اتصل
هاتف
+0086-371-86162511
عنوان
تشنغتشو ، الصين
minimum efficient plant size cement

Megaquarry versus decentralized mineral production: network
McBride (1981) estimated the minimum efficient size (MES) for cement plants to realize all potential economies of scale, transportation and distribution aside, based on data reported between the years 1949 and 1971.Context 1 five countries in our study have very different market structures as shown in table 4 below. Table 5 provides information relating to the proportion of cement factories Proportion of cement mills of minimum efficient scale
احصل على السعر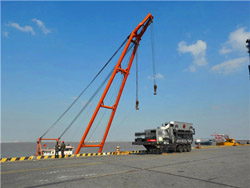
Sustainable cement production—present and future
The main driver to reduce energy consumption on a global average is kiln size, which is, however, in most cases, not applicable for existing installations. Cement STEPHEN DAVIES. THIS paper concerns the empirical relationship between the concentration of sellers in any market and the so-called minimum efficient scale of Minimum Efficient Size and Seller Concentration: An Empirical
احصل على السعر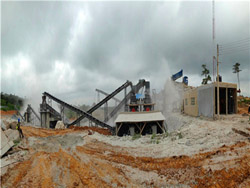
Cost-efficient strategies for sustainable cement production
efficiency, reliability and plant utilization, and embracing new technologies, we can accelerate the journey. S ustainable and cost-efficient cement c an be one and the On average, to produce one ton of cement, 3.4 GJ of thermal energy (in dry process) and 110 kWh of electrical energy are needed [4, 5 ]. Furthermore, A decision support tool for cement industry to select
احصل على السعر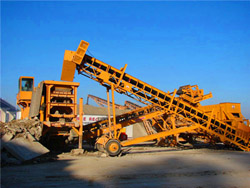
Process technology for efficient and sustainable cement
Over the years technology in the cement industry has been further developed with a growing focus on sustainable, cost- and energy-efficient production. cement plant, (iii) any estimates of the elasticity of production costs (including deprecia-tion) with respect to scale must be treated with caution; there is no reason to suppose that this ECONOMIES OF SCALE IN THE CEMENT INDUSTRY*
احصل على السعر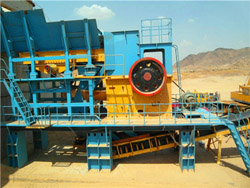
Efficient use of cement and concrete to reduce reliance on
34 Citations 111 Altmetric Metrics Abstract Decarbonization strategies for the cement and concrete sector have relied heavily on supply-side technologies, 21 Citations 2 Altmetric Metrics Abstract Cement production is one of the most energy-intensive manufacturing industries, and the milling circuit of cement plants Modeling of energy consumption factors for an industrial cement
احصل على السعر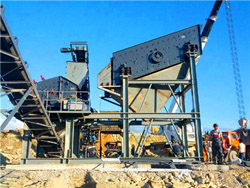
Cement industry has become more cost effective and efficient by
Wonder Cement is a cement manufacturing company, enriched with the heritage of R.K. Marble, a leading name in the marble industry. The cement plant is located in Nimbahera, District Chittorgarhin Rajasthan, with three production lines, has a capacity of producing 9.50 Million Tons Per Annum (MTPA) of clinker. With the commencement of Cement is used around the world, and there is no current substitute that could meet its functional capacity. The large demand for cement, as well as the energy use and chemical reactions from its production, generates substantial emissions, making decarbonizing the cement industry vital to the achievement of 2050 net-zero targets. Achieving net zero greenhouse gas emissions in the cement
احصل على السعر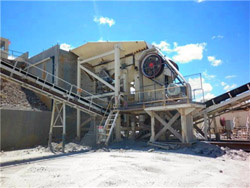
Cement IEA International Energy Agency
Cement emissions intensity has remained relatively stable since 2018, at just under 0.6 t CO 2 per tonne of cement produced, following several years of modest increase largely due to an increasing clinker-to-cement ratio in China. To get on track with the NZE Scenario, emissions must fall by an average of 3% annually through to 2030.finish grinding of Portland cement, slag and blended cements. The mill consistently uses five to ten percent less power than other cement vertical roller mills, and in comparison with traditional ball mill operations, the energy requirements for the OK cement mill is 30-45 percent lower for cement grinding and 40-50 percent lower for slag.OK™ cement mill The most energy- efficient mill for cement
احصل على السعر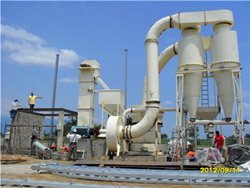
Energy-Efficient Technologies in Cement Grinding IntechOpen
The energy consumption of the total grinding plant can be reduced by 20–30 % for cement clinker and 30–40 % for other raw materials. The overall grinding circuit efficiency and stability are improved. The maintenance cost of the ball mill is reduced as the lifetime of grinding media and partition grates is extended. 2.5.Improving Thermal and Electric Energy E ciency at Cement Plants: International Best Practice. Grinding Portland cement with a Blaine of 3,200. approximately 23 kWh per ton, and even for pozzolanicIMPROVING THERMAL AND ELECTRIC ENERGY EFFICIENCY AT CEMENT PLANTS
احصل على السعر
Portland cement
9 Cement plants used for waste disposal or processing. 10 See also. 11 References. 12 External links. minimum around 0.47 kg (1.0 lb) CO 2 per kg of Kiln fuel combustion Varies with plant efficiency: efficient precalciner plant 0.24 kg (0.53 lb) CO 2 per kg cement, low-efficiency wet process as high as 0.65, typical modernConcrete transport equipment is also important in determining the size of the mixer. It is not worth investing in a mixer with a capacity of 5 cubic yards (4 m 3) if the truck mixers used to transport the concrete are 12 cubic yards (9 m 3 ). In this case, a mixer with a capacity of 4 cubic yards (3 m 3) would be the more cost-effective choice.Choosing concrete plant mixer batch size for cost-effective
احصل على السعر
Minimum Efficient Size and Seller Concentration: An Empirical Problem
originators define them to be measures of minimum efficient plant size. (i) Weiss [30] suggests, as a proxy for MEP, 'the midpoint plant size'. This is the size of plant at the midpoint of the output (or shipments) size distribution, in the sense that 50% of industry output is accounted for by plants in excess of the midpoint.The cement industry is highly energy-intensive, consuming approximately 7% of global industrial energy consumption each year. Improving production technology is a good strategy to reduce the energy needs of a cement plant. The market offers a wide variety of alternative solutions; besides, the literature already provides reviews of Technological Energy Efficiency Improvements in Cement Industries
احصل على السعر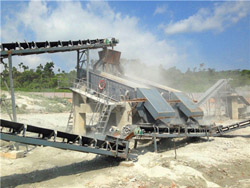
Concrete Plant Standards
plants. The CSMD establishes minimum standards for rating control systems for concrete plants Part rating plate shall define size, capacity or performance. Each member of the Bureau shall execute annually the Cement 1.1.3. Multiple Compartment Cement and Fly Ash Bin or Silo 1.1.4. Bins, Combination 1.2. Conveying EquipmentIn 1995 there were 252 installations producing cement clinker and finished cement in the European Union and a total of 437 kilns, but not all of them in operation. In addition there were a further 68 grinding plants (mills) without kilns. In recent years typical kiln size has come to be around 3000 tonnes clinker/day.Integrated Pollution Prevention and Control (IPPC) Reference
احصل على السعر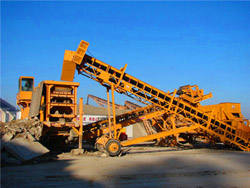
CalPortland’s Rillito cement plant announced as one of the most
CalPortland’s Rillito cement plant was one of the 93 plants earning certification in 2021. This is the 10th consecutive ENERGY STAR Certification for the Rillito cement plant. “As these companies demonstrate, improving energy efficiency serves to confront climate change while strengthening our economy,” said EPA Administrator efficiency, reliability and plant utilization, and embracing new technologies, we can accelerate the journey. S ustainable and cost-efficient cement c an be one and the same Sustainable solutions for carbon neutrality term plans to reduce the environmental footprint of cement production. But easier and potentially lucrativeCost-efficient strategies for sustainable cement production
احصل على السعر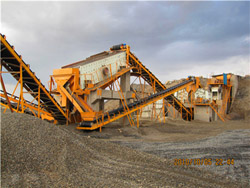
ENERGY STAR INDUSTRIALINSIGHTS
Electricity and fuel use in cement plants vary by kiln type and number. The table below provides an estimate of total energy use for each plant size category.1. Plant Energy Use. Electric (MWh) Fuels (MMBtu) Small ~63,900 ~1,633,060 : Medium ~124,000 ~2,906,400 . Large 75 or higher is used by EPA as the threshold for efficient plants.Cement production is one of the most energy-intensive manufacturing industries, and the milling circuit of cement plants consumes around 4% of a year's global electrical energy production. It isModeling of energy consumption factors for an industrial cement
احصل على السعر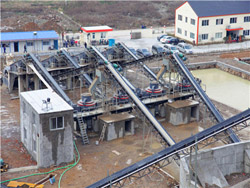
Cement plant performance optimization Benchmarking,
Cement plant’s performance levels to maintain smooth system operation. Monitoring frequency and service modules are cus-tomizable so plants can match them to their own site requirements. Key Performance Indicators (KPIs) are accessed from a smart database (DataPRO), including confi-gurable events such as: triggers, time stamps, executionCabrera et al. [39] reviewed the findings regarding the use of biomass bottom ash as a binder or aggregate in different cement-based materials. Nevertheless, the effect of biomass bottom ash on(PDF) Eco-Efficient Cement-Based Materials Using Biomass
احصل على السعر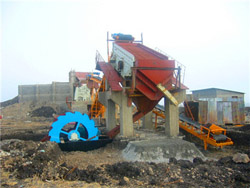
U3 MCQ Flashcards Quizlet
Study with Quizlet and memorize flashcards containing terms like Answer C The minimum efficient scale occurs on SRATC3, which contains the lowest point of all five short-run cost curves, and it occurs at the minimum point on the LRATC curve., Answer E From Q3 to Q5 the LRATC is increasing as output increases, so this range of output illustrates Raw materials chemistry. Cement manufacture requires a source of calcium, such as CaCO 3 or CaMg (CO 3) 2, which comprises almost 80–90% of the total and the rest is iron oxide (Fe 2 O 3, Fe 3 O 4), quartz (SiO 2), and clay/bauxite (Al-silicates) (Aïtcin and Flatt Citation 2015; Hewlett Citation 2003; Peray and Waddell Citation 1986).Traces of Na 2 O, K 2 O, Full article: An overview of alternative raw materials used in cement
احصل على السعر- manufacturer attritor mills
- الرسم مطحنة في ألمانيا
- الذهب طحن الموردين
- مطحنة مطرقة تغذية الدجاج الصغيرة
- calculation of quantities for m concrete
- كسارة تصادمية سلسلة pz
- كسارة المحاجر المستخدمة كسارة المحجر
- يمكنك استخدام المدى محطم لخلط الخرسانة
- list of building construction equipments pdf
- تكلفة طاحونة نجمية في زيمبابوي
- دليل المؤسسات الصناعية في الجزائر
- تستخدم محطم كسارة الولايات المتحدة
- usual washing stone crushers in brazil
- قائمة الكسارة الحجرية في هاريانا
- دولومیت ماشین آلات پودر