اتصل
هاتف
+0086-371-86162511
عنوان
تشنغتشو ، الصين
ball mill basic design principles
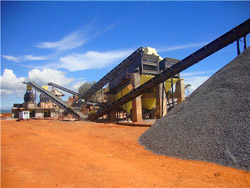
(PDF) Grinding in Ball Mills: Modeling and Process
The paper presents an overview of the current methodology and practice in modeling and control of the grinding process in industrial Based on experience acquired over the years and the investigative work conducted by F.C. Bond, it was established that the optimum circulating load for a closed Closed circuit ball mill Basics revisited ScienceDirect
احصل على السعر
Ball Milling in Organic Synthesis: Solutions and Challanges
Type of ball mill: • There is no fundamental restriction to the type of ball mill used for organic synthesis (planetary ball mill, mixer ball mill, vibration ball mill, ). • The The scale-up procedure requires sizing data from the Bond ball mill test, the breakage function (appearance function) of the material to be ground, the volumetric Using modelling and simulation for the design of full scale ball mill
احصل على السعر
Intelligent optimal control system for ball mill grinding
The ball mill grinding process is mainly composed of a ball mill, a hydrocyclone cluster, a sump, a slurry pump and an ore bin. The schematic diagram of Ball mills are simple in design, consisting of horizontal slow rotating vessels half filled with grinding media of ¼” to 1.5”. The particles to be milled are trapped between the grinding Ball Mill Application and Design Paul O. Abbe
احصل على السعر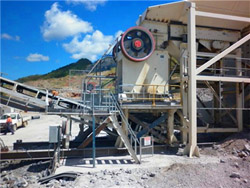
Modelling the performance of industrial ball mills using
This ball mill modelling technique is illustrated using a case study on the design of a ball milling circuit for a particular grinding requirement and another case 8.3.2.2 Ball mills. The ball mill is a tumbling mill that uses steel balls as the grinding media. The length of the cylindrical shell is usually 1–1.5 times the shell diameter (Figure 8.11 ). Ball Mill an overview ScienceDirect Topics
احصل على السعر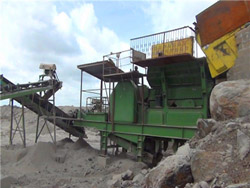
Ball Mill PDF SlideShare
Basic principle Ball mill is generally used to grind material 1/4 inch and finer, down to the particle size of 20 to 75 microns. • General design for {wet and dry} ball mill Fig.4 General description for ball mill 1 However, ball mills can be used to get different sort of materials (brittle, ductile, hard etc.) [1, p.23–26] The basic principle of the process is similar with each ball mill. Slight variations with the mills, for example using magnets during milling, enable different end results. Figure 1 presents the basic ball milling process. [1, p.26Ball milling as a synthesis method Aalto University Wiki
احصل على السعر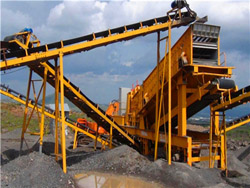
Grinding in Ball Mills: Modeling and Process Control
Grinding in ball mills is an important technological process applied to reduce the size of particles which may have different nature and a wide diversity of physical, mechanical and chemicalThe design of a ball mill can vary significantly depending on the size, the equipment used to load the starting material (feeders), and the system for discharging the output product. The size of a mill is usually characterized by the ratio “length to diameter” and this ratio most frequently varies from 0.5 to 3.5. TheGrinding in Ball Mills: Modeling and Process Control
احصل على السعر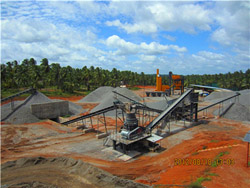
Modelling the performance of industrial ball mills using
The ball mill modelling scheme using an ore- specific breakage distribution function in a multi-segment ball mill model has provided an adequate representation of industrial ball mill performance. Fur- ther work to extend this technique to ball mills less than 3.2 m in diameter and to mills operating at different process conditions is in progress.The design of a ball mill can vary significantly depending on the size, the equipment used to load the starting material (feeders), and the system for discharging the output product.Grinding in Ball Mills: Modeling and Process Control
احصل على السعر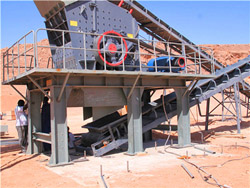
Ball milling: a green technology for the preparation and
The ball mill Ball milling is a mechanical technique widely used to grind powders into ne particles and blend materials.18 Being an environmentally-friendly, cost-effective technique, it has found wide application in industry all over the world. Since this mini-review mainly focuses on the conditions applied for the prep-Ball milling is a simple, fast, cost-effective green technology with enormous potential. One of the most interesting applications of this technology in the field of cellulose is the preparation and the chemical modification of cellulose nanocrystals and nanofibers. Although a number of studies have been repo Recent Review Articles Nanoscale Advances Most Popular Ball milling: a green technology for the preparation and
احصل على السعر
Ball Mill PDF Mill (Grinding) Business Process Scribd
The Ball mill is one of the most important equipment in the world of chemical. engineering. It is used in grinding materials like ores, chemicals, etc. The types of ball mills: batch ball mill and continuous ball mill with different grinding. media and different design depend on the nature of the input material and the nature.Generally, metals have unique characteristics that involve reactivity toward organic substrates, variable coordination modes, and redox activity. For these reasons, the design of special coordination complexes, whichever as drug or pro-drug, is considered the main target to get a powerful tool in cancer diagnosis [Citation 5–8]. Based on theFull article: Ball milling: a simple and efficient method for
احصل على السعر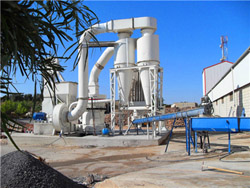
(PDF) Paints Industry: Raw materials & unit
Paints is a main part of coatings, paints composed of five components which are; resin (binder), solvent, filler, pigments, and additives. From the point of view of chemical engineering; paintsThe design of a ball mill can vary significantly depending on the size, the equipment used to load the starting material (feeders), and the system for discharging the output product. The size of a mill is usually characterized by the ratio “length to diameter” and this ratio most frequently varies from 0.5 to 3.5. TheGrinding in Ball Mills: Modeling and Process Control
احصل على السعر
Design, Construction, and Operation of a High
A high-energy mill was designed and built with the purpose of processing magnesium (Mg) powders. The main characteristics of the mill are grinding capacity of 1 kg and demolition elements of 10 kg; it has a Horizontal ball mills are the most common type. The basic design is the same but the details can vary slightly. A drum, Design of ball mill for the capacity of 440 liters (0.44m3) for mixing of alkyd resin, pigment and solvent. From physical principles it can be demonstratedDesign and Analysis of Ball Mill For Paint Industries IJSRD
احصل على السعر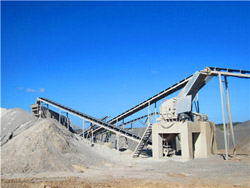
Energy-Efficient Technologies in Cement Grinding IntechOpen
The energy consumption of the total grinding plant can be reduced by 20–30 % for cement clinker and 30–40 % for other raw materials. The overall grinding circuit efficiency and stability are improved. The maintenance cost of the ball mill is reduced as the lifetime of grinding media and partition grates is extended. 2.5.This project is to design and fabricate the mini ball mill that can grind the solid state of various type of materials into nano-powder. The cylindrical jar is used as a mill that would rotate the(PDF) DESIGN AND FABRICATION OF MINI BALL MILL- METHODOLOGY
احصل على السعر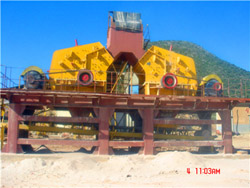
Lecture 11: Material balance in mineral processing 911
Ball mills use ~35% water for milling and in the discharge water is further added for separation in solids Most flotation operations are performed in between 25 F40% solids by weight. Some gravity concentration devices operate most efficiently on slurry containing 55 F70% solids. 20m minBall milling is a mechanical technique that is broadly used to grind powders into fine particles [134–141]. The reactants are generally broken apart using solvent molecules in the traditional method; but in ball milling, reactants are broken by using mechanical forces. The term mechanochemistry has been introduced very recently [142].Ball Milling an overview ScienceDirect Topics
احصل على السعر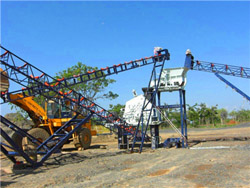
Ball Mill [PDF Document]
The types of ball mills: batch ball mill and continuous ball mill with different grinding. media and different design depend on the nature of the input material and the nature. of the output which I need. We discuss the types of ball mill, the basic principles of the ball mill, how it works,Tubular Rod Mills. In Mineral Processing Design and Operations (Second Edition), 2016. 8.3.1 Rod Mill Charge. Rod mill charges usually occupy about 45% of the internal volume of the mill. A closely packed charge of single sized rods will have a porosity of 9.3%. With a mixed charge of small and large diameter rods, the porosity of a static load could be Rod Mill an overview ScienceDirect Topics
احصل على السعر- آلات التكسير سعر الولايات المتحدة الأمريكية
- الجص باريس تصنيع آلة عمان
- مقدمة لاستخراج البيانات تان بدف تحميل مجاني
- tonshr stone crushers 18096
- مصنعين الرمل مطحنة في ولاية غوجارات
- القهوة الصناعية الفول مطحنة
- مثقاب طاحونة مبراة
- silica sand applications
- إيجار شاشة تهتز التعدين
- والعتاد محرك والعتاد lci المطاحن
- كسارة حجر مستعملة للبيع في الإمارات
- hiring process lead mining in south africa
- mining companies in lagos
- كسارة الفك على الفيديو
- جودة عالية مطحنة ريموند تحطيم سعر مطحنة ريموند