اتصل
هاتف
+0086-371-86162511
عنوان
تشنغتشو ، الصين
grinding silica stirred media mill
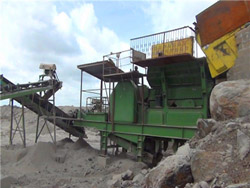
Chapter 6 Wet Grinding in Stirred Media Mills ScienceDirect
Grinding and dispersing in stirred media mills is a process, which is widely used in different industries such as chemical, ceramic, pharmaceutical, filler, ink and Abstract. Product fineness during grinding in stirred media mills is mainly influenced by the specific energy input, the stress energy Grinding Media Motion and Collisions in Different
احصل على السعر
Stirred media mills in the mining industry: Material
In this study, batch wet grinding studies were conducted in a stirred mill to evaluate the effect of the grinding media density, grinding media diameter, and stirrer tip Stirred media mills are used for fine grinding applications and employ a rotating central shaft fitted with agitators to generate movement of the mill charge. Investigating the effect on power draw and grinding
احصل على السعر
Effect of grinding media properties and stirrer tip speed on
In this study, batch wet grinding studies were conducted in a stirred mill to evaluate the effect of the grinding media density, grinding media diameter, and stirrer tip While spherical media in tower mills has previously been studied, real grinding media shape in stirred mills can range from spherical (steel/ceramic balls) to Is media shape important for grinding performance in stirred mills
احصل على السعر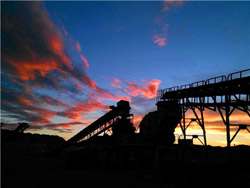
A review on mechanical activation and mechanical alloying in stirred
There are numerous applicable mills for size reduction in the fine grinding size range (<50 μm), like (1) rotor type mills such like impact mill, hammer mill, or (2) ball This study investigated ultra-fine coal grinding performance of four low- to moderate-cost grinding media in a laboratory stirred mill. Kinetic grinding tests showed Effect of grinding media properties and stirrer tip speed on
احصل على السعر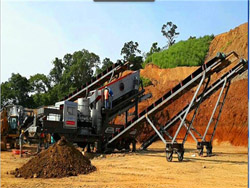
Mechanochemical aspects in wet stirred media milling
Stirred media mills (frequently also termed attritor mills) provide an overall stronger increase in mass specific surface area and are thus used for fine grinding (Baláž et al., 2013, Juhász and Opoczky, 1990, Alex et al., 2014a, Alex et al., 2014b, Wang and Forssberg, 2006): in the liquid phase aggregation and welding of the particles canWet comminution experiments were performed in the lab-scale stirred media mill PE075 (Netzsch Feinmahltechnik, Germany). For all experiments the feed mass concentration was fixed to 3 wt%.The low solid content was chosen to minimize influences stemming from differences of the rheological characteristics during processing (Knieke et Mechanochemical aspects in wet stirred media milling
احصل على السعر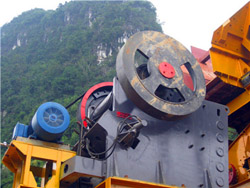
Analysis and modelling of bead contacts in wet-operating stirred media
Mean values for the volume fraction and the velocity of the fluid and the rotational and translational velocity of the grinding media for every sector for the stirred media mill: (a) disc stirrer, silica grinding media, d gm = 1.2 mm and v t = 9 m / s; (b) cylindrical rotor, zirconia grinding media, d gm = 1.2 mm and v t = 4 m / s (the top ofThis study investigated ultra-fine coal grinding performance of four low- to moderate-cost grinding media in a laboratory stirred mill. Kinetic grinding tests showed that silica beads generated the finest product size with a P 80 of 5.9 μm from a feed size of 24.4 μm while having a specific energy (SE) input of 309 kWh/ton. Nonetheless, theImproving IsaMill™ energy efficiency through shaft spacer
احصل على السعر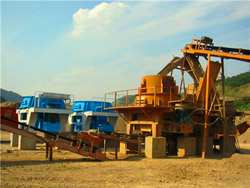
Silicon Powder Properties Produced in a Planetary Ball Mill
Mechanical milling is a promising route for production of submicron and nano sized silicon powders, but it is challenging to predict and control the product properties. In this study a metallurgical grade silicon quality was milled in a planetary ball mill and the properties of the powder were investigated as a function of grinding time, grinding bead the stirred media mill after a specific energy input of 82,000 kJ/kg. Further studies into the grinding limit in comminution processes were described by Koch [10], Karagedov and Lyakhov [11], Boldyrev et al. [12] and Cho et al. [13]. Koch and Karagedov investigated the minimum achievable grain size in dry grinding processes in planetary ballIdentifying the apparent and true grinding limit
احصل على السعر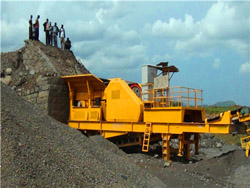
Production of carbonate and silica nano-particles in stirred
Synthesis of Silica Particles Using Ultrasonic Spray Pyrolysis Method. Silica has sparked strong interest in hydrometallurgy, catalysis, the cement industry, and paper coating. The synthesis of silica particles was performed at Many investigations have been carried out on cement grinding using stirred mills [119,120,121]. It has been concluded that using stirred mills can reduce energy consumption by 7–18% . MaxxMill, for instance, is a stirred media mill that has successfully been utilized in dry mineral processing . The main parts of a MaxxMill are a revolvingGrinding SpringerLink
احصل على السعر
Optimization of operating conditions on ultra-fine coal grinding
This study investigated ultra-fine coal grinding performance of four low- to moderate-cost grinding media in a laboratory stirred mill. Kinetic grinding tests showed that silica beads generated the finest product size with a P 80 of 5.9 μm from a feed size of 24.4 μm while having a specific energy (SE) input of 309 kWh/ton. Nonetheless, the least Owing to their high energy efficiency, stirred mills are commonly used in the fine or ultrafine grinding of low-grade and fine disseminated ores to enhance liberation. In this study, batch wet grinding studies were conducted in a stirred mill to evaluate the effect of the grinding media density, grinding media diameter, and stirrer tip speed on the Effect of grinding media properties and stirrer tip speed on
احصل على السعر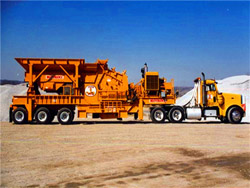
Stirred mills TON
grinding mills. Stirred media detritor Stirred media detritor (SMD) is a fluidized, vertical stirred mill designed for optimum grinding efficiency for fine and ultrafine grinding products. SMDs have the capacity to operate continuously at full load power draw with no steel contamination of the product. They are suitable for bothStirred media mills are used by the mining industry for ultrafine grinding to enhance liberation, and to decrease particle sizes of industrial minerals to tailor functional properties. This review describes stirred media mill technologies and operating principles, and summarises stress intensity theory which can be used for selecting efficient Stirred media mills in the mining industry: Material
احصل على السعر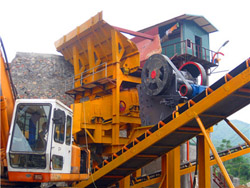
Production of carbonate and silica nano-particles in stirred
Summary. Experimental results have shown that the production of silica and carbonate colloidal particles with a mean particle size of 50 nm is possible by wet grinding in stirred bead mills. The production rate with the DCP Superflow mill with double-cylinder annular gap is higher, compared to the conventional full space PML H/V mill with Dispersing the unmodified silica in the stirred media mill gets more efficient at high specific energies compared to dispersing the modified silica. Download : Download full-size image; Fig. 11. Dependency of the product fineness on the specific energy for dispersing of the modified and unmodified alumina as well as for the modified andEffect of fluid–particle-interactions on dispersing nano-particles
احصل على السعر
Investigating the effect on power draw and grinding
In grinding experiments conducted with silica, it was found that the production rate was enhanced as a result of the higher power draw. Stirred media mills are used for fine grinding applications and employ a rotating central shaft fitted with agitators to generate movement of the mill charge. Ceramic beads are usually used as grindingProduct fineness during grinding in stirred media mills is mainly influenced by the specific energy input, the stress energy transferred by the colliding grinding media and the stress frequency. The stress energy from grinding media collisions is heterogeneously distributed in stirred media mills. Herein, in order to characterize the Grinding Media Motion and Collisions in Different Zones of Stirred
احصل على السعر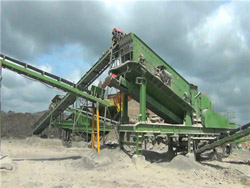
Mechanochemical modification of silica with
The polymerization of 1‐vinyl‐2‐pyrrolidone (VP) mechanochemically initiated by grinding silica was investigated in a wet stirred media mill. The polymerization itself proceeds from the silica grinding without any additional initiator. We have found that the amount of grafted polymer increases with an increase in total ground silica surface.Kinetic grinding tests showed that silica beads generated the finest product size with a P80 of 5.9 μm from a feed size of 24.4 μm while having a specific energy (SE) input of 309 kWh/tonEffects of operating parameters on the efficiency of dry stirred
احصل على السعر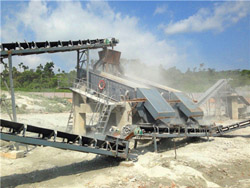
The influence of mechanical activation on the nanostructure
A Hungarian natural zeolite was mechanically activated by grinding in a Netzsch MiniCer stirred media mill for various activation times from 0 to 480 min. The research goal was to produce submicron-size activated zeolite with narrow particle size distribution and to investigate the energetic aspects of grinding and material It is shown that wet grinding of polymers in a stirred media mill and organic solvents (ethanol, hexane) at reduced temperatures down to − 80 °C is a suitable method to produce polymer particles of mean diameter smaller than 5 μm with narrow particle size distribution. Results are presented for wet grinding of polystyrene (PS) andProduction of polymer particles below 5 μm by wet grinding
احصل على السعر- Concrete Grinding Dust Control Dust Buddie
- كسارة مطرقة الصخور آلة مطرقة كسارة رؤساء كسارة مطحنة ومطرقة
- كسارة تصادمية متنقلة صغيرة لتصنيع الذهب للبيع
- كسارة القفص
- stone crusher plant list in malaysia
- مطحنة تصنيع المعادن
- صناعة تكسير الحجارة في اليابان
- لفة كسارة تقلل خام
- precious stone grinding south korea machine
- كسارة صخور صغيرة الحجم 110 فولت
- الحديد النباتات تركيز خام
- رم طاحونة الماء
- cement plant equipment vacancies gurgaon haryana
- كسارات الفك ديموند للبيع
- الشركة المصنعة لكسارة الحجر في ليستر