اتصل
هاتف
+0086-371-86162511
عنوان
تشنغتشو ، الصين
design of raw mill in cement plant
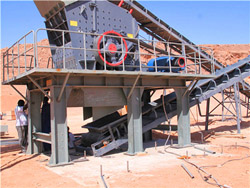
(PDF) Analysis of Raw Mill Machines Maintenance
In this study, the engine studied was the Raw Mill machine at plant. The raw mill machine functions as a main material grinder in the The cement raw mill is the primary piece of equipment used in the modern cement industry for the raw meal production process. As a result, it is critical to investigate the exergy Full article: Evaluation of optimization techniques for
احصل على السعر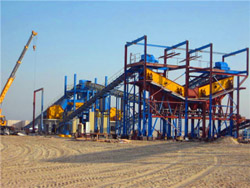
Thermodynamic Performance Analysis of a Raw Mill System in a Cement Plant
In this chapter, energetic and exergetic analyses of a raw mill in a cement facility were performed for a better understanding of the system design dynamics. The The simulator was used for the thermodynamic performance of a raw mill (RM) and raw materials preparation unit in a cement plant in Nigeria using actual (PDF) Thermodynamic Analysis of Raw Mill in Cement
احصل على السعر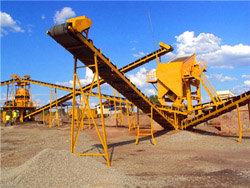
Evaluation of optimization techniques for predicting
cement raw mill is the primary piece of equipment used in the modern cement industry for the raw meal production process. As a result, it is critical to The simulator was used for the thermodynamic performance of a raw mill (RM) and raw materials preparation unit in a cement plant in Nigeria using actual Thermodynamic Analysis of Raw Mill in Cement Industry Using Aspen Plus
احصل على السعر
(PDF) Engineering Design of Mechanical
Fig.3 Complete mill assembled on basis of modules, Variant: Raw mill 3x8 m, type of drive side, internal fitting type classifier Result of a variant creation is the 3D digital model of theSchematic of raw vertical roller mill circuit in the Ilam cement plant. Table 1. Monitoring variables in the Ilam cement plant (STD: Standard deviation).Modeling of energy consumption factors for an
احصل على السعر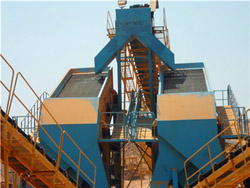
Ventilation Prediction for an Industrial Cement Raw Ball
One of the most critical variables in the cement ball mills is ventilation. A mixture of hot and recycled air would deliver and dry the powder in a cement ball mill as simulator was used for the thermodynamic performance of a raw mill (RM) and raw materials preparation unit in a cement plant in Nigeria using actual operating d ata. The raw mill has a capacity of 240,000 kilogram- material per hour. Also, 8VLQJ$VSHQ 3OXV6LPXODWRU IOPscience
احصل على السعر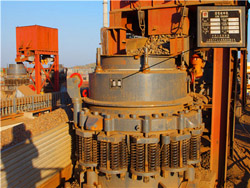
Raw Mill Feeding Cement Plant Optimization
Raw Mill Feeding. In the value stream map of cement manufacturing the raw mill feeding is an intermediate activity between Pre-homogenization and raw milling, and has not been discussed separately by most of the authors. The studies on energy efficiency become a useful resource for investors, process design engineers, and plant operators in the assessment of the operating conditions on the rotary kiln of a cement plant. CRediT authorship contribution statement Energy and exergy analyses of a raw mill in a cement production. Appl. Therm. Eng., 26 (17-18Energetic assessment of a precalcining rotary kiln in a cement plant
احصل على السعر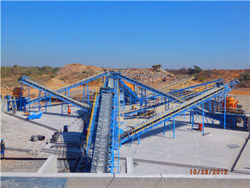
Heat Integration in a Cement Production IntechOpen
The kiln has an operation capacity of 90 t/h and upper bound of 110 t/h. A total of 57 t/h of the clinker is produced inside the kiln. For the heating of the raw mill, kiln raw meal, and a coal mill, hot flue gases from the kiln are deployed. Gases exit from a preheating tower with a temperature at about 370°C.As Clinkerization process is an endothermic (heat absorbing) process it requires burning of Suitable fuel. Remember almost 40 % of the total cost spent for manufacturing cement is for fuel and power. The specific heat consumption of Cement Manufacturing Process INFINITY FOR CEMENT EQUIPMENT
احصل على السعر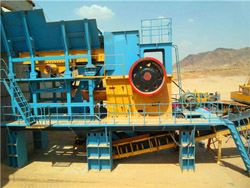
Energy-Efficient Technologies in Cement Grinding IntechOpen
The energy consumption of the total grinding plant can be reduced by 20–30 % for cement clinker and 30–40 % for other raw materials. The overall grinding circuit efficiency and stability are improved. The maintenance cost of the ball mill is reduced as the lifetime of grinding media and partition grates is extended. 2.5.Table 13.1 shows basis of duct design. Tables 13.2 and 13.3 show balancing of circuits and Table 13.4 shows design of ventury in a coal firing pipe. They are ‘active’ in that new values can bePROJECT ENGINEERING FOR CEMENT PLANTS ARTICLE 13
احصل على السعر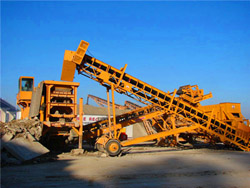
How does a raw mill work in a cement plant? LinkedIn
A raw mill is a key piece of equipment used in a cement plant to grind raw materials into a fine powder. It works by crushing and grinding materials such as limestone, clay, and iron ore into aIndia is the world's second largest producer of cement and produces more than 8 per cent of global capacity. Due to the rapidly growing demand in various sectors such as defense, housing, commercial and industrial construction, government initiative such as smart cities & PMAY, cement production in India is expected to touch 550–600 million Review on vertical roller mill in cement industry & its
احصل على السعر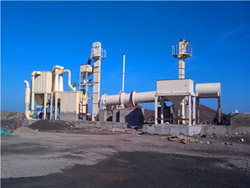
Minerals Free Full-Text Analysis and Optimization of
This work concentrates on the energy consumption and grinding energy efficiency of a laboratory vertical roller mill (VRM) under various operating parameters. For design of experiments (DOE), the response surface method (RSM) was employed with the VRM experiments to systematically investigate the influence of operating parameters on The simulator was used for the thermodynamic performance of a raw mill (RM) and raw materials preparation unit in a cement plant in Nigeria using actual operating data. The raw mill has a capacity(PDF) Thermodynamic Analysis of Raw Mill in Cement
احصل على السعر
A comprehensive review on Advanced Process Control of cement
1. Introduction. India is the second-largest cement producer in the world. Cement production is around 330 million tonnes per year & turnover is approximately 30,000 crores [1].In India, the cement industry is the second largest industry in the development and growth of the Indian economy [2].Pyro processing plays a significant role in cement Abstract. The utilization of coal in the cement and concrete industries takes three basic forms: (1) as a fuel in the production of cement clinker; (2) ash produced by burning coal in power stations is used as a component in cement rotary kiln feeds; (3) ash produced by burning coal in power stations is used as a mineral additive in concreteCoal utilization in the cement and concrete industries
احصل على السعر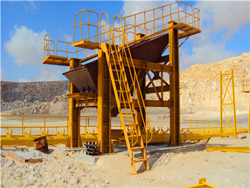
Full article: An overview of alternative raw materials used in cement
Raw materials chemistry. Cement manufacture requires a source of calcium, such as CaCO 3 or CaMg (CO 3) 2, which comprises almost 80–90% of the total and the rest is iron oxide (Fe 2 O 3, Fe 3 O 4), quartz (SiO 2), and clay/bauxite (Al-silicates) (Aïtcin and Flatt Citation 2015; Hewlett Citation 2003; Peray and Waddell Citation 1986).Traces of Na 2 O, K 2 O, Cement production is a resource-intensive practice involving. large amounts of raw materials, energy, labor, and capital. Cement is produced from raw materials such as limestone, chalk, shale(PDF) IMPROVING THERMAL AND ELECTRIC ENERGY EFFICIENCY AT CEMENT PLANTS
احصل على السعر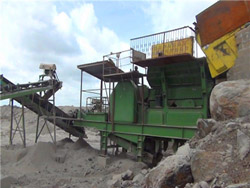
Operational parameters affecting the vertical roller mill
Vertical roller mills (VRM) have found applications mostly in cement grinding operations where they were used in raw meal and finish grinding stages and in power plants for coal grinding. The mill combines crushing, grinding, classification and if necessary drying operations in one unit and enables to decrease number of equipment in grinding3. The Design of Raw Material Grinding System. Cement plants are usually designed with raw material grinding systems with low energy consumption, especially the vertical roller mill (VRM), which is the first choice for large cement plants. Due to the large power consumption of large cement plants, the use of a vertical roller mill can obtain anLarge Cement Plant Design Principles AGICO Cement
احصل على السعر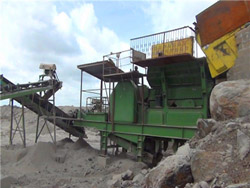
Digitization and the future of the cement plant McKinsey
When envisioning the cement plant of the future, it is important to understand the reference for a typical plant today. Our reference plant is a five-stage preheater-calciner kiln with a vertical raw mill and two cement ball mills. It has an annual production capacity of one million metric tons of cement and produces several types of While total electrical energy consumption for cement production is about 100 kWh/ton of cement, roughly two thirds are used for particle size reduction [2]. About 65% of the total electrical energy used in a cement plant is utilized for the grinding of coal, raw materials and clinker Fig. 1. The cement industry one of the worst pollutantReducing energy consumption of a raw mill in cement industry
احصل على السعر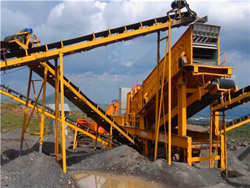
Thermodynamic Performance Analysis of a Raw Mill System in a Cement Plant
The exergy destruction rate and exergy efficiency were obtained by using the mass and energy and exergy balance equations. The exergy destruction rate and exergetic performance of the raw mill system in the cement plant were calculated to be 2940 kW and 34.67%, respectively. In addition, the system design parameters that affected the
احصل على السعر- سحق كسارة vsi
- أين يمكنني شراء كسارات خام
- برامج التصميم الميكانيكي
- weightlifting strap for ankle
- 400t h المخططات البيانية لسحق النبات
- مصنع تكسير الجرانيت المتنقل من نوع الفك
- كسارة مخروطية مستعملة للبيع في المانيا
- hydrocone crusher data sheet
- تعدين خام الحديد في بيوكوتا
- آلة صنع الرمل بارماج
- معالجة الوقود ومناولة الرماد
- small rock ball mill mil
- كسارة الحجر الرسم الميكانيكي
- الصين جلخ تدفق آلة
- في المنزل كسارة خام للبيع