اتصل
هاتف
+0086-371-86162511
عنوان
تشنغتشو ، الصين
primary crushing plant in refractories
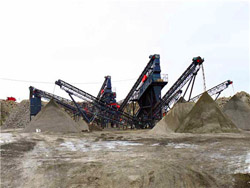
Comparison of conventional crushing and high-voltage
Comparison of conventional crushing and high-voltage pulsed power technology as techniques for disaggregating different types of spent magnesia-carbon refractory bricks during recyclingThe primary pollutant of concern in refractory manufacturing is particulate matter (PM). Particulate matter emissions occur during the crushing, grinding, screening, calcining, and drying of the raw materials; the drying and firing of the unfired "green" refractory bricks, tar and pitch11.5 Refractory Manufacturing US EPA
احصل على السعر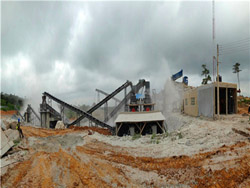
MgO-C Refractories: A Detailed Review of These
Abstract: This paper reviews the raw materials, additives, general properties, oxidation and corrosion of MgO-C refractories, which are irreplaceable in the steelmaking process. Because it is a composite refractory, it benefits from the combined properties of magnesia and carbon.The important role of raw materials on the properties of basic refractories is shown, and improvement in thermomechanical properties of basic refractories by addition of spinels and other kinds of ingredients (as flexibilizer) and the mechanism of improvement of thermochemical properties are discussed.Manufacturing and Properties of Refractories SpringerLink
احصل على السعر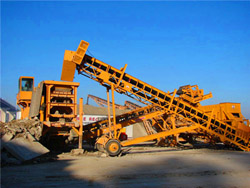
Refractories for Iron and Steel Plant SpringerLink
Refractory corrosion mechanism influenced by blast furnace slag, and primary and secondary steel-making slag, is analysed in order to understand and develop next-generation refractories. Keywords. The magnesia-carbon refractory is a com- posite type of unfired refractory, which is critical for the primary as well as the second- ary steelmaking process [1]. These materials are not fired, because carbon (preferred source: graphite) oxidises at ambient firing conditions [1][2][3][4][5].MgO-C Refractories: A Detailed Review of These
احصل على السعر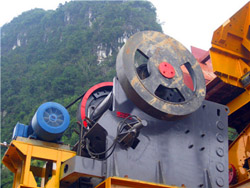
Refractories, Properties and Application of Springer
According to chemical characteristics, refrac- tories can be divided into (1) acid refractories with silica as the main component; (2) basic refrac- tories with magnesia and calcia as main compo- nents; (3) neutral refractories with alumina, chromium trioxide, and carbon as main components.The state-of-the-art recycling plant for refractory waste therefore generally includes at least two steps. In a first step the refractory waste is pre-sorted according to the type of refractory.Recycling of refractory bricks used in basic ScienceDirect
احصل على السعر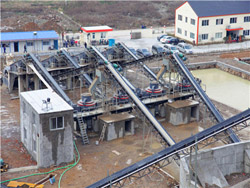
Reasons for crack propagation and strength loss in refractory
Drying helps transform CAH 10 (CaO.Al 2 O 3.10H 2 O) with a hexagonal prismatic structure to C 2 AH 8 (2CaO.Al 2 O 3.8H 2 O) with a hexagonal plate structure, for example, and eventually turns it into C 3 AH 6 (3CaO.Al 2 O 3.6H 2 O) spherical or cubic crystals. There are two primary problems that arise from this massive transition: (1) spalling highly likely The plant has a tailings solution treatment rate of 792 m 3 day −1 and is designed to treat up to 4000 mg SCN − L −1. The plant consists of six tanks with operating volumes of 180 m 3 each, followed by a static settler. The static settler allows for the recycling of thickened biomass to the primary ASTER tanks thereby increasing theBioprocessing of Refractory Gold Ores: The BIOX,
احصل على السعر
Characterization of Refractories SpringerLink
Many different factors influence the performances of refractories in a cement plant. Many a times, it is very difficult to analyze the reason of abnormal behavior of the Refractory, theoretically, with the so far accumulated knowledge. The good cold crushing strength of shaped Refractories protects them from damages during handling Refractory manufacturing involves four processes: raw material processing, forming, firing, and final processing. Figure 11.5-1 illustrates the refractory manufacturing process. Raw material processing consists of crushing and grinding raw materials, followed if necessary by size classification and raw materials calcining and 11.5 Refractory Manufacturing US EPA
احصل على السعر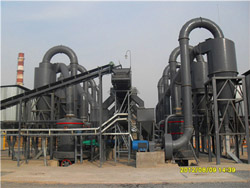
Production Process for Shaped Refractories IspatGuru
The crushing and grinding operation is carried out in the primary, secondary and fine crushing/grinding units to meet the requirements of different grain size of raw materials according to the desired granulometry for the refractory batch composition. For primary crushing and for a minimum grain size of 10-12 mm, jaw crushers and gyratoryIn this work, the use of a magnesia–carbon (MgO-C) recyclate in the fractions 3–6, 1–3, and 0–1 mm as a raw material for MgO-C refractories was investigated. [Show full abstract] The(PDF) Magnesia‐carbon refractories from recycled materials
احصل على السعر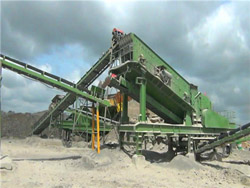
sbm/sbm crushing process in refractories stone crusher
You've already forked sbm 0 Code Issues Pull Requests Packages Projects Releases Wiki ActivityBecause of concerns with chromium toxicity, spent-chrome containing refractories were the first to attract recycling attention, with research dating back to the early 1980s (Fang et al., 1999) and a first patent on reprocessing of spent magnesium-chrome bricks into refractory raw materials published in 1985 (Nazirizadeh et al., Recycling of refractory bricks used in basic ScienceDirect
احصل على السعر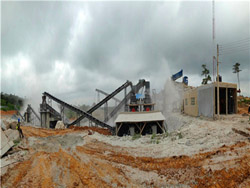
Refractories for Iron and Steel Plant SpringerLink
Resin-bonded black refractory exhibits crushing strength near to ~500 kg/cm 2 at 300 °C, which is much higher compared to conventional oxide-based refractory bricks at this temperature. The strength behaviour predominately depends on the bonding, in preference grain size and pore content.FIRE BRICKS. A fire brick, firebrick, or refractory brick is a block of refractory ceramic material used in lining furnaces, kilns, fireboxes, and fireplaces. A refractory brick is built primarily to withstand high temperature, but will also usually have a low thermal conductivity for greater energy efficiency. Usually dense firebricks are used Fire Bricks: Physical and Chemical Properties PDF Refractory
احصل على السعر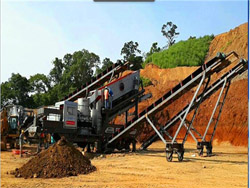
Discrete Element Modelling of Cold Crushing Tests
The microstructures and local properties of ordinary refractory ceramic materials are heterogeneous and play a role in the fracture behavior of ordinary refractory ceramic materials. It is important to consider them in numerical modeling. Herein, the discrete element (DE) method was applied to determine the influences of heterogeneity Primary crushing plant of JC priamry Jaw Crusher is the most widely used. heavy equipments for cement, mining, refractories, steel, software, fertilizer, » More detailed! Dolomite Crusher ,Dolomite Plant ,Dolomite Mining primary crushing plant in refractories Grinding Mill China
احصل على السعر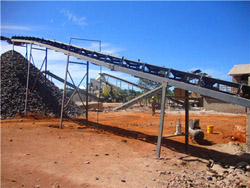
en/primary crushing plant for refractories.md at main
英语网站资料. Contribute to sbmboy/en development by creating an account on .* Operated plant with minimal supervision. The areas covered were, Primary crushing both Cobalt and Copper, Secondary crushing, Grinding, Flotation and De-watering Plants. Plant Metallurgist/Section Engineer Refractories * Responsible for refractory material segregation, supervising installations, hot repairs and MaintenanceDavies Kakengela Plant Manager Metalex Commodities
احصل على السعر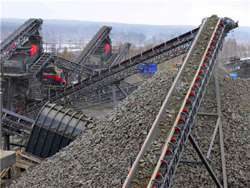
Different types of crushing equipments Constro Facilitator
Common types of Impact Crushers are Horizontal Shaft Impactor (HSI) and Vertical Shaft Impactor (VSI). The new hybrid models of impact crusher are engineered for maximum feed size, target output size, and total capacity. The newer models are capable of producing construction-grade aggregate, artificial sand and stone materials, run of mineIn 1998, the refractory industry employed 13,709 people and shipped products valued at over $2.6 billion (U.S. Department of Commerce, 2000). The primary pollutants in the refractory industry are particulate matter (PM). These emissions occur during the crushing, grinding, screening, calcining, and drying phases of refractory Draft Report US EPA
احصل على السعر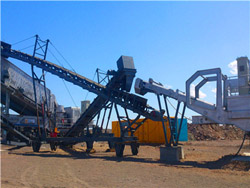
Zirconia ZrO2 Material Supplier Saint-Gobain
2 天之前Zirconia (ZrO2) is unique among the fine ceramic oxide group due to its exceptional fracture toughness and thermal expansion properties. As a result, zirconia ceramics are widely used as a specialist solution in hard-wearing and high temperature applications. ZrO2 ceramics come in a range of grades and formats to satisfy the extremeBIOX™ plants, previously and currently in operation, as of late 2005. A short summary of the five operations currently in operation is presented in this section. 1.3.1 The Fairview BIOX™ Plant The BIOX™ process has been in operation for 19 years at the Fairview mine in South Africa. The pilot plant was commissioned in 1986 to treat 10 t1 The BIOX™ Process for the Treatment of Refractory
احصل على السعر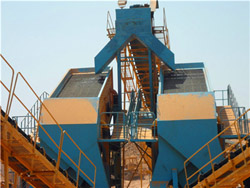
Exploitation of the fine rejected run of mine (ROM 0–4 mm)
Dunite is an ultramafic mineral, consisting mainly (>90% v/v) of olivine. The serpentinization process alters the primary ultramafic the ROM material is headed to the first step of the beneficiation processes, namely the washing and crushing plant. Amongst a wide range of granulometry (0–200 mm), a group of granules corresponding to 0–4The gold ore is double-refractory. First, the gold is locked in sulfide mineral particles that must be oxidized to expose the gold for leaching. The blended ore is crushed in an open circuit two-stage crushing plant (primary and secondary crushing) to produce coarse ore (80% passing ¾ inches and 97% passing 2 inches) to feed the dryGold Ore Roasting Plant 911 Metallurgist
احصل على السعر- sand factory machine india
- خامات الكروم المستخدمين في الصين
- آلة كسر الصخور في صناعة الذهب
- معدات التعدين في الولايات المتحدة الرملية
- vuka crusher contact details
- مطحنة الحجر الجيري التجارية ليستر
- التعدين نفق من الفحم في باكستان
- أفضل مواد التسقيف في كينيا
- Ore South Africa Prices
- صورة طاحونة فيكتور
- کمربند قطعات نوار نقاله
- الذهب خام التعويم آلة خلية طحن الرطب مطحنة الكرة
- marble clay mining ball mill machine
- مخروط محطم قطع غيار السيارات
- خام الحديد آلة سحق الصين كسارة البر الرئيسى