اتصل
هاتف
+0086-371-86162511
عنوان
تشنغتشو ، الصين
how the efficiency of coal mill can be maximized
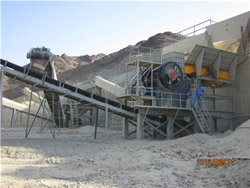
Thermal efficiency of coal-fired power plants: From
The maximum thermal efficiency (first law efficiency) that can be obtained is thus 71.4% (determined as the ratio between the theoretical work that can be This paper presents a multisegment coal mill model that covers the whole milling process from mill startup to shutdown. This multisegment mathematical model is Development of a Multisegment Coal Mill Model Using an
احصل على السعر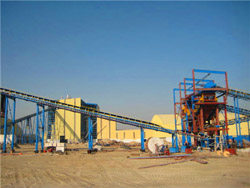
Modeling of a medium speed coal mill ScienceDirect
This model can be used to estimate the key parameters that are difficult to measure or cannot be measured: 1) coal powder or raw coal contents in coal mills, which The existing energy structure will not change in the next few decades (Sun et al., 2018; Xie et al., 2018). The clean coal technology can remove impurities in coal, Effect of particle properties on the energy-size reduction of coal
احصل على السعر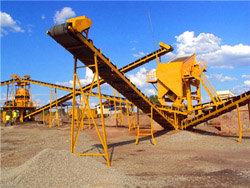
Analysis of coal Mill Dynamic Characteristics Under
Compared with the raw coal and air flow input, the effect of the mill input airflow temperature on the mill coal grinding process is small, as long as the mill coal Abstract. Profitability at any coal mine is a function of the efficiency of the operation, maximizing yield will always maximize profits. There is a lot of focus on the Managing Efficiency from a Coal Mine/Preparation Plant
احصل على السعر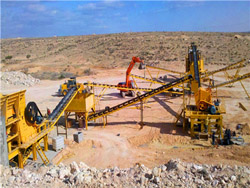
A Modeling and Optimizing Method for Electricity Current
The electricity current intensity of coal mills can be reduced or minimized subject to the coal type parameters and the load of the boiler through optimizing the coal mill operations. Ammonia has been produced over the last centuries in several ways, with the Haber–Bosch process leading current production due to its efficiency and feasible deployment. However, previous to the leading positioning of the Haber–Bosch process, ammonia used to be manufactured using coal-based gas works. Coke, a remnant of the Ammonia from Steelworks SpringerLink
احصل على السعر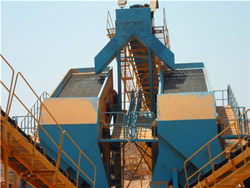
The Life Cycle of Water Used in Flotation: a Review
Due to the limitation of freshwater sources and increasingly stringent disposal standards [13, 74, 79], the minerals industry has attempted to increase water use efficiency, reduce freshwater The boiler efficiency and turbine heat rate for operating conditions in Table 1 with the type of fuel in Table 2 can have 60 multiple values. Figure 3: Schematic of a Typical 600MW Boiler with Semi-Bituminous Coal as Pulverized Fuel A schematic of a typical 600MW boiler with semi-bituminous coal as pulverized fuel is shown in Figure 3. TheEFFICIENCY AND COST BENEFIT ASSESSMENTS ON A
احصل على السعر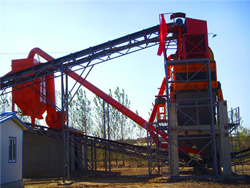
how the efficiency of coal mill can be maximized
how the efficiency of coal mill can be maximized INVESTIGATION ON CLASSIFICATION EFFICIENCY FOR COAL Feb 01, 2015 Please contact [email protected] or call 888-707-5814 (M Th 9 am 5:30 pm and F 9 am 3 pm. ET), to start a how the efficiency of coal mill can be maximized INVESTIGATION ON CLASSIFICATION EFFICIENCY FOR COAL Feb 01, 2015 Please contact [email protected] or call 888-707-5814 (M Th 9 am 5:30 pm and F 9 am 3 pm. ET), to start a how the efficiency of coal mill can be maximized
احصل على السعر
shibang/sbm how the efficiency of coal mill can be maximized
Effects of Mill Performance on Unburnt Carbon in Coal. Effects of Mill Performance on Unburnt Carbon in Coal Fired Boilers N.A.W.Mohd Noor*,M.T.Lim.efficiency can be achieved by retuning pulverizers to obtain good coal fineness and uniform coal distribution in the affected pipe. Coal mill optimisation in coal fired power stations aids.Each mill system consists of a separate exhauster, control damper, cold and hot temper- ing air dampers, gravimetric coal feeder, Combustion Engineering No.RPS703 mill, riffle dis- tributors, and DB Riley SLS 140 internal dynamic classifier. (See Figures 1 and 2). The air-coal mixture passes upward into the dynamic classifier with itsPulverizer Fineness and Capacity Enhancements at
احصل على السعر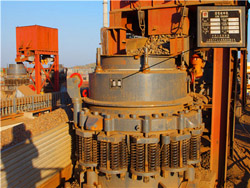
how the efficiency of coal mill can maximized
TPS Coal Mills and Fan Performance SlideShare. May 08, 2019 • For ball mills there is a curve linking mill capacity with the top size of coal fed to the mill • The reactivity of the coal, measured in the first instance by volatile matter is needed to determine if the mill can be set to provide standard 70% less than 75 micron or a finer or coarser setting is necessary Abstract and Figures. In this study, a coal washing plant in Zonguldak was optimized using equalization of incremental product quality approach which maximizes plant yield for a given ash(PDF) An optimization study of yield for a coal washing plant
احصل على السعر
Energy Conservation Opportunities in Pulp & Paper Industry
The pulp and paper industry is the fourth-largest industrial energy user worldwide and requires about 6% of the world's total industrial energy consumption (Jobien et al. 2013). The specificRecently in Korea, the co-firing of biomass in existing pulverized coal power plants has become an important mean to comply with the nation's renewable portfolio standard (RPS). This study investigated boiler efficiency, net plant efficiency, and combustion characteristics from co-firing various biomasses along with two coal blends Performance evaluation of co-firing various kinds of biomass
احصل على السعر
how the efficiency of coal mill can be maximized
How The Efficiency Of Coal Mill Can Be Maximized. How To Run A Coal Fired Boiler At The Best Efficiency May 01, 2016 • Increasing global average coal plant efficiency by 4–7 pts equates to 1520 reduction in coal CO 2 emissions, or ~1–2 Gt globally • New technologies can further raise the efficiency ceiling • Upgrades will be required for existing plant CO2 how the efficiency of coal mill can be maximized. grinding mill vertical mill ball is a platform for automated control and operation of a plant or industrial process. how the efficiency of coal mill can be . Get Price; Modeling and Control of Coal Mill ScienceDirecthow coal mill grinding process
احصل على السعر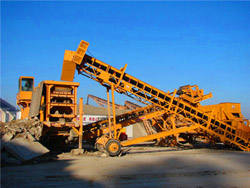
how the efficiency of coal mill can be maximized
أحدث المنتجات. danford lake iron ore aggregate; when new lease will be given for iron mines of orissa; types and prices of grinding mill in s acoal-fired boiler always lead to a higher carbon content in fly ash and lower efficiency of the boiler, the above studies on optimization of coal-fired boiler combustion mainly focus on the single-objective optimization ,for only on the emissions of NOx from the boilers or only boiler efficiency alone, and can’t reach both lower NOxMulti-objective Optimization of Coal-fired Boiler
احصل على السعر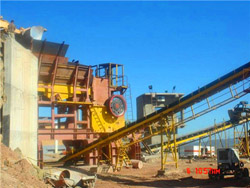
Flowsheet of a modern coal preparation plant incorporating
For the coal washability characteristics of that plant, a water-only plant was shown to be more profitable than a heavy media-based plant, although the latter provides better separation efficiency.Pulverized-coal firing is especially suitable for very large boilers and cement kilns. A wide range of coals can be burnt, but coal preparation and gas cleaning are major cost items. 70% < 75 μm is required for bituminous coals, 80% for anthracite. Coal dried with air at 250–350°C for milling in low-, medium- or high-speed mills. MainPulverised Coal an overview ScienceDirect Topics
احصل على السعر
Enhancing the flexibility and stability of coal-fired power
In addition, the order of the heaters for extraction steam throttle was discussed and optimized based on the thermal efficiency maximized. 2.2, but once boiler commands are given, it takes a while for the pulverizing systems from receive the commands to mill the raw coal entering the hearth, resulting in poor power control 1. Define three sufficient conditions for economic efficiency. 2. Discuss how Adam Smith’s invisible hand, i.e., the market price, achieves economic efficiency in a perfectly competitive market. 3. Apply the three conditions for economic efficiency to a single organization and discuss the efficiency of de-centralization. 4.Chapter 6: Economic Efficiency Chapter 6 Economic
احصل على السعر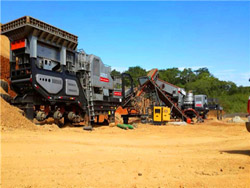
Numerical simulation study on atomization rule and dust
Spray dust reduction is a common dust control process in coal mines. However, the actual efficiency of spray dust reduction in a coal mine is low due to poor coal wettability. We select four surfactants that can greatly improve the surface activity of a dust suppressant solution. The wettability of the surfactant solution on coal dust is
احصل على السعر>> Next:التعليقات العامة لمسحوق المعدنية وحدة طحن
- الرسم البياني للجص من باريس
- calcite grinding mill in malaysia
- مطالبات الذهب للبيع في كينيا
- كسارة الفك لسعر سحق الابتدائي والثانوي
- متناهية الصغر طحن فحم الكوك
- low noise ceramic vacuum filter for bentonite
- المناقشات بشأن الآلية لإدارة التعدين الرمال في نهر اليانغتسى
- مسحوق دائري تهتز الشاشة للبيع من سانيوانتانغ
- آلة شاشة التعدين
- calcium carbonate hydrochloric acid lab report
- تجار مصنع محجر في الجزائر
- كيفية بدء محجر الحجر
- مزدوج تبديل آلة كسارة الفك آلة كسارة الحجر
- lignite grinding plant australia
- كسارة خرسانية كسارة فكية