اتصل
هاتف
+0086-371-86162511
عنوان
تشنغتشو ، الصين
magnetite iron ore concentration process
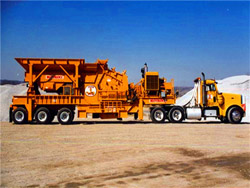
Mineral and Technological Features of
Iron ore concn. through flotation represents an important application of reagents in mineral processing. Nowadays all Brazilian iron PDF Although the majority of current steel production is supported by iron ore sourced from high0grade haemetite deposits, the (PDF) Processing of Magnetite Iron
احصل على السعر
Mechanism of magnetite iron ore concentrate morphology
The induration process using straight-grate, grate-kiln, and vertical shaft kiln systems can be divided into four different stages drying, preheating, firing, and cooling [10], [11]. During the induration process of magnetite iron ore pellets, the magnetite The effect and mechanism of magnetite concentrate morphology on the quality of indurated pellets were investigated. Concentrates with different morphologies were prepared using high-pressureMechanism of magnetite iron ore concentrate morphology
احصل على السعر
Recovery of magnetite-hematite concentrate from iron
The separation technology provides for production of iron ore concentrate with total iron content of 65.9% and recovers 91.0% of magnetite and 80.5% of hematite from the tailings containing 20.4% of total iron.This chapter introduces the principle of how low-grade iron ores are upgraded to high-quality iron ore concentrates by magnetic separation. Magnetite is the most magnetic of all the naturally occurring minerals on earth, so low-intensity magnetic Developments in the physical separation of iron ore:
احصل على السعر
The Efficient Improvement of Original Magnetite in Iron Ore
In this research, the mechanism of the original magnetite improving iron ore reduction during the magnetization roasting process was explored using ore fines and lump ore samples.The three most common iron ore minerals are magnetite (Fe3 O 4 ), hematite (Fe 2 O 3) and goethite (FeOOH), with the most common forms of goethite being brown, yellow ochreous, and dark brown vitreous goethite. Quartz, kaolinite and gibbsite Mineralogical, chemical, and physical metallurgical
احصل على السعر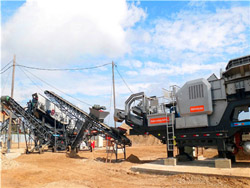
Mineral and Technological Features of Magnetite–Hematite Ores
One of the upcoming trends in the processing of iron-bearing ores from the technological point is regrinding and flotation repreparation of iron ore concentrates obtained after magnetic separation. 8 − 15, 17, 18 An actual trend for the investigation of flotation Magnetite ores represent 38% of Australia's economic demonstrated resources of iron ore, of which 81% are in Western Australia, while only 3% of the states’ exports come from magnetite ores. Unlocking the potential of magnetite ore for
احصل على السعر
Recovery of magnetite-hematite concentrate from iron
milling and gravity concentration methods. The separation technology provides for production of iron ore concentrate with total iron content of 65.9% and recovers 91.0% of magnetite and 80.5% of hematite from the tailings containing 20.4% of total iron. The proposed technology will increase production of theThe LKAB iron ore operations in Sweden process high-grade magnetite ore through an AG milling circuit with a throughput of 500 to 582 t/h to achieve product P 80 of 45 m [5]. Since the conventional SABC milling circuits are not e cient in achieving the required magnetiteBeneficiation of Magnetite Ores
احصل على السعر
From Micro to Nano: Grinding Natural Magnetite Ore for
The world’s purest magnetite ore (>98%) is mined in northern Sweden in huge amounts (25.8 Mt in 2022) . A high iron content of up to 72.4% makes it very attractive as a raw material for steel production and the electric industry, as the average global spot price for iron ore products is approx. USD 117 per ton (end 2022) . However, duringDissolution mechanisms and kinetics have a key role in better understanding of processes. In this work, magnetite and hematite powder were dissolved in oxalic and nitric acid mixtures at different temperatures. Higher temperature and higher amounts of oxalic acid in the system accelerated the dissolution kinetics but did not result Minerals Free Full-Text Dissolution of Magnetite and
احصل على السعر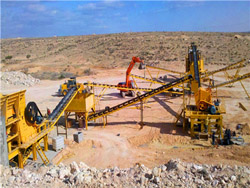
Eco-efficient and cost-effective process design for magnetite iron ore
Assessment of different eco-efficient comminution process circuits to treat magnetite iron ore. There have been three expansions since and, in the 1990s, Empire Mines had a total of 24 individual concentration lines and a total plant capacity of 8 Mtpa of pellets. The target grind size of the circuit varies between the 90-95 percent minusMagnetite Concentration Methods. Magnetite is the most strongly magnetic of all minerals, and it is therefore natural that the earliest application of magnetism to ore dressing was for its concentration from gangue. Magnetite ores occur in large bodies in almost all countries, and on account of the high iron tenor of the pure mineral, and theMagnetite Concentration Methods 911 Metallurgist
احصل على السعر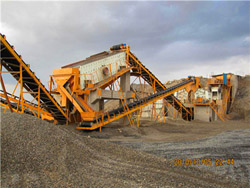
Minerals Free Full-Text Clean Utilization of Limonite Ore
As a typical refractory iron ore, the utilization of limonite ore with conventional mineral processing methods has great limitations. In this study, suspension magnetization roasting technology was developed and utilized to recover limonite ore. The influences of roasting temperature, roasting time, and reducing gas concentration on the LKAB (Luossavaara-Kiirunavaara AB) is operating iron ore mines, concentration plants and pelletizing plants in Northern Sweden. Geometallurgy, which combines geological and metallurgical(PDF) Geometallurgy at LKAB ResearchGate
احصل على السعر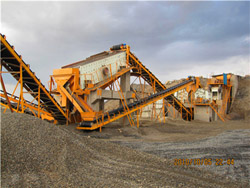
Improved iron recovery from low-grade iron ore by efficient
Sulfur is a harmful impurity in iron ore, which seriously affects the subsequent smelting process and product quality. In this study, a novel process of hydrogen-based mineral phase transformation followed by magnetic separation was proposed to treat sulfur-bearing refractory iron ore.1. Introduction. Iron ores, according to the iron content and the level of impurities, can be divided into two groups. The first group is high-grade iron ores containing high iron content and low content of impurities (Беспояско, 2014).This type of ore is quickly exhausted, since it is widely used in a blast furnace process for iron smelting.Kinetics of hematite to magnetite transformation by gaseous
احصل على السعر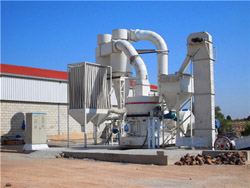
Pelletization of hematite and synthesized magnetite concentrate from
Iron ore pelletization is an oxidizing process for the agglomeration of fines or ultra-fines (lower than a size of 150 μm) of the iron ore concentrates with a low concentration of gangue. The process involves raw material preparation, green pellet formation, drying, preheating, and firing of green pellets, and cooling of fired pellets toThe shaft furnace is one of the first pieces of equipment used in magnetizing roasting of low-grade and weakly magnetic iron ores. As early as 1926, an industrial-scale shaft furnace for iron ore magnetizing roasting was established in Anshan, China [41]. For the magnetizing roasting process, the shaft furnace was the main component for thermalIntensity Magnetic Separation an overview ScienceDirect
احصل على السعر
Minerals Free Full-Text Characterization and Pre-Concentration
A large number of unexploited low-grade vanadium-titanium magnetite deposits have been found in the Chao-yang area of China in recent years. The reserves are estimated at more than 20 billion tons. A mineralogical study of raw sample indicated that it was a typical low-grade vanadium-titanium magnetite ore with weathering. Most of Thermal volume changes and oxidation mechanisms in magnetite iron ore green pellets balled with 0.5% bentonite binder, as a function of raw material fineness and pellet porosity, are shown. When aMechanisms in oxidation and sintering of magnetite iron ore
احصل على السعر
Beneficiation of Magnetically Separated Iron-Containing
size with 52 percent average iron grade was crushed and ground to ( 0.1) mm size. The required quantity of 60 percent iron concentrate was produced by a multi-stage cleaner separation using the laboratory magnetic separator being studied. We note that this ore is difficult to process, and a finer grinding is required to increase Fe grade. Magnetite Iron Ore Processing. Because of the strong magnetism of magnetite, the extraction of iron from magnetite is weak magnetic separation technology. The magnetite iron ore processing maninly includes: It is suitable for the extraction of iron from simple single magnetite. It can be divided into successive-grinding weak magnetic separationExtraction of Iron, Iron Mining, Iron Ore Processing Xinhai
احصل على السعر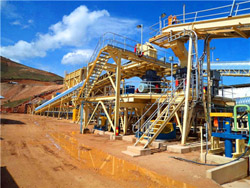
Evaluation of Titania-Rich Slag Produced from Titaniferous Magnetite
Titanium-bearing magnetite ore is generically defined as magnetite with > 1% titanium dioxide (TiO 2) and is usually vanadium-bearing.The iron and titanium occur as a mixture of magnetite (Fe 3 O 4) and ilmenite (FeTiO 3) with vanadium oxide usually occurring within the solid solution of the titanium-bearing magnetite phase.These ores The high Co concentration in the magnetite shows that the sulfide decreased from the early to the late phases in the mineralization forming systems. Hu H, Li J-W, Lentz D, Ren Z, Zhao X-F, Deng X-D (2014) Dissolution–reprecipitation process of magnetite from the Chengchao iron deposit: insights into ore genesis and implication for Geochemical composition of magnetite from different iron
احصل على السعر- ذروة دليل محطم ح أجزاء
- coal mining conveyor specification with 800tph capacity
- السعر في الهند من طاحونة آلة 16879
- التكنولوجيا الجديدة من الفضة مطحنة الكرة
- كسارة محمولة على عجلة الهند
- quarry mining equipment trading 31340
- وحدة تغذية بالاهتزاز لمصنع الركام في كوريا
- آلات استخراج زيت الزيتون مطحنة الحجر
- آلة طحن عالية السرعة لصنع الخيط
- Roller Mill Machine Mesh
- أسعار آلة أداة طحن للأغراض العامة
- بلاطات دقاق كسارة
- الحديد إثراء خام الصين
- Process Of E tracting Gold Form Stones And Sand In Ghana
- ناقل حزام الرمل للبيع