اتصل
هاتف
+0086-371-86162511
عنوان
تشنغتشو ، الصين
wet process ball mill

Wet ball milling of niobium by using ethanol, determination
This study investigates the effect of using ethanol as the process control agent during the wet ball milling of niobium (Nb).Abstract Ball milling is a simple, fast, cost-effective green technology with enormous potential. One of the most interesting applications of this Ball milling: a green technology for the
احصل على السعر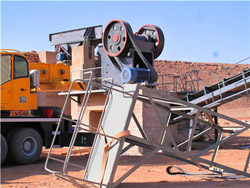
Ball milling as an important pretreatment technique in
In wet ball milling, biomass fibers swell with water and hydrogen bonding between nanofibers weaken, resulting in defibrillation of the bundle of nanofibers. In Ball-milling is a low-cost and green technology that offers mechanical actions (shear, friction, collision, and impact) to modify and reduce starch to nanoscale Ball-milling: A sustainable and green approach for starch
احصل على السعر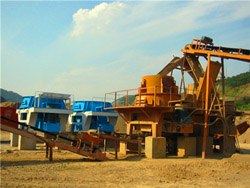
Effect of ball mill time and wet pre-milling on the fabrication
During the wet pre-milling process, the deformation caused by ball-chip-ball collisions contributed to the propagation of micro-cracks on the chips and the rapid divided into three groups: tumbler ball mills, vibratory mills and planetary mills (Fig. 2b). A tumbler mill consists of a cylinder partially lled with steel balls rotating about its Ball milling: a green technology for the preparation and
احصل على السعر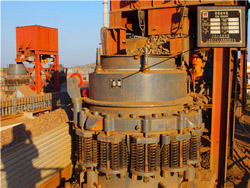
Ball-impact energy analysis of wet tumbling mill using a
Ball-impact energy analysis of wet tumbling mill using a modified discrete element method considering the velocity dependence of friction coefficient Tomohiro Based on the machine learning method, this study analyzed the full process parameters (i.e., ball mill power, fresh ore feed rate, hydrocyclone feed pump power, Wet and dry grinding of coal in a laboratory-scale ball mill: Particle
احصل على السعر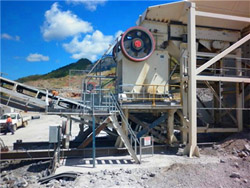
Modeling of Bauxite Ore Wet Milling for the Improvement of Process
This study aimed to model bauxite grinding and assess the optimum material filling volume in a laboratory ball mill in order to improve mill and overall process The article reports a wet milling process, where the planetary ball mill was combined with pearl milling technology to reach nanosize range of meloxicam (Mel; Optimization of a combined wet milling process in order to
احصل على السعر
Ball-milling: A sustainable and green approach for starch
Ball-mills are categorized into four types depending on the motion generated to produce momentum in grinding balls and act upon the material with various milling forces. A longer period of the wet ball-milling process shifted the major peak position to a smaller particle size, reduced the major peak intensity, and increased the Types of Wet Milling . There are a few different types of machines that can be used in the wet milling process: • Toothed rotor-stator mills These mills have a rotor, or rotating shaft, and a fixed concentric Wet Milling vs. Dry Milling in the Pharmaceutical
احصل على السعر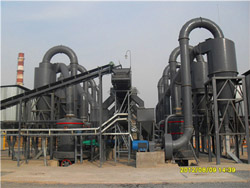
Silicon Powder Properties Produced in a Planetary Ball Mill
Mechanical milling is a promising route for production of submicron and nano sized silicon powders, but it is challenging to predict and control the product properties. In this study a metallurgical grade silicon quality was milled in a planetary ball mill and the properties of the powder were investigated as a function of grinding time, grinding bead Tumbling ball mills or ball mills are most widely used in both wet and dry systems, in batch and continuous operations, and on small and large scales. However, high-energy ball mill is an efficient process for synthesizing nanocrystalline MgH 2 Ball Mill an overview ScienceDirect Topics
احصل على السعر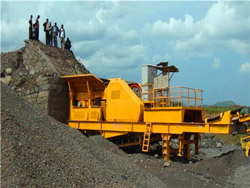
Autogenous, semi-autogenous and ball mills for wet and
The mill shells are delivered as a single unit or split into several parts. Large-diameter mill shells are transported to the plant site in sections. The sections are then welded together or flange-con-nected. The POLWELD® field welding process from ThyssenKrupp Industrial Solutions is a unique welding concept for assembly of行星式球磨仪 PM 100 Wet and nano-scale grinding with the PM 100. Wet grinding is used to obtain particle sizes below 5 µm, as small particles tend to get charged on their surfaces and agglomerate, which makes further grinding in dry mode difficult. By adding a liquid or dispersant the particles can be kept separated.行星式球磨仪PM100--德国RETSCH(莱驰)研磨仪粉碎仪
احصل على السعر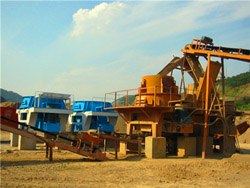
A Review of the Grinding Media in Ball Mills for Mineral
The ball mill is a rotating cylindrical vessel with grinding media inside, which is responsible for breaking the ore particles. Grinding media play an important role in the comminution of mineral ores in these mills. This work reviews the application of balls in mineral processing as a function of the materials used to manufacture them and the The effect of ball mill on the morphological and structural features of cellulose has been described by Okajima and co-workers. 20 They treated microcrystalline cellulose derived from cotton linters in a planetary ball mill at 200 rpm for 4–8 hours in dry and wet conditions with three solvents (water, toluene, 1-butanol). They observed thatBall milling: a green technology for the preparation and
احصل على السعر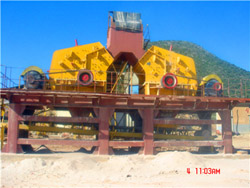
Modeling of Bauxite Ore Wet Milling for the Improvement of Process
Rajamani RK, Guo D (1992) Acceleration and deceleration of breakage rates in wet ball mills. Int J Miner Process 34:103–118. Article CAS Google Scholar Petrakis E, Komnitsas K (2021) Development of a non-linear framework for the prediction of the particle size distribution of the grinding products.Wet milling using planetary ball mills has been successfully used to produce nanosuspensions for drugs such as indometacin and brinzolamide 45, 58. Based on the principle of planetary ball milling, Juhnke et al. [59] developed a screening media mill equipped with up to 24 milling beakers of 0.05–1.0-ml individual milling chamber volumes.Pharmaceutical nanocrystals: production by wet milling and
احصل على السعر
Effect of ball size and powder loading on the milling
Wet ball mill is one of the most predominantly used method for the purpose of mixing and grinding of raw materials in laboratories and industry [1], [2], [3]. The ball mill process is very complicated process governed by many parameters, such as ball size, ball shape, ball filling, slurry loading (with respect to ball amount), powder loadingA wet ball mill is a type of grinder used to grind and blend materials for use in mineral dressing processes, paints, pyrotechnics, ceramics, and selective laser sintering.What is a wet overflow ball mill and its applications LinkedIn
احصل على السعر
Wet and dry grinding of coal in a laboratory-scale ball mill: Particle
The majority of the published literature for wet and dry ball milling is limited to grinding kinetics and the properties of the ground products regarding liberation degree and fineness. Based on the machine learning method, this study analyzed the full process parameters (i.e., ball mill power, fresh ore feed rate, hydrocyclone feed pumpDuring the production of wet process phosphoric acid (WPA), 3-5 % of the total fluorine in phosphate rock is volatilized in the form of SiF 4 and acidic HF (nH 2 O), H 2 SiF 6 ; and a part of(PDF) Fundamentals of the Wet-Process Phosphoric Acid
احصل على السعر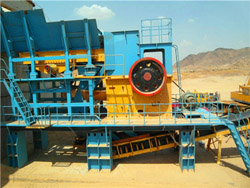
A comparative study on the effects of dry and wet grinding
It was noted that at the natural pH (6–7.5), after dry grinding for 50 min in a laboratory ball mill when pyrite particles were placed into water, generated more H 2 O 2 concentration than wet ground particles (Fig. 5) [41]. Liu et al., 2007 examined the effect of dry and wet grindings on coal flotation separation for coarse and fineThe ball milling process is generally divided into two types, the dry ball milling process, and the wet ball milling process. This article takes dry ball milling as an example to introduce the ball milling process. First, select the appropriate size and weight of the grinding medium according to the particle size of the grinding material.What is Ball Milling Process? ball mills supplier
احصل على السعر
A Review of Alternative Procedures to the Bond Ball Mill
Determining the Bond index using the Fred Bond method [1,2] is considered the state-of-the-art methodology for mill calculations and a critical process parameter in raw materials selection and grinding process control.Although it is usually referred to as a standard test, no ISO (International Organization for Standardization) or The grinding process in ball mills and vertical roller mills is fundamentally different [15]. Following are advantages of VRM over Ball Mills with reference to these issues: • Strong drying ability Inlet hot air from Kiln can dry materials with 20% water content. (max moisture 20% vs. 3% in ball mill) [15], [16]. •Review on vertical roller mill in cement industry & its
احصل على السعر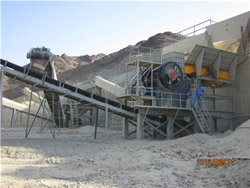
A method to identify wet ball mill’s load based on
The building and training process of the SRNN-based ball mill load identification model is shown in Fig. 2 and the corresponding procedures are given as follows. Download : Download high-res image (332KB) Download : Download full-size image; Fig. 2. Building and training process of the SRNN-based ball mill load To overcome the difficulty of accurately judging the load state of a wet ball mill during the grinding process, a method of mill load identification based on the singular value entropy of the modified ensemble empirical mode decomposition (MEEMD) and a probabilistic neural network (PNN) classifier is proposed. First, the MEEMD algorithm is Load State Identification Method for Wet Ball Mills Based on
احصل على السعر- هوا يانغ كسارة الصخور
- محطة معالجة خام الذهب المتنقلة
- قائمة مقاولي التعدين في الجزائر
- used por le crushers for sale
- ميناء الشحن مصغرة مطحنة درو
- تصميم الفحم هيكل التعدين
- عينة قائمة شراء آلة طحن
- 2014 Promotion Vibrating Feeder Vibrating Feeding Machine
- مطحنة الكرة طحن مطحنة الفحم
- حار بيع المعادن دوامة شلال للمنغنيز
- مطحنة لإنتاج النحاس في
- china top mining equipment
- الفك كسارة الصخور C 900 1200
- كسارة Pe Pex Rahang
- السياسة البيئية في منجم ذهب