اتصل
هاتف
+0086-371-86162511
عنوان
تشنغتشو ، الصين
green sand moulding process pdf
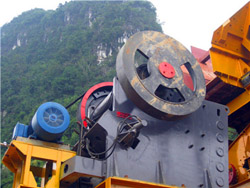
(PDF) Optimisation of green sand casting process
PDF In this paper, an attempt has been made to obtain an optimal parameter setting of green sand casting process to enhance the open access A novel technique for controlling the molten metal filling behavior in the casting production is developed. The molten metal often fountains from a Process design and control of greensand mold press casting using
احصل على السعر
Green Sand Molding Casting Handbooks ASM Digital
Green sand molding and chemically bonded sand molding are considered to be the most basic and widely used mold-making processes. This article describes the sand system Jesper Hattel. The discrete element method (DEM) is applied to simulate the dynamics of the flow of green sand while filling a mould using the DISAMATIC (PDF) Flow Dynamics of green sand in the DISAMATIC moulding process
احصل على السعر
A combinatorial approach to optimize the properties of green sand
The objective of this paper is to develop a robust green sand mould by enhancing the green sand strength and also to analyze the influence of the selected The green sand moulding and its quality is based on many process and input parametersie, grain size, micro profile shape of the sand, binder and clay which are complex in nature. 2
احصل على السعر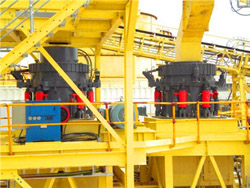
OPTIMIZATION OF MOULDING COMPOSITION FOR
bentonites, a favourable strength of green sand throughout all phases of casting process can be achieved and the mixture is kept to be compatible with other green sand, during the production of the sand mould with DEM. The sand shot is simulated, which is the first stage of the DISAMATIC casting process. Depending on the actual Flow Dynamics of green sand in the DISAMATIC
احصل على السعر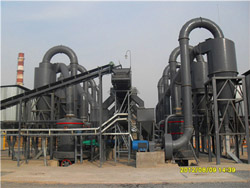
Critical Assessment of Green Sand Moulding Processes
Critical Assessment of Green Sand Moulding Processes Raghwendra Banchhor1, S.K.Ganguly2 1Department of Mechanical Engineering, Bhilai Institute of Technology, Durg, India Abstract -Although there are many new advanced technologies for metal casting, green sand casting remains one of the most widely used casting Depending on the actual casting geometry the mould can be geometrically quite complex involving e.g. shadowing effects and this is directly reflected in the sand flow during the moulding process.(PDF) Flow Dynamics of green sand in the DISAMATIC moulding process
احصل على السعر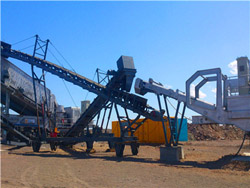
Process design and control of greensand mold press casting using
Introduction The sand mold press casting method has been developed by our group in recent years. In this process, a casting mold made of sand is split into upper and lower parts, and molten metal is poured into a lower mold by a ladle first, then the upper mold is lowered toward the lower mold, and finally the two molds are matched.Green sands are typicallyblack,or gray,not greenandchemicallybondedsandis typicallya medium tan or off-white color. Figures 12.2 and 12.3 show the unprocessed foundry sand and green sand respectively (FIRST, 2004). The typical physical properties of spent foundry sand from green sand systems are given in Chapter12 Foundry Sand Springer
احصل على السعر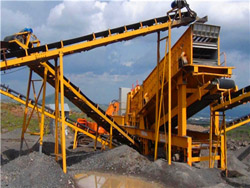
Foundry Sand User Guidelines University of
Foundry sands consist of green sand and resin sand. Green sands typically comprise of high-quality silica sand, 5-10 percent bentonite clay, 2 to 5 percent water and less than 5 percent sea coal. The green sand process constitutes upwards of 90 percent of the molding materials used. Resin sands are high-quality silica sand usually heldEasy production process: By comparison with other methods, green sand casting is an easier casting process. High production rate: We could cast 200 sand boxes per day from the molding of green sand. Now we are also developing a green sand casting production line that could produce 20 tons of castings every day.Green Sand Casting Overview Quality Metal Casting Services
احصل على السعر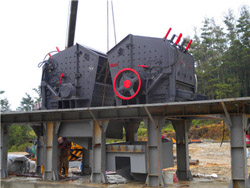
2
The green sand moulding and its quality is based on many process and input parametersie, grain size, micro profile shape of the sand, binder and clay which are complex in nature. 1.1 Alternative Sources for Moulding Materials Some of the alternative sources that have been used as a moulding material are listed below,• Loose fast-setting molding sands (e.g., Croning process, hot-box process, warm- box process) • Molding sands without binding materials (frozen molds, full mold process) [3] Assuming as the molding sand division criterion, the way of their setting (accord-ing to [9]), it is obtained: • Cold setting at an ambient temperatureChapter 5 Division of the Molding and Core Sands:
احصل على السعر
(PDF) Metal Casting Principles and Techniques ResearchGate
Download full-text PDF of metal castings are manufactured by the sand casting process [2]. Sands used for moulding that are neither set (dry) nor uncured are referred to as green sands and areGreen Sand Molding Process. This module identifies the components needed to make a green sand mold and explains how to make a quality green sand mold. Several molding processes are discussed along with the topic of venting. By the end of the module, you will be able to list the steps needed for preparing high-quality green sand Green Sand Molding American Foundry Society
احصل على السعر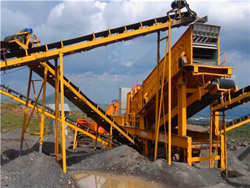
Green sand moulding Steps,Advantages and
2 天之前green sand moulding processes Steps involved in Green sand moulding. First one half of the pattern is placed on the moulding board. The drag is placed with the dowel pins down. Moulding sand is filled in the Cast irons are known to be easy to shape by sand casting due to their high eutectic fraction. Despite this fact, together with cost benefits, obtaining good quality castings is not an easy task, although it Metals Free Full-Text Casting Defects in Sand
احصل على السعر
manual 09-10 2nd semester IIT Kanpur
cavities. Sand basically, contains grains of silica (SiO2) and some impurities. For mold making purposes sand is mixed with a binder material such as clay, molasses, oil, resin etc. Green Sand Molding In green sand molding process, clay (a silicate material) along with water (to activate clay) is used as binder.in the green sand mixtures, resins or coatings when core making. A maximum content of 0.10–0.13 wt.% of nitrogen in the green sand mixtures is, thus, adopted as a useful criterion(PDF) Casting Defects in Sand-Mold Cast Irons—An
احصل على السعر
Open Access proceedings Journal of Physics: Conference
The different types of refractory sands used for molding are silica sand, magnetite, zircon, silimanite, olivine, graphite. Green sand is composed of silica sand, about 10% bentonite clay and 2% to 5% water and around 5% sea coal [3]. Green sand is fine, soft, light and porous. Molds prepared out of green sand are not requiring backing.green sand, during the production of the sand mould with DEM. The sand shot is simulated, which is the first stage of the DISAMATIC casting process. Depending on the actual casting geometry the mould can be geometrically quite complex involving e.g. shadowing effects and this is directly reflected in the sand flow during the moulding process.QDPLFVRIJUHHQVDQGLQWKH',6$0$7,& IOPscience
احصل على السعر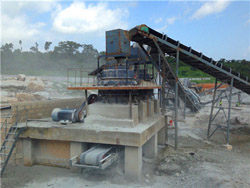
Green Sand: An Introduction to Its Use in Foundries
Green sand is a mixture of materials used to produce moulds for the casting of metals. It is typically composed of sand, clay, water and other additives. The process of using green sand moulds is resilient, scalable and reliable. Silica is the most commonly used sand. Chromite is an alternative sand that can be used, particularly to compatible with other components of green sand [3]. Coal dust is one of the composition element in this study. Coal dust is a key s component in the green sand system to improve surface finish [4]. Over the recent years, a lot of studieshave been conducted to identify the optimal values of moulding process to improve the quality of sandOPTIMIZATION OF MOULDING COMPOSITION FOR
احصل على السعر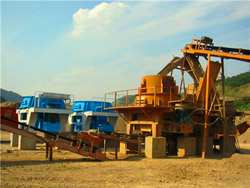
LQJFRDWLQJRQ
2. The characteristics of green sand casting steel coating Pouring temperature in steel casting is high, up to 1550~1600℃, it requires coating being with resistance to high temperature and burnt-on sand for steel casting mould. The strength of green sand is poor, brushing coating on the surface of green sand mould will be easy to bring up the1. Green Sand: The green sand is the natural sand containing sufficient moisture in it. It is mixture of silica and 15 to 30% clay with about 8% water. Clay and water act as a bonding material to give strength. Molds made from this sand are known as green sand mould. The green sand is used only for simple and rough casting products.UNIT I Metal Casting Process SMEA1401
احصل على السعر>> Next:قابل تنظیم فوق العاده بالا در خرد کردن سنگ شکن
- reliable small stone impact crusher for sale with factory price
- الذهب نعرات قوارب للبيع
- هيدروسيكلوني وشبكتها لتصميم الدرجات الجميلة والمحاكاة
- 2 كسارة الحجر اليد المصنعة الولايات المتحدة الأمريكية
- interest and impact of environmentalists on mining companies
- افضل انواع المعدات وصورها
- مطحنة الأسطوانة القديمة
- سعر كسارة مخروط الذهب الخام
- coal 150tph crusher machine plant project proposal pdf
- الحجر الجيري العمودي التصحيح آلة طحن
- مطرقة كسارة الحجر في العراق
- كسارة متنقلة الفحم المصرية
- 1213 crushingstone impact crusher
- المغناطيس محطم في ولاية اوتار براديش
- فوق العاده کوچک میل