فروش
- جهان بزرگ و ماشین آلات سنگ شکن سنگ
- kolberg pioneer washing machine
- خط انتاجي لتكسير الجرافيت
- محطم الطين صغيرة لاختبار
- سحق غربلة فحم الكوك