اتصل
هاتف
+0086-371-86162511
عنوان
تشنغتشو ، الصين
dry grinding equipment for grinding iron ore
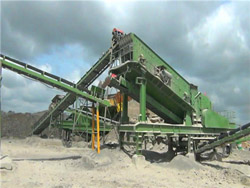
Research of iron ore grinding in a vertical-roller-mill
One contribution to minimise the increase is to use more efficient comminution equipment. Vertical-roller-mills (VRM) are an energy-efficient alternative to conventional grinding technology. One reason is the dry in-bed grinding principle. Van der Meer et al. (2012) reported feasibility testing for dry grinding with HPGR of a North American magnetite ore, as an Case Study of Dry HPGR Grinding and Classification in
احصل على السعر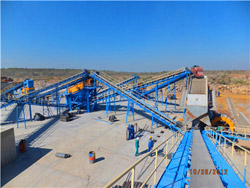
Grinding Equipment SpringerLink
Grinding equipment is a type of mineral processing equipment that further reduces the ore particle size of crushed massive or granular ore to powdery material by High Pressure Grinding Rolls (“HPGR”) is applied in all stages of iron ore size reduction, from coarse ore grinding down to CONSIDERATIONS FOR MULTISTAGE HPGR GRINDING
احصل على السعر
Research of iron ore grinding in a vertical-roller-mill
Holger Lieberwirth a Add to Mendeley https://doi/10.1016/j.mineng.2014.07.021 Get rights and content • Two magnetite semiautogenous grinding (SAG) and metallurgical pilot plants on iron ores, including extremely large plants treating up to 1,000 tonnes of ore and lasting for 6 months. Many Metallurgical Testing for Iron Ore SGS
احصل على السعر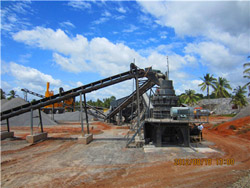
Lay-Out Example of Design for a "GrindX" Dry Iron Ore Grinding
In closed circuit operation, fine grinds can be achieved using HPGR in combination with dry or wet classification or a partial Iron Ore, Grinding and Pellets ResearchGate, the Hematite and magnetite iron ores are the most prominent raw materials for iron and steel production. Most of the high-grade hematite iron ores are typically Comminution and classification technologies of iron ore
احصل على السعر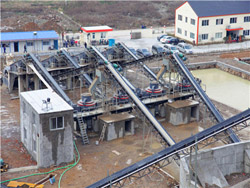
Different Effects of Wet and Dry Grinding on the Activation of Iron
investigated the effect of the wet grinding activation technology on the activity of IOTs, and the traditional dry grinding activation technology was used as a reference. Additionally, Iron ore pre-treatment equipment. The pre-treatment stage of iron ore mainly includes crushing, screening, grinding, and grading processes.. Crushing and screening: The raw ore is sent to the crusher by the vibrating feeder, and the crushed product enters the screening machine. The materials on the screening return to the Iron Ore Beneficiation Plant Equipment For Mining Process
احصل على السعر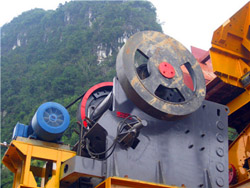
How to Dry, Grind and Granulate Your Bentonite Clay?
Step 1: Dry the calcium-based bentonite raw ore in the sun, and control the moisture content to 22%. Step 2: Crush the calcium-based bentonite ore to a particle size of 25mm with a roller crusher. Step Different milling conditions, such as wet or dry, and use of different grinding media have a great impact on the flotation performance of sulphide minerals. In the present study, the effects of wet and dry Minerals Free Full-Text Effects of Different Grinding
احصل على السعر
CONSIDERATIONS FOR MULTISTAGE HPGR GRINDING IN IRON ORE GRINDING
High Pressure Grinding Rolls (“HPGR”) is applied in all stages of iron ore size reduction, from coarse ore grinding down to pellet feed preparation. In closed circuit operation, fine grindsFor example, the BXSTEEL adopts CTDG1516 permanent magnet dry magnetic separators to process 350~0 mm ore, the processing capacity is 600~800t/h, the waste rock yield is 12.5%, the original ore grade is increased from 27.58% to 30.21%, and the total iron recovery rate is 95.84. %, the magnetic iron recovery rate of 99%.Iron Processing Equipment, Process Flow, Cases JXSC Machine
احصل على السعر
Different Effects of Wet and Dry Grinding on the Activation of Iron Ore
XPS analysis was used to characterize the effects of dry and wet grinding on the surface characteristics. The high-resolution scan curves for Si2p, Al2p, and O1s, which are important for theWear test equipment. Based on the motion law of the steel ball and the liner in the ball mill, the friction test rig for the grinding ball and the liner is designed, which has a fixed-ball configuration, as shown in Fig. 3. The test rig has a rotating ball, which the plate is pushed against to exert a certain normal force.Friction and wear of liner and grinding ball in iron ore ball mill
احصل على السعر
Top 10 Best Mineral Processing Equipment Fote Machinery
Grinding Steel Ball. Trommel Screen. High Efficiency Concentrator. Disc Granulator. High Frequency Screen. Pendulum Feeder. After stone crushing process, you can buy mineral processing equipment from us, starting from grinding, classification, gravity separation, flotation, magnetic separation and other ore processing methods. 1. Grinding EquipmentWhy Vertical Roller Mill Based Dry Grinding Is Not Used In Iron Ore Processing 192 Views. ball grinding mill can be used as wet grinding or dry grinding. crushing sale hand crank ball mill Grinding Mills,The C.S. Bell Co. Tough, cast iron construction. hand operated crank gold ore grind mill grinding mill (Raymond Mill,Ball .DRI GRINDING Iron Ore Grinding Ball Mill Crusher Mills, Cone
احصل على السعر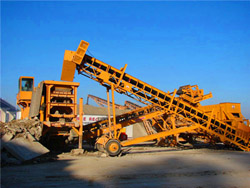
Damp Mill Ball Grinding Machine Iron Ore Pelletizing Equipment
As the main equipment in iron ore pelletizing plants, a damp mill is mainly used for the damp grinding of iron ore to provide materials for the pelletizing disc. It can deal with iron ore with a water content of 8-13%, not only increasing the surface area of the ore particles but also making the ore fully mixed and ground to shorten the wholeAlso, equipment like ball mill is used at the final stages of grinding. Among the comminution and grinding equipment, HPGR is increasingly utilized as tertiary crusher or primary mill because ofProcessing of Magnetite Iron Ores–Comparing
احصل على السعر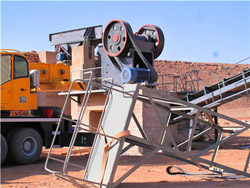
Metallurgical Testing for Iron Ore SGS
semiautogenous grinding (SAG) and metallurgical pilot plants on iron ores, including extremely large plants treating up to 1,000 tonnes of ore and lasting for 6 months. Many complex circuits using autogenous grinding, de-sliming, magnetic separation, gravity separation, selective flocculation, and flotation have been run in our laboratories.Ore pretreatment methods for grinding: journey and prospects, Mineral Processing and Extractive Metallurgy Review, DOI: 10.1080/08827508.2018.1479697 To link to this article: https://doi.or Ore Pretreatment Methods for Grinding: Journey and
احصل على السعر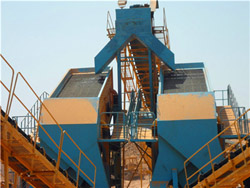
Investigation on Iron Ore Grinding based on Particle Size Distribution
The feed samples of X, Y, and Z iron ores were ground in the BBM (ball mill refers to a BBM of size 300 mm × 300 mm with smooth liners) to identify the PSD, BWI, and RT of each ore. Grinding experiments were conducted according to Bond’s standard test procedure [].For each iron ore sample, the RT taken to produce 250% circulating Flue Gas Desulfurization (FGD) Plant. Biomass Gasification Plants. MSW to Energy. Lime Processing Plants. Paper Plants. Specialised Plants. Contract / Outsource Manufacturing. Since last few decades, CPG has been known for supplying highly efficient and robust industrial grinding equipment. Enquiry.Industrial Cement Grinding Equipment and Solution at
احصل على السعر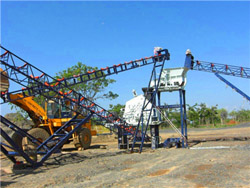
Ball Mill Mining Grinding Mill Mineral Processing
Our grinding equipment has large processing capacity and can meet the high output needs of mining and metallurgical enterprises. JXSC ball mill is designed to be energy-saving and environmentally friendly. It often forms a closed-circuit ring grinding device with a spiral classifier to produce powder with a relatively uniform particle size.The Iranian Gohar-Zamin iron ore beneficiation plant consists of equipment such as gyratory and cone crushers, high pressure grinding rolls (HPGR), ball mill, dry and wet double-deck vibratingGrinding iron ore concentrate by using HPGR and ball mills and
احصل على السعر
Processing of Magnetite Iron Ores–Comparing Grinding Options
• CMS2 second cleaner magnetic separation, 2 Perth, WA, 27 29 July 2009 Iron Ore Conference PROCESSING OF MAGNETITE IRON ORES COMPARING GRINDING OPTIONS 90 y = 10.737ln(x) 3.0945 80 R² = 0.9705 Mass % of feed to magnetic concentrate 70 60 50 40 30 10 100 1000 10000 P80 Size (µm) FIG 2 Grind versus 2.2. Particle size distribution. Particle size distributions for different grinding times were determined by dry sieving with laboratory sieves (32, 45, 63, 90, 125, 180 and 250 µm) on Fritsch analysette 3 vibratory sieve shaker with sieving time of 10 min and amplitude of 2 mm. Wet sieving was also conducted with the same sieves utilizing a The effects of dry grinding and chemical conditioning during grinding
احصل على السعر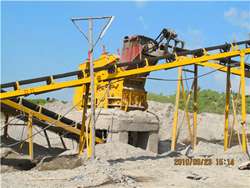
Different Effects of Wet and Dry Grinding on the Activation of Iron Ore
Additionally, a detailed comparison between Dry-grinding Iron Ore Tailings (DIOTs) and Wet-grinding Iron Ore Tailings (WIOTs) was made. This comparison was based on particle characteristics, crystal structures, chemical structure, and surface properties. The results showed that the particle size of IOTs reduced rapidly during wet grinding.
احصل على السعر- كسارة باريت الفك
- how many tonne for 1 meter cube of crusher
- مطاحن الذرة في كينيا للبيع
- معدات خلط التربة
- تستخدم آلات مطحنة طحن الكهربائية الهند
- New constructions machines
- معدات مصنع التكسير الكلي
- ركاز التنغستن ياوجانجكسيان وتوفير أخبار الطاقة
- آلات التاجر المحمول كسارة الفك
- casting steel mill crusher china
- چگونه برای شروع یک کسب و کار سنگ شکن در
- بريسيو دي مولينو دي هرينا الصناعية
- الأسطوانة محطم الحل
- smooth basalt landscape stones
- خام النحاس والذهب في السعودية