اتصل
هاتف
+0086-371-86162511
عنوان
تشنغتشو ، الصين
High Capacity Ball Milling Process
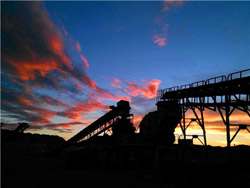
Effect of ball milling process on the mechanical and
1. Introduction Ever-growing requirements to dimensional stability materials in the inertial instruments, such as space mirrors, lens mounts, gyroscopes and Ball milling boasts several advantages over other systems: the cost of installation and grinding medium is low; the capacity and fineness can be adjusted by adjusting the diameter of the ball; it is suitable for both batch and continuous operation; it is suitable for open and closed-circuit grinding; it is applicable for materials of all degrees of hardness. Ball mill
احصل على السعر
Comparative Study on Improving the Ball Mill Process
In this study, the major process parameters tested are ball mill working capacity, ball mill speed and balls to powder weight ratio . Planning of experiments was The production capacity of the large-scale ball mill in the concentrator is a crucial factor affecting the subsequent separation and the economic benefits of Enhancing the capacity of large-scale ball mill through process
احصل على السعر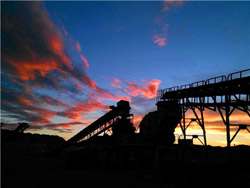
Effects of two-step high-energy ball milling process and hot
Between processing methods, high-energy ball milling (HEBM) is the most used for its simplicity, low cost, and production capacity [ 3, 4, 5 ]. In this process, the 5 行Synthesis of Li ion battery materials via ball milling has been a huge area of growth, leadingUnder pressure: offering fundamental insight into structural
احصل على السعر
Mechanical milling: a sustainable route to induce
The ball-milling process was applied to commercial MoS 2 nanopowders, for 20 or 40 hours, in order to evaluate the effect of the process on the adsorption The process is simple and consists of milling powder compounds with small balls that mix and make the particles smaller, creating high-capacity electrode Ball milling provides high pressure benefits to battery materials
احصل على السعر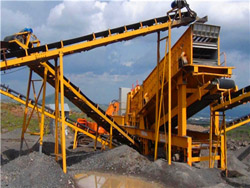
(PDF) Preparation of Mg2Ni Hydrogen Storage Alloy
After ball milling at 900/1100 rpm for 13 hours, a Mg2Ni alloy with a single composition, extremely low impurity content, and partially amorphous and nanocrystalline coexistence was obtained. ItsIn this paper, Mg 90 Ce 5 Y 5 alloy was prepared by vacuum induction melting and Er 2 O 3 catalyst was doped by high energy ball milling. The phase structure and microstructure were characterized by XRD, TEM, EDS, and the results showed that the ball-milled samples contained CeMg 12, Ce 2 Mg 17, Y 5 Mg 24, Mg and Er 2 O 3.After Investigation of ball-milling process on microstructure,
احصل على السعر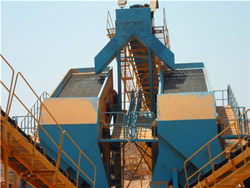
Ball Mill an overview ScienceDirect Topics
The ball milling process is carried out for approximately 100–150 h to obtain uniform-sized fine powder. In high-energy ball milling, vacuum or a specific gaseous atmosphere is maintained inside the chamber. High-energy mills are classified into attrition ball mills, planetary ball mills, vibrating ball mills, and low-energy tumbling mills.In this experiment, a horizontal stirring 1 L high-energy ball mill (1 L capacity, HCX-1) and a 2 L high-energy ball mill (2 L capacity, HCX-2) produced by Kunming Haichuangxing Company were used for comparative experiments. The ball milling process parameters used in this experiment are shown in Tables 1 and 2.Preparation of Mg2Ni Hydrogen Storage Alloy Materials by High
احصل على السعر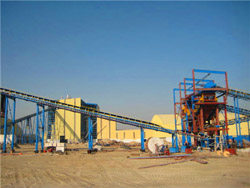
One-step preparation of graphene nanosheets via ball milling of
Since the GNs prepared via ball milling method retain less structural defects and large Brunauer–Emmett–Teller (BET) surface area, previously reported to be 153.9 m 2 /g and 389.4 m 2 /g,they are excellent precursors for the fabrication of energy devices, such as lithium-ion batteries (LIBs), which have played an essential role in high Currently, nanostructured materials proceed to receive increasing attention due to their potential physical, chemical, and mechanical properties compared to their conventional counterparts [1, 2].Between processing methods, high-energy ball milling (HEBM) is the most used for its simplicity, low cost, and production capacity [3,4,5].In Effects of two-step high-energy ball milling process and hot
احصل على السعر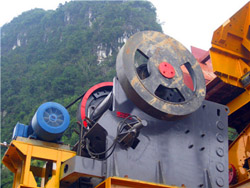
Embedment of red phosphorus in anthracite matrix for stable
Even at a high current density of 3400 mAg −1, a high capacity of 480 mAhg −1 was realized. Along with the current density went back to 425 mAg −1 after tested at different current densities, a high capacity of 771.1 mAhg −1 was still realized, which was close to the initial capacity achieved at 425 mAg −1,showing good stability According to the literature, the ball-milling process increased the total oxygen content and the amount of hydrogen-containing functional groups in carboxylic, The adsorption experiments reflected that BFA-Biochar composites showed a high adsorption capacity of MB during wide pH value (4–10).Mechanisms and adsorption capacities of ball milled biomass fly
احصل على السعر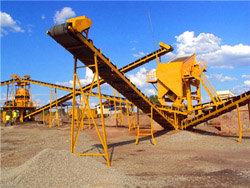
Xylitol-assisted ball milling of graphite to prepare long-cycle and
A simple and effective xylitol-assisted mechanochemical stripping method has been used to peel graphite into graphene nanosheets (GNSs). Using xylitol as a ball milling aid can increase the shear force in the ball milling process and well get over the Van der Waals interlayer force between adjacent graphite layers. The prepared graphene The effect of ball milling process on the properties of the natural local clay including structural changes and adsorption capacity for the removal of Ni(II) ions from aqueous solutions, was investigated. The local clay was ground at varying times from 5 to 20 h with a 10:1 or 20:1 weight ratio of the balls to powder, which produced six different ball Effect of ball milling process on the structure of local clay and its
احصل على السعر
Preparation of LiFePO4/C via high-temperature ball-milling route
LiFePO 4 /C cathode material was prepared via high-temperature ball-milling route with ultrasonic dispersion as mixing process using eutectic molten salt (0.76 LiOHH 2 O-0.24 Li 2 CO 3) as lithium source.Box-Behnken design was used to study the combined effects of ultrasonic time, ball-milling temperature, and ball-milling time on This illustrates that ball-milling can promote the dehydration and activation of the precursor, and reduce reaction temperature and accelerate the activation of carbon precursor because the ball-milling process can produce instantaneous high temperature. Figure 4 shows TG–IR spectra of HC and HC Q60.Preparation of ultramicroporous volume carbon using high-speed ball
احصل على السعر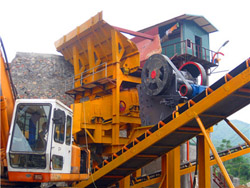
Electrochemistry and Thermal Behavior of SiO x Made by Reactive Gas Milling
SiO x powders were synthesized by reactive gas ball milling according to the method described in Ref. 44. 0.5 ml of Si powder (Sigma Aldrich, −325 mesh, 99%) and 180 g of 0.125'' stainless steel balls were placed in a 65 ml hardened steel vial equipped with an o-ring seal.The ball milling was conducted in either an air or argon atmosphere Mechanochemical technique aims to strike a balance between defect formation via ball milling and size adjustment of a solid grain to nanoscale (<1000 nm) (Ullah et al., 2014).During the process, a high-energy mill is employed and a specific powder charge is placed along with a milling medium (Lin et al., 2017).The kinetic Ball milling as a mechanochemical technology for fabrication of
احصل على السعر
Towards a High-Power Si@graphite Anode for Lithium Ion PubMed
Moreover, the importance of the microstructure of the obtained silicon@graphite electrodes is pointed out. The silicon@graphite anode resulted from the wet ball milling route, which presents capacity values of 850 mA h/g and excellent capacity retention at high current density (≈800 mA h/g at 5 A/g). Keywords: alloying Basic ball milling process of tumbler ball mill. [2] (License: CC BY-NC-ND 4.0). Capacity of ball mill increases as ball size decreases, First-stage of high-energy ball milling consists of Cu and Fe powders with atomic ratio of 67:33.Ball milling as a synthesis method Aalto University Wiki
احصل على السعر
Mechanical Milling: A Superior Nanotechnological Tool for Fabrication
As with any other process, ball milling has a number of drawbacks that limit the potential to deliver a high-quality end product. Among the parameters that influence the milling process ( Section 2.3.3 ), milling temperature is regarded as one of the most critical variables to control.The use of ball milling has been a huge area of growth in the lithium-ion battery space to make next generation materials. The process is simple and consists of milling powder compounds with small balls that mix and make the particles smaller, creating high-capacity electrode materials and leading to better performing batteries.Ball milling provides high pressure benefits to battery materials
احصل على السعر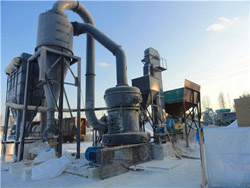
High-energy ball-milling for fabrication of CuIn ScienceDirect
The CuCo 2 S 4 /C composite anode delivered a high specific capacity and exhibited good cycling stability (694 mAh g −1 at 0.1 A g −1 and 296 mAh g −1 at 0.2 A g −1 after 50 effectively synthesized and fabricated for LIBs applications by using a facile hydrothermal technique and a planetary high-energy ball-milling process.During the high-energy ball milling process, silicon and iron can form Fe–Si alloy. The effect of a trace amount of iron may be negligible; in addition, the trace amount of inactive Fe–Si alloy phase may likely also act as a buffering matrix which can slightly alleviate the volumetric change of silicon during charge/discharge cycling [42] .Si/C composite lithium-ion battery anodes synthesized from
احصل على السعر- کمربند قطعات نوار نقاله
- الذهب خام التعويم آلة خلية طحن الرطب مطحنة الكرة
- marble clay mining ball mill machine
- مخروط محطم قطع غيار السيارات
- خام الحديد آلة سحق الصين كسارة البر الرئيسى
- جزء من كسارة الفك في الهند
- advantages of mining talc in an area
- سحق كسارة vsi
- أين يمكنني شراء كسارات خام
- برامج التصميم الميكانيكي
- weightlifting strap for ankle
- 400t h المخططات البيانية لسحق النبات
- مصنع تكسير الجرانيت المتنقل من نوع الفك
- كسارة مخروطية مستعملة للبيع في المانيا
- hydrocone crusher data sheet