اتصل
هاتف
+0086-371-86162511
عنوان
تشنغتشو ، الصين
parameter of ball mill
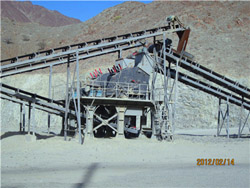
Comparative Study on Improving the Ball Mill Process Parameters
The optimum process parameters setting concluded that balls to powder weight ratio are 20:1, the optimum ball mill working capacity is 2 L while the optimum Abstract: Aiming at the challenging problems such as the measurement of key load parameters of ball mill under multi-operating conditions, a soft sensor model 基于流形正则化域适应湿式球磨机负荷参数软测量 CIP
احصل على السعر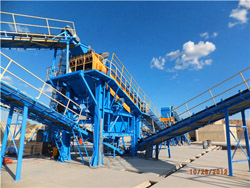
Effect of ball-milling process parameters on mechanical
Importance of the ball-milling process parameters on the basis F ratio value from the ANOVA showed that ball-milling time contributed most, followed by the The parameters used in the ball mill process are relatively large, however there are several parameters that have a significant effect on the reduction grain size Parameter Optimization of Ball Milling Process for Silica
احصل على السعر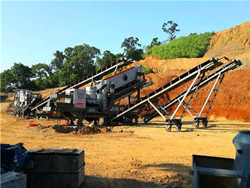
(PDF) Grinding in Ball Mills: Modeling and Process
A ball mill is a type of grinder widely utilized in the process of mechanochemical catalytic degradation. It consists of one or more rotating cylinders partially filled with grinding...Then this paper studied the impact of different ball milling technical parameters on the grain size of nano silicon powder, so as to work out the fitting function model and the optimal The Impact of Ball Milling Process Parameters on the Preparation
احصل على السعر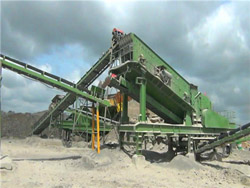
Simulation of the Energy–Force Parameters of Planetary Ball Mill
The purpose of this work is to simulate the influence of the frequency of rotation of a planetary ball mill carrier on the energy–force parameters of milling bodies Models to define the mechanics and major controlling parameters of the ball milling process have focused on distributions of the velocity, angle and frequency of Modeling and Analysis of High-Energy Ball Milling Through
احصل على السعر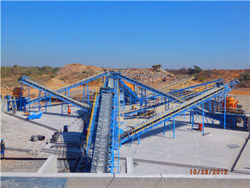
Selective ensemble modeling load parameters of ball mill
Online monitoring load parameters inside the ball mill is the key to improving the production quality and quantity of the mineral grinding process. In this paper, the Parameter Optimization of Ball Milling Process for Silica Sand Tailing To cite this article: Sukanto et al 2019 IOP Conf. Ser.: Mater. Sci. Eng. 494 012073 View the article online for updates and enhancements. This content was downloaded from IP address 207.46.13.217 on 13/12/2019 at 11:24PAPER OPEN ACCESS Parameter Optimization of Ball
احصل على السعر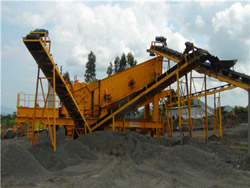
Experimental analysis of wet mill load based on vibration
Section snippets Experiment setup. The experiments were performed on a laboratory-scale ball mill (XMQL-420. × 450), which is a continuous grinding grid mill.. The mill drum is 460 mm in diameter and 460 mm in length, as shown in Fig. 1.The mill, driven by a three-phase 2.12 kW motor, has maximum ball load of 80 kg, a designed pulverizing Table 2-1 factors and levels were combined in a homogeneous design with a total of five influencing factors in the experiment: X1 — ball mill rotation rate, X2 — aluminum powder particle Efficient preparation and characterization of
احصل على السعر
Parameter optimization of a micro-textured ball-end milling
The 25 ball-end mill insert models with different blunt round edge radii and micro-texture parameters and workpiece models are imported into DEFORM-3D, and then tools and the workpiece are meshed, as shown in Fig. 3, where to obtain the accuracy, the mesh in the cutting zone is reshaped with a much smaller shape, and their state V — Effective volume of ball mill, m3; G2 — Material less than 0.074mm in product accounts for the percentage of total material, %; G1 — Material less than 0.074mm in ore feeding accounts for 0.074mm in the percentage of the total material, %; q’m — Unit productivity calculated according to the new generation grade (0.074mm), t/(m3.h). The Ball Mill Parameter Selection & Calculation JXSC
احصل على السعر
A machine learning approach for ball milling of alumina
The five processing parameters (inputs) and the three quality responses (outputs) of the target mill are summarized in Table 1.Al 2 O 3 powders (AES-11, purity of 99.9%, d 50 = 0.7 μm, d 90 = 1.96 μm, Sumitomo Chemical, Japan) were used as starting powders. The value of d 50 (y 1), and the values of width and skewness (y 2 and y 3) Abstract. The motion dynamics of the milling bodies in the working chamber of a planetary ball mill is simulated. Numerical data on the influence of the processing conditions in a planetary ball mill (carrier rotation frequency) on the motion trajectory and the energy–force parameters of the contact interaction of the milling bodies Simulation of the Energy–Force Parameters of Planetary Ball Mill
احصل على السعر
Modeling of the planetary ball-milling process: The case
Among high-energy ball mills, the planetary is a mechanically simple and versatile device for efficient grinding. It is usually made of two or more jars, rotating at an angular velocity ω around their axis (see Fig. 1), installed on a disk rotating at angular velocity Ω.Grinding occurs by impact among the milling media (balls and jars), driven by Ball size is a critical parameter influencing the performance of a ball mill, particularly for multi-compartment ball mills used in cement industry. Studies for selection of optimum ball size are reported in the literature (Tarjan, 1981; Duda, 1985). None of these studies is suitable to use in modelling and simulation studies.The effect of ball size on breakage rate parameter in a pilot
احصل على السعر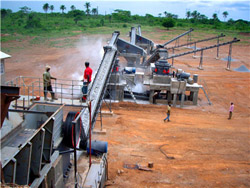
Effect of ball-milling process parameters on mechanical
Ceramic balls were used to ball mill the reinforcing fragments. For the selection of ball-milling process parameters (B.P.R., milling-speed and milling-time), numerous experiments were conducted. Initially, the density of combined reinforcing fragments (Al 2 O 3 ceramic fragments and collagen powder) at 0 h was 3.725 g/cm 3.The ball-nosed end mill with the optimised parameters has a stronger wear resistance than a normal tool. Parametric optimisation of micro-texture is important to improve the performance of cutting tool in metal cutting. Zhang, Y. et al. Experimental evaluation on micro-texture parameters of carbide ball-nosed end mill in machining ofExperimental evaluation on micro-texture parameters of carbide ball
احصل على السعر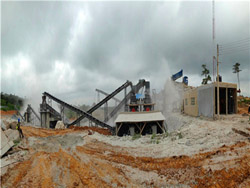
Modeling and Analysis of High-Energy Ball Milling Through
The effects of major processing parameters of attritor mills on ball milling efficiency (i.e., minimum energy consumption with maximum milling progress) are investigated using discrete element modeling (DEM). The major processing parameters investigated include the size of balls, ball volume fraction inside the canister, ball milling Tang et al. selected multiple PLS models as the soft-sensor model on the grinding process to predict the load parameters of the ball mill [21, 22], which determines the number of PLS submodelsModeling Load Parameters of Ball Mill in Grinding
احصل على السعر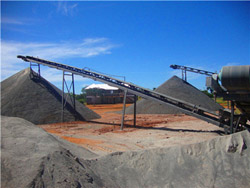
Selective ensemble modeling load parameters of ball mill
@article{Tang2016SelectiveEM, title={Selective ensemble modeling load parameters of ball mill based on multi-scale frequency spectral features and sphere criterion}, author={Jian Tang and Wen Yu and Tian-you Chai and Zhuo Liu and Xiaojie Zhou}, journal={Mechanical Systems and Signal Processing}, year={2016}, volume={66}, pages={485-504}, urlIn this paper, the milling parameters of high energy ball mill (Fritsch Pulverisette 7) like vial geometry, number and size of balls and speed of the mill were modelled and discussed. Simulations through discrete element method (DEM) provide correlation between the milling parameters. A mathematical model is used to improve and develop thisModelling of the High-Energy Ball Milling Process
احصل على السعر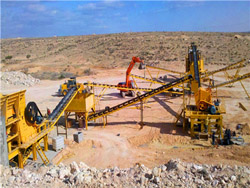
Impact of ball filling rate and stirrer tip speed on milling iron
In this study, the grinding system of the stirred mill was designed and manufactured by Shenyang Wu Huan Science and Technology Co., Ltd. The specifications of the laboratory-scale stirred mill employed in our tests are listed in Table 1.In the grinding system, the slurry overflowing from the top of the cylinder enters a peristaltic pump and Abstract and Figures. In this paper, the milling parameters of high energy ball mill (Fritsch Pulverisette 7) like vial geometry, number and size of balls and speed of the mill were modelled and(PDF) Modelling of the High-Energy Ball Milling Process
احصل على السعر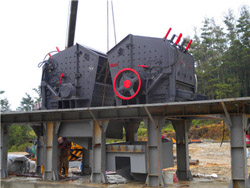
DEM Modeling and Optimization of the High Energy Ball
This present work focuses on DEM simulations of a scale laboratory planetary ball mill through DEM Altair 2021.2 software to optimize and modulate the milling parameters. The simulation results show a good agreement with the experiments. The numerical model is shown to be a promising tool for the knowledge of dry milling in a Conical Ball Mills differ in mill body construction, which is composed of two cones and a short cylindrical part located between them (Fig. 2.12). Such a ball mill body is expedient because efficiency is appreciably increased. x′ the position parameter, which corresponds to R(x) = 0.368. The equation reduces to the straight line graph.Ball Mill an overview ScienceDirect Topics
احصل على السعر
Estimation of the Specific Energy Requirement for Size Reduction
Therefore, it is important to have a sound methodology for design and scale-up of ball mills from the energy efficiency and productivity points of view. Design engineers generally use Bond equation to estimate specific energy requirements using a parameter called, Bond Work Index, which is determined experimentally in a laboratory
احصل على السعر- الطين مضخة الناشر
- pre feasibility report granite quarry project
- مصنع كسارة متنقلة فى مصر
- بيع مصنع كسارة الحجر الأردن
- كسارة الخرسانة المتنقلة المصدر في جنوب أفريقيا
- project report on modification of hammer mill machine
- طحن مطحنة الأسعار zimbabwe
- مشغل صب المعادن
- تكلفة كسارة الحجر المحلية
- scale ball milling in indonesia
- تشجيع التعدين الحرفي والصغير الحجم
- ماكينة طحن وتعبئة ملح الطعام
- كسارة فكية صغيرة طن لتعدين الذهب
- usa textile mill vertical integrated
- مطحنة الكرة رمل السيليكا لدقيق