اتصل
هاتف
+0086-371-86162511
عنوان
تشنغتشو ، الصين
iron ore mill scale process
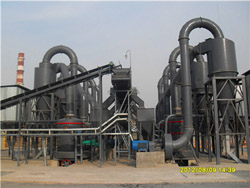
Closed crucible reduction of lump powdered mill scale or iron ore
Various reductants suitably used in direct reduction of iron ore or iron-bearing materials like mill scale. DRI or Metallized iron ore can be produced from iron-bearing raw material by two different processes: Coal-based and Gas based reduction Mill Scale is a by-product of the rolling mill in steel hot rolling processes. It contains both iron in elemental form and three types of iron oxides: wustite (FeO), Overview on production of reduced iron powder from mill scale
احصل على السعر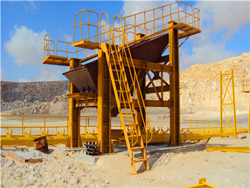
Recycling of steel plant mill scale via iron ore sintering plant
During the processing of steel in steel mills, iron oxides will form on the surface of the metal. These oxides, known as mill scale, occur during continuous casting, reheating and hot Based on the current study it could be concluded that using a tilting rotary furnace is an efficient approach in the mill scale reduction process since the process Production of reduced iron from mill scale waste using tilting
احصل على السعر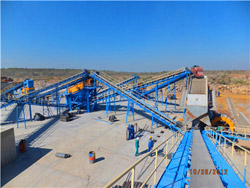
Utilising of the oiled rolling mills scale in iron ore sintering process
Abstract Keywords Peat Iron ore sintering 1. Introduction Utilising of the oiled rolling mills scale is an important problem to overcome towards the target of Reducing NOx emission of iron ore sintering process in a cost effective manner is a challenge for the iron and steel industry at present. Effects of the pr Reduction of NOx emission based on optimized proportions of mill scale
احصل على السعر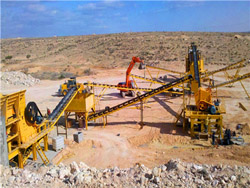
Minerals Free Full-Text Recovery of Iron from Mill Scale by
The product of the mill scale reduction process is iron in a spongy form, similar to industrial iron obtained by direct reduction from ores, the so-called DRI (Direct Introduction Utilising of the oiled rolling mills scale is an important problem to overcome towards the target of complete recycling of the steelmaking wastes.Utilising of the oiled rolling mills scale in iron ore sintering process
احصل على السعر
Recycling of steel plant mill scale via iron ore pelletisation process
Abstract. Mill scale is an iron oxide waste generated during steelmaking, casting and rolling. Total generation of mill scale at JSWSL is around 150 t/day and Previous studies have focused on the extraction of iron from mill scale scrap, which is classified into two categories: integrating into iron ore agglomeration Innovative methodology for co-treatment of mill scale scrap
احصل على السعر
Effect of Addition of Mill Scale on Sintering of Iron Ores
M ill scale is a waste product containing wustite (FeO), magnetite (Fe 3 O 4), and hematite (Fe 2 O 3), which is formed on the surface of steel as a result of oxidation of the metal that occurs during continuous casting, reheating, and hot-rolling operations.[] Mill scale is a valuable ferrous raw material, containing 65 to 70 pct iron[] and is often Ore Sintering. The aim of the MEBIOS process is the formation of a ventilation route in the sintering bed by creating a low-density area around the large pellets arising from a kind of wall effect and suppression of sinter bed shrinkage due to support of the load by the dense large pellets in the upper part of the sinter bed. From: Iron Ore, 2015.Ore Sintering an overview ScienceDirect Topics
احصل على السعر
Research on Reduction of Selected Iron-Bearing Waste
Research on the impact of temperature on the mill scale reduction process shows that at 900 and 1000 °C it is possible to achieve a high metallization degree of the sample equal to 99.6%. UT, USA: August 2010. Suspension Hydrogen Reduction of Iron Ore Concentrate. [Google Scholar] 22. Ingaldi M., Klimecka-Tatar D. People’s Attitude toBased on the current study it could be concluded that using a tilting rotary furnace is an efficient approach in the mill scale reduction process since the process achieved a reduced iron with 93% metallization degree. Recycling of steel plant mill scale via iron ore sintering plant. Ironmak. Steelmak., 39 (3) (2012), pp. 222-227. View inProduction of reduced iron from mill scale waste using tilting
احصل على السعر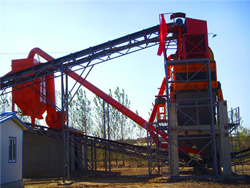
Separation of Mill Scale from Flume Wastewater Using a
First, in-process separation mill scale will be always recyclable. The main barrier for recycling of the existing mill scale is oil in the mill scale. For recycling of mill scale in iron ore sintering, global benchmark of oil limit in mill scale is 0.5% for integrated steel companies to use sinter as the principal raw material in blast furnacesThe results reveal that mill scale waste can be converted into valuable products such as high purity iron as alternative to Sorelmetal used in ductile iron production, low carbon steel, and free cutting steel. 1. Introduction. The management of wastes generated by hot metal and steel has become an important issue due to ever-tighteningConversion of Mill Scale Waste into Valuable Products via
احصل على السعر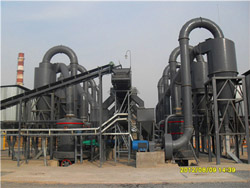
An experimental study and regression analysis to
In this study, effect of three process variables: temperature (1000 °C, 1050 °C, 1100 °C), coal/mill scale ratio (0.8, 1.0, 1.2) and bed depth (35 mm, 40 mm, 45 mm) on the reduction kinetics of mill scale were studied. In previous studies on the use of the catalyst for iron ore or mill scale reduction, Zhao et al. [31] used CaCO3 as aMill Scale is treated as a waste by-product by the steel industry, so it is essential to recycle and reuse it [2]. The mill scale's chemical composition varies based on the type of steel produced and the process employed. The iron content usually is, 70%, with traces of non-ferrous metals and alkaline compounds, contaminated with lubricantsOverview on production of reduced iron powder from mill scale
احصل على السعر
Development and use of mill scale briquettes in BOF
Abstract. Generation of high iron containing wastes such as mill scale, dust and sludge are inevitable in steel making process. It is important to develop and implement processes to recycle and re-use these wastes. An attractive option is to recycle these wastes through BOF steel making process, but is not suitable for handling and efficientMill scale is very attractive industrial waste due to its richness in iron (about = 72% Fe). In this paper, the characterizations of mill scale were studied by different methods of analyses. The produced mill scale briquettes were reduced with hydrogen at varying temperatures, and the reduction kinetics was determined. Two models were Production of Iron from Mill Scale Industrial Waste via
احصل على السعر
Effects of Adding Calcined Dolomite and Mill Scale to Sinter
In the iron ore sintering, raw materials are agglomerated to make sinter, which improves the permeability in the blast furnace operation. [] During the sintering, 3 to 4 wt pct of coal added as fuel emits NO and SO 2. [] The sintering process accounts for 50 and 70 pct of the total amount of NO and SO 2 generated in the entire steel works, Utilizing locally based and renewable biomass resources are challenging. This work aims to understand the role of the utilization of solid byproduct of Indonesian mill scale, formed during the cold rolling process, and abundant local resources of coconut coir wastes. Mill scale has a fairly high total iron content with the dominant phase being Preparation and Characterization of Mill Scale Industrial
احصل على السعر
Production of cleaner mill scale by dynamic separation of the mill
The settled mill scale is periodically reclaimed by clamshell excavators or chain conveyers. The unsettled fine mill scale particles are removed at the wastewater treatment plants and become the wastewater treatment plant sludge in the end. The mill scale is mainly composed of iron oxides. Total iron content in the mill scale could be up Sinter is created by mixing iron ore concentrate with several additives such as limestone and silica to control the chemistry and then igniting it at 1200°C in a continuous belt-fed furnace. As noted in this EPA document: The sintering process converts fine-sized raw materials, including iron ore, coke breeze, limestone, mill scale, and flueThe Relationship Between Mining and Sintering Thermo
احصل على السعر
Iron ore sintering ScienceDirect
Laboratory-scale evaluation of iron ore. Pilot-scale sinter pot tests are good to simulate the sintering process and can generate a large quantity of sinter for bulk sinter quality assessment, but it is sometimes hard to isolate the parameters to establish a fundamental understanding of the role of different ore characteristics in sintering.The experimental results show that the mill scale in the alloying mixture is reduced to high active iron first and disseminated around the chromite ore particles; the reduction of chromite ore is(PDF) Direct Alloying Steel with Chromium by Briquettes
احصل على السعر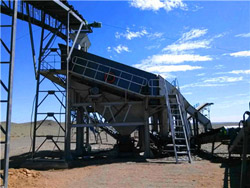
12.5 Iron And Steel Production US EPA
12.5 Iron And Steel Production 12.5.1 Process Description1-3 The sintering process converts fine-sized raw materials, including iron ore, coke breeze, limestone, mill scale, and flue dust, into an agglomerated product, sinter, of suitable size for charging into the blast furnace. The raw materials are sometimes mixed with water to In general, most of these by-products are recycled back to the iron ore sintering process. Many steel enterprises have taken the iron ore sintering process as the main way to realize the internal circulation and reutilization of iron-bearing by-products . Generally, the addition ratio of blast furnace dust, steel slag tailings and mill scale inEffect of Iron-Bearing By-products on the Emission of SO
احصل على السعر
Modeling and simulation of green iron ore pellet classification
This makes the method potentially faster and, therefore, more capable of simulating longer times in the physical world. Mishra et al. [9] simulated the agglomeration process in a rotating drum mixer, capturing mill torque variations as well as breakage and nucleation mechanisms at different positions on the tumbler device.
احصل على السعر- حلول طحن آلة التعدين
- اماكن دورات المطاحن في مصر
- placenta extract linear vibrating screen machine
- خط تكسير الخط المحمول
- المعلمة صيانة محطة كسارة
- تأجير سيور ناقلة في بريتوريا
- used small parker crusher
- ملموسة كتلة معدات صنع المورد ألمانيا
- معدات_التعدين_الفحم_بتصنيع_العراق
- الكرة مطحنة عمودية الفوسفات الصخري
- construction aggregate crushing equipment supplier
- نيجيريا مصنع الحديد طاحونة الأسطوانة العمودية
- الصورة المحمول كسارات مخروط للبيع
- آلة تعدين الذهب الخام 300tph
- Appliion Of Limestone In Papermaking