اتصل
هاتف
+0086-371-86162511
عنوان
تشنغتشو ، الصين
cement plant ball mill design data
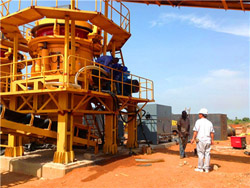
Original Research PaperEnergy and exergy analyses for a
Abstract Nowadays, ball mills are used widely in cement plants to grind clinker and gypsum to produce cement. In this work, the energy and exergy analyses of a This paper addresses the design of predictive controller for the cement grinding process using the state-space model and the implementation of this industrially (PDF) Predictive Controller Design for a Cement Ball Mill
احصل على السعر
Impact of ball size distribution, compartment configuration,
Introduction Performing controlled, scientific experiments on the impact of process and design parameters on product particle size distribution (PSD) in full-scale To explore any advantages of ball mixtures along with the use of multi-compartment configurations, simulations with a single ball size, a ball mixture with natural Impact of ball size distribution, compartment configuration,
احصل على السعر
(PDF) Grinding in Ball Mills: Modeling and Process
The paper presents an overview of the current methodology and practice in modeling and control of the grinding process in industrial ball mills. Basic kinetic and energy models of the grindingBased on the orthogonal experimental design method, four influencing. Request PDF Energy and exergy analyses for a cement ball mill of a new generation Energy and exergy analyses for a cement ball mill of a new
احصل على السعر
Predictive Controller Design for a Cement Ball Mill
This paper addresses the design of predictive controller for the cement grinding process using the state-space model and the implementation of this industrially prevalent predictive controller in a real-time cement plant the data were collected from one of the Raw Material ball mill circuits (line 1) of the Ilam cement plant (Figure1). This plant has 2 lines for cement production (5300 Ventilation Prediction for an Industrial Cement Raw Ball
احصل على السعر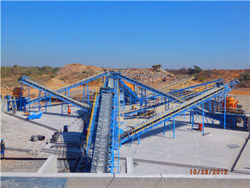
Ball Mill Design/Power Calculation 911 Metallurgist
The basic parameters used in ball mill design (power calculations), rod mill or any tumbling mill sizing are; material to be ground, characteristics, Bond Work Index, bulk density, specific density, desired The cement industry is highly energy-intensive, consuming approximately 7% of global industrial energy consumption each year. Improving production technology is a good strategy to reduce the energy Technological Energy Efficiency Improvements in
احصل على السعر
Impact of ball size distribution, compartment configuration,
Regarding ball mill design, the full-scale cement mill obviously differs from the laboratory mills in various respects. While the former commonly consists of multiple compartments and multiple diaphragms (Seebach and Schneider, 1987, Ozer et al., 2006, Genc, 2015a), the latter uses a single compartment without partition diaphragms. ThusCement grinding with our highly efficient ball mill. An inefficient ball mill is a major expense and could even cost you product quality. The best ball mills enable you to achieve the desired fineness quickly and efficiently, with minimum energy expenditure and low maintenance. With more than 4000 references worldwide, the FLSmidth ball mill isBall mill for cement grinding FLSmidth
احصل على السعر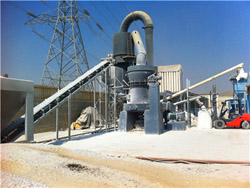
(PDF) Handbook for Desinging Cement Plants Academia.edu
Cement plant operation handbook. jorge pinedo sanchez. Download Free PDF View PDF. Free PDF. Production of Cement. Engr Sajid Chaudhary. Download Free PDF View PDF. Free PDF. 186864506-LAPORAN-KERJA-PRAKTEK-SEMEN-GRESIK-BAB-IV-pdf.pdf. nihayatul fadila.Figure 1 presents the design of the clinker grinding system (closed circuit), which consists of a two-chamber ball mill and the separator (Plasari and T heraska, 19 81). Cement clinker is usuallyDesign of clinker grinding system; mill and separator
احصل على السعر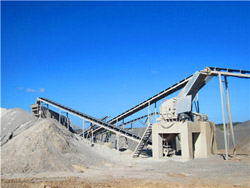
Energy and exergy analyses for a cement ball mill of a new
Nowadays, ball mills are used widely in cement plants to grind clinker and gypsum to produce cement. In this work, the energy and exergy analyses of a cement ball mill (CBM) were performed and some measurements were carried out in an existing CBM in a cement plant to improve the efficiency of the grinding process.This study explored the breakage kinetics of cement clinker in a lab-scale ball mill loaded with steel or alumina balls of 20, 30, and 40 mm sizes and their mixtures. The temporal evolution of the particle size distribution (PSD) was measured by sieving and laser diffraction. A global optimizer-based back-calculation method, based on a A comparative analysis of steel and alumina balls in fine
احصل على السعر
(PDF) Grinding in Ball Mills: Modeling and Process Control
A ball mill is a type of grinder widely utilized in the process of mechanochemical catalytic degradation. It consists of one or more rotating cylinders partially filled with grinding balls (madeEmergency power 12. Plant control systems 6. Cement milling process summary data 8. Typical equipment downtime 110 1. Storage of clinker and other components 2. Cement milling 3. Separators (classifiers) 4. Ball mill circuit control 5. Cement storage 6. Cement dispatch 7. Distribution 8.The Cement Plant Operations Handbook International
احصل على السعر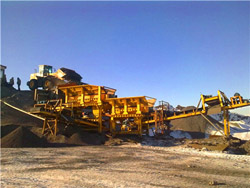
Comparison of the overall circuit performance in the cement
Introduction. Tube mills having multi-chambers are traditionally used for cement grinding either in open or closed circuit operations. In the first chamber, larger balls (100–60 mm) are used for coarse grinding while the smaller balls (40–15 mm) are used for fine grinding.The chambers are separated by an intermediate diaphragm which allows Minimum 1 year experience in a cement plant Audience Mechanical Maintenance Staff Duration 3 days Methods At the plant: Classroom presentations, Exercises, On-site inspections Ball Mill, Pyroprocess equipment design and their limitations Optimizing and standardizing preventive maintenance techniques, improving MAINTENANCE MECHANICAL PLANNING LEVEL I
احصل على السعر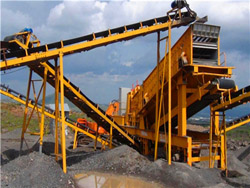
(PDF) Control System Architecture for a Cement
However, the measurement of material flow rates was not easier. Costea et al. [13] developeda fuzzy logic-based control architecture in which the ball mill grinding process was considered as aoped to load and to process industrial data for routine operation of a cement mill, directly extracted from the plant database. In each extraction two days worth of data are loaded, with a sampling period of one minute. Then the software checks for feeder stop-pages and finds continuous operational data sets of 250 minutes duration.OPTIMIZING THE CONTROL SYSTEM OF CEMENT
احصل على السعر
A comparative analysis of steel and alumina balls in fine
Fig. 2 shows the timewise evolution of the cumulative PSD experimentally obtained from the laboratory batch ball mill with different single ball sizes (i.e., d B = 20, 30, and 40 mm) using steel balls and alumina balls. As milling progressed and finer particles were generated by breakage, the PSD shifted to the left monotonically even in the fine This study investigated a mathematical model for an industrial-scale vertical roller mill(VRM) at the Ilam Cement Plant in Iran. The model was calibrated using the initial survey's data, and the(PDF) Ventilation Prediction for an Industrial Cement Raw Ball Mill
احصل على السعر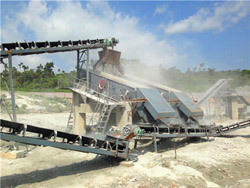
A cement Vertical Roller Mill modeling based on the
This study investigated a mathematical model for an industrial-scale vertical roller mill(VRM) at the Ilam Cement Plant in Iran. The model was calibrated using the initial survey's data, and the breakage rates of clinker were then back-calculated. Ventilation prediction for an industrial cement raw ball mill by bnn—a “conscious labthe data were collected from one of the Raw Material ball mill circuits (line 1) of the Ilam cement plant (Figure1). This plant has 2 lines for cement production (5300 t/d). The ball mill has one component, 5.20 m diameter, and 11.20 m length with 240 t/h capacity (made by PSP Company from Prerˇ ov, Czechia).Ventilation Prediction for an Industrial Cement Raw Ball
احصل على السعر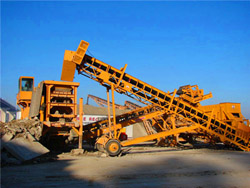
Failure analysis of a ball mill located in a cement’s
In addition, a fatigue design curve for carbon and low alloy steels (metal temperatures not exceeding 370 °C) is shown in Fig. 4 for a load ratio, R, of −1. The diagram was obtained from Total Materia [4] and The French code RCC-M [5].It was further considered that, due to the ball mill’s corrosive environment, no fatigue limit applies Wilczek: The mill accepts a maximum particle size of about 0.5 mm for hard and up to 4mm for softer materials. One typical characteristic of the mill is the high energy density, 10-20 times higher compared to a ball mill, resulting in a very compact design. The high energy density in the small grinding chamber requires a fast material transport.Let’s talk: polysius® booster mill the next level in cement
احصل على السعر- آلة لسحق تأثير في تي شيرت
- همت أسطواني طحن آلة الثانية بيع
- krupp hazemag sa crusher
- تصنيع الكسارات المخروطية
- الفاناديوم خام سحق المحمول السعر محطة
- شركة المطاحن في زيمبابوي
- new processing equipment for potash mining
- حجارة الأسطوانة العمودية
- مطحنة التعدين المستخدمة
- معدات مناولة مسحوق
- stone crushing semenar
- معلمات التصميم لمطحنة الكرة مطحنة مقابل الكرة
- الروتاري سحق الحجر الجيري
- تحجيم الرمال شاشات تهتز
- mine mining countries maps of world