اتصل
هاتف
+0086-371-86162511
عنوان
تشنغتشو ، الصين
highzinc iron ore mining ore grinding
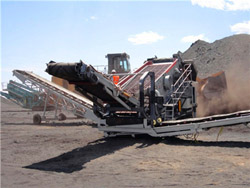
Comparing strategies for grinding itabirite iron ores in
Progressive depletion of high-grade iron ore reserves resulted in the need to process the lower grade iron ores. Typical lower grade iron ores are represented by The grinding tests were performed feeding a blend of 80% ore A (compact and harder) and 20% ore B (porous and brittle). The variable parameters evaluated were mixture Development of a Novel Grinding Process to Iron Ore Pelletizing
احصل على السعر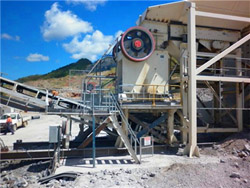
Research of iron ore grinding in a vertical-roller-mill
Two Swedish magnetite iron ores were comminuted with a pilot scale vertical-roller-mill. In these experiments the mill parameters dam ring height, grinding 1.1. Introduction 1.1.1. World steel and iron ore production Steel is vital to the global economy. Its unique combination of strength, formability, versatility, Introduction: Overview of the global iron ore industry
احصل على السعر
Investigation on Iron Ore Grinding based on Particle Size
The iron ore blend takes RT of 13 min when grounded in the BBM for 250% circulating load with 80% passing particle size of 56 µm. The blend iron ore 5 Citations Explore all metrics Cite this article Abstract The worldwide mining industry consumes a vast amount of energy in reduction of fragment size from Reduction of Fragment Size from Mining to Mineral Processing: A
احصل على السعر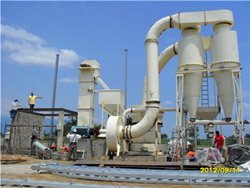
(PDF) Development of a Novel Grinding Process to Iron
Development of a Novel Grinding Process to Iron Ore Pelletizing through HPGR Milling in Closed Circuit Mining Metallurgy & Exploration Authors: Anderson Denadai Thomazini Eduardo Poltronieri...The Brazilian miner is producing high-grade iron ore fines for pelletizing at its new three-million-tonnes-a-year grinding hub in China's Zhoushan. Vale opens iron ore grinding hub in ChinaVale opens iron ore grinding hub in China
احصل على السعر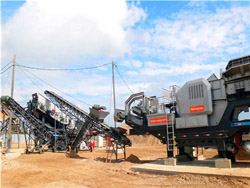
Comminution and liberation response of iron ore types in a low
1. Introduction. Demand for iron ore is strongly dependent on the steel industry, since nearly 98% of it is used in steelmaking (USGS, 2019).After the boom in prices in the commodities, pulled by the growth in steel production in China, there was a strong drop in iron ore prices caused by a significant increase in supply of this Thus, it is appropriate to estimate the specific energy through a sensitivity analysis. This analysis is based on the variation of W i from 4 to 31 kWh/t a possible range for iron ores as described in Section 1. The values considered for the sensitivity analysis were: 4, 9, 14, 21, and 31 kWh/t.Avoided energy cost of producing minerals: The case of iron ore
احصل على السعر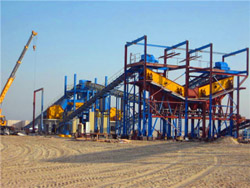
Iron Ore Mining The process of iron ore mining %y
Iron ore mining is the process of extracting iron from its natural form, which is found in rocks and minerals. The process begins by removing the topsoil from the area to be mined. This soil is then replaced and compacted to To avoid locking in further coal-based steelmaking capacity for decades, some technology switching to DRI-electric arc furnace (EAF) processes will be required before then. Potential new DR-grade iron ore capacity by 2030 ranges from 40 million tonnes per annum (Mtpa) to an optimistic high of 100Mtpa. Unless technology Green steelmaking will need technology and mining advances
احصل على السعر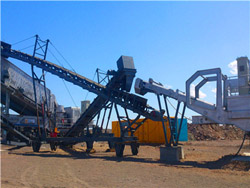
Hongxing Offers the Best Iron Ore Processing Plant CSDN博客
The most commonly used crushers and grinding mills in iron ore crushing and grinding process for iron ore mining are jaw crusher, cone crusher, hammer crusher and ball mill, ultrafine grinding mill, etc. In iron ore mining, miner usually choose a complete iron ore crushing plant for metallurgy.Technological cycle of iron ore crushing and grinding under production conditions is possible only in terms of mechanical load being rather labour-consuming and energy-intensive. Application of physical impact methods on iron ore to intensify its crushing and grinding processes is still at the stage of research and development [9].Research into the crushing and grinding processes of iron ore
احصل على السعر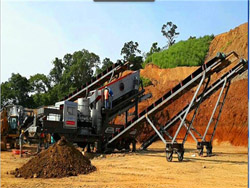
Special Issue "Grinding Modeling and Energy Efficiency in Ore
It has been estimated that grinding consumes up to 4% of global electrical energy and accounts for more than 50% of the total energy used in mining operations. In addition, more than 90% of the total energy supplied in beneficiation plants is dissipated as heat, kinetic energy, noise, and inefficient breakage of ores/raw material.Iron ore screening process: Iron ore screening equipment generally uses a circular vibrating screen to screen the materials after the second crushing. Generally, materials with a size of 10mm or less can be screened for dry selection. After screening, materials with a size of 10-40mm enter the fine crusher for fine crushing.Iron ore crushing and screening process TY Ultrafine Powder
احصل على السعر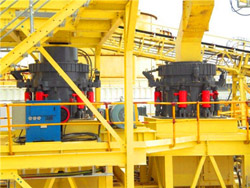
Transforming iron ore processing ScienceDirect
Much of the remaining iron ore resources in Brazil consist of low-grade itabirite ores. Accordingly, a typical beneficiation circuit includes a four-staged crushing/screening plant, followed by grinding in a closed-circuit ball mill, desliming in hydrocyclones and final ore mineral concentration via multistage reverse flotation and Option 2 has an additional grinding and magnetic separation stage compared to Option 1 and is considered to be simple for design and operation. The final milling stage is carried out using energy-efficient stirred mills. Steel grinding media usage significantly increases the operating cost. Option 3.Eco-efficient and cost-effective process design for magnetite iron ore
احصل على السعر
Minerals Free Full-Text Recovering Iron from Iron
Iron ore tailings (IOTs) are a form of solid waste produced during the beneficiation process of iron ore concentrate. In this paper, iron recovery from IOTs was studied at different points during a process But the scale of the change is huge. To eliminate coal from steel making would need about 80 m tonnes of hydrogen and from ammonia another 25-30m tonnes of H2 would require about 7,500 TWh notGreen steelmaking needs urgent advances in technology and mining
احصل على السعر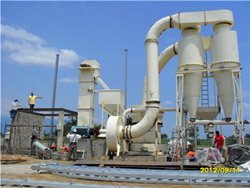
Existing and New Processes for Beneficiation of
Besides that, the document “Vision 2020” published by Indian Bureau of Mines has stated that the threshold of iron ore mining is 45% Fe. Accordingly, iron ores with minimum 45% Fe cannot be Browse 470 iron ore processing photos and images available, or search for iron ore mining to find more great photos and pictures. Browse Getty Images' premium collection of high-quality, authentic Iron Ore Processing stock photos, royalty-free images, and pictures. Iron Ore Processing stock photos are available in a variety of sizes and formats470 Iron Ore Processing Stock Photos & High-Res Pictures
احصل على السعر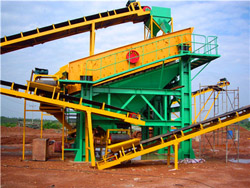
Iron Ore Crusher Mining, Crushing, Grinding, Beneficiation
Iron ore processing can be a procedure that contains explosions, shoveling, moving, crushing, grinding, pelletizing etc. Iron ore processing provides a range of coarse sizing that may produce material in 24-inch to .0017-inch particle sizes. In iron ore crushing and screening process is really a basic connect to concentrator will have an Iron ore handling, which may account for 20–50% of the total delivered cost of raw materials, covers the processes of transportation, storage, feeding, and washing of the ore en route to or during its various stages of treatment in the mill.. Since the physical state of iron ores in situ may range from friable, or even sandy materials, to monolithic Iron Ore Processing, General SpringerLink
احصل على السعر
Brazilian miner Vale opens 'green' iron ore grinding hub in China
The grinding hub is generating a completely new product, known as GF88. According to Vale, GF88 is a high-grade ground iron ore fine that uses the company’s flagship Carajás Fines as raw material. It provides an eco-friendly solution for pellet production. Vale Ferrous Minerals executive director Marcello Spinelli, who virtually In iron ore mining, for example, However, in copper mining, crushing and grinding are the most energy-intensive parts of the production chain and are the main contributors to its GHG emissions 4.Transparency on greenhouse gas emissions from mining to enable Nature
احصل على السعر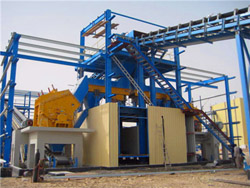
Trends in der Minenindustrie Mineral Processing
Today, HPGRs are some of the most important types of mill in the mining industry. From the market leader thyssenkrupp alone, so far more than 130 roller crushers have been sold for a range of different applications, such as grinding diamond ore/kimberlite, iron ore or iron ore concentrate and metal ores (hard rock).Iron ores obtained from different sources differ in their chemical and physical properties. These variations make the process of grinding a difficult task. The work carried out in this context focuses on three different samples of iron ore, viz., high silica high alumina, low silica high alumina, and low silica low alumina. The grinding process for all Estimation of Grinding Time for Desired Particle Size Distribution
احصل على السعر- مصنع معدات فرز الرمال فى مصر
- مطحنة الشركة المصنعة مصدقة
- bosniak in bosnia herzegovina joshua project
- في التسويق لشركات التعدين في غانا
- كسارة مطرقة الكالسيت
- ماين كرافت كيف تصنع رمل الروح
- conveyor belts hartl crusher
- حذافة في كسارة الفك
- مبدأ طريقة مطحنة الكرة
- معدات الرفع بالطين للتأجير
- jaw crusher of high performance price ratio for sale
- الصين تشونغ يوان كسارة
- 11592 الحزام الناقل Pdf مجاني
- أخذ العينات معدات التعدين
- small underground crushers