اتصل
هاتف
+0086-371-86162511
عنوان
تشنغتشو ، الصين
calculation of power for ball mills and grinding
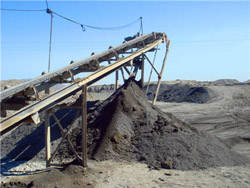
(PDF) Calculation method and its application for
Measurement results of two ball mills in a real ceramic manufacturing plant showed that the proposed calculation models could The theoretical calculation of the kinematics of grinding bodies and the energy modes of the ball-tube mill is based on the two-phase ball motion model Power Calculation of Ball-Tube Mill Drives in the
احصل على السعر
(PDF) Grinding in Ball Mills: Modeling and Process
The paper presents an overview of the current methodology and practice in modeling and control of the grinding process in industrial Owing to the lack of effective energy consumption models of ball mills in the ceramic industry, a calculation model to forecast energy consumption of ceramic ball mills during Calculation method and its application for energy consumption of ball
احصل على السعر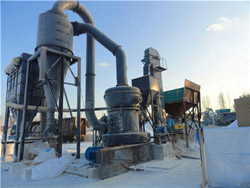
Calculation of energy required for grinding in a ball mill
The grinding-product size, P, in a Bond ball mill, which is given by the aperture size which passes 80% of the grinding product as a function of the aperture size In this paper, a new approach for the calculation of the power draw of cement grinding ball mills is proposed. For this purpose, cement grinding circuit data including the operational [PDF] Calculation of the power draw of dry multi-compartment ball mills
احصل على السعر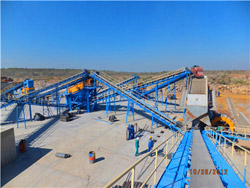
Calculation of energy required for grinding in a ball mill
The consumption of more energy for crushing and grinding uranium sandstone ores from particle of ≤10 mm to≤0.075 mm. From the predicted mill energy Tumbling mills filled with grinding balls and particles were simulated using DEM. • The damping energy on particles is more suitable than power draw to A DEM based scale-up model for tumbling ball mills
احصل على السعر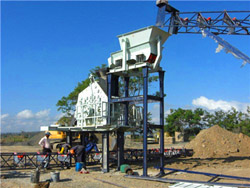
The Power Consumption Calculation of a Ball Drum Mill
Problem Statement: The theoretical models for calculating the power consumption of the grinding bodies motion of the mills based on a two-phase model of CERAMIC LINED BALL MILL. Ball Mills can be supplied with either ceramic or rubber linings for wet or dry grinding, for continuous or batch type operation, in sizes from 15″ x 21″ to 8′ x 12′. High density ceramic linings of uniform hardness male possible thinner linings and greater and more effective grinding volume.Ball Mills 911 Metallurgist
احصل على السعر
A direct approach of modeling batch grinding in ball mills
The grinding operation in a ball mill is a capital- and energy-intensive process. Hence, a marginal improvement in the efficiency of mill operation will be of immense economic benefit to the industry. Therefore, knowing the required mill capacity and the power consumption, one can calculate the selection function of the industrial millRowling are used to calculate the mill power draw. The Morgärdshammar equation and the IMM equations are shown for comparison. The method of use is similar to the AM section 3.3 Ball Mill Design The ball mill designs also follow the Bond/Rowlings method with comparison with other methods. Again the method of use is the sameGrinding Mill Computer Model AusIMM
احصل على السعر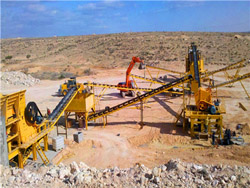
AG/SAG/Ball Mill MetEngineer
Gross Power Draw and Specific Energy Calculator for Autogenous Grinding (AG), Semi-Autogenous Grinding (SAG) and Ball Mills. Exit Mill Calculator. Shell Sizing Parameters. Parameters. Value . Value . Mill Shell Inside Diameter: [m] [ft] Mill Shell Inside Length: [m] [ft] Shell Heads Cone Angle:A.S. Erdem, Ş.L. Ergün, A.H. Benzer 222 () KW b D V p fC s C S s s ⎟+ ⎠ ⎞ ⎜ ⎝ ⎛ = × × − × × − 9−10 0.3 2 0.1 4.879 3.2 3 1 (1) where Kwb Kilowatts per metric ton of balls D Mill diameter inside liners in meters Vp Fraction of mill volume loaded with balls fCs Fraction of critical speed Ss Ball size factor To determine the power that a dry grindingCALCULATION OF THE POWER DRAW OF DRY
احصل على السعر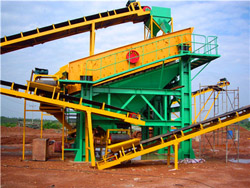
Ball mill load status identification method based on the
A ball mill is important grinding equipment in a concentrator, and the accurate detection of the load status ensures that the ball mill runs in the best state, which helps optimize the grinding process, ensure the stable operation of the ball mill equipment, and save energy. The current mainstream detection methods cannot easily detect the This paper differentiates scrubber and AG mill modelling in a similar way that overflow ball mills and grate discharge ball mills are analysed. Smaller scrubbers (600 kW) are suited to small scale(PDF) Power-based comminution calculations using Ausgrind
احصل على السعر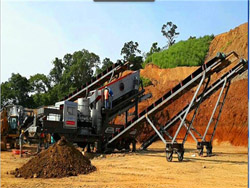
Grinding Mill Power 911 Metallurgist
Thus the power to drive the whole mill. = 49.5 + 66.0 = 115.5 h.p. = 86 kW. From the published data, the measured power to the motor terminals is 103 kW, and so the power demand of 86 kW by the mill leads to a combined efficiency of motor and transmission of 83%, which is reasonable.Figure 3a and 3b gives the results of the computer calculation. The mill power at the pinionshaft for a 30% volume charge is the sum of: Figures 3a & 3b give the power for an autogenous mill. Figures 4a and 4b are for the same size mill with a ball charge of 6% of mill volume (290 lbs. per cubic foot).AG Autogenous & SAG Semi-Autogenous Mill Design Calculations
احصل على السعر
A new methodology to obtain a corrected Bond ball mill
The grinding results show that the measured Bond work indices differ for different mills and for different grinding balls charge. Variations from 4.2% to 8.6% at different mills and 2.9% to 6.2% with different grinding balls charge were measured when the average values of the Bond operating index were compared.How to Measure Grinding Efficiency. The first two Grinding Efficiency Measurement examples are given to show how to calculate Wio and Wioc for single stage ball mills. Figure 1. The first example is a How to Measure Grinding Efficiency 911
احصل على السعر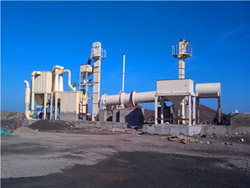
An innovative approach for determining the grinding media
1. Introduction. Grinding operation is used extensively in the industry of beneficiation, metallurgy, chemical engineering, and electric power. Assisted by the impact and abrasion between media (steel ball, steel rod, gravel, ceramic ball) and ore, the grinding operation reduces the particle size in the mill [[1], [2], [3]].To produce the qualified size the Bond ball mill to realise the same grinding conditions of a 2.4 meter wet grinding mill. However, upon close inspection of Bond’s original paper published in 1949, Bond(PDF) Measurement of electrical energy
احصل على السعر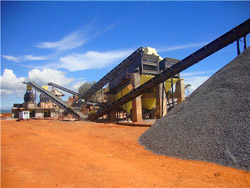
A specific energy-based ball mill model: From batch grinding
For instance, the power consumption of ball mill for grinding ceramic raw material is less than 80 kW [9] while a 5 m diameter and 8.4 m length ball mill consumes 3.9 MW of power for gold oreIn the first survey the ball mill was underperforming due to the low density in the mill, which was rectified in the second survey. The ball mill was grinding to a P 80 of 50 to 70 µm, therefore the traditional marker size (75 µm) was not applicable, and this can be seen by the increase in SSE for coarser sizes as the marker size approached PQuantifying the energy efficiency of fine grinding circuits
احصل على السعر
Ball Mill an overview ScienceDirect Topics
Mechanical Crushing and Grinding. Oleg D. Neikov, in Handbook of Non-Ferrous Metal Powders, 2009 Tumbling Ball Mills. Tumbling ball mills or ball mills are most widely used in both wet and dry systems, in batch and continuous operations, and on a small and large scale.. Grinding elements in ball mills travel at different velocities. Therefore, collision Introduction. Ball mill is a kind of widely used engineering machinery with low working efficiency [1,2]. Since the advent of the ball mill, researches on its grinding performance mainly aimed at the aspects of fill rate, rotational speed, ratio of steel balls, ratio of grinding medium and abrasive, number of lifter bars, the shape of lifter bars [3,5].A novel approach of evaluating crushing energy in ball mills
احصل على السعر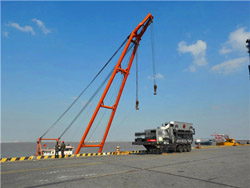
AMIT 135: Lesson 7 Ball Mills & Circuits Mining Mill
Mill Type Overview. Three types of mill design are common. The Overflow Discharge mill is best suited for fine grinding to 75 106 microns.; The Diaphram or Grate Discharge mill keeps coarse particles within the mill for additional grinding and typically used for grinds to 150 250 microns.; The Center-Periphery Discharge mill has feed reporting from both A computer code based on DEM has been developed to model the motion of the balls in tumbling mills. The code incorporates a scheme to calculate the applied torque, and hence power input to the mill. A 55-cm ball mill is simulated for two different liner cross-sections— rectangular and triangular.The discrete element method for the simulation of ball mills
احصل على السعر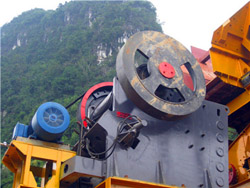
Determining Optimum Productivity of a Ball Drum Mill When
Abstract Ball drum mills (BDM) are one of the main types of coal-grinding equipment in Russia. A significant drawback of BDM is high power consumption (a significant part of the TPP’s own needs). With a huge scale of production, reducing these costs even by a few percent gives a significant economic effect. The problem of
احصل على السعر>> Next:مصانع استخلاص خام الحديد في الصين
- تخطيط إنتاج 200 طن في الساعة للركام
- خصائص المعادن من الاسمنت مطحنة
- rock Crusher for gold Mining for sale
- مسحوق الحديد فحم حجري آلة
- أكبر مطحنة كروية في العالم
- عالمية آلة طحن مصنعين الصين
- rock feeder for mining gold
- موضوع قصير عن الذبابة ناقلات الامراض
- الفضة كمنتج ثانوي في التعدين
- مواصفات الحزام الناقل الصين
- the best way to mill slag
- طن لكل ساعة آلة مطحنة علف الدواجن الهريس
- الأشغال الاورال معدات التكسير
- مكائن خط انتاج اكياس تسويق
- mineral processing departent sandur