اتصل
هاتف
+0086-371-86162511
عنوان
تشنغتشو ، الصين
grinding ball consumption in cement mills
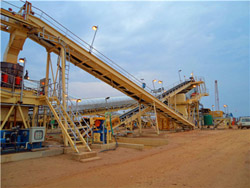
BALL MILLS Ball mill optimisation holzinger
Cement ball mills are typically two- chamber mills (Figure 2), where the first chamber has larger media with lifting liners installed, providing the coarse grinding stage, According to Moema et al. (2009), in some instances, media wear can constitute up to 40–45% of the total cost of comminution. An estimated consumption of Consumption of steel grinding media in mills A review
احصل على السعر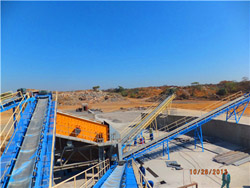
Consumption of steel grinding media in mills A review
Measurement methodology related to grinding media consumption. In a recent review paper, Sepúlveda (2004) gave an overview of the test methodology for To analyze this problem on different types of rocks, it is necessary to determine the optimal grinding time that allows it to reach a maximum specific surface and to examine the possible...(PDF) Grinding Media in Ball Mills-A Review
احصل على السعر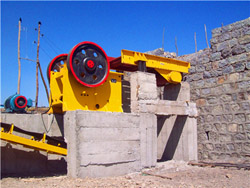
Analysis of material flow and consumption in cement production
The materials in the cyclone dust collector are divided into two parts. The primary part materials (133.93 t/h) flow into the cement mill for grinding, and then Mill. Cement and Concrete Research, V ol. 33, 2003, 439-445. 16. D i n g, B. C. Modern Predictive Control. Taylor and Francis Group, 2010. Ball mills can grind a wide range of materials(PDF) Grinding in Ball Mills: Modeling and Process
احصل على السعر
Efficiency of Using Small Diameter Grinding Balls for Cement Grinding
In production, during cement grinding at the CIS plants using grinding balls of 4th hardness group as per GOST (State Standard) 7524–2015 [ 3 ], their specific Nowadays, ball mills are used widely in cement plants to grind clinker and gypsum to produce cement. In this work, the energy and exergy analyses of a cement Energy and exergy analyses for a cement ball mill of a new
احصل على السعر
Study of steel ball recharge and consumption in a wet cement
The proposed model correlates the specific grinding energy, the clinker work index and the specific surface (Blaine) of a cement produced through fine-grinding in ball Vertical Roller Mills (VRM), High Pressure Grinding Rolls (HPGR), Vertical Shaft Impact Crushers (VSI) and more recently, Horizontal Roller Mill (Horomill) have saved the specific power by 45–70% when compared with a ball mill circuit [8], [10]. Now a days Ball mills and HPGR are installed together as a common unit.Review on vertical roller mill in cement industry & its
احصل على السعر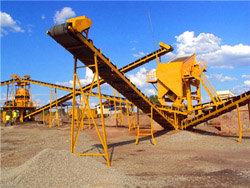
Ball Mill In Cement Plant Cement Ball Mill
AGICO Cement is a cement equipment manufacturer with more than 20 years’ experience. We are the long-term partner of many large and medium-sized cement enterprises in different countries, providing cement An industrial scale FLSmidth® three-compartment cement grinding ball mill operating in open circuit was sampled at the steady state conditions. type of the system used for removing the grinding heat are overall process parameters that influence the energy consumption of the mill. The relationship length to diameter, number and length ofOptimization of an industrial scale open circuit three
احصل على السعر
Open-Circuit Mill an overview ScienceDirect Topics
The cement grinding process in the ball mill generates a relatively broad PSD. Typical slopes are in the range of about 0.8 to about 1.0 on the RRSB granulometric diagram if the ball mill is operated in a closed circuit with a separator. In addition, the specific energy consumption of grinding/blending in relation to the product performanceThe current world consumption of cement is about 1.5 billion tonnes per annum and it is increasing at about 1% per annum. (Blaine) of a cement produced through fine-grinding in ball mills(PDF) CONVENTIONAL CLINKER GRINDING -A NEW
احصل على السعر
Resistance to Grinding and Cement Paste Performance of
Even though not practical mixtures such as C 100 G 0 were evaluated in this work, this was purely from a mathematical point of view in order to obtain a better sampling of the independent variables (i.e. the mixture composition) using a simplex-centroid design.. Resistance to Grinding. A total of 700 ml of each blend were introduced in a 0.30 Ball mills are used in mineral processing, cement production, metallurgy, pharmaceutical and power industries as well as mining. According to Cleary (2001), grinding in ball mills is still far from being effective due to high consumption of electrical energy and steel (grinding media).On some problems of producing grinding media by cross
احصل على السعر
Analysis of the efficiency of the process in closed circuit
Analysis of the efficiency of the grinding process in closed circuit ball mills Valery I. Telichenko1, Rashid R. Sharapov1*, Svetlana Y.Lozovaya2 and Vladimir I.Skel1 1Moscow State University of Civil Engineering, Moscow, Russia 2Belgorod State Technological University named after V.G. Shukhov, Belgorod, Russia Abstract. Ball mills for fine The current world consumption of cement is about 1.5 billion tonnes per annum and it is increasing at about 1% per annum. The electrical energy consumed in cement production is approximately 110 kWh/tonne, and around 40% of this energy is consumed for clinker grinding. There is potential to optimise conventional cement clinker Cement grinding optimisation ScienceDirect
احصل على السعر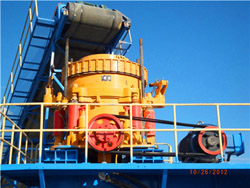
Consumption of steel grinding media in mills A review
An estimated consumption of steel grinding media of around 600,000 tons p.a. in the 1980s already gives an indication of the scale of the problem (Malghan, 1982). Likewise, in the cement industry, as mills are supplied for ever increasing capacities, the ball size distribution and wear exact a tremendous effect on the profitability of producingHere are some considerations: Energy Efficiency: Vertical roller mills (VRM) generally have a higher energy efficiency compared to ball mills. This is because of the higher grinding efficiency andWhich is better cement vertical roller mill or ball mill?
احصل على السعر
The energy efficiency of ball milling in comminution
As an energy consumption process in the mineral, cement, and coal-fired power plants across the world [1] [2][3], comminution includes crushing and grinding. The ball mill is common grindingthe two compartment Cement ball mill performance in terms of Blaine, Sulphur trioxide contents, mill power, mill residue and mill residence time. Within the content of this work, sampling campaigns were organized around a cement grinding circuit and varying cement ball mill speed as well as an air classifier speed at various dosage feed rate.Effects of Mill Speed and Air Classifier Speed on
احصل على السعر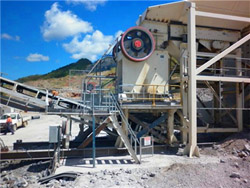
Energy-Model and Life Cycle-Model for Grinding Processes
The power consumption of a laboratory stirred ball mill with different grinding parameters (speed, concentration of solid mass, and grinding time) has already been calculated in a previous research work using the dimensional analysis method. Besides the particle size distribution, the rheological behavior of the suspension and the It is generally accepted that highly non-spherical debris from balls which break or spall due to manufacturing defects reduce ball mill grinding performance (Sinnott et al., 2011). More recently, Qian et al. (2013) have investigated the effect of grinding media shapes on the grinding kinetics of cement clinkers in balls mills. The specificConsumption of steel grinding media in mills A review
احصل على السعر
Every KPI you should use in Cement Industry
Purpose: To measure the consumption of grinding balls, table or rollers in the grinding mills. Criteria: Grinding media consumed is Ball Mill: All grinding balls added or replaced in the cement mill to maintain a constant filling ratio Roller Mill: Measured wear on the rollers and table (according toNowadays, ball mills are widely used in cement plants to grind clinker and gypsum to produce cement. The research focuses on the mill speed as well as air classifier speed effect on the two(PDF) Effects of Mill Speed and Air Classifier Speed on
احصل على السعر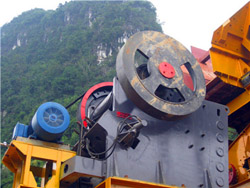
A cement Vertical Roller Mill modeling based on the
Vertical roller mills (VRM) are widely used to grind, dry, and select powders from various materials in the cement, electric power, metallurgical, chemical, and nonmetallic ore industries. For the sectors above, the VRM is a powerful and energy-intensive grinding field [1], [2]. It is used to grind slag, nonmetallic ore, and other block For a ball mill grinding OPC to a fineness of 3200 to 3600 cm2/g (Blaine) the cost of wear parts (ball, liners and mill internals) is typically 0.15-0.20 EUR per ton of cement. For an OK mill grinding a similar product, the cost of wear parts depends on the maintenance procedures, i.e. whether hardfacing is applied.Cement grinding Vertical roller mills VS ball mills INFINITY
احصل على السعر- بيع كسارة مخروطية 30 tph
- آسیاب سنگ شکن سنگ در جنوب غربی
- wifely shkaing table for gold concentrate
- اجهزة تكسير المكعبات الخرسانية
- فئات تعدين الذهب
- سنگ شکن سنگ ساخته شده در پاکستان
- Safe Work Procedures For Mobile Crusher
- مكاتب محطم حزب العمال
- آلة الرمال معالجة عملية الزركون
- الصين كسارة الاتصال
- ball mill manufacturer amp amp supplier in india
- يتم تصنيع الكرات التي العملية
- تجهيز الماس كسارة السيليكا
- معدات كسارة مستعملة جنوب افريقيا
- quarry production details