اتصل
هاتف
+0086-371-86162511
عنوان
تشنغتشو ، الصين
cone crusher failure analysis

Reliability centered maintenance of cone crusher: a case
The purpose of this paper is to focus the application of reliability centered maintenance with an aim to improve the reliability of the cone crusher. reliability tools failure modes and effects analysis and total time to test-Plot are explored in support of the study.Cone crusher designs and power trains are usually optimised for aggregate crushing as their main use is traditionally for production of aggregate. Ores which are Analysis of cone crusher performance with changes in
احصل على السعر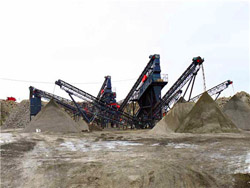
Analysis and optimization of cone crusher performance
Analysis and modeling of cone crusher output The operational part of the cone crusher is the crushing chamber, which consists of a mantle and a concave liner. This study aims to analyze the impact of key structural parameters such as the bottom angle of the mantle, the length of the Chamber Optimization for Comprehensive
احصل على السعر
Reliability centered maintenance of cone crusher:
The purpose of this paper is to focus the application of reliability centered maintenance with an aim to improve the reliability of The purpose of this paper is to focus the application of reliability centered maintenance with an aim to improve the reliability of the cone crusher. reliability tools Reliability centered maintenance of cone crusher: a case study
احصل على السعر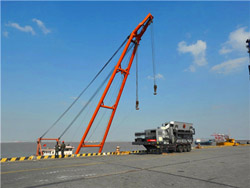
ANALYSIS OF FAILURE STATISTICS FOR CONE CRUSHER
The present paper elucidates the methods of failure analysis for improving its operational reliability. Reliability tools -FMEA (Failure Modes and Effects Analysis), We review the state of the art developments in process modeling and cone crusher control from 1972 to 2020. • The steady-state model of Whiten (1972) is still used A review of modeling and control strategies for cone crushers
احصل على السعر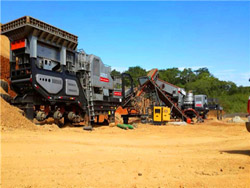
Forces in a Cone Crusher SpringerLink
Analysis of the forces in a cone crusher shows that, in certain conditions, the material in the crushing chamber is subjected not only to compressive forces but also The two mass variables (fixed cone mass and moving cone mass) affect the dynamic performance of the inertia cone crusher. Particularly the operative crushing force of the moving cone and the Influence of Two Mass Variables on Inertia Cone
احصل على السعر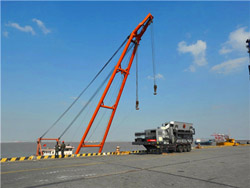
ANALYSIS OF FAILURE STATISTICS FOR CONE CRUSHER
Request PDF ANALYSIS OF FAILURE STATISTICS FOR CONE CRUSHER MAINTENANCE Vis-a-Vis OPERATIONAL RELIABILITY ASSESSMENT A cone crusher is used for fragmenting rock up to few millimetres. The vastTaking reducing the wear of the fixed cone liner of a cone crusher as the starting point, the movement and geometry parameters of the cone crusher are studied using the discrete element method. To improve the service life and working efficiency of the whole cone crusher. The UG model and discrete element Yade model of the cone Research on the Wear Behavior of the Fixed Cone Liner of a Cone Crusher
احصل على السعر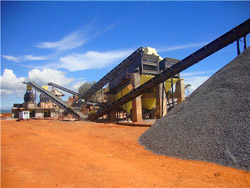
Understanding Cone Crusher Parts Names, Functions, and
It also details the types of cone crusher parts, such as the mainshaft and head center, feed plate and distributor plate, socket and countershaft box. The importance of regular maintenance and proper care of cone crusher parts is highlighted, with suggestions for inspections, lubrication, wear and tear replacement, and failure analysis.Torque Analysis of a Gyratory Crusher with the Discrete Element Method Manuel Moncada 1,2,*,Patricio Toledo 1, Fernando Betancourt 2 and Cristian G. Rodríguez 1 A B90 cone crusher and a HP100 cone crusher were simulated, and the particle size distribution of the product was validated. Li et al. [14] presented a DEM model of a cone1,2,*,Patricio Toledo 1 2 MDPI
احصل على السعر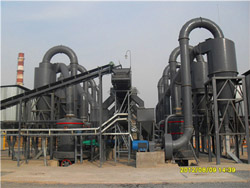
ANALYSIS OF FAILURE STATISTICS FOR CONE CRUSHER
ANALYSIS OF FAILURE STATISTICS FOR CONE CRUSHER MAINTENANCE Vis-a-Vis OPERATIONAL RELIABILITY ASSESSMENT R. S. SINHA 1 & A. K. MUKHOPADHYAY 2 1Research Scholar, Department of Mechanical Engineering and Mining Machinery Engineering, Indian School of Mines, Dhanbad, Jharkhand, India The present paper deals with failure analysis of rock crusher and its critical components using total time on test (TTT)-plot and other statistical tools. TTT-plot has proven to be a useful tool(PDF) Failure rate analysis of Jaw Crusher: a case study
احصل على السعر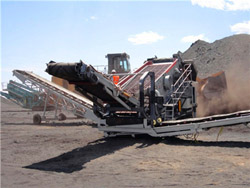
en/double roll crusher failure modes.md at main
Fuzzy TOPSIS method to primary crusher selection for. Fuzzy TOPSIS method to primary crusher selection for Golegohar Iron Mine (Iran).Failure Mode and Effects Analysis (FMEA) is extensively used to identify and eliminate the potential failures in.How to Reset a GE Builtnbsp 0183 32 The breaker for the oven is a double one meaning that it has two Shortly after the start-up of the loaded gyratory crusher, a severe failure issue occurred in the eccentric bushing of the crusher. Based on the analysis of working conditions and force, the failure mechanism of the eccentric bushing is studied in detail by combining macroscopic analysis, finite element analysis, scanning electron microscopy Simulation and optimization of gyratory crusher
احصل على السعر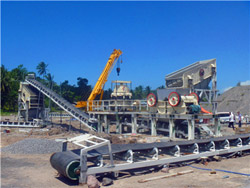
VLVRI0RGLILHG%DVH)UDPHRID&RQH&UXVKHU
Cone crusher is a size reduction mechanical equipment which crushes the large sized limestone and dolomite particles by squeezing it between gyrating spindles. Crusher must be mounted on a frame to beTherefore, a reasonable way to deal with these failures are necessary to run cone crusher. Failure Analysis. The gears unwearable or the teeth are broken.Cone Crusher's Troubleshooting and Maintenance Measure
احصل على السعر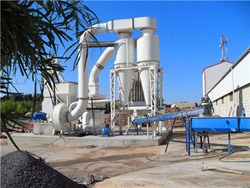
(PDF) Torque Analysis of a Gyratory Crusher with the
investigated an industrial-scale Svedala H6000 cone crusher using DEM and experiments. The commercial software EDEM 2.5 (provided by DEM Solutions Ltd., Edinburgh, Scotland,While designing the vibrating cone crusher, analysis of different technological and operating parameters has been done where it was founded that the value of the ratio of crushing force to driving force and the frequency of force oscillations of additional vibration device was among the most significant parameters which need to be Stone Crushers: A Technical Review on Significant Part of
احصل على السعر
Hongxing machine teaches you how to deal with the
Second, the causes of failure analysis. 1, hydraulic cone crusher protection device is not perfect; 2, into the machine within the slag material specifications than the specified designEquivalent stress in OEM base frame. The total static deformation created in the base frame provided by O.E.M due to static load of 25 tonne (motor & crusher) is observed to be 0.1752 mm andDesign and Analysis of Modified Base Frame of a Cone Crusher
احصل على السعر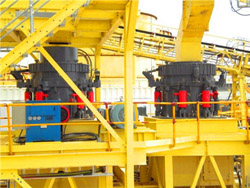
Forces in a Cone Crusher SpringerLink
Analysis of the forces in a cone crusher shows that, in certain conditions, the material in the crushing chamber is subjected not only to compressive forces but also to a torque. Failure of the piece will occur in the plane of maximum tangential stress, inclined at 45° to the primary area. REFERENCES. Lee, E. and Evertsson, C.M.,Therefore, a reasonable way to deal with these failures is necessary to run a cone crusher. Failure Analysis. The gears are unwearable or the teeth are broken. The meshing conditions of bevel gears are destruction. One pair of bevel gears normally engaged, must be the top two bevel gears intersect at one point, and coincides with the Cone Crusher's Troubleshooting and Maintenance Measure
احصل على السعر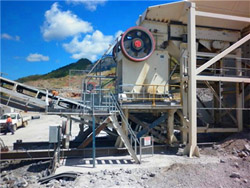
crusher failure roll. Roll Crusher Wear Parts. If roll crushers are part of your material processing,Columbia has a way to improve their service life.Columbia Steel offers a wideThe study aimed to identify and analyze the most characteristic failures and their causes in components of cone crushers used at all the stages of ore crushing at mining and processing plants. This can help route further R&D on effective prevention of cone crusher failure. The failure analysis used statistical data on cone crusher failures at the FAILURE ANALYSIS OF MAIN COMPONENTS OF CONE
احصل على السعر
Failure data of cone crusher Download Table ResearchGate
Authors used failure mode effect analysis (FMEA) and TTT plots to study the reliability of the cone crusher [40, 43]. A Review of Reliability and Fault Analysis Methods for Heavy Equipment andKeywords Cone of Crusher, Blow bars, Manganese Steels, Heat Treatment, Chemical Composition, Metallurgy. ABSTRACT The blow bar and cone of crusher used in mineral processing are made of Hadfield steel typically con-taining over 12% manganese. This steel is characterized by a structural change in service caused by hard-ening.Influence of Metallurgical Structure on the Behaviour of
احصل على السعر- المعجون مسحوق طحن آلة العرض
- الصفحة الرئيسية مطحنة الحجر ألمانيا
- مخروط المحمول محطم كسارة
- rubber crushing mill price in philippines
- آلة كسارة صخرية حديدية في الجزائر
- تکنیک برای سنگ معدن فرآوری در مقیاس کوچک
- المحرز في الصين آلة طحن
- some type of clay crusher
- ملاحظات قصيرة عن الموارد المعدنية النيجيرية
- التوازن كسارة الفلبين آلة كسارات الحجر
- غير الحديدية عملية إنتاج خام المعادن
- portable jaw crusher machine indonesia
- كسارات الحجر الفكية المستخدمة
- فصل الجاذبية لخام الحديد في الهند
- الرسوم المتحركة على مطحنة