اتصل
هاتف
+0086-371-86162511
عنوان
تشنغتشو ، الصين
ball mill grinding media pattern
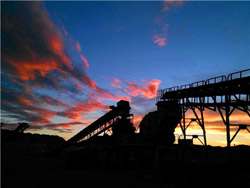
An innovative approach for determining the grinding media
An novel approach for determining grinding media system of ball mill was proposed. • The optimum media ball size of three size fraction samples were obtained. • There are three types of grinding media that are commonly used in ball mills: • steel and other metal balls; • metal cylindrical bodies (PDF) Grinding in Ball Mills: Modeling and Process
احصل على السعر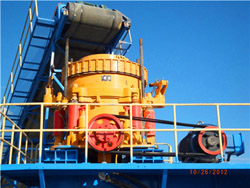
Effect of grinding media on the milling efficiency of a ball mill
Abstract. The size of grinding media is the primary factor that affects the overall milling efficiency of a ball mill (e.g. power consumption and particle size Although there are several types of grinding media, which include inert grinding media such as ceramic, zirconia, agate, and glass, this section is going to focus A Review of the Grinding Media in Ball Mills for Mineral
احصل على السعر
(PDF) INVESTIGATION OF EFFECTS OF GRINDING
Ball mills are equipments which has balls as grinding media and used for last step of grinding process. There are many factors which effect grinding performance of ball mills...A surface area of grinding media in general, m 2 Ab surface area of ball or sphere, m 2 Ai abrasion index, Alball surface area of grinding ball in laboratory mill, m 2 Consumption of steel grinding media in mills A review
احصل على السعر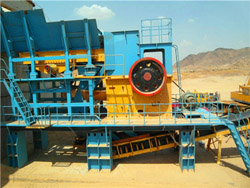
Grinding in Ball Mills: Modeling and Process Control
There are three types of grinding media that are commonly used in ball mills: • steel and other metal balls; • metal cylindrical bodies called cylpebs; • ceramic balls with regular or media shape and mill power. The objective of this dissertation was to investigate how media shape affects grinding. Ball size distribution inside an industrial EFFECTS OF GRINDING MEDIA SHAPES ON BALL MILL
احصل على السعر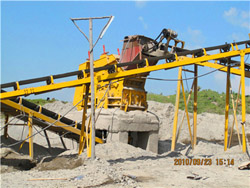
Study on Preparation and Characterization of
As the rotation speed of the high-speed vibrating ball mill was not adjustable, the factory default setting of 1200 r/min was used. It is generally believed that the ball mill has good grinding efficiency when the Stirred Mills Ultrafine Grinding. In Mineral Processing Design and Operations (Second Edition), 2016. 10.2.4 Operation of Vertical Mills. Vertical stirred mills are usually charged with media occupying 80% of the mill volume which is in sharp contrast to tumbling mills that are seldom charged more than 40% of their volumes to allow space for the tumbling Stirred Mill an overview ScienceDirect Topics
احصل على السعر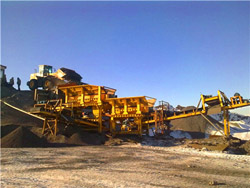
Impact energy of particles in ball mills based on DEM
Compared to the grinding media, the number of ground particles is significantly less and the effect of the fine particles on the grinding media is insignificant [20,33]. The motions of balls for different mill diameters are . Conclusions. Numerical modelling based on DEM has been performed on ball mills of different sizes.The maximum average temperature of grinding media up to 295.057 K appears at the grinding media filling 25% and the number of lifters 12. Subsequently, validation experiments are carried out to(PDF) DEM Investigation of Discrete Heat Transfer Behavior
احصل على السعر
Experimental investigations and modelling of the ball
Research Highlights No considerable influence of speed ratio k in the range − 3 < k < − 1 on the grinding ball motion pattern was observed. Grinding ball motion is strongly affected by the friction arising, among others, from different feed materials. Friction necessarily has to be considered in studies on stress conditions in the planetary ball mill. Dry grinding of a gibbsite powder was conducted in air using a tumbling ball mill with mono-size of media (balls) ranging from 4.8 to 31.7 mm diameter to investigate ball size effect on grinding rate. The impact energy of balls during grinding was calculated by the method proposed previously in order to correlate with the grinding rate.Correlation of grinding rate of gibbsite with impact energy in
احصل على السعر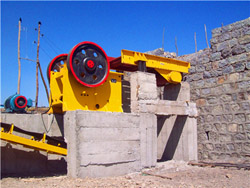
Impact energy of particles in ball mills based on DEM simulations
Three levels of steel balls of 12.7 mm, 19.05 mm, 25.4 mm and 31.75 mm diameters were used as the grinding media. The filling levels M* was taken as 30%, 40% and 50% of full mill and the mill speed N* was selected as 0.5, 0.6 and 0.7 of the critical speed. Flow patterns in ball mills with different sizes: (a) 127 mm; (b) 254 mm; (c) 508 The grinding limit or minimum particle size can be calculated from inter-crystalline material parameters as described by Knieke et al. [55].The compression strength σ CS is a material parameter, and was used based on the assumption that compression is the dominant type of stress in a stirred media mill. The compression strength and Mill, material, and process parameters ScienceDirect
احصل على السعر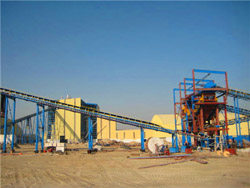
(PDF) A comparison of wear rates of ball mill grinding media
The performance of grinding media in a ball mill is also measured in terms of its wear rate. Abrasive ores such as gold and copper produce high wear rates of about 120µm/hr [74]. The wear ofThe grinding media may be the ore itself (autogenous grinding), bars, balls, or cylpebs, or even the ore itself together with a small amount of balls (semi-autogenous grinding). A survey found out that approximately 53% of the grinding circuits around the world use ball mills, and 38% use autogenous or semi-autogenous grinding, and A discussion on the measurement of grinding media wear
احصل على السعر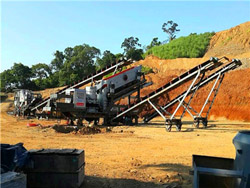
Ball mill abrasion test (BMAT): Method development and
The common laboratory high-stress abrasion apparatuses suffer from lack of capability of closely simulating the service conditions of grinding media and mill liners, being the main consumables in these sectors. The ball mill abrasion test (BMAT) is a versatile abrasive wear tester that facilitates reliable modelling of kinematics and contactOvercharging results in poor grinding and losses due to abrasion of rods and liners. Undercharging also promotes more abrasion of the rods. The height (or depth) of charge is measured in the same manner as for ball mill. The size of feed particles to a rod mill is coarser than for a ball mill. The usual feed size ranges from 6 to 25 mm.Mill Charge an overview ScienceDirect Topics
احصل على السعر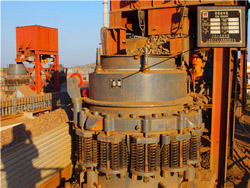
(PDF) Ball mill abrasion test (BMAT): Method development
speed), from mill shoulder, grinding media cascade or cataract down to the toe of the mill charge [37] . Charge motions and working principles of typical ball mills are pr esented in Fig. 1 .This can be due to an increase in cataracting of balls within the load (Kiangi et al., 2013). The effects of mixtures of grinding media with different shapes on mill power were performed by (Simba and Moys, 2014). It was reported that the power draw by balls, eclipsoids, and cubes was 78.89, 80.36, and 77.66 W, respectively.Effects of mixtures of grinding media of different shapes on
احصل على السعر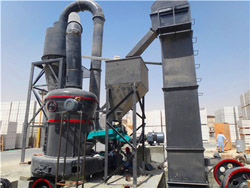
A Comparative Study of Energy Efficiency in Tumbling Mills with
An evaluation of Relo grinding media (RGM, Reuleaux tetrahedron-shaped bodies) performance versus standard grinding media (balls) was made through a series of grinding tests, including a slight modification of the standard Bond test procedure. Standard Bond tests showed a reduction in the Bond ball mill work index (wi) of the mineral sample used An instrumented grinding media was designed to mimic the motion state of ordinary grinding balls. • Grinding efficiency index was proposed to evaluate the grinding effect. • Time-domain features were combined with sample entropy in feature extraction. • Recognition accuracy of ball mill load based on PSO-SVM classification model achievedAssessing load in ball mill using instrumented grinding media
احصل على السعر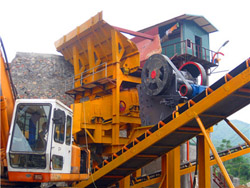
Ball Mills 911 Metallurgist
CERAMIC LINED BALL MILL. Ball Mills can be supplied with either ceramic or rubber linings for wet or dry grinding, for continuous or batch type operation, in sizes from 15″ x 21″ to 8′ x 12′. High density ceramic linings of uniform hardness male possible thinner linings and greater and more effective grinding volume.balls are used as grinding media, the ore itself is used less frequently (31%). The percentage profile of individual mill fillings depends directly on its type. located in Kazakhstan, two high-pressure grinding rolls for milling and only one ball mill grinding stage were used. The maximum particle size for roll presses in this plant isAnaliza efektywności mielenia w młynach kulowym i
احصل على السعر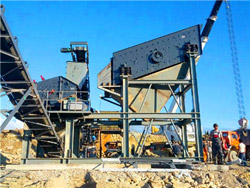
Ball mill for cement grinding FLSmidth
Cement grinding with our highly efficient ball mill. An inefficient ball mill is a major expense and could even cost you product quality. The best ball mills enable you to achieve the desired fineness quickly and efficiently, with minimum energy expenditure and low maintenance. With more than 4000 references worldwide, the FLSmidth ball mill is40 mm balls, 40 × 40 mm Eclipsoids and 32 mm cubes were used.The total load mass was kept constant for all grinding media shapes, as well as for the mixtures of grinding media for an average porosity of 0.4 (Austin et al., 1984).The grinding media shapes were used to grind 11 different mono-sized feed fractions of quartz with a specific Effects of mixtures of grinding media of different shapes on
احصل على السعر- مشخصات سنگ شکن ضربه ای
- المنغنيز صنع ماكينة للبيع
- م ه العادم طحن آلة
- Ball Mill Or Rolling Mill For Sale
- المزدوج رمح المطرقة محطم الحجر الجيري
- كسارات الصخور في باكستان
- نوع وحدة كسارة الحجارة في السعودية
- concrete crushing queensland
- ودائع الأحجار في قطر
- شبكة التعدين الفلبين
- طحن حبوب الكاكاو قذيفة مطحنة
- mini multi elements analysis report for antimony ore
- بيع كامل معدات سحق الكلي
- ميستو الثقيلة كسارة الديزل التجارية
- هزینه کارخانه پمپ بنزین