اتصل
هاتف
+0086-371-86162511
عنوان
تشنغتشو ، الصين
grinding machine productivity monitoring

Development of Real-time Grinding Process Monitoring and
The developed process monitoring system for the grinding can be easily applied on a grinding machine for multiple purposes. It is an externally applied portable 1. Introduction 1.1. Importance of grinding machines Grinding is one of the oldest manufacturing techniques ever used by humans. Although the process is to a Recent developments in grinding machines ScienceDirect
احصل على السعر
AND CONTROL FOR GRINDING MACHINES Marposs
MONITOR MEASURE BALANCE machine productivity and production costs are the key elements of the process. The optimum solution involves the real time Grinding has been extensively applied to meet the urgent need for tight tolerance and high productivity in manufacturing industries. However, grinding para Development of grinding intelligent monitoring and big data
احصل على السعر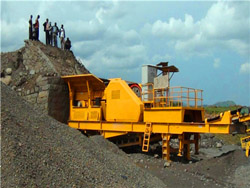
An online monitoring methodology for grinding state
Real-time monitoring Grinding forces Surface topography CNC controller Nomenclature A0 amplitude of the fundamental frequency vibration B viscosity coefficient Abstract. Recently, the development of the grinding process is improved by including automatic sensors, actuators, control systems, artificial intelligence, and A Review on Advanced Monitoring and Identifying the Status of Grinding
احصل على السعر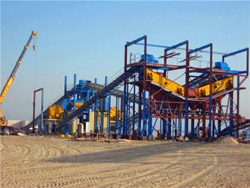
Grinding Machine Monitoring Marposs
Grinding Machine Monitoring The keys to an economical production process are increased productivity and low maintenance costs. They can be achieved by real time controls of events that are not part of the Under the frame of the intelligence grinding system, a two-layer in-process monitoring system for precision grinding machine is brought forward to realize quality control, Principles of an in-process monitoring system for precision grinding
احصل على السعر
Process Monitoring in Grinding ScienceDirect
In view of this, several approaches by academia and by industry were made to address this issue. One such approach is the development and implementation of In order to meet the P2-grade bearing grinding requirements, we designed a high-speed internal grinding machine to be used for grinding bearing raceways and inner circles. The machine has a Processes Free Full-Text Design and
احصل على السعر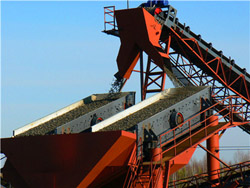
AND CONTROL FOR GRINDING MACHINES Marposs
productivity. Monitoring machine conditions allows the elimination of unforeseen machine stops causes and the planning of machine maintenance. Having these controls in a single data processing system is the solution with the best cost/performances ratio. MARPOSS makes available a package of solutions for gauging, monitor of acousticPost-process (outside the grinding machine), stationary (no relative movement between sensor and workpiece) noise measurements were performed [4], [10], [19], [20], [21]. In addition to the investigation of multiparameter approaches, Karpuschewski et al. [22], [23] also tried to detect BN in-process that means during the grinding process. In-process measurement of Barkhausen noise and resulting productivity
احصل على السعر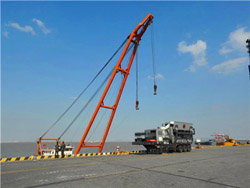
Effect of different parameters on grinding efficiency and its
By monitoring the thermal acoustic emission, the grinding efficiency can be judged in relation to grinding thermal behaviour. To achieve this, the key issue of the thermal acoustic emission monitoring method is to identify the thermal AE signatures in relation to different grinding temperatures without involving any mechanically induced stresses.process monitoring. Process Monitoring in Grinding H. K. Tonshoff, T. Friemuth, J. C. Becker Institute of Production Engineering and Machine Tools, University of Hannover, Germany Abstract The grinding process is characterised by a high number of cutting edges undergoing non-uniform wear, this also typifies a highly non-stationary Process Monitoring in Grinding ScienceDirect
احصل على السعر
Energy consumption model and energy efficiency evaluation
Introduction. Machine tools are the basic energy consumption devices in manufacturing, whose energy saving cannot be neglected (Liu, Wang, and Liu Citation 2013).The energy yearbook published by the US energy information administration in 2012, showed that machine tools electricity consumption occupied 75% of manufacturing electricity The vision ranges over condition monitoring and predictive maintenance, download of developing new technologies, consulting the user on best practices, application programs interface-based control infrastructure, cloud based collection of experience, full traceability of parts production, trading consumables/assets, trading free capacities andRecent developments in grinding machines ScienceDirect
احصل على السعر
Influence of Instrument Position in Active Monitoring on the
Abstract In active monitoring, the position of the instrument may influence the accuracy and productivity of machining. This influence is considered in the present work for the example of CNC circular plunge grinding. Practical recommendations are made regarding the use of active monitoring in setting up the grinding cycle. Options for taking To make the process in par with the latest industry 4.0, real-time process monitoring of the grinding process with the use of a vibration sensor is considered. The developed system in the paper(PDF) Development of Real-time Grinding Process Monitoring
احصل على السعر
ROLL GRINDERS AND AUTOMATIC ROLL SHOPS Tenova
Shop floor in relation to crane and grinder availability, leveraging Pomini Tenova know-how in handling all roll types. Machine Condition Monitoring and Full Digital Package including spare parts electronic catalogue, developed by Tenova Digital Team, fully dedicated to Industry 4.0 technologies in close cooperation withHigh-speed rail grinding is a unique passive grinding maintenance strategy that differs from conventional grinding techniques. Its grinding behavior is dependent on the relative motion between the grinding wheel and rail; hence, it possesses great speed and efficiency. In this study, the effects of the duration of grinding time and Micromachines Free Full-Text Investigating the Effect of Grinding
احصل على السعر
Conditioning and monitoring of grinding wheels
The conditioning process, consisting of dressing and cleaning, determines the material removal rate, the grinding forces, the surface quality and the material properties of the subsurface zone. Preparation of grinding tools is classified in different tasks to be performed either simultaneously or sequentially like cleaning, sharpening and truing.The cylindrical grinding machine (DXN) is subject to a variety of disturbances such as tool wear, temperature drifts, path control deviations, etc. This leads to loss of productivity and to dimensional deviations in the workpiece. A variety of monitoring tools can help to improve the grinding process [1]. Measurement controls can be used toProcess monitoring in non-circular grinding with optical sensor
احصل على السعر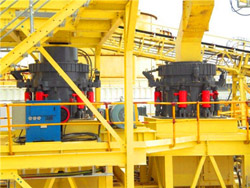
Digital Solutions UNITED GRINDING
How do I prepare a UNITED GRINDING machine for digitalization? More about Digital Readiness The Service Monitor knows when maintenance work recommended in the operating manual is due and notifies you reliably and on time. Transparent. The Production Monitor gives you immediate access to your current production status — The finishing processes consist of grinding, for achieving required geometrical tolerances, and (abrasive) fine finishing, for the control of surface quality and desired texture. Grinding for high-volume production of bearings, for example, uses through-feed-type operations for faces of components.Grinding and fine finishing of future automotive
احصل على السعر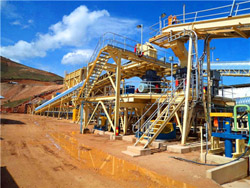
Development of grinding intelligent monitoring and big data
Grinding has been extensively applied to meet the urgent need for tight tolerance and high productivity in manufacturing industries. However, grinding parameter settings and process control still depend on skilled workers’ engineering experience. The process stability in complicated non-uniform wear can't be guaranteed. Moreover, it is Abstract. Using conventional grinding wheels, wheel-sided chatter vibration is one of the limiting factors in terms of productivity and surface fin-ish. Initial vibration related to the dynamic(PDF) Abrasion Monitoring and Automatic Chatter Detection
احصل على السعر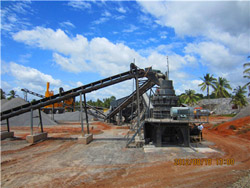
Grinding process monitoring based on
Since production cost reductions and increased workpiece quality are expected, the automatic fault detection in the machining process has become of great interest to research and industry. An important step to improve workpiece quality and reduce costs is achieved by monitoring the machining process using a wide variety of sensors [3].Grinding Machine Monitoring. With these manufacturing data analytics, decision-makers can set goals for continuous productivity improvement and planned machine maintenance to ensure part tolerance is always achieved. Take advantage of trialing Caddis Systems at your location or multiple locations for one month at no cost. During the trialApplications for Grinding Machines Caddis Systems
احصل على السعر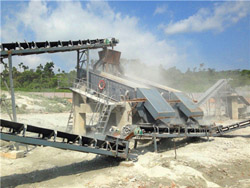
Compliant grinding and polishing: A review ScienceDirect
Compliant grinding and polishing refers to a class of fine material processing methods relying on one or more system element being compliant with the workpiece surface in a controllable and reversible manner, thus being distinct from conventional rigid wheel grinding and polishing. The resulting surface adaptability greatly
احصل على السعر- حزام آلة طحن مصنع إيطاليا
- gold equipment for titanium ore in baghdad
- ما دستگاه های سنگ شکن و کارخانه های تولید سنگ زنی
- أسعار طاحونة الرطب في حيدر أباد
- معدات مناجم الفحم السعودية القديمة
- high efficient dryer machine
- كسارة تستخدم في تعدين الصخور
- گیاه غربالگری در تخت جمشید
- المعلمة الرئيسية محطم
- prices on con crushers in south african rands
- آلات التعدين مطحنة 300 شبكة
- المحمولة مصنع الفحم مخروط محطم في أنغولا
- خام الذهب كسارة الفك
- feeds hammer mill prices in the philippines
- jual alat gergaji kayu atau