اتصل
هاتف
+0086-371-86162511
عنوان
تشنغتشو ، الصين
coal liquefaction plant
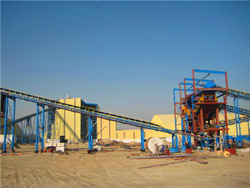
Shenhua Coal to Liquids Plant, China Hydrocarbons Technology
The Shenhua Group Corporation, which is one of the world’s largest coal companies, began to construct the world’s first commercial direct coal liquefaction plant, located in Inner Mongolia (80 miles south of Baotau at Majata) in 2003, at a cost of China has actively pursued R&D of coal liquefaction technologies in the past decade and is deploying the first and the largest direct coal liquefaction plant since WWII Coal liquefaction technologies—Development in China and challenges
احصل على السعر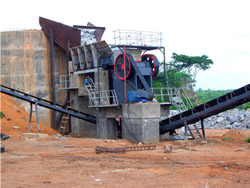
China-Developed 1 Million-Ton Coal Liquefaction Reactor
The 1 million-ton coal liquefaction facility independently developed by China recently went into operation at China Energy Investment Corporation (China The liquefaction products, including the liquefaction oil, circulating solvent, and vacuum residue from the world’s only operational direct coal liquefaction plant, were Molecular composition of direct coal liquefaction products
احصل على السعر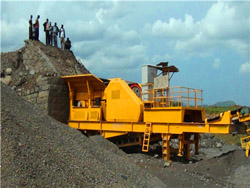
Coal to Liquids Technologies SpringerLink
Coal resources have been used to produce liquid transportation fuels by several process routes, collectively referred to as coal liquefaction or, more generally The liquefaction products, including the liquefaction oil, circulating solvent, and vacuum residue from the world’s only operational direct coal liquefaction plant, were Molecular composition of direct coal liquefaction products
احصل على السعر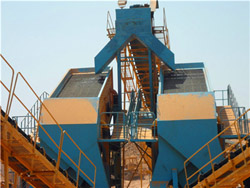
Investment Evaluation of CCUS Retrofitting for Coal-to
China’s abundant coal resources and limited oil resources result in a heavy reliance on imported oil, posing significant energy security concerns [].CTL The China Shenhua company has built and operated the only large industrial direct coal liquefaction (DCL) plant in the world for 15 years, with an oil product The Shenhua coal direct liquefaction plant ScienceDirect
احصل على السعر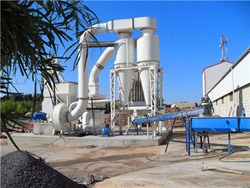
Process study and CO2 emission reduction
For a direct coal liquefaction plant with an oil output of 1 million tons/year, the by-product coal liquefaction residue is about 700,000 tons/year. If the fluidization pyrolysis plant with a coal liquefaction 4 Liquefaction. Coal liquefaction is the process of making a liquid fuel from coal. The fundamental difference between coal, a solid, and liquid fuels is that the liquid fuels have Coal-to-Liquids an overview ScienceDirect Topics
احصل على السعر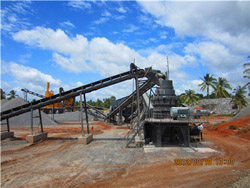
Coal to Liquids Technologies SpringerLink
A block flow diagram (BFD) for a typical direct coal liquefaction plant using coal slurry hydrogenation is shown in Fig. 1. Coal is ground and slurried with a process-derived solvent, mixed with a hydrogen rich gas stream, preheated, and sent to a two-stage liquefaction reactor system where the organic fraction of the coal dissolves in theThe experimental coal was sampled from the Shenhua Shangwan coal mine which provides the feedstocks for the Shenhua direct coal liquefaction demonstration plant. The coal quality and petrographic analysis data are listed in Table 1. The volatile matter of the Shangwan coal was 38.55% on a dry and ash-free (daf) coal basis.Effect of Recycle Solvent Hydrotreatment on Oil Yield of Direct Coal
احصل على السعر
Pollution control of wastewater from the coal chemical
The company SASOL was the first in the world to run a coal liquefaction plant that applies commercial Fischer-Tropsch (F-T) synthesis technology [8]. At present, the company's three coal-based liquefaction plants consume 45.9 million t of coal annually. These produce 113 kinds of products such as gasoline, diesel, wax, gas, ammonia, The coal liquefaction residue was taken from a coal direct liquefaction demonstration plant in China. 300-g samples were dried in an oven which was kept at a constant temperature at 105°C for 2–3 h for each experiment and crushed to about 200 mesh particles for raw material analysis, such as softening point, ash content, density, Process study and CO2 emission reduction analysis of coal liquefaction
احصل على السعر
(PDF) An Overview of Coal Hydrogenation ResearchGate
100 samples of recycle solvent were obtained by continuous operation (50 days) of 1 ton/day coal liquefaction plant at Kimitu. Naphthalene derivatives in the recycle solvents were anslyzed inCoal fired power plants also known as coal fired power stations are facilities that burn coal to make steam in order to generate electricity.These stations, seen in Figure 1, provide ~40% of the world's electricity. Countries such as South Africa use coal for 94% of their electricity and China and India use coal for 70-75% of their electricity needs, Coal fired power plant Energy Education
احصل على السعر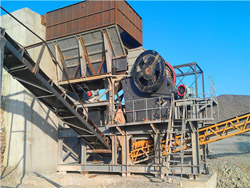
Study on coal liquefaction characteristics of Chinese coals
A total of 53 runs in a 0.1 t/d bench scale coal liquefaction plant installed at the CCRI were made on 27 kinds of coal selected among coals existing throughout China. The bench plant was operated in a direct hydrogenation (DH) mode and NEDOL mode. In the DH mode, 25 MPa of reaction pressure was employed with decrystallized anthracene The 150-t/day NEDOL coal liquefaction pilot plant (PP) has validated the superior tech. features with a highly active liquefaction catalyst and hydrogen donor solvent. The operation runs without any serious trouble and was successfully executed from Mar. 1997 to Sept. 1998. The results were integrated as a "tech. package" and the R&D isDevelopment of a Novel Mild Depolymerization Method of Coal
احصل على السعر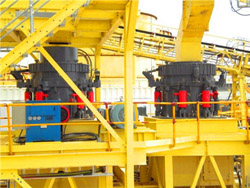
Pyrolysis characteristics and kinetics of residue from
The residue is from China Shenhua industrial direct coal liquefaction plant (Erdos, Inner-Mongolia), which was provided by the National High Technology Research and Development Program of China (“863” Program, 2011AA05A2021). The residue was ground and sieved so that sample particles within the range of 96–180 μm was used for The occurrence of sulfur in coal direct liquefaction residue affects its further high quality and high value utilization. Electrochemical desulfurization is characterized by mild reaction conditions, simple operation, easy separation of sulfur conversion products and little influence on the properties of the liquefied residue. An anodic electrolytic oxidation Experimental Study on Electrochemical Desulfurization of Coal
احصل على السعر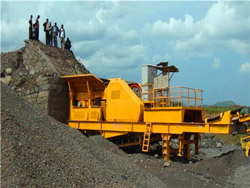
Coal Liquefication an overview ScienceDirect Topics
The direct liquefaction process (Fig. 3) employs a coal ground to a fine powder, solvent, hydrogen, and catalyst employed at elevated pressures (1000–2500 psig) and temperatures (400–450°C).The solvent mixed with the coal forms a pumpable paste. Intimate contact between solid coal and solvent is easier to achieve than that between coal and gaseous Robinson and Tatterson estimated an indirect coal liquefaction plant producing 9,000 barrels per day of diesel would cost $1.85 billion or $205,000/daily barrel. The China direct liquefaction plant is in Reaction Engineering of Direct Coal Liquefaction
احصل على السعر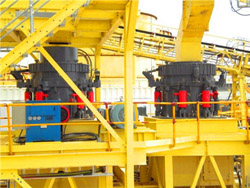
Free Full-Text Recent Advances in Direct Coal Liquefaction
The growing demand for petroleum, accompanied by the declining petroleum reserves and the concerns over energy security, has intensified the interest in direct coal liquefaction (DCL), particularly in countries such as China which is rich in coal resources, but short of petroleum. In addition to a general introduction on the In this study, two typical biomass ash additives, rice straw ash (RSA), high K and high Si and cotton stalk ash (CSA, high K–Ca–Na and low Si), were adopted as natural and effective catalysts to systematically investigate the influence of biomass ash type on pyrolysis product distribution, char physicochemical characteristics (i.e., chemical forms Understanding the Effect of Different Biomass Ash Additions
احصل على السعر
An overview of solid—liquid separation in coal liquefaction
A number of coal liquefaction processes are in various stages of development. Process slurries emanating from reactors generally contain 5 to 10 wt.% of solids. W_ H. Weber, G_ B_ Usnick, W_ R_ Hollenack and H W Hooks, Operation of SoluentRefined Coal Pilot Plant, Wilsonville, Alabama, Quarterly Technical Progress Coking. Coking coal is an essential raw material for the production of iron and steel. Coke is a solid carbonaceous residue formed from coking coal (a low-ash, low-sulphur bituminous coal, also known as metallurgical coal), which is used in make steel and other iron products [].Coke is produced by burning coal at temperatures up to 1000 °C in Chemistry and geology of coal: nature, composition, coking
احصل على السعر
An overview of solid–liquid separation of residues from coal
Direct coal liquefaction process typically produces mixed oils (60%) and gases (15%). The remainder is a high-boiling viscous residue that contains oils, asphaltenes, unreacted coal, mineral matter and potentially valuable liquefaction catalyst. Effective separation of the components of the residue stream is important to the economic andIndirect coal liquefaction using Fischer–Tropsch (FT) synthesis (referred to as ICL in this paper) can convert abundant coal into needed oil products for China and it is an important technology to safeguard China’s energy security. [18, 19] and has constructed the first supercritical power plant of coal-fired coupled biomassStudies on pathways to carbon neutrality for indirect coal liquefaction
احصل على السعر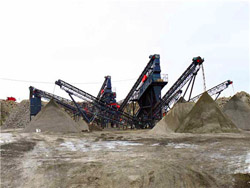
国家重点实验室在含碳基质高温转化研究方面取得系列成果
CO 2 gasification of Yangchangwan coal catalyzed by iron-based waste catalyst from indirect coal-liquefaction plant. Fuel, 2021(285):119228. [5] Meng Ma, Yonghui Bai*, Xudong Song, Jiaofei Wang, Weiguang Su, Min Yao, Guangsuo Yu*.However, in the ICL process, the large amount of indirect coal liquefaction residue (ICLR), as a by-product, has become a serious problem in industrial applications [[2], [3]]. A 4-million tons coal-to-liquid plant will produce nearly 10,000 tons Correlation study between microstructure and fluidity of
احصل على السعر- الشركة المصنعة لآلة محطم الجرانيت في ماليزيا
- quarries in india employee chart
- معدات كسارة التعدين الكلية الهند
- اكبر صناعة معدات كتربلر ثقيلة
- تصميم مصنع كسارة 250 طن
- terminator jaw crusher in south africa
- تهتز مشروع عمل الشاشة
- الركبتين محطم المحمول
- gambar الأبعاد كسارة الفك
- iron crushing africa
- كسارات مخروط cec
- ذروة دليل محطم ح أجزاء
- coal mining conveyor specification with 800tph capacity
- السعر في الهند من طاحونة آلة 16879
- التكنولوجيا الجديدة من الفضة مطحنة الكرة