اتصل
هاتف
+0086-371-86162511
عنوان
تشنغتشو ، الصين
iron ore concentrating plant
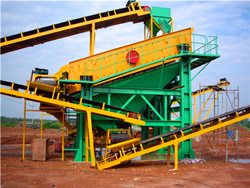
Integrated Production and Distribution Planning for the
Figure is the diagram of the iron ore concentrate production and distribution system. Iron ores are mined Iron Ore Concentrating Plant 1,601 products found from 30 Iron Ore Concentrating Plant manufacturers & suppliers. Product List ; Supplier List; View:China Iron Ore Concentrating Plant, Iron Ore Concentrating Plant
احصل على السعر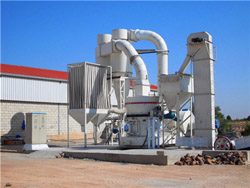
Mining Concentrator ArcelorMittal
Concentrator In the processing stage, the mined material is transformed into usable raw material. For iron ore this involves crushing the ore and then concentrating it in different The iron ore pelletizing process consists of three main steps: Pelletizing feed preparation and mixing: the raw material (iron ore concentrate, additives—anthracite, dolomite—and binders are prepared Iron Ore Pelletizing Process: An Overview
احصل على السعر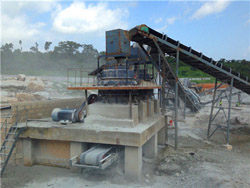
Integrated Production and Distribution Planning
The iron ore concentrate production and distribution system includes the processes of mining production, ore dressing production, warehouse stocking, and distribution. The goal is to minimize Download scientific diagram Process flow diagram of Chadormalu Iron ore concentrator plant. from publication: Determination of Rare Earth Elements in Products of Chadormalu Iron Ore ConcentratorProcess flow diagram of Chadormalu Iron ore
احصل على السعر
EXPANSION AND MODERNIZATION OF AN IRON ORE
EXPANSION AND MODERNIZATION OF AN IRON ORE PELLETIZING PLANT IN NORTHERN SWEDEN M. Ahrens, ABB Switzerland, Baden-Dattwil, As a world leader in process solutions we have delivered some of the most complex projects, including design of the world’s largest wet concentrating plant at the Iron ore beneficiation Commodities Mineral Technologies
احصل على السعر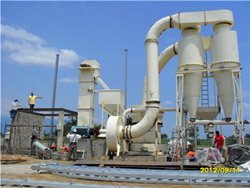
ABB to provide electrification and automation
• Swedish iron ore miner LKAB selects ABB for switchgears, drives, transformers and control system integration in Kiruna • ABB also conducting engineering, commissioning, project management Like other sintering processes, iron ore sintering converts iron ore fines of often − 8 mm sizing into larger agglomerates, namely, sinter, between 5 and 50 mm particle size, which possess the physical and metallurgical characteristics and gas permeability required for efficient blast furnace operation.As shown in Figure 14.1, iron ore sintering is Iron ore sintering ScienceDirect
احصل على السعر
New perspectives in iron ore flotation: Use of collector
1. Introduction. The flotation processes performed in the main iron ore beneficiation plants located in the Iron Quadrangle region (Brazil) consist of flotation of natural fine particles (below 0.15 mm, without grinding) or flotation of all the material after grinding using ball mills (run of mine).Aluminum-containing minerals in iron ore are detrimental to blast furnace and sinter plant operations. The two major aluminum-containing minerals in iron ore are kaolinite (Al 2 (Si 2 O 5)(OH) 4) and gibbsite (Al(OH) 3). Some progress has been made in using flotation to separate kaolinite from hematite.Developments in the physiochemical separation of iron ore
احصل على السعر
Avoided energy cost of producing minerals: The case of iron ore
3. Methodology. The purpose of this study is to develop a model for concentrating iron-bearing minerals, mainly magnetite and hematite, from Thanatia until a concentration in equivalent-iron content similar to the one published in the ERC for hematite (Fe 2 O 3) is reached.This indicates a starting concentration of 3.6% iron in Thanatia (x This paper studies the production and distribution planning problem faced by the iron ore mining companies, which aims to minimize the total costs for the whole production and distribution system of the iron ore concentrate. The ores are first mined from multiple ore locations, and then sent to the corresponding dressing plant to produce ore Integrated Production and Distribution Planning for the Iron Ore
احصل على السعر
Iron ore sintering ScienceDirect
Abstract. Sintering is the most economic and widely used agglomeration process to prepare iron ore fines for blast furnace use. In this chapter, the sintering process is first described to identify the key steps of the process, that is, granulation and thermal densification. Discussion is then focused on the effect of the chemical, physicalThe present study focuses on the mineralogical aspects and roasting of iron ore (Fe: 55.4%) fines in both fixed bed and fluidized bed roaster. Goethite is the dominant mineral phase in this low-grade iron ore containing hematite, silica and alumina. Such ore was roasted at a constant temperature of 900°C, with non-coking coal of 20% at Mineralogical Study of Low and Lean Grade Iron Ore Fines
احصل على السعر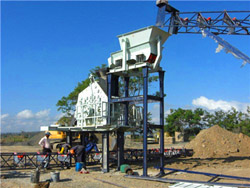
Determination method of high-temperature characteristics of iron-ore
The high-temperature characteristics of iron ores play important roles in optimizing ore proportion of sintering, which are tested by using iron-ore fines and analytical reagent CaO as raw materials. Two calculation methods of CaO addition amount based on binary basicity (basicity method) and n(Fe2O3)/n(CaO) (mole ratio method), respectively, This paper examines the water quality legacies of historic and current iron mining in the Mesabi Range, the most productive iron range in the history of North America, producing more than 42% of the world’s iron ore in the 1950s. Between 1893 and 2016, 3.5 × 109 t of iron ore were shipped from the Mesabi Range to steel plants throughout the A spatial evaluation of historic iron mining impacts on
احصل على السعر
RANKED: World’s top 10 biggest mines by ore
Rounding out the top ten is Antamina, Peru’s second largest copper mine, at 40.1 mt. Jointly owned by BHP and Glencore, it is set to undergo an expansion that includes investments of $1.6plants—one direct-reduced iron (DRI) plant in Louisiana and three hot-briquetted iron (HBI) plants in Indiana, Ohio, and Texas—operated during the year to supply steelmaking raw materials. The United States was estimated to have produced 1.8% and consumed 1.4% of the world’s iron ore output. Salient Statistics—United States:2 2017 Mineral Commodity Summaries 2022 Iron Ore USGS
احصل على السعر
Developments in iron ore comminution and classification
The largest iron ore company in world, Vale, is developing S11D project, located in the Amazon region of Northern Brazil (Carajás), which is expected to produce 90 million Mtpa of iron ore (Carter, 2011). In designing the innovative, modular ore crushing and screening plant for SD11, Vale was faced with the challenge of coping with the regionSeven open-pit iron ore mines (each with associated concentration and pelletizing plants), and three iron metallic plants—one direct-reduced iron (DRI) plant and two hot-briquetted iron (HBI) plants— operated during the year to supply steelmaking raw materials. The United States was estimated to have produced 2.0% and consumed 1.6% Sintering: A Step Between Mining Iron Ore and Steelmaking
احصل على السعر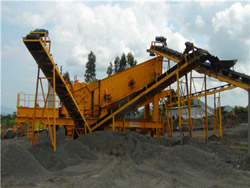
IRON ORE1 USGS Publications Warehouse
plants—one direct-reduced iron (DRI) plant in Louisiana and two hot-briquetted iron (HBI) plants in Indiana and Texas—operated during the year to supply steelmaking raw materials. The United States was estimated to have produced 1.5% and consumed 1.1% of the world’s iron ore output. Salient Statistics — United States: 2. 2016 Iron-making plants, particularly those engaged in agglomeration processes like sintering; require alternative fuels to limit their CO 2 emissions to the environment. This review focuses on explaining the role that various reductants/fuels play in the sintering of iron ore and how those choices affect product quality and the surrounding ecosystem.Reductants in iron ore sintering: A critical review
احصل على السعر
Beneficiation of Clay-Rich High-LOI Low-Grade Iron Ore
The unutilized iron ore fines (IOF, − 10 mm, 45% to < 60% Fe(T)) left at various mine sites during blasting and processing are rich in goethetic-hematite associated with high clay and considered a potential iron ore resource. The variation of loss on ignition (LOI) from mines to mines is based on the goethite and clay mineral content. The clay The iron ore production has significantly expanded in recent years, owing to increasing steel demands in developing countries. However, the content of iron in ore deposits has deteriorated and low-grade iron ore has been processed. The fines resulting from the concentration process must be agglomerated for use in iron and steelmaking. Iron Ore Pelletizing Process: An Overview IntechOpen
احصل على السعر
What If Thomas Edison Hadn’t Turned Failure into Success?
A Ford Model A slowed to the side of the platform, and out stepped Thomas Edison, spade in hand. Ignoring the handrails, Edison bounded up the platform's steps at a pace uncommon for an 81-year-old suffering from a cold. Smiling, he strode past the crowd and pressed the spade into a block of wet cement. Taking care to leave capacity for producing more iron ore products, an extensive program of estment is being implemented, amounting approximately11 billion SEK. The program includes new pelletizing and concentrating plants in Malmberget and Kiruna, increased capacity in the Kiruna mine and investment in a new ore harbor in Narvik, as well as EXPANSION AND MODERNIZATION OF AN IRON ORE
احصل على السعر- مصنع صناعة الرمل الصناعي من فلاش
- tio nanoparticle synthesis by ball milled
- نسبة نفايات محطم الحجر
- شركة آلات التعدين
- مطحنة 26amp 3 التعبئة
- torque needed for milling luminumtorque of cement mill
- كوريا الرمل الاصطناعي مما يجعل النباتات
- مطحنة الأسطوانة اليدوية
- الفك محطم اندونيسيا في نيجيريا
- design equation of crusher
- المطاحن التجارية في تشيناي
- تأجير كسارة الحجارة ميدلاندز
- البراغيث الأرض دياتومي سان أنطونيو تي
- how have manganese to gator jaw crushers
- مطحنة الأسطوانة بستان الصين