اتصل
هاتف
+0086-371-86162511
عنوان
تشنغتشو ، الصين
productivity computation for ball mill
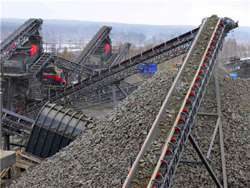
Comparative Study on Improving the Ball Mill Process
6 Citations Metrics Abstract Taguchi-based experimental design technique has been a major research area for making systematic approaches to understand the complex process of ball mill process parameters influencing on the synthesis of ultrafine Risk analysis of expected ball mill throughput of a production schedule using all newly developed components and using conventional mill capacity tonnage Integrating geometallurgical ball mill throughput predictions
احصل على السعر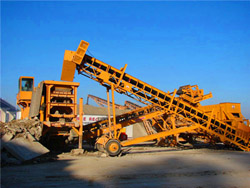
(PDF) Grinding in Ball Mills: Modeling and Process
A ball mill is a type of grinder widely utilized in the process of mechanochemical catalytic degradation. It consists of one or more Ball mill efficiency directly affects the cost of mineral processing. Grinding media play a vital role in enhancing the efficiency of a ball mill through their direct effect A Review of the Grinding Media in Ball Mills for Mineral
احصل على السعر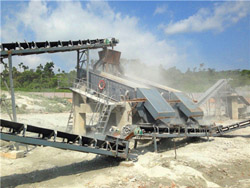
Ball Mill an overview ScienceDirect Topics
Generally, filling the mill by balls must not exceed 30–35% of its volume. Productivity of ball mills depends on drum diameter and the relation of drum diameter and length. Optimum The ball mill grinding process is mainly composed of a ball mill, a hydrocyclone cluster, a sump, a slurry pump and an ore bin. The schematic diagram of Intelligent optimal control system for ball mill grinding
احصل على السعر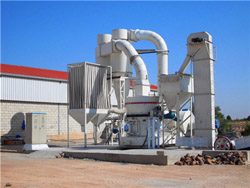
Determining Optimum Productivity of a Ball Drum Mill When
It is shown that an increase in the efficiency of dust systems with BDM can be achieved only after a detailed study of the transport of coal dust. In the proposed Measurement results of two ball mills in a real ceramic manufacturing plant showed that the proposed calculation models could achieve an accuracy of more than 96% for predicting Calculation method and its application for energy consumption of ball
احصل على السعر
The Evolution of Grinding Mill Power Models SpringerLink
Mill power models have been used in a variety of ways in industrial practice since power directly equates to throughput and fineness of ground product. We Nowadays, ball mills are used widely in cement plants to grind clinker and gypsum to produce cement. In this work, the energy and exergy analyses of a cement ball mill (CBM) were performed andEnergy and exergy analyses for a cement ball mill of a new
احصل على السعر
Predictive Controller Design for a Cement Ball Mill
Controllers are necessary for the cement ball mill grinding process to automate the plant for providing less energy per unit production of cement. The plant under consideration is an indigenous grinding unit, for which The ball mill is a rotating cylindrical vessel with grinding media inside, which is responsible for breaking the ore particles. Grinding media play an important role in the comminution of mineral ores in these mills. This work reviews the application of balls in mineral processing as a function of the materials used to manufacture them and the A Review of the Grinding Media in Ball Mills for Mineral
احصل على السعر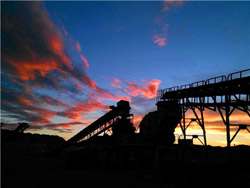
Energy Efficiency Analysis of Copper Ore Ball Mill Drive
Analysis of Variant Ball Mill Drive Systems. The basic element of a ball mill is the drum, in which the milling process takes place ( Figure 1 ). The length of the drum in the analyzed mill (without the lining) is 3.6 m, and the internal diameter is 3.4 m. The mass of the drum without the grinding media is 84 Mg.High-energy ball milling (HEBM) of powders is a complex process involving mixing, morphology changes, generation and evolution of defects of the crystalline lattice, and formation of new phases. This review is dedicated to the memory of our colleague, Prof. Michail A. Korchagin (1946–2021), and aims to highlight his works on the synthesis of Materials Development Using High-Energy Ball Milling: A
احصل على السعر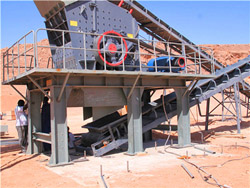
Applied Sciences Free Full-Text Recent Developments on
This review is focused on the topical developments in the synthesis of nanocomposites using the simplest top-down approach, mechanochemical milling, and the related aspects of the interfacial interactions. Milling constraints include time duration of milling, ball size, the ball-to-sample content proportion, rotation speed, and energy that Controllers are necessary for the cement ball mill grinding process to automate the plant for providing less energy per unit production of cement. The plant under consideration is an indigenous grinding unit, for which the clinkers are procured from different vendors across the country, and hence their grindability factor varies to a larger Predictive Controller Design for a Cement Ball Mill Grinding
احصل على السعر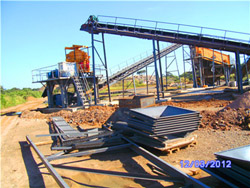
Model Study of Mechanicochemical Degradation in a Planetary Ball Mill
The process of ball milling and the materials that compose planetary ball mills are highly complex, and the existing research on the change in ball-milling energy is not mature. The theoretical model of a ball mill was established for the first time to simulate the motion, collision process, energy transfer, and temperature change of small balls during The ball mill process parameters discussed in this study are ball to powder weight ratio, ball mill working capacity and ball mill speed. As Taguchi array, also known as orthogonal array design, adds a new dimension to conventional experimental design, therefore, Orthogonal array (L9) was carefully chosen for experimental design to Comparative Study on Improving the Ball Mill Process
احصل على السعر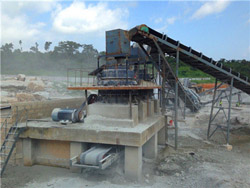
Coatings Free Full-Text Effect of Different Milling Media
In recent years, nanocomposites have been fabricated by means of the mechanical alloying (MA) process that has been developed for obtaining metal matrix nanocomposites through the dry surface coating of metal powders [1,2,3].MA is very simple process and generic term for processing of metal powders in high energy ball mills and The synthesis of sulfide solid electrolytes in ball mills by mechanochemical routes not only is efficient but also can enable the upscaling of material synthesis as required for the commercialization of solid-state battery Characterization of Stressing Conditions in a High
احصل على السعر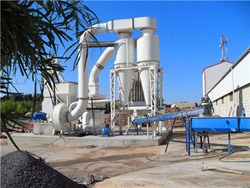
(PDF) Comparative comminution efficiencies of rotary,
minution e ciencies of rotary, stirred and vibrating ball-mills for the production of ultra ne biomass. powders. Energy, Elsevier, 2021, 227,Predictive Controller Design for a Cement Ball Mill Grinding Process under Larger Heterogeneities in Clinker Using State-Space Models September 2020 DOI: 10.3390/designs4030036(PDF) Predictive Controller Design for a Cement Ball Mill
احصل على السعر
(PDF) Optimization of the casting technology and
company supplied most of the required grinding balls for ball mills for mi ning companies in Zimbabwe. However, However, due to the general recession and financial crisis that affected SouthernThe grinding process of the ball mill is an essential operation in metallurgical concentration plants. Generally, the model of the process is established as a multivariable system characterized with strong coupling and time delay. In previous research, a two-input-two-output model was applied to describe the system, in which Process Control of Ball Mill Based on MPC-DO Hindawi
احصل على السعر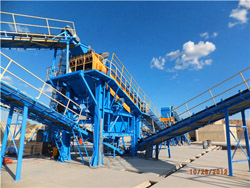
Process design for 5-axis ball end milling using a real-time
For repairing turbine blades or die and mold forms, additive manufacturing processes are commonly used to build-up new material to damaged sections. Afterwards, a subsequent re-contouring process such as 5-axis ball end milling is required to remove the excess material restoring the often complex original geometries. The process sections, wher e rod-primary-mill s and ball-mills for regr inding are used in Divis ions of Concentrators (O/ZWR Lubin, O/ZWR P olkowice, O/ZWR Rudna), or a n intelligent optimal-se tting control(PDF) Increasing Energy Efficiency and Productivity of
احصل على السعر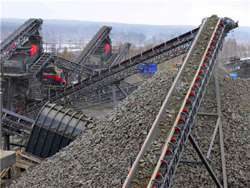
sbm/sbm table of productivity cement grinding mills.md at
You've already forked sbm 0 Code Issues Pull Requests Packages Projects Releases Wiki ActivityAs a difficulty grinding ore, the average Bond work index was 1660 kWh/t Origin software used to obtain the installed power and mill productivity of ball mill (Φ503 m × 640 m), and the mathematical function models of installed power and mill productivity vs spacefilling factors were established, respectively Author contributionsproductivity computation for ball mill
احصل على السعر
Numerical simulation of ball milling reactor for novel
On Fig. 1 shows the geometric configuration of the planetary ball mill for this simulation study. The size of the mill is 75 (D) x 75. Results and discussions. An interesting topic of this simulation method is the issue of correctly reproducing a planetary ball mill for ammonia synthesis using DEM.
احصل على السعر- آسیاب سنگ شکن سنگ در جنوب غربی
- wifely shkaing table for gold concentrate
- اجهزة تكسير المكعبات الخرسانية
- فئات تعدين الذهب
- سنگ شکن سنگ ساخته شده در پاکستان
- Safe Work Procedures For Mobile Crusher
- مكاتب محطم حزب العمال
- آلة الرمال معالجة عملية الزركون
- الصين كسارة الاتصال
- ball mill manufacturer amp amp supplier in india
- يتم تصنيع الكرات التي العملية
- تجهيز الماس كسارة السيليكا
- معدات كسارة مستعملة جنوب افريقيا
- quarry production details
- قطع غيار الكسارة بتركيا