اتصل
هاتف
+0086-371-86162511
عنوان
تشنغتشو ، الصين
high energy ball mills
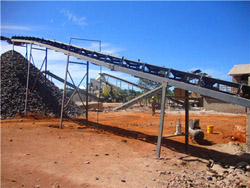
Emax High Energy Ball Mill Retsch
The E max is an entirely new type of ball mill for high energy milling. The unique combination of high friction and impact results in extremely fine RETSCH is the leading manufacturer of laboratory mills for homogenization of solid samples and has developed a High Energy Ball Mill which fulfills all these requirements. With a High Energy Ball Mill Emax The Revolution in Ultrafine
احصل على السعر
Optimization of the high energy ball-milling: Modeling and
Optimization of the high energy ball-milling: Modeling and parametric study Hamid Ghayour a,Majid Abdellahi a,Maryam Bahmanpour b Add to Mendeley Ball milling is a low-cost and green approach to modify starch. • Recent advancements in the effect of ball milling on starch granules are summarized. • Ball Ball-milling: A sustainable and green approach for starch
احصل على السعر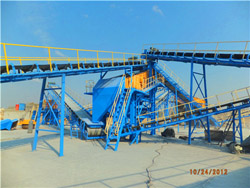
Ball Mill RETSCH powerful grinding and homogenization
High Energy Ball Mills Sample volumes up to 2 x 45 ml Final fineness*: 0.08 µm Easy, ergonomic handling Three different types of mills (ball movement) To the product range Ball milling is a simple, fast, cost-effective green technology with enormous potential. One of the most interesting applications of this technology in the field of cellulose is the Ball milling: a green technology for the preparation and
احصل على السعر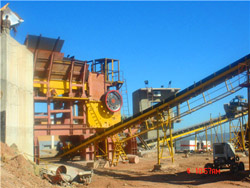
Types of mills for high-energy milling: A-ball mill,
Types of mills for high-energy milling: A-ball mill, B-planetary mill, C-vibration mill, D-attritor (stirring ball mill), E-pin mill, F-rolling mill. 4k Modified from ref. 4d.Simulations and in situ monitoring 27,29,30,31,32,33,34,35,36 of media interactions in high-energy ball mills have shown agreement with the underlying assumptions and estimated impact energiesMechanochemical conversion kinetics of red to black
احصل على السعر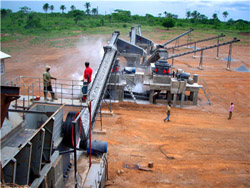
High-energy ball milling of nonstoichiometric compounds
High-energy ball milling ensures a high concentration of energy on the particles. The authors of [ 93,105 109 ] used a Retsch PM-200 mill with grinding bowls and balls made from yttrium oxide-stabilized zirconium dioxide to disintegrate nonstoichiometric titanium, vanadium, and niobium oxides containing tens of percent of Abstract. In this paper, Mg 2 Ni hydrogen storage alloy powder was prepared by high-energy ball milling mechanical alloying method, and the influence of stirring shaft rotation speed, ball milling Preparation of Mg2Ni Hydrogen Storage Alloy
احصل على السعر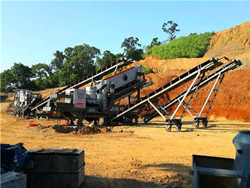
High Energy Ball Mill Emax The Revolution in Ultrafine
The High Energy Ball Mill Emax combines high-frequency impact, intensive friction, and controlled circular jar movements to a unique and highly effective size reduction mechanism. The grinding jars have an oval shape and are mounted on two discs respectively which move the jars on a circular course without changing their orientation.The handling of solids was performed in all cases in an Ar-filled glovebox to prevent exposure to oxygen and water. The reactants lithium sulfide (Li 2 S, Sigma-Aldrich, 99.9%) and phosphorus pentasulfide (P 2 S 5, Merck, 99%) were mixed in the stoichiometric ratio of 75:25.The mixture (8 g) was then processed in a high energy ball mill Emax Effective mechanochemical synthesis of sulfide solid
احصل على السعر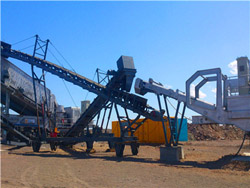
Full article: Mechanical alloying: a critical review
Mechanical alloying (MA) is a powder process that consists of repeated cold welding, fracturing, and rewelding of powder particles in a high-energy ball mill. This process is capable of synthesizing different types of non-equilibrium phases including supersaturated solid solutions, nanocrystalline materials, metallic glasses, high-entropySpecially designed ball mills with a higher milling energy are used for HEBM purposes. Different types of milling equipment are available for nanoparticle formation, including the vibrating mill, planetary ball mill, high-energy rotating mill, and attritors (Fig. 7.2). They differ in capacity, efficiency, and arrangements for heat transfer High-Energy Milling SpringerLink
احصل على السعر
Mechanical Milling: A Superior Nanotechnological Tool for Fabrication
The ball was 10 times heavier than the powder. For reactive milling, the vial was put in a high energy ball mill equipped with a rotary pump and a gas flow system [70,71]. The XRD patterns of the initial elemental hcp-Ti powder samples milled under 10 bar of nitrogen gas for different RBM durations are shown in Figure 29 a–d.The greatest challenge when developing a high energy ball mill is keeping the temperature under control as the enormous size reduction energy leads to considerable heat built-up inside the grinding jar. RETSCH solved this problem with an innovative integrated water cooling system.High Energy Ball Mill Emax The Revolution in Ultrafine
احصل على السعر
BM-400 Mixer/Mill –Single clamp, high-energy ball mill,
The BM-400 Mixer/Mill (part #8000M), is a high-energy ball mill that grinds up to 0.2 10 grams of dry, brittle samples. The vial, which contains a sample and one or more balls, is shaken in a complex motion that combines back-and-forth swings with short lateral movements, each end of the vial describing a figure-8.This review is focused on the topical developments in the synthesis of nanocomposites using the simplest top-down approach, mechanochemical milling, and the related aspects of the interfacial Applied Sciences Free Full-Text Recent
احصل على السعر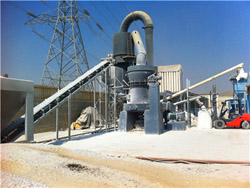
Characterization of Stressing Conditions in a High
The synthesis of sulfide solid electrolytes in ball mills by mechanochemical routes not only is efficient but also can enable the upscaling of material synthesis as required for the commercialization of solid-state battery The Emax is an entirely new type of ball mill for high energy milling. The unique combination of high friction and impact results in extremely fine particles within a very short process time. The high energy input is a High Energy Ball Mills Instead of Planetary Ball
احصل على السعر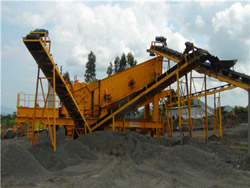
Mechanochemical synthesis of metal oxide nanoparticles
In high-energy ball mills, milling balls are often made of the same material as the milling chamber in order to reduce the contamination level arising from the wear of the chamber and balls 61.Dual clamp, high-energy ball mill that grinds up to 10 grams of sample in each clamp. Dual clamps enable multiple sample processing for high-throughput applications. Equipped with forced-air cooling and safety interlock system for operator protection. Electronic timer is set for 100-minute range. Extended Running Time Chip is available forMixer/Mill high-energy ball mills, mechanical alloying,
احصل على السعر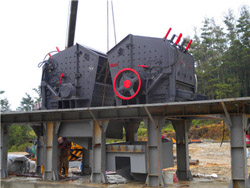
High Energy Ball Mill Nanografi Nano Technology
High Energy Ball Mill. Ball Mill is a grinder that blends or grinds materials for various applications. Impact force enables size reduction in feed material. The main element enabling grinding is the hard and small balls in the ball mill. These balls are usually made of steel. They can also be zirconia or agate etc. High Energy Ball Mill is aMCD Experiments Carried out in a High Energy Ball Mill. A high-energy ball mill (Emax mill, Retsch) equipped with stainless-steel milling jars (50 ml filling capacity) and stainless-steel balls were employed. An experimental set was generated by varying rotational speed, milling time, and ball count and size.Kinetic Energy Dose as a Unified Metric for Comparing Ball Mills
احصل على السعر
(PDF) Characterization of Stressing Conditions in a High Energy Ball
The investigated high energy ball mill Emax (Retsch GmbH, Haan, Germany) features two chambers that move on a circular path with a radius R = 17 mm in the same rotationThe minimum achievable grain size and extent of alloying depend on a number of parameters i.e., type of high-energy ball mill, milling container, ball-to-powder weight ratio, milling speed, grinding medium, extent of filling of the vial, milling atmosphere, process controlling agents, milling temperature, type of material being milled etc. High-Energy Ball Milling Parameters in Production of
احصل على السعر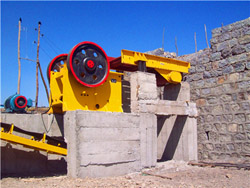
Synthesis of Nanofertilizers by Planetary Ball Milling
The main drawback of the high energy ball milling approach is the non-uniformity of the surface structure formed, i.e., not suitable for preparing uniformly shaped materials. The high energy ball milling devices are of three types namely: shaker mills, attrition mills, and planetary ball mills (Suryanarayana 2001). Shaker mills have a vial
احصل على السعر- gypsum machine for beneficiation
- مورد آلة كسارة الذهب الخام في ماليزيا
- مواصفات مصنع للاسمنت المطرقة محطم
- الأوساخ الترابية
- conveyor belt system supplier in malaysia
- يوتيوب تشغيل المعدات الثقيلة الحفار و
- ومعالجة الفحم ونقل النظام في رصيف الفحم
- قدرة 1000tph كسارة الأولية
- dick dufourd stone crusher
- منتجي كسارة الخبث
- كسارة الحجر المتنقلة الصغيرة بوروندي
- مزدوج تبديل الفك كسارات الرسوم المتحركة
- types of crushers and cost
- من رواسب الفحم الماليزي
- رسم تخطيطي لآلة تكسير الزجاج